Carbon emissions mitigation methods for cement industry
Many cement companies typically operate only one production plant and the availability and costs of mitigation resources vary among these plants (Edwards 2017). Previous studies have neglected the interactions between different mitigation methods.
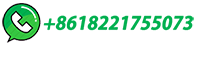
Key factors in setting up a cement plant
Setting up a cement plant is both time and capital intensive; it could take anywhere between five to seven years from concept to commissioning and an investment of around to Rs 1,800-2,000 crore for a typical integrated plant of 3 million tpa cement capacity. Size of a cement plant could vary from 0.2 million tpa to 5.0 million tpa.
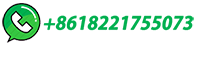
Must-know: The cost elements of cement
The cement industry relies on power. Power and fuel costs account for ~30% of the price of cement when it's sold. As a result, power and fuel have a major impact on the company's operating ...
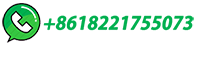
How to Reduce the Cost of Concrete Production
Home; Concrete; How to Reduce the Cost of Concrete Production. The National Ready Mix Concrete Association (NRMCA) estimates 3-5% of ready-mix concrete deliveries in the U.S. are rejected at the ...
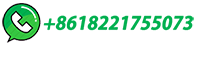
Projecting future carbon emissions from cement production …
In Group 2 countries, the largest cement producer, China, started most large-scale construction of cement plants around the year 2000 and experienced rapid growth in production from around that time.
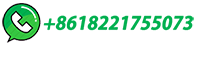
Energy Efficiency Improvement and Cost Saving …
The production of cement is an energy-intensive process. Typically, energy consumption accounts for 20-40% of production costs. In 2008, the U.S. cement industry spent about …
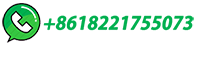
Global Cement Industry Outlook: Trends and Forecasts
This stability reflects the continued influence of various factors, including supply chain disruptions, increased production costs, and regulatory pressures and industry discipline. ... At the present technology level, the investment requirement is more than the capital cost of a cement plant. (refer to the latest announcement of Heidelberg ...
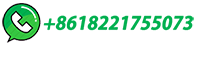
Digitization and the future of the cement plant | McKinsey
The cement plant of the future achieves considerably lower operating costs and higher asset value through higher energy efficiency, yield, and throughput. More …
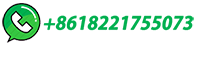
Concrete Batch Plants for Sale: Ready Mix, Precast & Central Mix
F Direct offers custom concrete batching plants for sale: ready mix, precast, & central mix. Call us for new or used concrete batching plants.
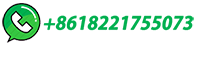
The cement industry at a turning point: A path toward value …
Shree Cement has been able to beat price leaders by achieving significantly lower raw-material costs through proximity to the source and lower labor, fuel, and …
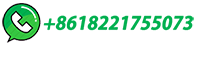
Holcim US Flagship Cement Plant to Accelerate …
The capital investment will expand the plant's current state-of-the-art production and logistics capabilities. The installation of a fifth vertical cement grinding mill will enhance processing and allow cement production capacity to increase while reducing net CO2 emissions by more than 400,000 tons per year.
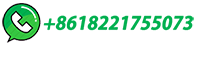
Energy and Cost Analysis of Cement Production Using the Wet …
The study evaluates the energy consumption of both wet and dry processes cement manufacturing plant in Nigeria. Energy consumption data collected for the period 2003 to 2011 were used to estimate ...
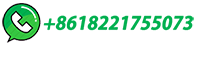
(PDF) Comparison of Technologies for CO2 Capture from Cement Production …
This paper presents an assessment of the cost performance of CO2 capture technologies when retrofitted to a cement plant: MEA-based absorption, oxyfuel, chilled ammonia-based absorption (Chilled ...
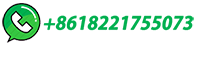
To decarbonize cement, the industry needs a full …
To decarbonize cement, the industry needs a full transformation Cement production has an enormous carbon footprint. That can be curbed with plug-and-play solutions, but eliminating emissions ...
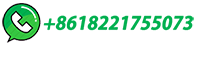
Cracking the problem of cement, one of climate's hardest …
Sublime Systems is trying to use electricity to drive down the carbon footprint of cement production. ... But traditional large-scale cement plants can cost over a billion dollars to build and ...
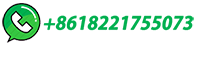
Process technology for efficient and sustainable cement production
Over the years technology in the cement industry has been further developed with a growing focus on sustainable, cost- and energy-efficient production…
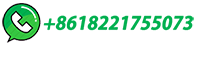
Cement
CEMENT (Data in thousand metric tons unless otherwise noted) Domestic Production and Use: In 2020, U.S. portland cement production increased slightly to an estimated 87 million tons, and masonry cement production decreased slightly to 2.3 million tons. Cement was produced at 96 plants in 34 States, and at 2 plants in Puerto Rico.
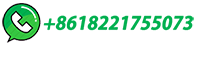
Energy and Economic Comparison of Different Fuels in Cement Production …
Cement clinkerisation is the major energy-consuming process in cement manufacturing due to the high-temperature requirement. In this paper, energy data including specific energy consumption, forms, and types of energy used at different units of cement manufacturing processes were analyzed and compared for effectiveness, availability, …
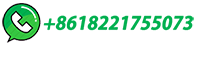
How Is Cement Produced in Cement Plants | Cement …
The dry process is the most popular industrial cement making process which is widely adopted by cement plants all over the world for its great advantages in energy saving and environmental protection.
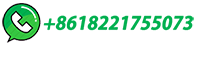
Cement industry greenhouse gas emissions
A recent single cement plant analysis came to a similar conclusion (Feiz et al., 2015). 3.5. The abatement cost of reducing GHG emissions in cement production. The mitigation of GHG emissions in the cement industry is progressing slower than the growth rate of production. Cement production grew by 73% between 2005 and 2013.
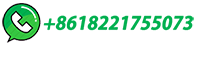
Cost-efficient strategies for sustainable cement …
efficiency, reliability and plant utilization, and embracing new technologies, we can accelerate the journey. S ustainable and cost-efficient cement c an be one and the same Sustainable solutions for carbon neutrality term plans to reduce the environmental footprint of cement production. But easier and potentially lucrative
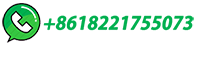
Global database of cement production assets and upstream …
The IEA tracks energy consumption and production data for the cement industry globally, while the DOE provides data on energy usage and costs for cement …
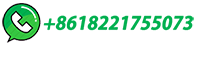
Everything about Cement Production
Extending Quarry Life through Raw Material Analysis in Cement Production. While the life of a cement plant quarry is by its very nature finite, it can be extended by means of a quarry plan that takes into account the mix of raw materials required and mines them according to a mining plan. How is the Crystalline Structure of Your Cement?
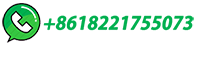
Cement Manufacturing Plant Report 2024: Setup and Cost
IMARC Group's report on cement manufacturing plant project provides detailed insights into business plan, setup, cost, machinery & raw material requirements.
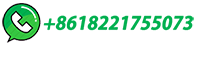
To decarbonize cement, the industry needs a full… | Canary …
Crucially, costs have actually dropped along with emissions, the company says. Its most recent step came just last week with a $ 100 million investment in its biggest U.S. cement plant that will increase production capacity by 600, 000 metric tons per year while cutting carbon dioxide emissions by 400, 000 tons per year.
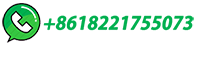
The four major costs associated with cement production
Since cement is a low-value, high-volume commodity, freight costs constitute a significant proportion, around 20-25 per cent, of the total cost of sales. There are three major …
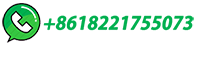
How much does it cost to start a cement manufacturing plant …
Starting a cement manufacturing plant can be a significant investment, with costs ranging from hundred to thousand crore rupees. There is…
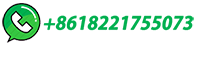
Impact assessment of alternative fuels on production Cost, plant …
The cement industry is highly energy intensive, consuming ∼ 15% of total energy demand and responsible for 26% of total industrial CO 2 emissions. With the world's second-largest installed production capacity of 594.14 million tonnes, presently Indian cement industry is struggling with uncertainty in availability as well as the cost of fuel …
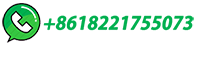
MAINTENANCE IN THE CEMENT INDUSTRY
Maintenance in the cement industry is one of the contributors to the production cost and represent typical 15 – 25 percent of total manufacturing expenditure. Many companies have tried to use standard production methods to control maintenance costs.
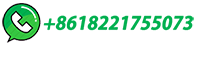
The cement industry in Europe at the crossroads
According to the VDZ (German Cement Association), a clinker factor of 63% could be possible by 2030. Based on our projection of German cement production of 28.5 Mt/a by 2030, this will result in a clinker production of only 18.0 Mt/a by 2030 (Figure 13). In 2021 there were 54 cement plants with a combined clinker capacity of 102860 t/d or 32.9 ...
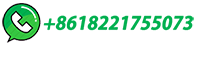