Application of deep learning in iron ore sintering process: a …
Along with the rapid development of deep learning technology, process modelling and simulation incorporating sintering theory and large-scale production data information are one of the important tools for future technological innovation in iron ore sintering and the entire iron and steel metallurgical industry, and deep learning …
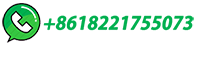
Lesson Explainer: Extracting Iron | Nagwa
The following equation shows how roasting process can transform an undesirable iron carbonate (F e C O 3) compound into a more useful iron(II) oxide ... The sintering process ensures that the iron ore, limestone, and coke materials are mixed evenly. It also ensures that the sinter materials are of the appropriate size and structure for the ...
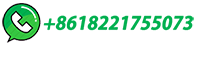
An Introduction to the Chemistry of Metal Extraction
Details for the extraction of aluminum, copper, iron and titanium are given in separate pages in this section. What are "ores"? An ore is any naturally-occurring source of a metal that you can economically extract the metal from.
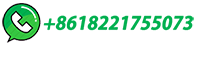
Roasting in Metallurgy
" The main object of the process which has been considered is the formation of soluble sulphate of silver." The reactions, however, are precisely similar in an ordinary oxidising roast. ... The following general equation approximately represents the reaction :— ... This was formerly effected by spreading the roasted ore on sheet-iron ...
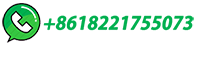
The six main steps of iron ore processing
Learn about the steps involved in iron ore processing, from crushing and grinding to separation. Contact Multotec experts for guidance on iron processing.
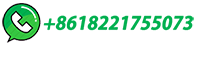
Iron Ore Processing
This review focussed on two main aspects of oolitic iron ore processing: beneficiation by conventional mineral processing techniques (differential grinding, scrubbing, gravity concentration, magnetic concentration, flotation, oil agglomeration and selective flocculation) and more energy intensive processes (hydrometallurgical, using …
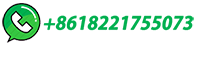
Extracting iron
Iron ore (haematite) Iron(III ... the less reactive metal and becoming an oxide itself. iron from iron(III) oxide. Here are the equations for the reaction. ... furnace is a continuous process (ie ...
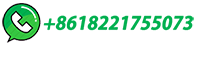
Direct reduced iron process
The reduction gases only dissolve oxygen from the iron ores. This causes the iron ores to crack on the surface. The appearance resembles a porous sponge, which is why the deoxidized and thus strongly ferrous iron ore is also called sponge iron. Sponge iron is a highly ferrous ore from the direct reduced iron process!
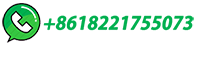
CHAPTER-7 GRAVITY CONCENTRATION OF IRON ORE
It finds immense application in the processing of iron ores besides coal, beach sands, gold, diamonds, platinum, baryte, fluorspar, tin, tungsten ores etc. ... density a and moving in a medium having density p is given by equation (3), Fg = it/6 d3 g (a — p) The centrifugal force is given by, ... for iron ore industry, was first tested at IOC ...
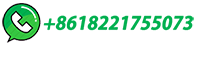
The Preparation of High-Purity Iron (99.987%) Employing a Process …
In this study, high-purity iron with purity of 99.987 wt.% was prepared employing a process of direct reduction–melting separation–slag refining. The iron ore after pelletizing and roasting was reduced by hydrogen to obtain direct reduced ...
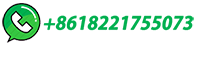
Iron Ore Processing, General
Making iron and steel from iron ore requires a long process of mining, crushing, separating, concentrating, mixing, agglomeration (sintering and pelletizing), and …
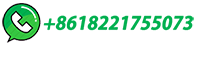
Iron processing
Iron processing - Smelting, Refining, Alloying: The primary objective of iron making is to release iron from chemical combination with oxygen, and, since the blast furnace is …
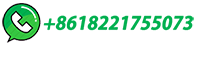
Steel Production
Even though equipment is improved and higher production rates can be achieved, the processes inside the blast furnace remain the same. The blast furnace uses coke, iron ore and limestone to produce pig iron. Coal traditionally has been a …
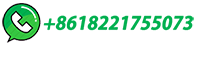
Process simulations in mineralogy-based geometallurgy …
ABSTRACT. Mineral processing simulation models can be classified based on the level that feed stream to the plant and unit models are described. The levels of modelling in …
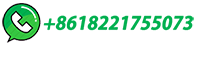
Iron Extraction and Purification / Steel | ChemKey
Loss of landscape due to mining, processing and transporting the iron ore, coke and limestone. Noise and air pollution (greenhouse effect, acid rain) involved in these operations. Extracting Iron From the Ore
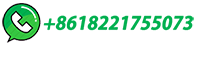
Recent Trends in the Technologies of the Direct Reduction …
The challenges associated with iron ore processing have resulted in rigorous research of new processing techniques in the iron and steelmaking process, considering their diverse applications in the construction and manufacturing industries. Iron ore consists of various elements within its metal matrix with the presence of silicate and …
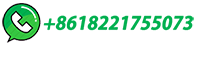
Iron Ore Sintering: Process: Mineral Processing and …
Sintering is a thermal agglomeration process that is applied to a mixture of iron ore fines, recycled ironmaking products, fluxes, slag-forming agents, and solid fuel (coke). The purpose of the sin...
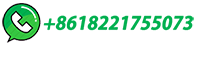
Iron processing
Iron processing - Smelting, Refining, Alloying: The primary objective of iron making is to release iron from chemical combination with oxygen, and, since the blast furnace is much the most efficient process, it receives the most attention here. Alternative methods known as direct reduction are used in over a score of countries, but less than 5 percent of iron …
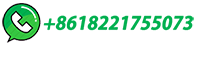
Nickel processing
Nickel processing - Extraction, Refining, Alloying: The extraction of nickel from ore follows much the same route as copper, and indeed, in a number of cases, similar processes and equipment are used. The major differences in equipment are the use of higher-temperature refractories and the increased cooling required to accommodate the higher operating …
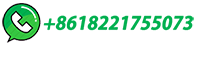
Extraction of Iron from Hematite
For Core students, the symbol equations are not needed for the different reactions involved in the extraction of iron from hematite.
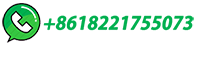
Solved 4. The equation for one of the reactions in the
Question: 4. The equation for one of the reactions in the process of reducing iron ore (Fe2O3) to the metal is [Molar masses: Fe2O3( s)+3CO(g)→2Fe(s)+3CO2( g)159.728.0155.8544.01] (a) What is the maximum mass of iron, in grams, that can be obtained from 454 g (1.00 lb) Fe2O3( s) (iron(III) oxide) ?
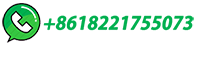
Common & Basic Formulas for Mineral Processing …
The control of a milling operation is a problem in imponderables: from the moment that the ore drops into the mill scoop the process becomes continuous, and continuity ceases only when the products finally come to rest at the concentrate bins and on the tailing dams. Material in process often cannot be weighed without a ...
23.2: Pyrometallurgy
It contains other impurities (such as Si, S, P, and Mn from contaminants in the iron ore that were also reduced during processing) that must be removed because they make iron brittle and unsuitable for most structural applications.
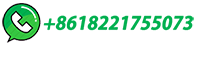
Thermodynamic Analysis of Iron Ore Sintering Process …
The sinter process of iron ore with biomass carbon instead of coke breeze as fuel was investigated via thermodynamic analysis in this paper through a comparison of sinter composition indexes, metallurgical properties, and pollutant emissions.
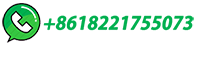
REMOVING IMPURITIES FROM IRON ORES: METHODS AND …
The inclusion of small amounts of silicon, phosphorus and sulphur in iron ores or concentrates can have a profound effect on the steel making process and thus on the final iron and steel products.
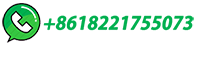
Ironmaking 101 – From Ore to Iron with Blast Furnaces
Iron is made by reacting iron ore (iron oxide and impurities), coke (a reductant) and limestone (CaCO 3) in a blast furnace. Iron ores with lower iron content …
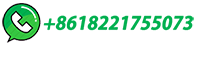
Copper Mining and Processing: Processing …
Copper processing is a complicated process that begins with mining of the ore (less than 1% copper) and ends with sheets of 99.99% pure copper called cathodes, which will ultimately be made into products for …
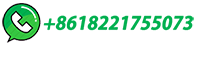
Iron processing
The primary objective of iron making is to release iron from chemical combination with oxygen, and, since the blast furnace is much the most efficient process, it receives the …
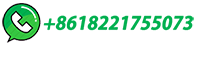
Iron Ore Processing: From Extraction to Manufacturing
Iron ore processing is a complex and vital process that transforms raw iron ore into usable steel. From exploration and extraction to grinding, beneficiation, and ironmaking, each stage plays a crucial role in producing high-quality iron ore products. The advancements in processing technologies have made it possible to efficiently extract …
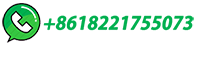
Iron processing | Definition, History, Steps, Uses, & Facts
Ironmaking is a critical step in producing high performance steel because high-quality raw materials reduce the time and energy to purify the iron to steel. On the …
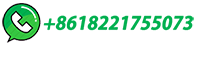
Extraction of Zinc: Process, Ores, Diagram
Extraction of Zinc and processing of zinc metal or chemical compounds for usage in various products. Learn Zinc extraction process at Embibe.
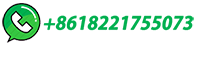