Below the surface: Setting up an underground primary jaw crusher
Jaw crushers are the most common solution in underground applications when the throughput is below 1000 tonnes per hour, depending somewhat on the scalping solutions. Above 1000 tph, primary gyratory crushers are an option. After the throughput reaches 2000 tph, jaw crushers are very rare, with the exception of a parallel plant layout.
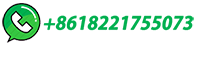
Primary Jaw Crusher – Everything You Need to Know
Learn everything you need to know about primary jaw crushers in this comprehensive guide. Discover how they work, their applications, and where to buy them from reputable sources. Whether you're in the mining or construction industry, this guide will help you make an informed decision when it comes to selecting the right primary jaw …
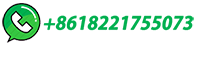
What Are Jaw Crushers and How Do They Work? | Oreflow
The primary applications for using jaw crushers are: Crushing different kinds of ore; Reducing building rubble to pieces; ... An adjustable wedge system allows for multiple adjustments of the crusher settings. All parts of the adjusting system can be easily accessed and requires little to no maintenance. The parts can also be replaced in the ...
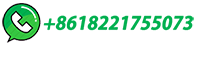
Primary Crushing: A Comprehensive Guide
The different hardness, how abrasive it is, and the size of the material all play a big part in deciding on the primary crusher. For instance, jaw crushers work really well with hard and abrasive stuff like granite and limestone.
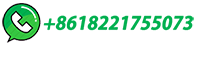
In- depth – Components of a Jaw Crusher
1. Crusher Body. The design of the crushing body ensures that it is capable of exhibiting resistant to bending stress even when the crushing hard materials. 2. …
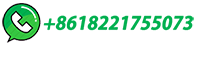
Primary Crusher Optimisation for Improved Comminution
the primary crusher. DEFINITION The primary crusher selection is the key to the success of any mining operation that involves the reduction in size of the ore. The crushing plant can be provided with almost any type of primary rock crusher. The rock/ore determines the type of crusher. The plant capacity determines the size of the crusher.
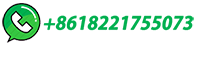
Crusher
13.3.1.1 Primary Crusher. Primary crushers are heavy-duty rugged machines used to crush ROM ore of (−) 1.5 m size. These large-sized ores are reduced at the primary crushing stage for an output product dimension of 10–20 cm. The common primary crushers are of jaw and gyratory types.
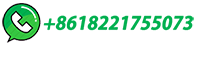
McLanahan | Vibrating Grizzly Feeders
The main purpose of a Vibrating Grizzly Feeder is to feed a primary crusher in a primary application. Vibrating Grizzly Feeders reduce the amount of material going into the crusher by scalping out the product size ahead of the crusher.
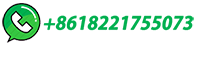
Primary Crusher vs. Secondary Crusher: Understanding Their …
The function of the primary crusher is to break down the larger rocks and stones into manageable sizes, while the function of the secondary crusher is to further refine these sizes into the desired product.
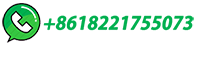
How Does a Jaw Crusher Work? A Simple Guide
The material from the primary crusher is fed into secondary crushers for a more uniform and finer size. Tertiary Crushing: ... Other crucial parts include the toggle plate, a safety device that serves as a fuse in the system, preventing damage to the crusher when uncrushable material is fed into it. Then there's the eccentric shaft itself ...
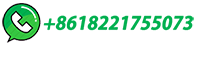
Understanding Cone Crusher Parts Names, Functions, and …
Description: This article provides a comprehensive guide to understanding the different parts of cone crushers, their functions, and the importance of proper maintenance. It covers various types of cone crusher parts, common issues and solutions, and future developments in the industry.
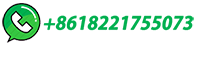
What Is Primary, Secondary, and Tertiary Crushing?
Primary crushing is the first stage of material reduction and can sometimes be the only stage needed to generate the desired product for a job. Depending on the …
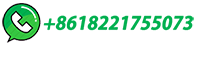
Cone Crushers (Parts of a Cone Crusher) Explained
Cone crushers are more often used for 2nd, 3rd & 4th stage crushing steps (although not always). Cone Crusher Components (Crusher Parts) The main components of a cone crusher include the main shaft, mantle, concaves, cone, eccentric bushing, drive, crown gear, frame, and tramp release mechanism (mechanically or hydraulically actuated).
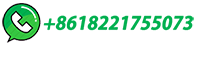
Primary Crushing: A Comprehensive Guide
Primary crushing happens when we take big rocks, even ones bigger than a meter, and make them into smaller bits. These bits are often between 150 and 200 mm. …
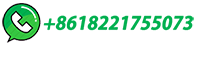
Types of Crushers: What You Need to Know
Parts diagram of a gyratory crusher . Secondary crushing equipment. ... Hammermills can be used as a primary crusher in many types of aggregate and industrial applications, including limestone, marble, shale, gypsum, phosphate, bauxite, aluminum dross, uranium, cryolite, clinkers, quicklime, petroleum coke, coal and more. ...
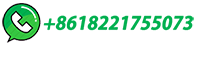
Jaw Crusher Diagram: Simplified Guide
Learn how each part functions in our Simple Guide: How Does a Jaw Crusher Work?. Anatomy of a Jaw Crusher Every jaw crusher diagram is a window to the soul of this rugged machine, providing vital insights to …
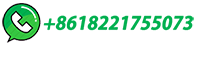
How it Works: Crushers, Grinding Mills and Pulverizers
Crushers, grinding mills and pulverizers are types of grinding equipment that transform or reduce a coarse material such as stone, coal, or slag into a smaller, finer material.
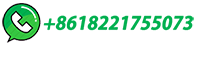
What Is The Difference Between Primary And Secondary Crusher?
Stay tuned to discover more about primary crusher, secondary crusher, crushing operations, and their distinct functions. Understanding Primary Crushers Primary crushers are an essential part of the crushing process, as they are responsible for reducing the size of large rocks into smaller particles.
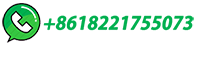
Primary and Secondary Crushing: Understanding the Basics
Learn the differences between primary and secondary crushing and how to choose the right crusher for your mining or construction project. This guide explains the basics of crushing, the factors that determine the choice of crusher, and more.
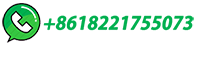
In- depth – Components of a Jaw Crusher | PROPEL …
A jaw crusher consists of Crusher Body Pitman Jaw plate Rear end frame Eccentric shaft The jaw crusher is one of the most admired and most sought after equipment from the house of Propel Industries. For the benefit of newcomers in the industry, here is an explainer of the various components of the Jaw crusher.
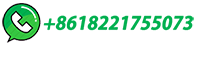
A Detailed Overview of Cone Crushers and What You Need …
Since cone crushers serve one function, it's easy for manufacturers to focus on making them more efficient and cost-effective to run. Today's advanced cone crushers are computer-controlled and carefully optimized to generate the most force while expending the least energy. ... Based on the diagram above, we can identify the main parts of a …
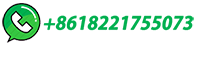
Types of Crushers Explained: Everything You Need to Know
The main function of a rock crusher is to generate particles of similar sizes. These particles can be further purified for use in other applications, including road construction, building materials, and raw materials for other industries. ... which will impact the choice of crusher and the use of wear-resistant parts. 3. Moisture Content: The ...
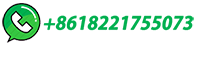
The Complete Guide to Plastic Crusher: Essential Tips and …
Each type of crusher is tailored to handle the specific characteristics of the targeted plastic material, ensuring efficient processing and reducing the risk of damage to the machine. Main Components and Structure. Plastic crushers typically consist of several main components and a specific structure to facilitate the crushing process.
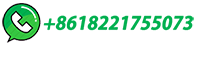
Choosing the right primary crusher for your aggregate …
Primary crusher is the workhorse that takes blast feed sizes and turns them into smaller sizes that are manageable for other site components—the belts, the screens, and …
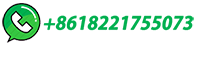
Cone Crusher Diagram: Simplified Guide
Understand cone crusher diagram basics with our comprehensive blog post. Learn about the structure and operation of cone crusher models.
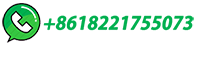
Understanding the Different Types of Crushers | Agg-Net
Jaw crushers are mainly used in primary crushing stages and are rarely used for secondary crushing. As a compression crusher, this type of machine generally produces the coarsest material because it breaks the …
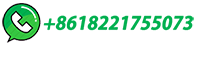
Gyratory Crushers
Wearing parts in the gyratory crusher may be either chilled cast iron or manganese steel, depending on the character of the material to be crushed and the particular class of service for which the machine is intended. Standard crushers, in the small and medium sizes, are customarily fitted with chilled-iron head and concaves for …
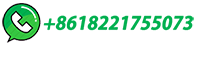
What Type of Crusher Is Best for Primary Crushing?
There are several different types of primary crushers. The right one for a primary crushing application depends on the material to be crushed, the feed size, the desired product size and the capacity required.
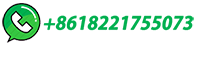
Parts of a Crusher: Jaw Crusher | Wagner Used Equipment
There are many different types of crushers, and one of the most popular kinds is the jaw crusher. Jaw crushers are usually primary crushers, meaning they handle large chunks of material and crush them into smaller bits before sending them onto other crushers before they go to the screening process.
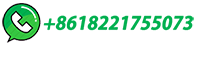
What is a Primary Crusher?
Learn what a primary crusher is and why it is important for your crushing business. Discover the types of primary crushers to increase crushing efficiency.
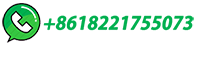