A Comprehensive Guide to Cone Crusher Types
The standard cone crusher is the most commonly used type of Cone Crusher. It is designed to provide a consistent product size and is suitable for medium to fine crushing applications. The standard cone …
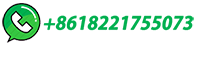
Types of Crushers: Choosing the Right One for Each Stage
Medium crushing: Employ cone crushers or impact crushers in secondary crushing to further reduce material into smaller particles. Fine crushing: Utilize sand making …
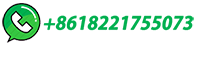
® TC Series Cone Crusher |
The ® TC Series cone crusher is the latest iteration of the live-shaft crusher design. This design has been proven to perform in heavy-duty secondary and tertiary crushing applications being tough, reliable, simple to operate and easy to maintain.. Embodying the tried and tested design elements of the original live-shaft cone crushers with added hydraulic and control …
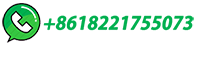
Crushers
Fine crushing with cone crushers. Due to their design, cone crushers are generally a more expensive investment than impactors are. However, when correctly used, a cone crusher offers lower operating costs than a conventional impact crusher. Therefore, clients crushing hard or abrasive materials are advised to install cone crushers for the final ...
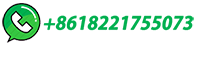
Gyratory Crusher vs. Cone Crusher: What's the …
A gyratory crusher has a mantle that rotates within a concave bowl, while a cone crusher has a mantle that rotates within a bowl-shaped concave. This design allows for a larger feed size and a higher capacity for …
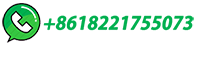
Cone Crushers
Mantle and concave for coarse, medium and fine crushing can be installed in the same top cell assembly. ... Incorporating the well proven fully hydraulic Parker Cone Crusher, this unit is ideal for working in a composite crushing arrangement with Parker primary crushing plants, screens and conveyors. ...
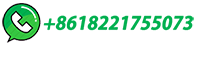
MCC Series Cone Crusher | Minyu Machinery Corp.
The MCC Series Cone Crusher by Minyu is used for standard or coarse crushing and can be stationary or portable. ... There are generally four types of Standard Cone Crushers: the MCC Standard or Coarse type, the MCF Fine or Medium type, the MCS Short Head type & MCSS Super Fine type. All four types are designed for secondary or tertiary crushing ...
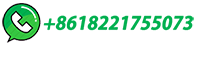
Forces in a Cone Crusher | Steel in Translation
The crushing of minerals and ore is of great industrial importance. With global population growth, urbanization, and continuing improvements in living conditions, the productivity and efficiency of existing crushers must be increased to meet the growing demand [].Cone crushers are characterized by a continuous operating cycle and may process strong and …
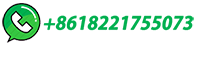
Understanding the Cone Crusher Working Principle: How It
The cone crusher's unique design allows it to rotate at high speeds and crushes material through a combination of compression and impact. When the cone crusher is in …
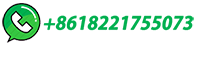
® HP500™ cone crusher
In a size-class comparison, this cone crusher has a higher output capacity, higher density in the crushing chamber and better reduction ratio, producing higher on-spec yield end products with the same energy consumption. ... and select the product size distribution according to your preference of coarse or fine aggregate production. ...
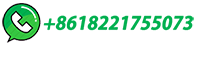
Cone crusher basics in 4 minutes
Cone crusher basics in 4 minutes. This is the starting point for understanding how cone crushers work – and how they can make your mine or quarry more productive. Elsewhere on the site …
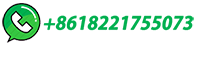
Cone Crusher For Sale in The Philippines
Cone crusher for sale in the Philippines is ordinary crushing equipment for medium and fine crushing in the processes. With the features of high crushing ratio, low energy consumption, and uniform particle size, it is used for …
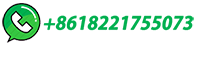
® GP Series™ cone crushers Wear parts …
crusher is 3-5 and, for the GP fine crusher, 1.5-3. Wear parts application guide - ® GP Series™ cone crusher GP Series crushers and basic concepts Product Feed Reduction ratio = F80 / P80 The GP cone crusher is a compressive crusher where feed material is crushed between a fixed concave and a movable mantle. Bigger
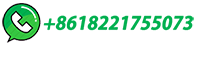
Ore Crushing | SpringerLink
Ore fine crushing is a process of crushing ore blocks with a feeding particle size of 50–150 mm to 5–25 mm, and the maximum crushing ratio of fine crushing is about five. The main equipment suitable for fine crushing operations includes a fine crushing jaw crusher, short head cone crusher, high-pressure roller mill, etc. Ore superfine crushing.
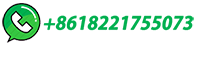
The pros and cons of cone crusher applications
A cone crusher in a secondary crushing application will typically work with a 3.5:1 to 5:1 reduction ratio. Tertiary cone crusher configurations typically work with a reduction ratio of 2.5:1 to 4:1. ... If the liners are too fine, …
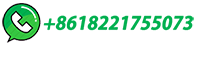
Crushing
Cone Crusher. Cone crushers are mainly used for fine crushing of raw materials and for maximizing production. The cost for servicing is very less due to simple yet stable structure. Cone crushers are used widely for raw materials processing ranging from hard to medium hard mineral stones. Cone crushers are very stable in production performance ...
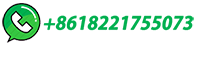
4 Types of Cone Crushers: What Are They and How to Select
The single-cylinder cone crusheris a medium and fine crusher with betterperformance than the cone crusher. It is suitable for crushing soft ores and weathered ores with large output. Many users like to use it to crush granite, basalt, river pebbles, limestone, dolomite, and …
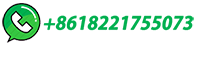
Stone Crusher Machines In Philippines
Stone crusher machines are equipment designed to crush or break down large stones, rocks, and minerals into smaller pieces, gravel, or dust for various applications. According to the customer's final particle size requirements for crushed aggregate, it has different crushing stages with various machines, including primary crushing equipment, medium crushing machine, …
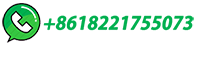
Cone Crusher For Sale In Indonesia
AIMIX provides quality spring cone crusher, single/multi-cylinder hydraulic cone crusher, compound cone crusher for sale in Indonesia, check! Skip to content. Tel: +62 898-3129-840. Email: [email protected]. ... they are suitable for …
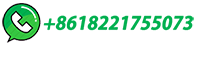
Primary and Secondary Crushing: Understanding the Basics
The secondary crusher can be a cone crusher, impact crusher, or gyratory crusher, depending on the hardness, abrasiveness, and size of the materials. The cone crusher is the most common type of secondary crusher used in mining and quarrying operations.
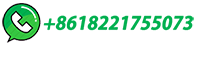
Astec Kodiak® Cone Crushers
The Kodiak ® cone crusher meets coarse and fine crushing application requirements and offers on-the-fly adjustability for easy operation. Kodiak® Cone Crusher Animation. Applications. Aggregates. There are two main classes of aggregates: natural and manufactured. Deleterious material needs to be removed from both classes.
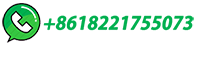
HP series cone crushers Wear parts …
• The crusher should be choke fed so that the crushing chamber is full all the time. This is important, especially in fine crushing. Choke feeding maximizes the amount of multi-layer crushing, improves the shape of the crushing cavity as it wears and improves the crushing efficiency. => Choke feed level for an HP cone crusher is
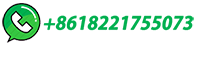
Cone Crusher Sizing & Selection To Maximize Production
Carefully screen out oversized rocks using a grizzly system before the material enters the cone crusher. Select The Right Chamber Profile. Cone crushers utilize a variety of chamber profiles suited to fine, medium or coarse crushing applications. Fine crushing chambers have a steep head angle with a short crushing stroke.
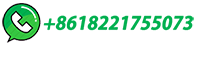
Understanding the Cone Crusher Working Principle: How It …
A cone crusher is a powerful tool used in the mining, aggregate, and construction industries to crush materials into smaller pieces. But how does it work? In this article, we'll explore the cone crusher working principle, including the eccentric motion of the main shaft, the crushing process, and the importance of proper maintenance. Whether you're a seasoned …
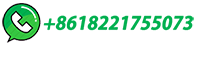
The Complete Guide to Primary Crushing, Secondary Crushing…
Learn everything you need to know about primary crushing, secondary crushing, and tertiary crushing in this comprehensive guide. Discover the types of crushers used in each stage, their working principles, and the advantages and disadvantages of each process. Get answers to frequently asked questions and improve your understanding of the comminution …
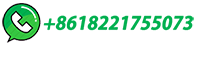
A Detailed Overview of Cone Crushers and What …
Most cone crushers have a feed opening size of 5-14", so material that's larger than the maximum size allowable will need a first stage of crushing before they can be fed into a cone crusher. Final Product Isn't Uniform. Cone …
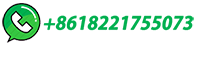
Cone Crusher
Cone crushers are used for intermediate and fine crushing after primary crushing. The key factor for the performance of a cone type secondary crusher is the profile of the crushing …
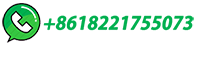
Three cone crushers by Superior Industries
PAT CONE [Bushing Cone] DAKOTA CONE [Bearing Cone] ENDEAVOR CONE [Spider Bushing Cone] Maximize horsepower per ton: Most efficient horsepower per ton: Largest range of feed size: Strong performance in fine crushing: Better installation on portable chassis: Easiest to operate and maintain: High tolerance for misapplication: Simplified oil ...
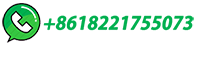
Understanding the Cone Crusher Working Principle For …
The cone crusher is one of the most popular and commonly used crushing equipment in quarries, mines, and other industries. It is designed to crush materials with high hardness and medium hardness, such as basalt, granite, limestone, gravel, quartz, iron ore, copper ore, and so on.
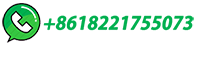
How to Adjust a Cone Crusher: A Step-by-Step …
Introduction. A cone crusher is a type of crushing equipment used in mining and aggregate industries. It works by compressing materials between a mantle and a concave, which causes them to break apart. Proper …
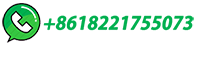