Understanding Jaw Crusher Parts and Their …
Learn about the different components of a jaw crusher and their respective functions. This article covers everything you need to know about jaw crusher parts, from the movable jaw to the flywheel.
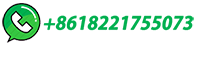
Jaw Crusher: Range, Working Principle, Application
Jaw crushers are used as primary crushers, or the first step in the process of reducing rock. They crush primarily by using compression. The rock is dropped between two rigid pieces of metal, one of which then moves inwards towards the rock, and the rock is crushed because it has a lower breaking point than the opposing metal piece.
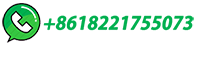
What Is a Jaw Crusher? Here's How It Works
A jaw crusher essentially crushes large rocks to a more usable size. They're typically the first-line machinery used in the material reduction for several …
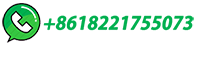
Jaw crusher
Description. PE600×900 jaw crusher is used in the first process of coarse and medium crushing various minerals and rocks. The advantages of high efficiency, strong crushing capacity and low investment cost make jaw crusher popular in mining, metallurgy, and other industries.
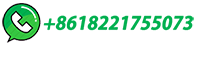
The Ultimate Guide to Jaw Crushing Machines: Types
Discover everything you need to know about jaw crushing machines, from the various types such as single and double toggle, hydraulic and portable models, to their working principles, advantages, and disadvantages. This comprehensive guide also provides expert tips on maintenance and selecting the right machine for your specific …
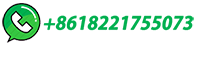
JAW CRUSHER SERIES
The jaw crusher line is designed for the motor sizes listed in RPG and technical specifications. This means that for harder materials, the crusher will have to be operated at larger settings to avoid overload of drive and/or motor. Using oversized motors will lead to radically shorter crusher life and various mechanical problems.
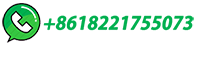
Jaw Crusher: What Is It & How Does It Work?
What Is A Jaw Crusher, And How Does It Work? A jaw crusher is a machine that breaks down large rocks into smaller pieces of rock, gravel, or dust. It does this by placing two …
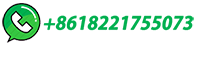
"Computer Aided Design of Jaw crusher"
3.2 Crushing Process 29 3.3 Wear Analysis 31 Chapter 4 Design of flywheel for Jaw crusher 4.1 Flywheel 32 4.2 Role of flywheel in a jaw crusher 32 ... Jaw crusher movement is guided by pivoting one end of the swinging jaw. and an eccentric motion located at the opposite end. [4]
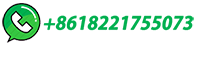
Selecting the right crusher for your operations
Like the jaw crusher, the cone crusher provides a relatively low cost crushing solution, but there are application drawbacks that may make another crushing solution more appealing. ... While tonnes per hour are critical, another production factor that significantly affects the crusher selection process is the number of end product ...
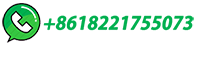
Process description of barite crushing plant
Home » News » Process description of barite crushing plant. 7 Jun 2024; Barite is a heavy, white or colorless mineral that is used in a variety of applications, including drilling fluids, paint and pigment fillers, and X-ray shielding. ... This is typically done using a jaw crusher or a gyratory crusher. 2. Secondary Crushing.
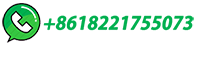
Introduction to Jaw Crushers: Understanding the Basics
At the heart of every jaw crusher lies a set of precisely engineered components that work in harmony to facilitate the crushing process. The primary elements include:
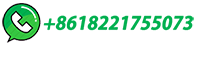
Blake Jaw Crusher
A sectional view of a jaw crusher which incorporates the Blake double-toggle mechanism is shown below. The Blake crusher in common with all machines of the jaw family is built into a rectangular frame, at one end of which is located the crushing chamber; in fact, the end of the box-frame constitutes the stationary jaw. The movable …
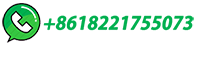
Industrial Solutions Jaw crushers
Single-toggle jaw crushers are characterized by the swing jaw being suspended directly on the eccentric drive shaft and the lower part of the swing jaw being braced against the crusher frame by means of a toggle plate.
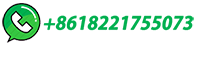
Jaw Crusher
The jaw crusher is widely used in many fields where the breaking strength is less than 320 MPa like mining, smelting, building material production, highway, railway, water …
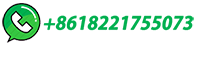
The Ultimate Guide to Jaw Crushing Machines: Types
The crushing process in a jaw crusher begins with the feeding of the material into the crushing chamber. The material is crushed between a fixed jaw and …
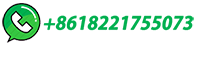
In- depth – Components of a Jaw Crusher | PROPEL …
The jaw crusher is one of the most admired and most sought after equipment from the house of Propel Industries. For the benefit of newcomers in the industry, here is an explainer of the various components of the Jaw crusher. A jaw crusher consists of Crusher Body Pitman Jaw plate Rear end frame Eccentric shaft
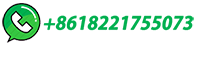
Jaw Crusher Explained
Jaw crushers are classified based on the position of the pivoting swing jaw. There are threemain jaw crusher types: 1. Blake crusher – the swing jaw is fixed at the lower position. 2. Dodge crusher – the swing jaw is fixed at the upper position. 3. Universal crusher – the swing jaw is fixed at …
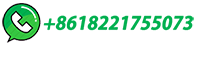
Jaw Crusher Diagram: Simplified Guide
Unravel the inner workings of jaw crusher diagram and gain valuable insights into its functionality. Visit blog for a detailed explanation.
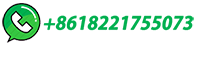
Types of Crushers: What You Need to Know
Crushing is an versatile process and the kind of crusher you need depends on the 'stage' of crushing. The three main stages of crushing are primary, secondary, and tertiary - all of which have their own unique benefits. ... Often smaller and more expensive than a jaw crusher, gyratory crushers are suitable for larger amounts of materials when a ...
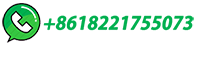
Small Crushing Plant Operating Guide
Detailed Process Description and Control of our EXAMPLE small crushing plant. ... jaw crusher discharge chute at conveyor #1, cone crusher discharge chute at conveyor #1, transfer point between conveyors #1 and #2, screen feed chute, cone crusher feed chute, and the screen undersize discharge chute at conveyor #3. The collector …
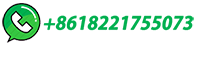
(PDF) DESIGN AND OPERATIONS CHALLENGES OF A SINGLE TOGGLE JAW CRUSHER
A review on the design and operations challenges of a single toggle jaw crusher is presented. Strength and fracture toughness of the material to be crushed are intrinsic properties that determine ...
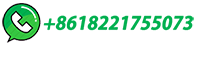
Ranger® Jaw Crusher Plant
Astec offers a complete line of compact track-mounted plants including jaw crushers, impact crushers, cone crushers, screens and trommels.The Ranger® line of track-mounted units serves a variety of markets.
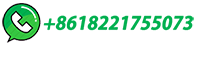
What Are Jaw Crushers and How Do They Work?
How do jaw crushers work? Jaw crushers use compressive force to break down large materials into smaller, more manageable pieces. It has two crushing jaws (one is …
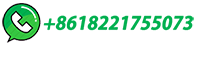
Jaw Crusher Working Principle
A jaw crusher size is obtained by looking at its feed opening (gape) and length. As an example, a monster 7959 of 79″ x 59″ (2m x 1.5m) will have its fixed jaws …
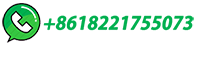
Downstream Crushing Options for Secondary, Tertiary …
Each of the crushing stages plays an important role in the production process, whether it be material reduction for further handling downstream or final product sizing. Selecting the right crusher for each stage of the crushing process depends on an understanding of the material to be crushed and the site's production goals.
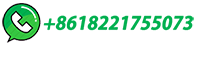
Solved Equipment design for process given the following
Question: Equipment design for process given the following description.Mini-Project20CHME18I 2020/2021 The manufacturing process include equal feed of 150 ton/day of particle size 50 cm of clay and 60 cm of lime stone (L.S) these feed are feed to separate jaw crusher and the product from both crushers is screened over an ideal …
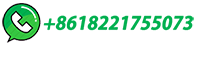
Intro to Aggregate Equipment: The Jaw Crusher
One of the most common types of aggregate equipment that you'll encounter is a jaw crusher, also sometimes called an impact crusher. The only difference between the two types is the types of rock they are designed to crush.
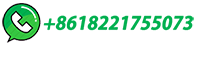
Mineral Crushing Operator Job Description, Duties, Skills
Mineral crushing operators operate and monitor crushers and other machines to crush materials and minerals. They move stones to the crushers, fill the machines with minerals, monitor the crushing process and ensure that the end products meet requirements.
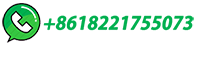
Jaw Crushers – MEKA
Jaw crushers reduce large rocks or ore by means of compression. Mechanical pressure is applied using the crusher's two jaw; one is fixed while the other makes an eccentric movement.
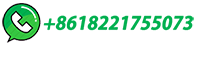
Crushing Plant Flowsheet & Design-Layout
From the following crusher application descriptions, it can readily be seen that each crusher has its own designed level of reduction. The range of feed sizes and product sizes, for each crushing stage, somewhat overlaps into the succeeding and preceding stages.
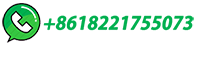