Size reduction control in cone crushers
The size reduction takes place in the volume between crushing liners; ... Cone crusher size reduction control (Itävuo et al., 2012, ... were installed. In addition, two SICK UM30 ultrasonic level sensors were installed on crusher output (q tot) and circulation (q circ) conveyors to provide redundant (duplicate) ...
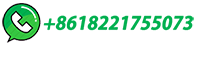
AMIT 135: Lesson 5 Crushing – Mining Mill Operator Training
For secondary cone crushers, the 0.75 value takes a value of unity. Advantages vs. Disadvantages of Gyratory Crushers. Advantages: Designed for direct dump from trucks up to 300 tons. High capacity rating. Lowest maintenance per ton processed . Highest availability.
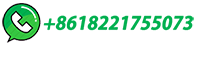
Tuning Your Cone Crusher for Specific Applications
Understanding Crusher Limits Volume Limited A combination of chamber volume, ... Typical reduction ratio by crusher type: Jaw: 6 to 1 Cone (standard/ secondary): 6 to 1 Cone …
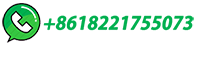
Getting To Know The Complete Set Stone Crushing Plant
Introduction. For the 100tph stone crushing plant, the truck transfers the original stone with input size under 500mm into vibrating feeder 380*96, and it transfers the stones to jaw crusher PE 600*900, after first crushing the material gets 65-180mm size, and then it goes to second crushing cone crusher 1200, the output (16-40mm) of cone crusher transfer to …
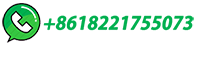
Auger Torque Launches its Cone Crusher Bucket, …
Promising to save the user time, money and hassle, Auger Torque have developed the Cone Crusher Bucket – engineered to work with excavators (2.5T to 8T), skid steers, backhoes and telehandlers. It provides a simple, …
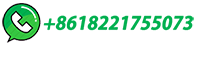
Understanding the Cone Crusher Working Principle: How It …
A cone crusher is a powerful tool used in the mining, aggregate, and construction industries to crush materials into smaller pieces. But how does it work? In this article, we'll explore the cone crusher working principle, including the eccentric motion of the main shaft, the crushing process, and the importance of proper maintenance. Whether you're a seasoned …
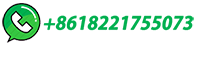
Cone Crushers
Cone crushers are highly effective at using compression to crush material into a consistent product. For this reason, cone crushers are the most commonly used crushing plant for secondary and tertiary crushing stages in both the aggregate and recycling industries. When used correctly, cones will have a far lower operating cost than an impactor ...
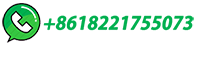
The pros and cons of cone crusher applications
A MC1150 cone crusher module that includes a feed bin with a variable speed vibrating feeder. ... explains that quarries have numerous factors to consider when selecting cone crushers to create quality aggregate products. ... Running the crusher too slow will coarsen the output and not allow the attrition rock on rock crushing action that ...
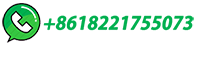
Cone Crushers (Parts of a Cone Crusher) Explained
Learn about the Cone Crusher! How it works, its components, design, advantages, disadvantages and applications. 3d models; ... only relatively small volumes of rock and aggregate could be produced. ... The width of the discharge opening dictates the size of a crusher's product output.
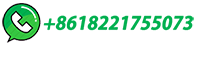
(PDF) Cone Crusher Performance
PhD Thesis Cone crushers are used by both the aggregate producing and the mining industry. ... For a given volume of material, ... product size distribution of the output from a cone crusher ...
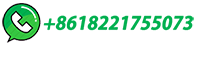
Cone crushers
MX™ Series cone crushers are the latest addition to the cone crushers portfolio. MX™ Series cone crushers utilize a revolutionary technology that combines a rotating bowl with piston into one crusher. Known for lower operating costs, high uptime and consistent high-quality output, MX™ Series cone crushers are ideal for ...
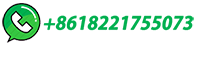
McLanahan | CMB Cone Crushers
A Cone Crusher with coarse-style liners would typically have a 6:1 reduction ratio, though reduction ratios of 8:1 may be possible in certain coarse crushing applications. Fine liner configurations typically have reduction ratios of 4:1 to 6:1.
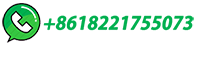
Cone Crushers | Molson Finlay
The Finlay range of cone crushers available here provide high rates of flexibility, productivity and excellent product shape in secondary and tertiary applications. ... Rated Engine Power Output. 350hp . European Emission Standard. Stage IV-compliant engine. ... achieving paramount aggregate shape everytime. FINLAY C-1545.
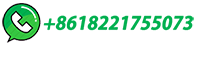
Output prediction of cone crushers | Semantic Scholar
Semantic Scholar extracted view of "Output prediction of cone crushers" by C. Evertsson
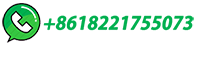
How to Choose A Rock Crusher?
Easily adaptable to various feed sizes(130mm to 1000mm) and output requirements(15mm to 300mm). Cone Crusher in Medium and Fine Crushing. ... If your project requires fine, precise aggregate shapes, the impact crusher might be ideal. Get Price Now. Features.
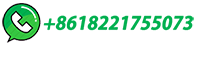
Crusher Aggregate Equipment For Sale
Browse a wide selection of new and used Crusher Aggregate Equipment for sale near you at MachineryTrader. Find Crusher Aggregate Equipment from KINGLINK, , POWERSCREEN, and more ... These machines come in three main types, jaw crusher, cone and gyratory crusher, and impact crusher. Jaw crushers, occasionally referred to as …
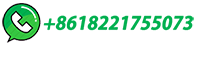
This Cone Crusher Bucket Attachment from Auger …
It provides a simple, efficient, and cost-effective way to reprocess and/or recycle small volume construction rubble and debris into useable aggregate. With an output of 5T-10T per hour (depending on your material), …
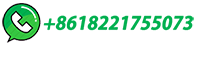
Armstrong Equipment
The ® Cedarapids RC Series cone crushers feature advanced crushing chamber technology that yields impressive capacities, fine output gradations and a highly cubical product. With improved crushing capabilities, the Rollercone® roller bearing design is able to produce larger outputs than conventional cone crushers.
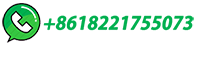
Caring for your cone crusher: A guide to optimising performance
A cone crusher punishes itself in every minute of operation. It squeezes a dense mass between heavy castings until the mass disintegrates. It abrades and minces aggregate until the material yields to the applied forces. It rumbles and vibrates and bangs as its core shaft spins eccentrically to capture and reduce chunks of aggregate.
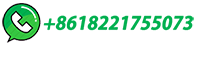
Influence of jaw crusher parameters on the quality of …
The part of aggregate processing investigated in this paper is the crushing, specifically primary crushing using a jaw crusher. Coarse aggregates for unbound use are often produced using a single crushing stage in a jaw crusher, as opposed to concrete or asphalt aggregates, where at least two and often three or four crushing stages are used ...
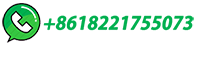
An empirical model for predicting flakiness in cone crushing
Volume 79, Issue 1, April 2006, ... of the factors influencing particle shape is of central importance for optimisation of the output quality from crushing plants for aggregate production. The literature reports that the wear on and setting of a cone crusher influence particle shape, The fact that wear on and the setting of a cone crusher ...
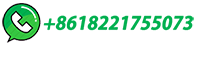
Portable 'mega' cone doubles output | Pit & Quarry
The two smaller crushing systems were exactly alike, each producing at a relatively low volume (about 200,000 tpy). Yet those two systems were easy and economical to move. The much larger third portable system (about 500,000 to 600,000 tpy) was more complex, so it was more time consuming and costly to move.
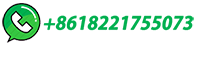
Powerscreen 1000 Maxtrak Mobile Cone Crusher from Blue
The Powerscreen 1000 Maxtrak mobile cone crusher truelly is best in class. Contact Blue Group today to find out exactly why ... The 1000 Maxtrak crusher is capable of excellent volume reduction whilst ensuring product cubicity for the production of high-quality aggregate and sub-base materials. ... Output Potential – up to 230 tph. Hopper ...
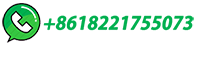
4 Types of Cone Crushers: What Are They and …
The cone crusher is a popular rock crusher in mining operations, aggregate production, and recycling applications. Many users use it for size reduction and shaping of precious metals (e.g. gold, silver, and palladium), …
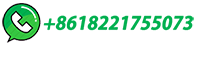
Crusher Efficiency Calculations
The following example demonstrates a method of selecting the components of an aggregate plant. Good component efficiency and part performance pre-evaluation is essential to a solid design. The aggregate …
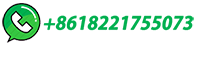
Crushing and Screening Handbook
the crusher and scalp out fi nes. Primary gyratory crushers – ideally suited to all high-capacity primary hard rock crushing applications. Jaw crushers – we have more installed jaw crushers than anyone in the world. The lead-ing choice due to their high reduction ratio and heavy duty design. Cone crushers – capacities available to suit all
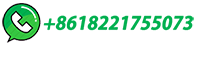
Jaw Crusher VS Cone Crusher (A Comparison …
Thus, it proves itself as an effective primary crusher in aggregate, mining, recycling, and concrete industries. ... Capacity: In terms of processing capacity, the output of the cone crusher can generally reach …
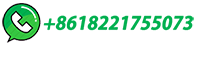
Cone Crusher Sizing & Selection To Maximize …
Proper sizing and selection of cone crushers are essential to maximize productivity and efficiency in aggregate and mining operations. Cone crushers are indispensable crushing machines, but their output capacity …
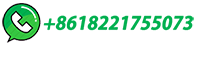
Output prediction of cone crushers
The output prediction of cone crushers has been focused on both by the aggregate producing industry and the mining industry as the demands for higher quality and lower costs increase. ... and in the crushing chamber volume ratio caused by different meta-particle sizes can significantly cause different wear depths. And with the increase of the ...
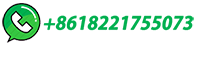
Maximize your cone crusher productivity | Pit & Quarry
Most cone crushers have a feed opening size of 5-14", so material that's larger than the maximum size allowable will need a first stage of …
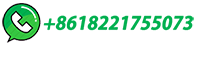