Why Choose Cement Rotary Kiln In Cement Plant? | Cement …
The wet process refers that make raw materials into cement slurry contain 32%-40% water. The finished cement slurry is diffluent, so the raw materials have a good mixture, the raw material composition is uniform, so the clinker is high-quality. Dry-process rotary kiln. The dry-process rotary kiln has opposite features.
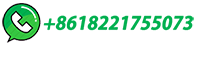
Gypsum Demand and Supply Scenario in India
Though gypsum accounts for just 2-3 per cent of the total cost of cement sales, Indian cement manufacturers are likely to face issues regarding its availability and cost in the near future. Identifying and ensuring a consistent supply of gypsum has become a challenge for cement producers. Ramachandran elaborates on the gypsum demand …
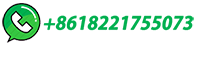
The Use of Phosphogypsum as a Source of Raw Materials for …
Not only natural gypsum (NG), but also phosphogypsum (PG), which is a by-product of the synthesis of orthophosphoric acid from phosphorite rock, can be used …
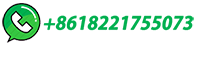
Raw material handling and storage
An insight into the criteria for the design of the plants for raw materials handling, storage and homogenisation in the cement industry. Raw materials used in cement plants have a great influence on the investment for a cement plant as the design and selection of the handling equipment is based on their physical and chemical […]
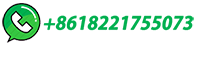
Cement Euipment Overview | Cement Making Machines | Cement Plant
Cement mill is another necessary cement equipment of the cement plant. After raw material crushing, cement mill plays vital role in the further cement manufacturing process. Cement ball mill, vertical cement mill, and cement roller press are common types of cement grinding plant.
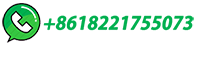
Gypsum technology by IPS Makina
IPS Makina provides complete solutions, including design, engineering, manufacturing, installation and commissioning of productions lines for gypsum plasters, gypsum plasterboards and construction chemicals, and provide turn-key supply for your gypsum factory, plasterboard plant or construction chemical factory.
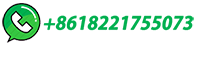
Preparation of gypsum with high purity and whiteness from …
The purity and whiteness of the purified gypsum (CaSO4) significantly increased to 99% and 92%, respectively. The migration of impurities and the material …
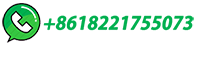
Innovative gypsum processing at GIPS AD
It sells not only calcined plaster directly to the market but also raw gypsum from its own underground mine to building material companies. The old calcining plant from the early 1970s was based on Russian kettle calcining technology with a heavy fuel oil hot gas generator and electrostatic filter.
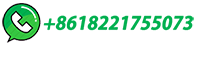
A comprehensive review of flue gas desulphurized gypsum: …
It also reviews the various applications of FGD gypsum, such as in cement and concrete production, agriculture, and gypsum board manufacturing. In the construction industry, FGD gypsum is widely used as a raw material for producing gypsum products, such as plasterboard and cement, due to its high purity and low cost.
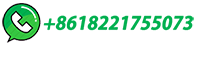
Separation and Purification Technology
The modified treatment of desulfurized gypsum with cement, inorganic waste, straw fiber and other wastes can be used to manufacture high-insulation and compression-resistant wall materials [108].
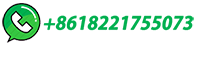
Cement Grinding Plant Overview
Cement grinding process. The whole workflow of the cement grinding plant is as follows: the cement clinker, gypsum, and mixture in the cement silo are mixed by the belt conveyor in a certain proportion and transported to the cement roller press, cement mill or group of them for grinding.
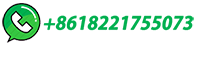
Turn-Key Solutions for Wallboard Manufacturing | Gyptech
Proven Technology Worldwide. Gyptech has established a strong reputation of providing high quality, reliable equipment for wallboard production. Designed, built, installed and backed by extensive industry experience. ... Turnkey or upgrade, our complete solutions take you from raw gypsum to a superior finished product. Equipment. Why Choose ...
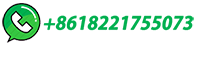
How Cement is Made
While each cement plant may differ in layout, equipment, and appearance, the general process of manufacturing portland cement is the same: crushed limestone and sand are mixed with ground clay, shale, iron ore, fly ash and alternative raw materials. Some manufacturers grind the raw materials dry, while others use a wet-grinding process ...
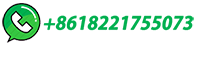
Scarcity of Domestic Gypsum Supply
Gypsum, key critical raw material for the cement and gypsum board manufacturing industries, much of the imported gypsum consuming the above countries is now turning to the Sultanate of Oman for its requirements of the commodity. The Sultanate of Oman is emerging as the single most important supply source for gypsum, with no …
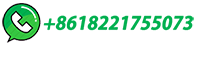
The role of gypsum in cement
Most of this variety of gypsum is used by cement plants to advantage. Experience with this anhydrite gypsum has also resulted in import of natural anhydrite gypsum by many Cement plants so to have the indicated advantages in …
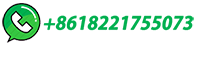
The Future of Gypsum
Raw material availability: ... converting electrical energy into mechanical motion. In cement plants, motors power various machines, such as conveyors, crushers, mills, and fans. ... Their proper selection, maintenance and operation are critical to the productivity and longevity of cement plants. Advancements and technology Recent …
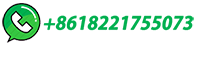
Cement Equipment, Cement Plant Equipment | Cement Plant …
Clinker production. cement equipment for clinker plant mainly include cement kiln, preheater, and other cement plant equipment, to ensure the smooth operation of equipment and technology.
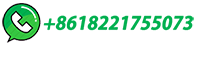
Cement Plant, Cement Equipment | Cement …
Cement plant is necessary for cement production, and mainly consists of a series of cement equipment apply for the preparation of cement raw materials, clinker production, and finished cement production, such as …
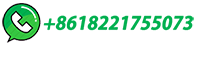
Synthetic Gypsum Manufacturing Plant Project Report 2024: Raw Materials …
IMARC Group's report, titled "Synthetic Gypsum Manufacturing Plant Project Report 2024: Industry Trends, Plant Setup, Machinery, Raw Materials, Investment Opportunities, Cost and Revenue ...
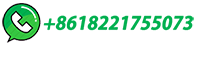
AP-42, CH 11.16: Gypsum Manufacturing
Raw gypsum ore is processed into a variety of products such as a portland cement additive, soil conditioner, industrial and building plasters, and gypsum wallboard.
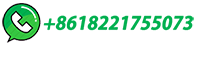
Increasing the use of synthetic gypsum in the cement industry
This paper introduces the innovative technology and highlights the steps taken by a cement company located in Alabama to operate continuously using …
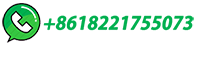
Cement Production Line,Cement Machine,Rotary Kiln,Cement Equipment
Cement production line with annual output of 1.2 million tons. Pengfei EPC cement production line project includes process design, equipment supply (including mechanical and electrical parts), civil engineering, installation and commissioning, trial operation, reaching the production standard and final delivery and other services.
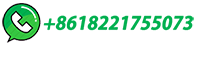
Extraction of Rare Earth Elements from Phospho …
secondary raw materials," intends to extract rare earth elements from these gypsum tailings. In this paper, a chemical process route to obtain a mixed rare earth carbonate from a monazite ...
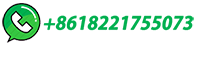
Mini Cement Plant, Small Cement Plant | 100-700tpd EPC Cement Plant
Mini cement plant for sale. Production Capacity: 100~600 tpd. Equipment: shaft kiln, rotary kiln, ball mill, raw mill, etc.. Application: Portland cement, white cement and etc.
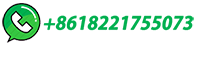
Vibrating Screen | Vibrating Screen Machine
Vibrating screen, also known as vibrating screen machine, is common cement equipment used in the cement plant. The vibrating screen helps to improve the working efficiency of the whole cement production line.
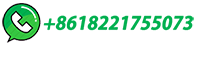
ENVIRONMENTAL PRODUCT DECLARATION …
calcium fluoride rich waste and postconsumer gypsum as recovered materials and thus, the environmental impacts allocated to these materials are limited to the treatment and transportation required to use as a cement material input.
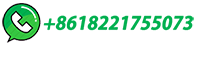
Construction and Building Materials
The three-level classification system helped to reveal the evolutionary trends of key property of composite cementitious material with gypsum under various levels, recommend the optimal content of gypsum of each level, and maximize the use of gypsum to meet the strength requirements of cement-based materials. (iii)
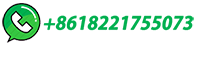
Production of High-Quality Gypsum Raw Materials from …
For economically feasible recovery of REEs from phosphogypsums, their integrated use is necessary. Large amounts of gypsum can be consumed in manufacture of gypsum …
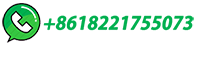
Application of titanium gypsum as raw materials in cement …
This work studied the possibility of recycling TG as raw materials for the preparation of cement-based (Sulphate Aluminate Cement and Ordinary Portland Cement) self-leveling mortars. The effects of TG on mechanical strength, fluidity, shrinkage, and …
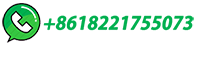
Raw Mill, Cement Raw Mill, Raw Mill In Cement Plant | Cement Equipment
Raw mill is generally called cement raw mill, raw mill in cement plant, it refers to a common type of cement equipment in the cement plant.In the cement manufacturing process, raw mill in cement plant grind cement raw materials into the raw mix, and the raw mix is sent to the cement kiln to make cement clinker, next, clinker and other …
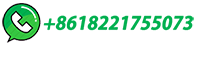