23.3: Metallurgy of Iron and Steel
Originally, the iron was collected in pools called pigs, which is the origin of the name pig iron. Figure (PageIndex{1}): A Blast Furnace for Converting Iron Oxides to Iron Metal. (a) The furnace is charged with …
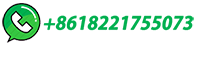
Iron Ore Processing, General | SpringerLink
Iron ores are rocks and minerals from which metallic iron can be economically extracted. The ores are usually rich in iron oxides and vary in color from dark gray, bright …
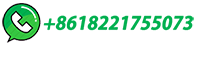
Iron Production
The production of iron from its ore involves an oxidation-reduction reaction carried out in a blast furnace. Iron ore is usually a mixture of iron and vast quantities of impurities such as sand …
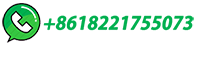
The Extraction of Iron
This page looks at the use of the Blast Furnace in the extraction of iron from iron ore, and the conversion of the raw iron from the furnace into various kinds of steel. …
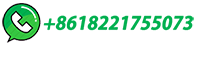
Iron Production
The production of iron from its ore involves an oxidation-reduction reaction carried out in a blast furnace. Iron ore is usually a mixture of iron and vast quantities of impurities such as sand and clay referred to as gangue. The iron found in iron ores are found in the form of iron oxides.
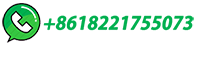
Iron ore extraction techniques
Iron ore was won by drilling and blasting (Figure 7.1).As mining technology generally developed, so did drilling techniques and the explosives used. Smith (1990) reported that the Cleveland deposit was associated with a very strong stone roof rock (known as "dogger") allowing mine drivages to be self-supporting. However, he states that in later years where the …
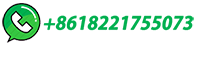
Why Is Iron Ore Valuable? Behind the Scenes of Production …
Iron Ore Extraction. Most iron ore mining takes place in surface or open-pit mines. Usually, heavy machinery removes the top layer of the ground over a wide area and exposes the iron ores. In some cases, miners dig shafts into the earth with side tunnels that allow them to follow the layer of ore.
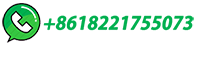
Extraction and separation of manganese and iron from …
Fe-Mn ores and poor Mn ores resources are abundant all over the world (Yao, 1996, Fan and Yang, 1999, Tan et al., 2004, Granina et al., 2010, Baioumy et al., 2013, El-Hussiny et al., 2015).During the mining, crushing, beneficiation and transportation of rich Mn ores, about 30% of the mined ores are converted into manganese ore fines with low Mn grade …
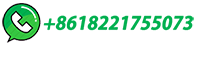
Nickel processing
Nickel processing - Extraction, Refining, Alloying: The extraction of nickel from ore follows much the same route as copper, and indeed, in a number of cases, similar processes and equipment are used. The major differences in equipment are the use of higher-temperature refractories and the increased cooling required to accommodate the higher operating …
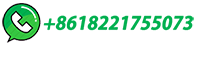
Iron Ore Processing: From Extraction to Manufacturing
The extracted ore undergoes further processing to separate the valuable iron-bearing minerals from the impurities and gangue minerals, as described in the subsequent stages of iron ore processing. Exploration and extraction are vital steps in the iron ore processing chain, as they determine the presence and viability of iron ore deposits.
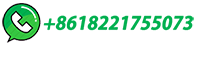
Iron Extraction by Blast Furnace Metallurgy
Iron, when extracted from iron ore such as haematite containing iron(III) oxide, Fe 2 O 3, in a blast furnace is called iron extraction blast furnace metallurgy. In this reduction reaction, oxygen is removed from the iron(III) oxide to leave behind iron. Generally, the extraction of metals and their isolation are based on three major procedures.
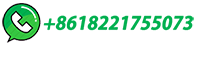
Extraction methods of iron and aluminium
Extraction methods of iron and aluminium Extracting iron from iron ore using a blast furnace Iron is extracted from iron ore using carbon and limestone inside a blast furnace. Iron ores are present as iron oxides in rocks like magnetite and haematite. These are mined from the ground in massive open cast mines in the USA, Canada, Brazil, Australia,
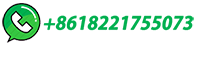
Ironmaking 101 – From Ore to Iron with Smelting …
Reduction of iron ore to reduced iron form adds value and provides more compact products, which reduces shipping costs. The specific iron content of the direct reduced iron is a function of the iron content of the iron …
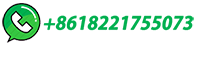
A critical review on metallurgical recovery of iron from iron ore
In the processing of various iron ores, the resulting IOTs demonstrate a diverse phase composition, often influenced by the presence of low-grade goethite-hematite ore and associated clay minerals. The phase composition of IOTs, as presented in Table 2, varies significantly due to the diverse mineralogy inherent in the iron ore extraction ...
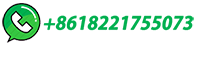
iron and steel
Extracting iron from the ore. Think about: Loss of landscape due to the size of the chemical plant needed. Noise. Atmospheric pollution from the various stages of extraction. For example: carbon dioxide (greenhouse effect); carbon monoxide (poisonous); sulphur dioxide from the sulphur content of the ores (poisonous, acid rain).
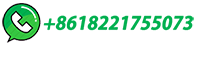
Iron Ore in India, Types, Uses, Distribution, World Map
Iron Ore is a naturally occurring solid material from which valuable minerals are extracted for commercial use. Iron ores are rocks and minerals that can be economically extracted to produce metallic iron. They are generally rich in iron oxides. They come in various colours such as dark grey, bright yellow, rusty red, deep purple, etc. ...
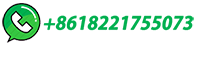
12.3: Metals and Ores
Iron ore is reduced with coke in a blast furnace (Figure (PageIndex{1})). ... Metal ores contain sufficient minerals with important elements including metals that can be economically extracted from the rock. The ores must be processed to extract the metals of interest from the waste rock and from the ore minerals.
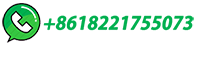
Lesson Explainer: Extracting Iron | Nagwa
Iron ore; Answer . This question lists many different substances involved in the extraction of iron. The extraction of iron occurs inside a blast furnace, a large 40 m tall steel tower. The waste gases produced from this process are carbon …
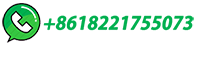
Chemistry KS4/GCSE: How is iron extracted?
Fran Scott explains iron extraction. The main raw material is iron ore and this arrives in the UK by ship in huge quantities from Brazil. Other raw materials include coal and limestone. The coal ...
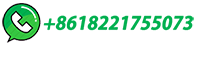
An Introduction to the Chemistry of Metal Extraction
Copper is much rarer, but fortunately can be found in high-grade ores (ones containing a high percentage of copper) in particular places. Because copper is a valuable metal, it is also worth extracting it from low-grade ores as well. Ores are commonly oxides, for example: bauxite (Al 2 O 3) haematite (Fe 2 O 3) rutile (TiO 2). . . or sulfides ...
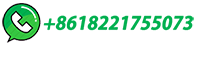
Extraction of Iron from Hematite | CIE IGCSE …
Carbon monoxide reduces the iron (III) oxide in the iron ore to form iron. This will melt and collect at the bottom of the furnace, where it is tapped off. iron (III) oxide + carbon monoxide → iron + carbon dioxide. Limestone (calcium …
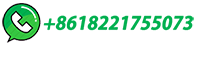
Iron Ore Processing: From Extraction to …
The extracted ore undergoes further processing to separate the valuable iron-bearing minerals from the impurities and gangue minerals, as described in the subsequent stages of iron ore processing. Exploration and …
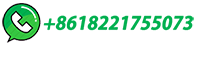
Ironmaking 101 – From Ore to Iron with Blast Furnaces
Roasting or calcination of the ore oxidizes some of the sulfur, phosphorus and arsenic impurities. Sulfur oxide is volatile and evaporates off or is washed out. Iron is mainly extracted from hematite (Fe 2 O 3) and magnetite ores. Natural or direct shipping iron ores contain between 50-70% iron and can be fed directly into the blast furnace.
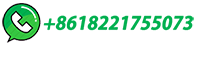
Extraction of Metals from Ores – Different Processes Involved
Iron, which is one of the most important and beneficial metals, is extracted from iron ores. Iron ores mines are found in Goa, Karnataka, Orissa. Aluminium is extracted from Bauxite ore. In India, the most available ore is Bauxite ore. States with Bauxite deposits are Maharashtra, Tamil Nadu and Gujarat. Tin which is obtained from tinstone can ...
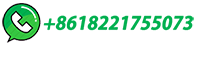
Extraction of manganese from iron rich MnO2 ores via …
Furthermore maximum iron extraction for these ores is only 3.2%, which is well below compared to that in conventional processes. The results demonstrate using SO 2 as reductant in the absence of O 2, selective sulfation roasting–water leaching is a process that is promising for the extraction of manganese from low-grade manganese ores.
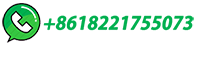
The Extraction of Iron
This page looks at the use of the Blast Furnace in the extraction of iron from iron ore, and the conversion of the raw iron from the furnace into various kinds of steel. Contributors and Attributions. Jim Clark (Chemguide.co.uk) Prof. Robert J. Lancashire (The Department of Chemistry, University of the West Indies)
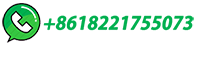
C10.3 – Extraction of Metals – IGCSE AID
An ore is a rock from which metals can be extracted. The main ore of iron is hematite, which contains large amounts of iron (III) oxide. It is reduced by carbon to form iron, but this takes place in a huge blast furnace. The raw materials needed …
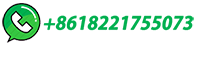
The six main steps of iron ore processing
When iron ore is extracted from a mine, it must undergo several processing stages. Six steps to process iron ore. 1. Screening We recommend that you begin by screening the iron ore to separate fine particles below the crusher's CSS before the crushing stage. A static screen is used to divert the fine particles for crushing.
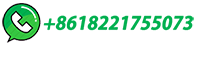
23.2: Principles of Extractive Metallurgy
Figure (PageIndex{2}): Three Common Ores. (left) Iron ore, (middle) Manganese ore – psilomelane, and (right) Lead ore – galena and anglesite. Most metals are found as …
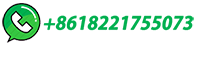
Extraction of Metals | CIE IGCSE Chemistry Revision Notes …
The Earth's crust contains metals and metal compounds such as gold, copper, iron oxide and aluminium oxide; Useful metals are often chemically combined with other substances forming ores: A metal ore is a rock that contains enough of the metal to make it worthwhile extracting
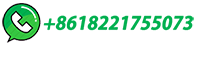