Estimation of the Specific Energy Requirement for Size Reduction …
In view of the above mentioned facts, in this paper we show how the Kapur energy-size relationship can be used to obtain more accurate estimates of the specific energy for size reduction of solids in ball mills.
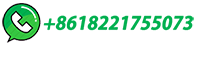
Mineral Processing Design and Operations
The energy required to liberate a mineral of economic interest from its gangue constituents in the host rock is described in this chapter.
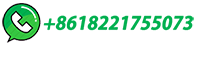
Comminution
Size reduction is an integral part of mineral processing which has the largest contribution to the energy consumption of mineral processing plants. This chapter provides an overview of size reduction theories and describes different mechanisms of breakage which are relevant in the mineral processing context, along with ore characterisation tests …
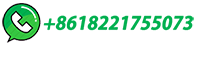
Size–energy relationship in comminution, incorporating scaling …
The size–energy relationships in comminution have been the subject of much thought. One of the first theories, developed by Rittinger, postulated that the energy dissipated by the process is proportional to the new surface area generated.
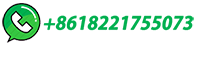
Chapter 6 Comminution
al processing plants. This chapter provides an overview of size reduction theories and describes different mechanisms of breakage which are relevant in the mineral …
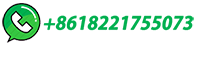
Stirred Mills – Ultrafine Grinding
The kinetic energy generated at such high tip speeds produces the energy needed for abrasion of fine mineral particles and therefore aids in size reduction. The mechanics of size reduction is described as due to the spinning and centrifugal action of the spirals, discs or pins that produces a high differential shear within the slurry between ...
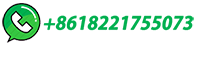
Comparison of the performance of different comminution
How does the SFC's performance compare with that of HPGR in terms of particle reduction ratio (RR), size-specific energy (SSE), and Bond operating work index (Wi o) when both devices are operated at a similar net specific energy (NSE)? 2. ... The current mineral processing methods used are highly water intensive and, …
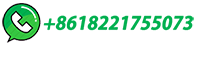
Sustainable and responsible development of minerals
The Role of Critical Minerals in Clean Energy Transitions - Analysis and key findings. A report by the International Energy Agency.
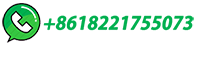
AMIT 135: Lesson 6 Grinding Circuit – Mining Mill …
The mill product can either be finished size ready for processing, or an intermediate size ready for final grinding in a rod mill, ball mill or pebble mill. AG/SAG mills can accomplish the same size reduction work as two or three stages of crushing and screening, a rod mill, and some or all of the work of a ball mill.
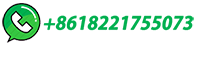
Modeling of Bauxite Ore Wet Milling for the Improvement of …
Size reduction is a necessary operation in mineral processing plants and provides the desired size for separation operations and the liberation of the valuable minerals present in ores. Estimations on energy consumption indicate that milling consumes more than 50 % of the total energy used in mining operations. Despite the …
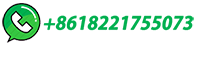
Comminution | SpringerLink
Size reduction is an integral part of mineral processing which has the largest contribution to the energy consumption of mineral processing plants. This chapter …
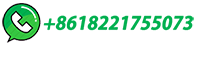
Development of ore sorting and its impact on mineral processing
The energy costs required to refine metal values contained in ore to concentrates constitute the majority of the cost to produce metals. On average across the mining industry, 44% of the total electricity consumption is dedicated to crushing and milling activities (Fig. 1).Size reduction operations, nearly 150 × 10 9 kW h, are the largest …
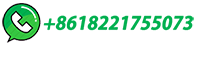
Plant Automation for Energy-Efficient Mineral Processing
The mineral processing sector holds a significant and growing share of the energy balance of the mining industry. Tromans [] reported striking data from the U.S. Department of Energy showing that 39% of the energy footprint of mining operations originated from beneficiation and processing operations in 2004.More recently, the …
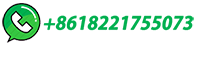
Mine-to-Mill Optimization of Aggregate Production
Developed at the Julius Krutschnitt Mineral Research Center in Queensland, Australia, the Mine-to-Mill approach attempts to minimize energy consumption through optimization of …
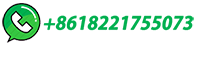
Size specific energy (SSE)—Energy required to generate …
International Journal of Mineral Processing. Volume 136, 10 March 2015, Pages 2-6. Size specific energy (SSE)—Energy required to generate minus 75 micron material. ... The relationship between energy and size reduction is of primary importance in the field of comminution.
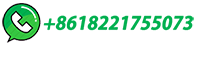
Energy conservation and consumption reduction in …
Meanwhile, grinding operations account for more than 50% of the mineral processing cost in the concentrator [[3], [4], [5]]. Therefore, it is of great significance to research saving and consumption reduction of energy during grinding operations [[6], …
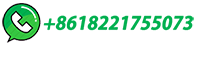
Mineral processing | Metallurgy, Crushing & Grinding
Mineral processing, art of treating crude ores and mineral products in order to separate the valuable minerals from the waste rock, or gangue. It is the first process that most ores undergo after mining in order to provide a more concentrated material for the procedures of extractive metallurgy.
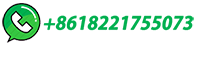
Energy conservation and consumption reduction in
Therefore, it is of great significance to research saving and consumption reduction of energy during grinding operations [[6], [7], [8]]. With the large-scale exploitation and utilization of mineral resources, the free-milling of mineral resources gradually decrease, and the refractory mineral resources gradually increase.
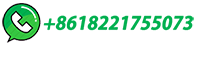
Future of Mining, Mineral Processing and Metal Extraction …
Mining, mineral processing and metal extraction are undergoing a profound transformation as a result of two revolutions in the making—one, advances in digital technologies and the other, availability of electricity from renewable energy sources at affordable prices. The demand for new metals and materials has also arisen …
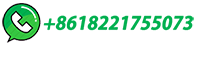
Mineral Processing
Mineral Processing. Errol G. Kelly, in Encyclopedia of Physical Science and Technology (Third Edition), 2003. VI The Mineral Processing Plant. Most mineral processing plants are represented by the flow sheet shown in Fig. 11. Simpler operations, such as a quarry producing aggregate, would involve only the initial stages of size reduction.
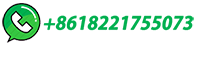
Comminution
The energy required (E) for size reduction is calculated using the so-called "Third Law", ... paper presents a perspective of the authors on how DEM contributes to the science of comminution applied to the mineral processing and aggregate industry. Rather than attempt to present a fully comprehensive review of the area, we have focussed on ...
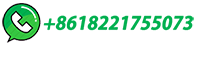
Unlocking Value: The Art of Comminution in Mining
Introduction. In the realm of mining, the journey from raw material to valuable resource begins with a critical yet often overlooked step: particle size reduction, or comminution.
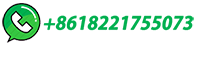
Particle Size Reduction (Chapter 5)
Introduction to the Principles of Size Reduction of Particles by Mechanical Means, NSF Center for Particle Technology Instructional Series, University of Florida.
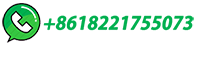
Jaw Crusher
Overview of size reduction of raw materials of the cement industry. Vipin Kant Singh, in The Science and Technology of Cement and Other Hydraulic Binders, 2023. 4.2.1 Jaw crushers. Jaw crushers are used for the primary reduction of hard and abrasive materials used for cement manufacture. Jaw crushers 3 are of either Blake-type or Dodge-type …
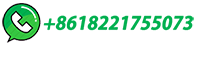
An alternative energy–size relationship to that
Size reduction–energy predictions. The proposed new energy–size relationship uses a variable size exponent in contrast to Bond's fixed value. It will therefore predict different energy requirements to reduce a rock from one size to another.
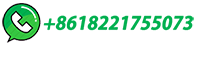
Mineral Processing | SpringerLink
The main goal of mineral processing is to reduce the amount of ore that must be translated to and processed by the smelter where the metal is obtained from the ore. It is carried out by utilizing relatively non-expensive, low-energy physical methods to split the useful minerals from the gangue. ... 6.6.2 Energy for Size Reduction.
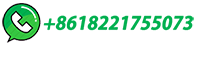
Comminution | SpringerLink
Size reduction is an integral part of mineral processing which has the largest contribution to the energy consumption of mineral processing plants. This chapter provides an overview of size reduction theories and describes different mechanisms of breakage which are...
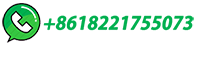
CHAPTER 5 GENERAL PRINCIPLES OF MINERAL …
in a mineral processing plant, the objective of which is to reduce large lumps to fragments or smaller particles, the largest particles in the crushed product being 1/20 in. or greater in size. Generally the objective of crushing is to accomplish size reduction, and occasional
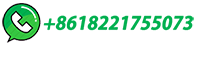
Particle Size Reduction (Chapter 5)
Introduction to Mineral Processing, chapters 7 and 8, Australian Mineral Foundation. ... Introduction to the Principles of Size Reduction of Particles by Mechanical Means, NSF Center for Particle Technology Instructional Series, University of Florida.Google Scholar. Kwade, A. and Schwedes, J., 1997. Wet comminution in stirred media mills. KONA ...
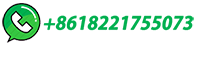
Automation and Robotics in Mining and Mineral Processing
Process automation systems in mineral processing plants provide important plant operational information such as metallurgical accounting, mass balances, production management, process control, and optimization. ... and the objectives are always broken down into particle size reduction, mineral liberation, and mineral separation …
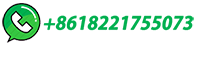