Crusher Principle Of Operation | Crusher Mills, Cone Crusher, Jaw Crushers
The Mill Operating Resource – 1: Crusher Types and Operation; Grinding 2 – Unit Operations: Cone Crusher Principles of Operation; Gyratory Crushing – Fundamental, Unit … mining crusher operating principle
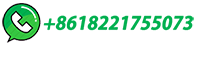
Cone Crusher | SpringerLink
Its main variants include spring cone crusher, gyradisc cone crusher, single-cylinder hydraulic cone crusher, multicylinder hydraulic cone crusher, and complex cone crusher. Depending on the needs of crushing operation, each variant can have a different cavity type, which can be classified into standard type and short head type, or standard ...
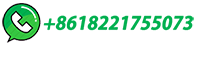
Principles Of Operation Pavement Breaker | Crusher Mills, Cone Crusher …
CS Series Cone Crusher. Jaw Crusher. Impact Crusher. Cone Crusher. Hammer Crusher. Sand Making Series. VSI5X Sand Making Machine. VSI Sand Making Machine. ... The principle of operation is similar to the air blast breakers, except that the SF6 gas is not discharged into the atmosphere. FUNDAMENTAL RELAY-OPERATING PRINCIPLES AND CHARACTERISTICS.
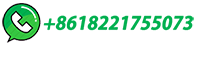
(a) Structure diagram and (b) functional principle diagram of cone crusher.
The mathematical modeling and optimization of the parameters and working processes of a cone crusher were addressed in [22, 23].A mathematical model of the working process of a jaw crusher was ...
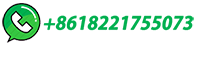
Cone Crusher Operation Principle
Cone crusher Operating principle and Cone Crusher Specification … offers primary stone crushers and jaw crushers; reliable … Spring cone crusher working principle,cone crusher … During operation, the motor of Spring Cone Crusher Crushes drives the eccentric shaft shell to turn around through ahorizontal axle and a pair of bevel gear.
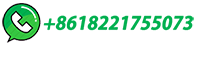
Cone Crusher
The cone crusher is a modified gyratory crusher, and accordingly many of the same terms including gape, set, and throw, apply. ... and the continuous operation principle (while the …
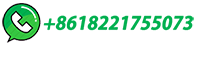
Understanding the Different Types of Crushers | Agg-Net
Cone crushers and gyratory crushers are also compression-type machines that crush material between a moving piece of steel and a stationary piece. The output is controlled by the setting between the two pieces of steel. ... This allows production of a consistent product as well as efficient, reliable operation of the crusher. Choke feeding is ...
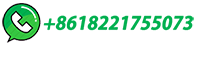
A Comprehensive Guide to Cone Crusher Types
Discover the most popular types of cone crushers on the market and their unique features, advantages, and disadvantages. ... The medium-sized cone crusher is designed for larger operations that require a higher capacity and a more uniform product size. It is similar to the standard cone crusher, but with a larger crushing chamber and a higher ...
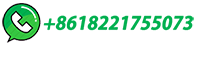
Cone Crushers (Parts of a Cone Crusher) Explained …
Cone Crushers; Typically, the initial crushing stage is completed using either gyratory crushers or jaw crushers. It is often the case that there will be only one crusher installed, and this will be referred to as the primary crusher. Cone …
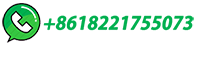
Cone Crusher Diagram: Simplified Guide
Example Analysis: Working Principle of Cone Crushers. In a gold mining operation, the raw ore is first taken from the mine to the crushing plant. ... The performance of the cone crusher is monitored and adjusted …
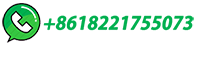
Crushing Principles of Mechanical Crushing
• Cone Crusher Operating Principle • Crusher Capacity • Crusher Operation • Optimization and Crusher Performance Map • Conclusions NCC, Borås, Sweden . ... Crusher Operation • Relation between Feed size and Shape – The greater reduction ratio the worse particle shape. – Inter particle breakage improves
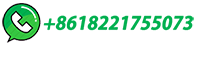
Cone Crusher
The description of the Operating Principle of cone crushers and how this machine works should begin with the driveline and how the crushing action is generated. ... The accompanying sketch shows the simplicity of the Hydrocone crusher's principle of operation. The main shaft assembly, including the crushing cone, is supported on a hydraulic ...
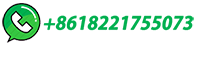
McLanahan | CMB Cone Crushers
McLanahan CMB Cone Crushers are specifically designed with attrition crushing applications in mind. ... The closed side setting, which determines product size, can be adjusted quickly, easily and while the crusher is in operation. In the event tramp material enters the crushing chamber, a vertical lift raises the upper frame to allow large ...
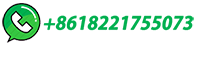
Gyratory Crushers
Wearing parts in the gyratory crusher may be either chilled cast iron or manganese steel, depending on the character of the material to be crushed and the particular class of service for which the machine is intended. Standard crushers, in the small and medium sizes, are customarily fitted with chilled-iron head and concaves for crushing soft and medium …
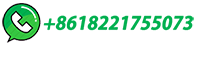
Cone Crusher
The operation procedure of cone crusher can be divided into four stages: before the start, at start-up, at run time and turning-off time. All conditions should be paid attention in each stage, and the potential problems can be found and …
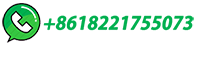
Construction Working and Maintenance of Crushers …
Generally gyratory crushers, jaw crushers, high speed double roll crushers, low speed sizers, impactors and hammer mills are used as primary crushers. In the secondary and subsequent stages, the material is further reduced and refined for proper size and shape, mostly based on specifications. Most secondary crushers are cone crushers and
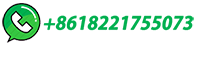
Cone Crusher Diagram: Simplified Guide
Learn about the structure and operation of cone crusher models. Equipment Processing Plants Solutions Expertises Media Company Contact Consult Experts. Home Blog; Equipment Info ... Example Analysis: Working …
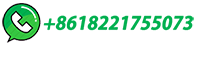
Cone crusher basics in 4 minutes
Cone crusher basics in 4 minutes. This is the starting point for understanding how cone crushers work – and how they can make your mine or quarry more productive. Elsewhere on the site you can find detailed information about all …
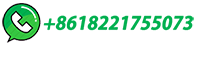
4 Types of Cone Crushers: What Are They and How to Select
The single-cylinder cone crusher is a medium and fine crusher with better performance than the cone crusher. It is suitable for crushing soft ores and weathered ores with large output. Many users like to use it to crush granite, basalt, river pebbles, limestone, dolomite, and diabase with a particle size of less than 560 mm.
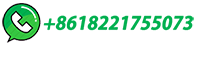
A Guide to Mobile Crushing Plants: Types, …
Mobile crushing plants have revolutionized the way materials are extracted and processed in various industries. They offer flexibility, mobility, and efficiency that cannot be achieved with traditional stationary crushing plants. …
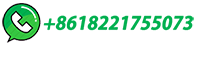
Demystifying Cone Crushers: Understanding Their …
This crusher type is essential equipment in the mining and aggregate industries. Cone crushers are perfect for hard-to-mid-hard ores, including iron ores, copper ores, limestone, quartz, …
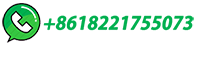
Jaw Crusher: Range, Working Principle, Application
Jaw crushers are used as primary crushers, or the first step in the process of reducing rock. They crush primarily by using compression. The rock is dropped between two rigid pieces of metal, one of which then moves inwards towards the rock, and the rock is crushed because it has a lower breaking point than the opposing metal piece.
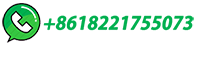
Impact Crusher Working Principle
The pendulum product distribution is a breakage function and can be used in models of the process to predict crusher product distributions for different operating conditions. As an example of this approach, Whiten's …
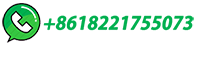
The Ultimate Guide to Jaw Crushing Machines: Types
While jaw crushers have their own set of advantages and disadvantages, they are often compared with other types of crushers, such as impact crushers, cone crushers, and gyratory crushers. In general, jaw crushers are a good option for applications where the material is relatively hard and where a high degree of reduction is required.
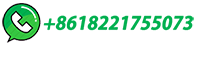
Jaw Crusher Working Principle – StudiousGuy
A jaw crusher mainly works on the principle of reciprocating motion exhibited by the moveable jaw of the jaw crusher. The repeated movement of the jaws results in the development of compression force that further causes the breakdown of the rock or the ore placed between the two jaws into smaller pieces. The movement of the jaw crusher is ...
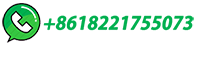
Principle of a cone or gyratory crusher.
The crushing chamber is the core component of a cone crusher, consisting of mantle and concave parts. Reducing the impact of crushing chamber wear on the performance of cone crushers and the ...
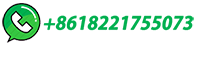
How it Works: Crushers, Grinding Mills and Pulverizers
During the primary crushing operation, boulder size feeds from 20 to 100 in. are reduced to secondary crusher sizes of 1 to 20 in. or mill feed size of .5 to 3 in. ... Table Source: Wikipedia (Crushers) Cone crushers use a spinning cone that gyrates in the bowl in an eccentric motion to crush the rock between the cone surface, referred to as ...
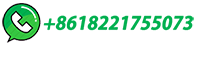
Construction Working and Maintenance of Crushers for …
Generally gyratory crushers, jaw crushers, high speed double roll crushers, low speed sizers, impactors and hammer mills are used as primary crushers. In the secondary and subsequent stages, the material is further reduced and refined for proper size and shape, mostly based on specifications. Most secondary crushers are cone crushers and
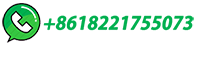
Crushing 101 – Different types of crushers for distinctive needs
Compressive crushers that press the material until it breaks, and impact crushers that use the principle of quick impacts to crush the material. Jaw crushers, gyratory crushers and cone crushers operate according to the compression principle. Impact crushers, in turn, utilize the impact principle. Another way to classify the equipment is ...
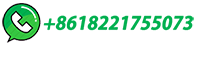
The Complete Guide to Primary Crushing, Secondary …
Working Principle of Secondary Crushers. The working principle of secondary crushers varies depending on the type of crusher, but generally, they work by applying pressure to the material through compression or impact. Cone crushers work by compressing the material between an eccentrically rotating mantle and a concave bowl.
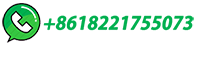