Construction Working and Maintenance of Crushers for …
Above figure shows sectional view of a typical gyratory crusher. Essentially, a gyratory crusher consists of a heavy cast-iron, or steel, shell/frame which includes in its lower part an actuating mechanism (eccentric and driving gears), and in its upper part a cone shaped crushing chamber, lined with wear resisting plates (concaves ...
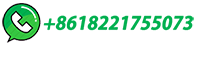
Gyratory Crusher
The gyratory crusher. The gyratory crusher shown in Figure 2.6 employs a crushing head, in the form of a truncated cone, mounted on a shaft, the upper end of which is held in a …
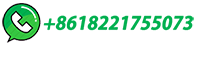
Gyratory Crusher l Introduce, Working Principle
Gyratory crusher is a new type of crusher which can replace fine jaw crusher or cone crusher, click, read more information about this crusher machine.
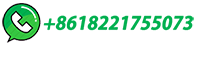
Working Principle of Crushers
Working Principle of Crushers. On left is a showing of the "standard gyratory with straight concaves" is a section through any vertical, radial plane in the crushing chamber of one of the intermediate sizes of the crusher. In order to understand the crushing action in such a chamber it is helpful to consider the process as though …
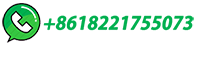
Gyratory Crusher
The majority of gyratory crushers are used as primaries, i.e. they receive the initial feed from the mine or quarry. The same type of crusher with chamber modifications is used …
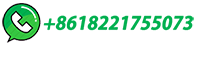
AMIT 135: Lesson 5 Crushing – Mining Mill Operator Training
Rule 1: Always use a jaw crusher if you can due to lower costs. Rule 2: For low capacity applications, use jaw crusher and hydraulic hammer for oversize. Rule 3: For high …
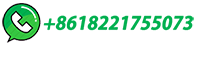
Type of crushers and their difference
gyratory crusher working principle animation. image credit by 911 Metallurgist. Similar to a jaw crusher, the gyratory crusher pulverizers the stones by placing them between two manganese steel plates and going straight down.
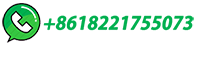
Simulation and optimization of gyratory crusher
Therefore, the working process of the gyratory crusher is taken as the specific analysis object, in this paper, the gyratory crusher performances, including the productivity, crushing force distribution, and particle size distribution, are explored by the DEM simulation.
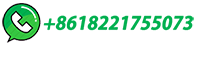
Jaws Crushers
The parameters used in the basic design of a gyratory crusher are nip angle, feed rate, feed opening, closed-side setting, work index, and horsepower. The combination of the …
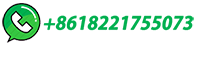
Gyratory Crusher (TS) for harsh environments
This Gyratory crusher (TS) is designed from the ground up, focusing on safety, maintenance and functionality — ready to meet your operational needs.
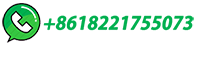
Gyratory Crushers | Mellott
How Do Gyratory Crushers work? The gyratory crusher is a heavy machine consisting of an iron or steel frame with an actuating mechanism and a cone-shaped chamber lined with wear-resisting plates.
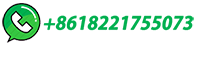
Superior™ MKIII 54-75 primary gyratory crusher
Superior™ MKIII 54-75 primary gyratory crusher gives higher throughput and less downtime to your primary crushing circuit. Read more here.
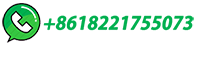
CG820 Primary Gyratory Crusher For Safe Crushing …
The automation system optimizes the performance of the crusher without overloading it, allowing you to get the most out of your crusher. It can also automatically adjust your crusher settings to compensate for crush-ing chamber wear – …
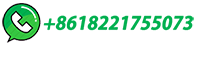
Gyratory Crusher (Gyratory Crushers Explained)
Primary Crushing Training Module. In this training module, Performance Associates International (PAI) covers the characteristics of a gyratory crusher that's designed to be …
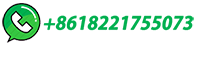
Superior™ MKIII Series primary gyratory crushers
Superior™ MKIII crushers bring higher capacity making this crusher the most capex efficient primary gyratory crusher in the industry. ... Hydraulic separation and individual lifting of shells creates a better environment for any …
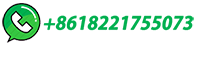
Superior™ MKIII 42-65 primary gyratory crusher
Superior™ MKIII 42-65 primary gyratory crusher brings high capacity and lower footprint to your mineral processing circuit's primary crushing. Read more here.
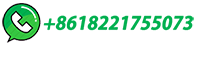
Crusher Close Side Settings
In the standard gyratory crusher this is accomplished very simply by increasing the thickness of the concaves at the top, ... Anyone who has seen hard granite boulders shoot out of a gyratory or jaw crusher, or has watched a wide-angle crusher at work on hard granite or trap rock, has had a visual demonstration of this physical fact.
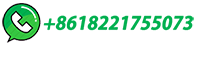
Industrial Solutions Gyratory crushers
The bevel gear and pinion of the crusher are both of a cyclo-palloid spiral type, which allows greater forces to be absorbed and greater drive power to be installed. A B C C D F E I J H K G Gyratory crusher Weights 1) Type Feed opening Mantle diameter (oversized) Speed of eccentric bushing Max. motor power Total weight of gyratory crusher ...
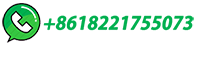
Gyratory Crushers
Gyratory Crushers The primary rock breaker most commonly used in large plants is the gyratory crusher, of which a typical section is shown in Fig. 5. It consists …
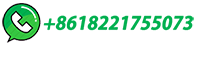
Unveiling the Advantages and Applications of Gyratory …
Gyratory cone crushers are essential machines in the mining and construction industries, used to crush hard and abrasive materials into smaller pieces. In this article, we will provide a detailed guide to gyratory cone crushers, including their working principles, advantages and disadvantages, types, and applications.
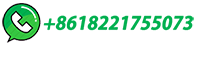
Superior™ MKIII 60-89 primary gyratory crusher
Superior™ MKIII 60-89 primary gyratory crusher gives less downtime and higher throughput with a mild capacity for your mineral processing circuit. Read more here.
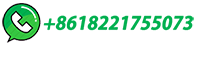
Heavy duty, maintenance-friendly Gyratory Crusher
The Gyratory Crusher "NT" incorporates all of the TC's heavy-duty design features (Heavy Cast-Steel Shell Sections, Forged Main Shaft and Countershaft, Robust Gearing, Generous Lubrication, Long-Life Bronze Components) and focuses on coupling these historical characteristics with updated maintenance-friendly features.
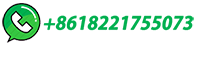
Gyratory VS Jaw Crushers: Advantages & Disadvantages
The jaw crusher, because of its box-frame construction, and simple toggle mechanism, is especially well adapted to extra heavy design for the crushing of extremely tough materials: in this respect it holds some advantage over the gyratory type, because the extra strength necessary for such work can be built into it at less cost than is …
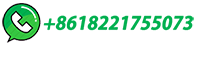
Construction Working and Maintenance of Crushers for …
A gyratory crusher uses a mantle that gyrates (rotates) within a cone shaped inner surface lined with wear resisting plates often called concaves. As the mantle gyrates within the …
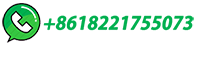
Jaw Crusher Working Principle
The jaw crusher is not so efficient a machine as the gyratory crusher described in the next paragraph, the chief reason for this being that its crushing action is confined to the forward stroke of the jaw only, whereas the gyratory crusher does useful work during the whole of its revolution.
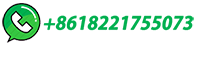
Safer, smarter, more powerful crushing | FL
Crush even the most challenging ore with the digitally-enabled TSUV gyratory crusher and achieve the lowest total cost per metric tonne in operation.
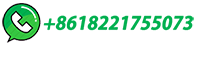
The Ultimate Guide to Gyratory Cone Crushers
Gyratory cone crushers are essential machines in the mining and construction industries, used to crush hard and abrasive materials into smaller pieces. In …
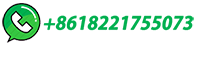
drawings and gyratory crusher working principle – stone …
How Gyratory Crushers Work Gyratory crushers may seem like complex machines, but their principle of operation is surprisingly straightforward. At its core, a gyratory crusher …
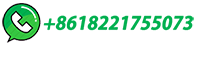
2. GYRATORY CRUSHERS
The gyratory crusher has been built in three types known respec- tively as the suspended-spindle, the supported-spindle and the fixed- spindle type. The second type, with the hydraulic piston as the sup ... direction when the crusher is working. The older long-shaft gyratory crusher which has the gear above the eccentric (Fig. 23) has another ...
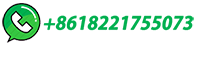