(PDF) Zinc Oxide—From Synthesis to Application: …
The direct (American) process involves the reduction of zinc ore by heating with coal (such as anthracite), followed by the oxidation of zinc …
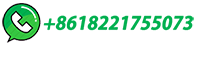
Zinc Ore
Lead. A. Mohamad Ghazi, James R. Millette, in Environmental Forensics, 1964. 4.3.2 Mining and Production of Lead. Lead and zinc ores often occur together, and there are a large number of countries that mine and process lead ore, making it among the most widespread metals in terms of primary production (Kesler, 1994).Most of lead mining is done by highly mechanized …
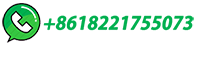
Zinc Oxide
In 1981, the world production of zinc oxide was about 0.8 Mt with a projected annual growth rate of 3.5%. 1. Processing. Zinc oxide is prepared commercially by two …
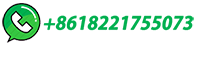
Nanostructure of ZnO Fabricated via French Process and its …
The rich nanostructural diversity of commecial zinc oxide, fabricated via French process, is investigated. FESEM images of ZnO nanostructures reveal nanorods, nanoplates, …
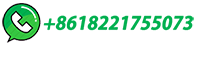
Novel 'green' zinc ore refining process | Energize
A concept study into the development of a mini-scale, simple, green and energy-efficient process to recover pure zinc from polymetallic South African ore concentrates is forging ahead at the University of Cape Town's (UCT's) Department of Chemical Engineering under the leadership of Professor Jochen Petersen. Processing zinc into a pure form is complicated by …
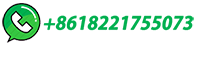
Exploring the potential health and ecological damage of lead–zinc …
The methodological framework of this study mainly comprised goal and scope definition, data collection, inventory construction, LCIA, social economic impact assessment, and correlation analysis as shown in Fig. 1.The goal of this study is to quantify the potential environmental and economic impacts of lead–zinc production activities via a macro-level …
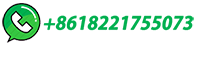
American Process Grades of Zinc Oxide Provide the Highest …
Zinc oxide has long been used as a fungistat in the coatings industry and our American process grades are particularly suited to provide the highest level of performance and stability. There are two processes used in producing pigment grade zinc oxide, the American process and the French process.
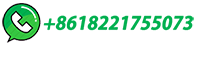
Experimental and theoretical evaluation of zinc recovery from zinc
In the present study, the production process of zinc sulfate from the zinc oxide ore was experimentally investigated. The effect of main operating condition such as weight ratio of sulfuric acid ...
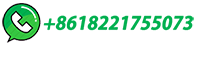
Zinc oxide production by French process, p. 2
Dear Mr Shaurya Mittal. Zinc oxide was discovered by Cramer in 1750 while the French process was popularized by LeClaire in 1844 during when he mass-produced ZnO for white oil paint. Pure zinc metal was used then. The use of cheaper zinc dross has been …
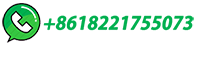
92 years of zinc oxide: has been studied by the scientific …
2.1. The indirect (French) process. From 1840 to 1850, the indirect process, called the French process, was developed to meet the need for ZnO in paints [51]. In 1850, …
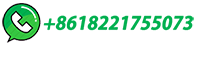
A PROCESS FOR THE MANUFACTURE OF ZINC OXIDE USING ZINC
2) Indirect process also known as 'French' process In the 'French' process, pure zinc is boiled in retorts on crucibles, and vapours of zinc are oxidized, sucked by exhaust fans in to bag houses and then collected. 3) Wet process also known as 'secondary' zinc oxide In this process, by product zinc hydroxide and carbonates are washed and ...
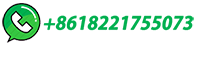
Technical Support Document for the Zinc Production …
estimate includes both process-related emissions (CO2 and CH4) resulting from zinc production operations at the 4 facilities identified as process emissive in Table 1, and combustion emissions (CO 2, CH 4 ) from all 9 facilities. 1 Process-related GHG emissions were 528,777 mtCO 2 e (62
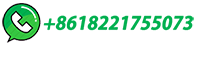
Zinc oxide production by French process, p. 2
Weight gain for dross and other scrap is defined by, {wt of zinc oxide =%metallic zinc content * 1.2} 4)Raw materials:- French process is concern only to metallic zinc content in raw material and raw material is deciding factor for quality of zinc oxide formed.
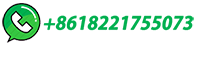
Chemicals | ZINC. International Zinc Association
In the French (indirect) method, zinc oxide is produced by the combustion of zinc metal. When zinc oxide is extracted from zinc ore or smelter by products (e.g., using oxidized zinc) it is called the American or the direct method. ... the material and production process are more cost-effective and safer. Chemicals. ... P: +32 2 776 0070 E ...
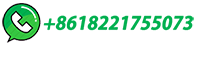
Zinc Oxide French Process: How Useful Is It?
In the Zinc Oxide French process, the quality of a particular zinc can be determined based on several quality control metrics. First, zinc oxide is heated at the medium level to make it volatile. The vapors from the Zinc Oxide chemical are drawn to a controlled chamber to react with the oxygen that will produce the final product.
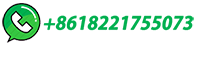
23.2: Pyrometallurgy
A plot of the temperature dependences of the free energies of these reactions, superimposed on similar plots for the oxygen removal reactions (ref{2.4}) is called an Ellingham diagram (Figure (PageIndex{2})). For a given oxide MO to be smeltable, the temperature must be high enough that reaction (ref{2.4}) falls below that of at least one of the oxygen-consuming reactions.
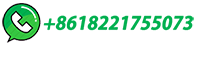
Zinc processing
Zinc processing - Compounds, Refining, Alloying: Two main processes are employed for producing zinc oxide, a white powder. In the direct, or American, method of manufacture, zinc ores (or residues) are heated in air with coke or anthracite, and the resulting zinc vapour is subjected to controlled oxidation. In the indirect, or French, process, the zinc vapour to be …
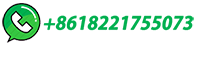
Zinc solvent extraction in the process industries …
Capital and operating cost estimates were also projected for plants up to 4000 t/d of processed ore. Recoveries of 99% for zinc, 98% for lead, and 96% for copper were achieved in laboratory tests ...
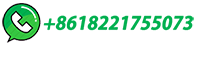
Zinc: Production, Price Drivers and Why It's Valuable
The process of primary production involves four steps: Ore concentration; Smelting; Refining; Alloying; Ore Concentration. A series of steps called froth flotation breaks down the ores into particles with greater concentrations of zinc. First, the ore is ground into a fine powder and placed in flotation tanks with water, pine oil and chemicals
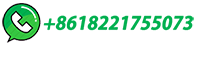
Study underway into a novel 'green' zinc ore refining process
A concept study into the development of a mini-scale, simple, green and energy-efficient process to recover pure zinc from polymetallic South African ore concentrates is forging ahead at the University of Cape Town's (UCT's) Department of Chemical Engineering under the leadership of Professor Jochen Petersen.
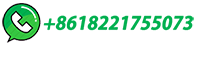
Zinc oxide particles: Synthesis, properties and applications
The purified zinc sulfate solution was used to prepare active zinc oxide (97.04 %) by direct precipitation at a molar ratio of CO 3 2– /Zn 2+ of 1.15 and a temperature of 50 °C. The average particle size of the product was 21.95 nm, which …
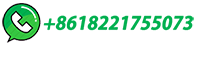
Zinc oxide particles: Synthesis, properties and applications
1. Introduction. Zinc oxide has been used in diverse applications for thousands of years [1] and could reasonably be considered to be a mature engineering material [2] with …
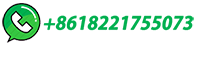
Hydrometallurgical processes for Waelz oxide valorisation …
The ZnO market supposes 100,000 tonnes per year, and it is fabricated through three different technologies: French process, ... During SHG zinc production process some valuable by-products are obtained. ... Leaching kinetics of low grade zinc oxide ore in NH 3-NHCl 4-H 2 O system. J. Cent. South Univ. Technol., 15 (2008), ...
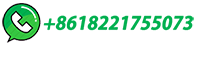
Zinc Oxide—From Synthesis to Application: A Review
2.1. Metallurgical Process. Metallurgical processes for obtaining zinc oxide are based on the roasting of zinc ore. According to the ISO 9298 standard [], zinc oxide is …
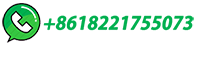
Zinc Mining and Processing: Everything you Need to Know
The major types of zinc ore deposits are generally found to be sediment-hosted, volcanic-hosted, intrusion-related, Broken Ore type or Mississippi Valley Type. The Zinc Mining Process. The zinc mining process is conducted primarily underground, with more than 80 percent of all zinc extracted beneath the Earth's surface.
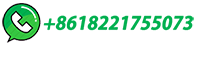
Zinc | SpringerLink
The important ores of zinc are sphalerite (ZnS) and marmatite [(ZnFe)S]. Less common ores are zincite (ZnO), smithsonite (ZnO.CO 2), and franklinite.The oxidized zinc ore calamine (Zn 2 O.SiO 3) was at one time the main source of zinc.Zinc ore is widely distributed, the most important sources being USA, Canada, Australia, Mexico, Germany, Poland and India.
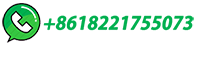
SKORPION ZINC
PRODUCTION OUTLOOK: FY2018 In FY2018, Skorpion is expected to produce approximately 90kt of zinc. This is expected to rise, due to the Pit 112 expansion, to approximately 130kt by 2020. The Skorpion Refinery – unlike most zinc refineries globally, which refine concentrate produced from zinc sulphide ore – is currently configured to treat
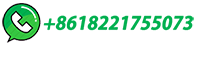
Chemistry: 2) Explain the different process that are involved …
Chemistry: 2) Explain the different process that are involved in the extraction of zinc from its ores. Open in App. Solution. Verified by Toppr. ... (2) calcination of zinc ore. View Solution. Q2. How can Zinc metal be extracted from Zinc oxide ore? Suggest a chemical reaction and explain the key concept involved in the process. View Solution. Q3.
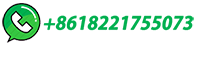
Nanostructure of ZnO Fabricated via French Process and
Chemistry and morphology of zinc fertiliser products While ZnSO 4 fertilisers tend to have a very consistent composition (sold as ZnSO 4 .7H 2 O or ZnSO 4 .H 2 O), ZnO fertilisers can have a large ...
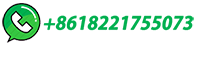
SOLVENT EXTRACTION IN ZINC PRODUCTION FROM A …
approaching full production of 150 000 t/a of special high grade zinc (> 99.995 % Zn). The orebody presents unique challenges, containing fluorides and chlorides that cannot be
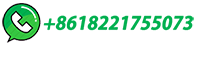