iron sponge h2s removal process and methods | by Rlalajm
The sponge iron system consists of: 1) a reaction vessel containing the bark impregnated with iron oxide (Fe2O3), 2) an atomization system to maintain the moisture level, 3) a support for the ...
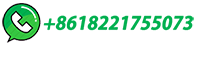
MV Technologies
MV Technologies designs both iron sponge based (H2SPlus™ Systems) and granular iron oxide based (SulfAx® Systems) for removal of hydrogen sulfide (H 2 S) from biogas. MV Technologies also designs and OdorFilter™ Systems to remove H 2 S vapors and sulfur-based odors.
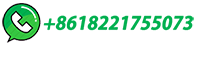
The HBI direct reduction process
As voestalpine, we plan to gradually switch from the coal-based blast furnace route to a green power-based electric steel route starting in 2027. This is made possible by a fundamental technological innovation. In addition to scrap and liquid pig iron, HBI is used, which is produced in the so-called direct reduction process.
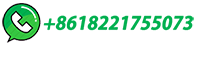
ENERGY-EFFICIENT TECHNOLOGY OPTIONS FOR DIRECT …
cope for energy-eficiency improvements by employing feasible WHR system. The WHR-based power generation, the most attractive among a. l, is economically viable for plants …
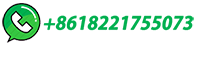
Low-carbon production of iron and steel: Technology options, economic
These processes operate with different feedstocks. The BF-BOF pathway converts raw iron ore to pig iron and then to steel HM, whereas EAF converts both steel scrap and sponge iron to steel HM. DRI converts raw iron ore to sponge iron, a porous, permeable, and highly reactive product that requires treatment with EAF before selling to …
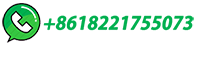
SulfaTreat H2S Removal Adsorbents | SLB
SulfaTreat adsorbents are used in H2S scrubbers as a nonhazardous alternative to iron sponge H2S removal media for natural gas processing of water-saturated gas streams and liquid streams.
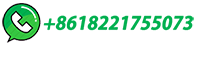
Sponge Iron | SpringerLink
Sponge iron means porous iron produced by direct reduction process.Direct reduction (DR) process is a solid-state reaction process (i.e. solid–solid or solid–gas reaction) by which removable oxygen is removed from the iron ore, using coal or reformed natural gas as reductants, below the melting and fusion point of the lump ore or …
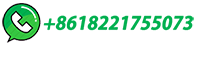
Iron Sponge
Iron Sponge is most frequently supplied with 15 pounds of iron oxide per bushel of product. Iron Sponge, which has been used for many years to treat other gas streams, is a very simple way to remove the corrosive, bad smelling H2S. It works to effectively remove the sulfide from the gas stream by forming stable iron sulfide, a solid.
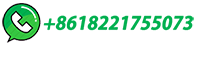
Sponge Iron
DRI, also known as sponge iron, is the product of reducing iron oxide in the form of iron ore and steel plant wastes into metallic iron, below the melting point of iron and typically in …
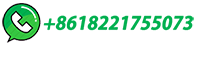
Enhanced refractory organics removal by sponge iron …
Sponge iron (SFe) is a zero-valent iron (Fe0) composite with a high-purity and porous structure. In this study, SFe was coupled with microorganisms that were gradually domesticated to form a Fe0/iron-oxidizing bacteria system (Fe0-FeOB system). The enhancement effect of the Fe0-FeOB system on refractory organics was verified, the …
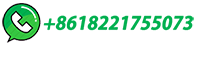
H2S Removal for Biogas Project
Iron Sponge Changeouts •Used Iron Sponge react exothermically with Oxygen •One site's changeout strategy: •Take vessel off line •Flood vessel with water •Bubble Air through vessel for a day •Change out vessels with new media
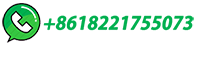
HYBRIT: SSAB, LKAB and Vattenfall first in the world with …
HYBRIT: New research shows hydrogen-reduced iron has superior properties. New research within the HYBRIT project, driven by SSAB, LKAB and Vattenfall, shows superior results on the properties and quality of the hydrogen direct reduced sponge iron (H-DRI) made using HYBRIT technology.
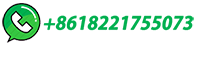
A review of ironmaking by direct reduction processes: …
2. Overview of DR processes Direct reduction processes reduce iron ore (in the form of lumps, pellets or fines) to the solid state using a reducing gas to produce Direct Reduced Iron (also known as sponge iron).
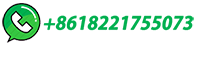
Low-Carbon Production of Iron & Steel: Technology …
These processes operate with different feedstocks. The BF-BOF pathway converts raw iron ore to pig iron and then to steel HM – while EAF converts both steel scrap and sponge iron to steel HM. DRI converts raw iron ore to sponge iron, a porous, permeable, and highly reactive product that requires treatment with EAF before selling to …
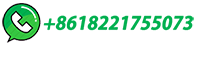
Sponge Iron | A-One Steel Group
Sponge iron is obtained by direct reduction (elimination of oxygen) of iron ore, without melting it in a blast furnace. Sponge iron is an intermediate iron product used as a substitute for steel scrap while producing steel through the electric induction furnace route, the entire production of sponge iron is consumed in-house for the manufacturing of MS …
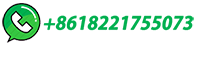
Sponge Iron | SpringerLink
Processes that produce iron by reduction of iron ore in solid state are generally classified as direct reduction (DR) processes and the products also referred …
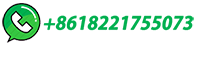
After more than a century, iron sponge still soaks up …
The iron sponge technique originated in Europe more than 100 years ago, and the earliest operators used a naturally occurring form of hydrated iron oxide known as bog iron or bog ore. As refinements were made in the process, it was found that more efficient sulfur removal could be attained by uniformly distributing the iron oxide hydrate …
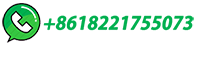
ENERGY-EFFICIENT TECHNOLOGY OPTIONS FOR …
3.0 Energy-efficient Technologies in Direct Reduction of Iron Process 17 3.1 Waste Heat Recovery for Power Generation 18 ... the Indian Sponge Iron Industry in 2019–20, which was undertaken by the Joint Plant Committee set up under the aegis of the Ministry of Steel (GOI). The Association provides a platform for knowledge sharing
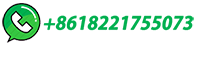
Powder Production Technologies
The sponge iron process. The longest established of these processes is the sponge iron process, the leading example of a family of processes involving solid state reduction of an oxide.
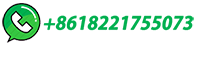
Direct reduced iron process
The reduction gases only dissolve oxygen from the iron ores. This causes the iron ores to crack on the surface. The appearance resembles a porous sponge, which is why the deoxidized and thus strongly ferrous iron ore is also called sponge iron. Sponge iron is a highly ferrous ore from the direct reduced iron process!
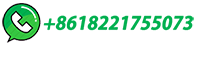
Iron Sponge Process
The Iron Sponge Process, a technology used for removing hydrogen sulphide (H2S) from biogas, can potentially use various biodegradable wastes as the supporting material for the H2S adsorption media, providing improved flexibility and cost-effectiveness. In this study, ground garden waste, digested garden waste, and spent tobacco were evaluated as …
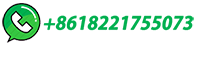
ENERGY-EFFICIENT TECHNOLOGY OPTIONS FOR …
The Sponge Iron Manufacturers Association (SIMA) acts as an apex body to promote and protect the growing needs of the industry and plays a vital role in bringing together the DRI industry, the Government
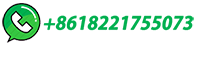
A review of the sponge iron process for the storage and …
Two types of processes could be envisioned for the application of sponge iron technology to the storage and transmission of marine or wind energy: Process 1 produces hydrogen from wind or marine energy at a remote location. The sponge iron and iron oxide remain onsite (static storage), and the iron oxide is used to absorb surplus …
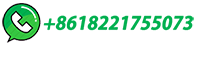
Sponge Iron
Iron oxide ores extracted from the Earth are allowed to absorb carbon by a reduction process. In this natural reduction reaction, as the iron ore is heated with carbon, it …
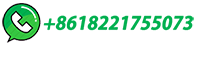
Iron Sponge
The iron sponge process uses the chemical reaction of ferric oxide with H2S to sweeten gas streams. This process is applied to gases with low H2S
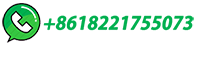
Sponge Iron
Direct reduction iron or sponge iron is an old method for producing hydrogen (Milne et al., 2006; Peña et al., 2010; Biljetina and Tarman, 1981) that was replaced by more efficient and economic processes.Recently, the interest in sponge iron as a hydrogen production process has grown again, although the technology still has some major technical and …
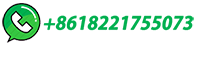
What Becomes of Spent H2S Removal Media?
Although our patented BAM™ iron sponge media is often the most cost-effective solution, there are system designs for which granular media or activated carbon media make more sense. MV Technologies provides ALL solutions and will help evaluate the best technology (or combination of technologies) for each customer's specific …
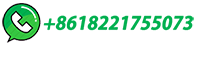
WHAT IS SPONGE IRON AND HOW IS IT MADE?
Sponge iron, also called direct reduced iron (DRI), is made from directly changing iron ore (in any form whatsoever) to iron by a cutback gas or carbon, produced from natural gas or coal.
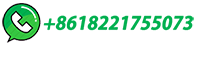
SPONGE-IRON
Sponge Iron. SIPL is operating 4 x 100 TPD Direct Reduced Iron Rotary Kilns for production of 2000 TPA Sponge Iron at Purulia, using the proven German SL/RN technology.
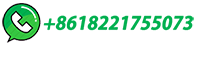
(PDF) i) Direct Reduced Iron: Production
In book: Encyclopedia of Iron, Steel, and Their Alloys (pp.pp 1082-1108) Chapter: i) Direct Reduced Iron: Production; Publisher: CRC Press, Taylor and Francis Group, New York.
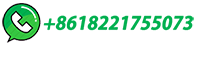