Exploring Steel Production: A Comprehensive Visual Process …
Steel making is a sophisticated process that turns iron ore into steel, involving methods like the Blast Furnace and Electric Arc Furnace to produce various grades of steel. The industry emphasizes sustainability by using additives and recycled materials while ensuring quality through rigorous testing for diverse applications.
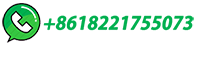
Lithium iron phosphate comes to America
In November, the start-up Nano One Materials finalized the purchase of the old Phostech LFP plant in Montreal, promising to introduce a manufacturing process that will require less energy and ...
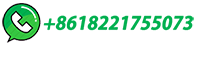
Pig Iron Manufacturing Process
Pig Iron Manufacturing Process. Previous. Next. Table of Contents. At the beginning of the use of the electric furnace, for the manufacture of calcium carbide and ferro-alloys, experimental work was conducted in it upon the production of steel from iron ore. For many years steel and wrought iron have been produced directly from ore on a …
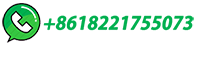
Evolution of Ironmaking Techniques | From Ancient to …
The Bessemer process involved blowing air through molten pig iron to oxidize impurities and reduce carbon content, resulting in the production of high-quality steel.
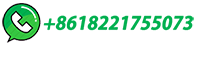
How Is Cast Iron Made? | Sciencing
Cast iron that has not cooled evenly produces a low-quality cast. Other problems faced during the cast iron process include contamination of the iron, gas porosity (the forming of bubbles in the iron), and problems with the fluidity of the metal. The casting process is an art that must be examined and experienced to be fully understood.
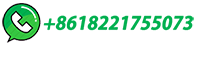
12.5 Iron And Steel Production
The molten iron and slag are removed, or cast, from the furnace periodically. The casting process begins with drilling a hole, called the taphole, into the clay-filled iron notch at the base of the hearth. During casting, molten iron flows into runners that lead to transport ladles. Slag also flows
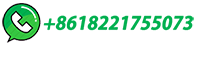
Infographic: the Iron and Steel Manufacturing Process
Overview of the products that make each stage of the iron and steel manufacturing process possible, from incoming raw materials to the final coating line.
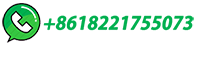
Iron rods – Prices, uses, types, manufacturing process
The manufacturing process of iron rods involve several meticulous steps to ensure quality and strength. Here's a simplified breakdown of the steps: Iron rod manufacturing process step-by-step. Step 1: Raw material procurement.
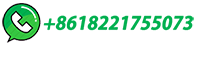
Metal Forging
Metal forging is a metal forming process that involves applying compressive forces to a work piece to deform it, and create a desired geometric change to the material. The forging process is very important in industrial metal manufacture, particularly in the extensive iron and steel manufacturing industry.
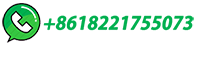
(PDF) iron-steel making From start to finish
Presentation will help to provide basic principle and brief overview of iron making to steel making process. which is cover each and every stage of iron and steel making process along with ...
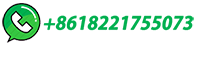
Cast Iron Explained: How's It Made, Casting Methods, Types …
The manufacturing process of cast iron is also named cast iron casting. There are several casting methods used to make cast iron, each with its own advantages and disadvantages. Here are some of the most common casting methods used for cast iron:
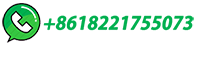
Manufacturing Process From Ore To Stainless Steel: A Step …
The conversion of iron into steel is a critical step in the stainless steel manufacturing process. This process involves carefully controlling the chemical composition and physical properties of the iron to achieve the desired steel characteristics.
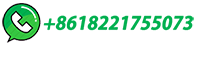
A Guide to Cast Iron, Ductile Iron and Steel Manufacturing Process
Dive into learning about the cast iron, ductile iron, and steel manufacturing process to learn more about the top materials to use for your next project.
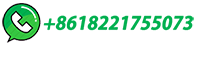
How Cement is Made
While each cement plant may differ in layout, equipment, and appearance, the general process of manufacturing portland cement is the same: crushed limestone and sand are mixed with ground clay, shale, iron ore, fly ash and alternative raw materials.
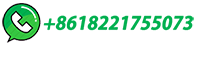
From Ore to Iron with Smelting and Direct Iron Reduction
Ironmaking 101 – From Ore to Iron with Smelting and Direct Iron Reduction. Figure 1: Steelmaking byproducts for blast furnace (BF), basic oxygen furnace (BOF) …
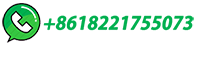
How It's Made | Lodge Cast Iron
Lodge creates its diverse line of cast iron cookware through an age-old process called sand molding. A proprietary mix of molten pig iron, steel and other ingredients are poured into a mold made of sand.
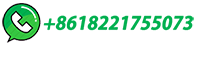
Manufacturing Process | AMERICAN
Beveling the Pipe. The final process before quality assurance and testing. Beveling prepares the ends of the pipe to a 30-35-degree angle to prepare it for welding at the construction site.
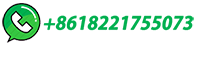
How iron is made
Iron ore is converted into various types of iron through several processes. The most common process is the use of a blast furnace to produce pig iron which is about 92 …
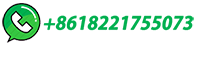
(PDF) Basic Concepts of Iron and Steel Making
This book presents the fundamentals of iron and steel making, including the physical chemistry, thermodynamics and key concepts, while also discussing associated problems and solutions.
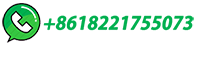
Steel Manufacturing Process
The process starts in the center of the wheel with the three main ingredients of iron in the form of iron ore, coke and lime, which are fed into a blast furnace to produce molten …
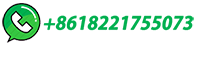
The Steel Manufacturing Process — How is Steel Made?
Today, the manufacturing of steel is done by using one of these two methods: Blast furnace: The blast furnace process, also known as the basic oxygen process (BOP), combines raw iron ore with small amounts of steel scrap metal into a furnace. Then, pure oxygen is blown into the furnace, raising its temperature.
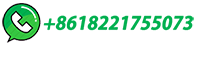
6 Steps of the Steel Manufacturing Process | Dixon
Steel Manufacturing Process The steel manufacturing process can be divided into six steps: Making the iron, primary steelmaking, secondary steelmaking, casting, primary forming, and secondary forming. Step 1: Making the Iron. Steel is a metal alloy made of iron and carbon. Thus, the steel manufacturing process starts by …
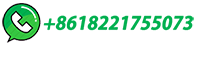
Manufacturing Process of Iron Wheel Rims for Vehicles
Explore the factory production process of iron wheel rims for vehicles. Watch as raw materials are transformed into durable and precise wheel rims, showcasing the advanced techniques and machinery ...
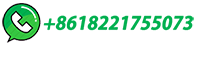
How Is Ductile Iron Pipe Made?
Quality checks are preformed throughout each step of the process to ensure our facilities are making quality Ductile iron pipe. ... McWane Ductile has just finished producing a series of 20 videos that break down each step of the manufacturing process into video clips of 60 seconds or less. ... Building Iron Strong Utilities for Generations.
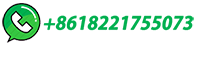
Steel Making Process – Complete Overview with Flowchart
4. The Crucible Steel Making Process. In the crucible steel making process, mixtures of wrought iron, steel scrap and ferromanganese are melted down with charcoal in an air tight crucible.Other ferro alloys may be added when alloy steel is produced by this process. In the crucible process, carbon is added to the iron as the carbon content of wrought iron …
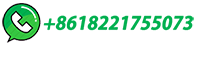
Iron processing | Definition, History, Steps, Uses, & Facts
Iron processing - Smelting, Refining, Alloying: The primary objective of iron making is to release iron from chemical combination with oxygen, and, since the blast furnace is …
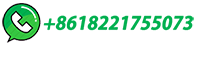
Exploring the Steelmaking Process: From Ore to Alloy
Discover the intricate process of steelmaking, from extracting iron ore to refining it into versatile steel alloys & the future innovations reshaping the industry.
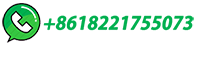
Iron and Steel Manufacturing | Department of Energy
Iron and steel manufacturing in the United States produces 7% of industrial emissions. Steelmaking is energy- and emissions-intensive, requiring high process temperatures and a source of carbon to drive reactions. Generating heat and the chemical reactions that occur during steelmaking processes both produce significant emissions.
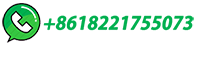
Exploring Steel Manufacturing: A Step-by-Step Insider Guide
Steel manufacturing is a complex process that transforms iron ore into steel, involving precise heating and mixing to create different grades for various applications. The journey includes primary methods like Basic Oxygen Steelmaking BOS and Electric Arc Furnace EAF, followed by secondary refining to meet specific quality …
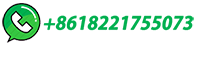
Current and future lithium-ion battery manufacturing
The roll-to-roll manufacturing processes such as coating, calendering, and slitting have a high throughput of over 35 m/min. However, processes like vacuum drying and formation/aging are time-consuming (up to 3 weeks) because of their strict moisture level restriction and sensitive chemical reaction (Heimes et al., 2019a).
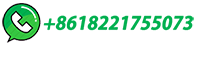