The impact of new technologies on the iron ore screening …
Abstract The iron ore screening process plays a pivotal role in determining the dimensions of pellets that enter the firing process of a pelletizing plant.
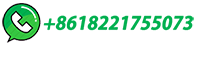
BENEFICIATION OF LOW/OFF GRADE IRON ORE: A …
BENEFICIATION OF LOW/OFF GRADE IRON ORE: A REVIEW . Dr. Rubina Sahin *1 *1 Department of Basic Science & Humanities, ... includes, crushing of ores, screening of proper size and grinding to liberate desire size and ensure feed of a correct ... In gravity concentration process, Jigging method is oldest one. This technique is app licable …
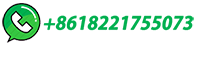
Advances in screening technology in the mining sector
Screening is mainly used in the mining sector in primary and secondary crushing systems (Fig. 3), coarse screening (scalping) in the pre-heap leaching process, fine screening and fine-grain elutriation in various process stages, enrichment of valuable materials, e.g. of the iron content in iron ore, grinding and screening circuits (open and ...
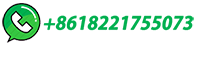
Characterization and Beneficiation of Dry Iron Ore
Characterization and Beneficiation of Dry Iron Ore Processing Plant ... terization results, two process flow sheets comprising wet screening followed by conventional gravity concentration and two ... concentration followed by the combination of grinding, classification, and froth flotation produced iron concentrate of 2.36% ...
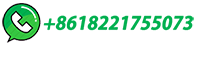
Energy and Environmental Profile of the U.S. Mining …
4.1 Process Overview 4.1.1 Iron Ore Mining There are two basic methods of mining iron ore. These are: • Surface mining or open-pit mining ... • Crushing & Screening • Grinding • Concentration • Agglomeration 4.1.2.1 Crushing and Screening Following blasting, the fragmented ore is loaded on a mining truck and hauled to the crusher for ...
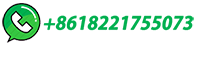
High Performance Process Development for Iron Ore Concentration
Download Citation | High Performance Process Development for Iron Ore Concentration | References on microwave energy use were reviewed and it demonstrated wide use of this kind of energy in ...
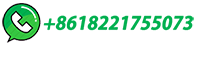
Iron ore beneficiation: an overview
Dry processing of iron ore: In dry processing of iron ore, ROM is generally crushed below 40 mm through three-stage crushing and thus segregated by screening into 10–40 and −10 mm fractions. For softer ore, tumbler index is generally low and hence lump ore is crushed below 10 mm to produce fine product. Yield from the plants has …
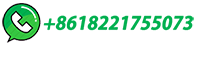
Ore Beneficiation
Use of indigenous microorganisms isolated from an iron ore deposits makes the process cheaper, flexible, and environment-friendly. ... the decrease in sulfate concentration corresponding to exponential bacterial growth was significant. ... Screening is an important step for dry beneficiation of iron ore. Crushing and screening is typically the ...
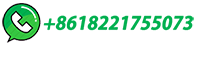
How does gravity concentration equipment work?
Gravity concentration spirals are optional in gold processing, used for carbon degritting. Iron ore Gravity concentration is used in iron ore processing. Following a range of screening processes, large assemblies of spiral concentrators are located downstream of a cyclone cluster and are used in classifying iron ore fines from waste.
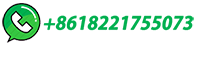
Iron Ore Beneficiation Process
The whole process of magnetic concentration as applied to the eastern Mesabi magnetites is a good illustration of the manner in which the various types of machines can be made to work together so as to produce a high-grade furnace product from an ore material containing only 25 per cent of iron in the form of magnetite.
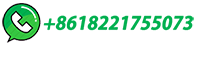
Measurement-Control for Crushing and Screening Process
Measurement-control for crushing and screening process is the measurement and control of key equipment and key process parameters to ensure the continuous, stable, and safe operation of ore crushing and screening.
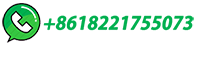
Heavy Media Separation Process
The HMS Heavy Media Separation Process Flowsheet FEED PREPARATION SCREEN. The heavy-media feed, crushed to the proper size, is screened, washed and drained on the Vibrating Screen to eliminate as much of the fines as possible. ... Iron ore; Tin ore; Chromite; Lead ore; Uranium ore; Diamond ground; ... The …
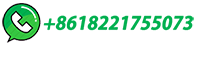
Low grade Iron Ore Beneficiation and the Process of Jigging
concentration, density, gangue material, gravity separation, iron ore beneficiation, Jig, Jigging, Low grade iron ore, Low grade Iron Ore Beneficiation and the Process of Jigging . Iron ore resources are getting consumed at an accelerated rate because of the growth in the production of iron and steel.
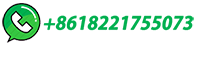
Iron Concentrate Particles
Iron ore concentrate is an output product from processed iron ores that have been milled (crush, grind, magnetic separation, flotation) to separate deleterious elements and produce a high-quality product. ... To clarify the dust concentration distribution of chute at the enclosed stockyard in steel works during the discharging ...
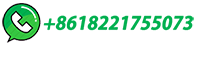
The impact of new technologies on the iron ore screening …
The iron ore pellet holds a pivotal role in the ironmaking process, enabling the utilization of high-grade ore and the upgrading of low-grade deposits [1]. This …
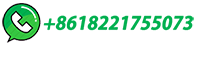
Processes for Beneficiation of Iron Ores – IspatGuru
Washing is the simplest iron ore concentration process that takes advantage of the high specific gravity and comparatively coarse size of the iron bearing minerals to separate them from the finer, lighter, siliceous gangue which is predominantly quartz and clay minerals.
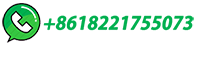
Iron ore beneficiation: an overview
The iron-making process requires high-quality raw materials, with Fe ≥ 64% and <2% alumina and silica each, to enhance blast furnace productivity at a given energy consumption rate.
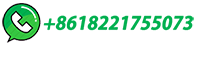
Eco-efficient and cost-effective process design for magnetite iron ore …
Assessment of different eco-efficient comminution process circuits to treat magnetite iron ore. Determination of the process operating costs and the capital costs for each process route. Comparison of the benefits of the different process routes from an economics point of view.
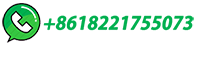
Iron Ore Pelletizing Process: An Overview | IntechOpen
The iron ore production has significantly expanded in recent years, owing to increasing steel demands in developing countries. However, the content of iron in ore deposits has deteriorated and low-grade iron ore has been processed. The fines resulting from the concentration process must be agglomerated for use in iron and …
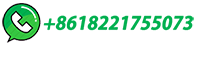
Mineral processing | Metallurgy, Crushing & Grinding
Mineral processing, art of treating crude ores and mineral products in order to separate the valuable minerals from the waste rock, or gangue. It is the first process that most ores undergo after mining in order to provide a more concentrated material for the procedures of extractive metallurgy.
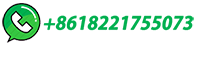
Advanced Analytics for Mineral Processing | SpringerLink
Chaurasia and Nikkam demonstrated the neural network application for modeling the performance of the gravity concentration process for iron ore fines. The trained model could capture, understand, and predict the grade, recovery, and separation efficiency of the process.
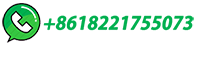
Transforming iron ore processing
In the recent past, iron ore resources from Brazil consisted of relatively high-grade iron ore, commonly processed via multi-stage crushing/screening, gravimetric concentration, magnetic separation, and reverse flotation. However, the high-grade iron ore reserves are in decline, resulting in the need to process the lower grade itabirite …
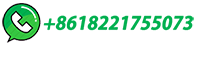
Iron Ore Concentration
Iron ore concentration equipment from Multotec, part of its mineral processing equipment, reduces downtime and maximises Capex returns. ... Iron ore concentration is a mineral-specific concentration process within the mineral processing industry. ... Different assembly methods make Multotec's static screens ideal for numerous screening ...
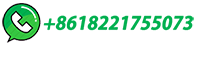
Wet High Intensity Magnetic Separators | Multotec
Wet High Intensity Magnetic Separators (WHIMS) from Multotec apply magnetism, matrix rotation and gravity to achieve para-magnetic materials separation. Applications include heavy minerals, ilmenite, manganese and iron ore (haematite) beneficiation; PGM upgrading as well as manganese recovery from slimes dams.
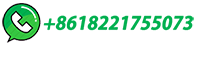
Mining 101: Direct shipping ore (and how to win the iron ore …
Once mined, the hematite is subjected to a rudimentary crushing and screening process, which segregates the ore into different-size fractions, enhancing its suitability for the blast furnace ...
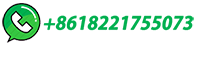
Concentration of Ore Definition, Types and Properties of Ore …
Concentration of Ore - Understand the properties of Ore and its types, Hydraulic Washing, Magnetic Separation, Froth Flotation Method, Leaching and more.
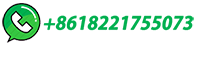
Iron Ore Screening
Iron Ore Screening Services: Our screening solutions manufacturing technique, combined with our in-depth understanding of mineral processing industry flow sheets, four decades …
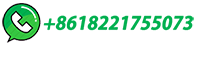
The six main steps of iron ore processing
Six steps to process iron ore. 1. Screening ... The concentrate collected from the middlings and tails after spiral gravity separation has a lower iron concentration (magnetite) so it must be further concentrated to achieve the customer's 65% Fe concentration. It is immediately directed to a magnetic separator circuit.
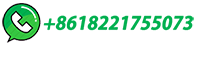
What is the Beneficiation Process?
Size classification will require screening, de-sliming and cycloning. In the case of a lower-grade iron ore, the beneficiation process includes activities such as crushing, milling, gravity or heavy media separation, screening and silica froth flotation. These activities will help improve the concentration of the ore and remove impurities.
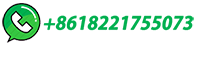
Iron Ore Processing, General
Making iron and steel from iron ore requires a long process of mining, crushing, separating, concentrating, mixing, agglomeration (sintering and pelletizing), …
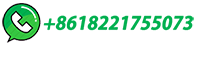