Iron Oxide Ore Mineralogy and Its Plant Flotation …
A large proportion of iron ore at the Donganshan processing plant, which is the largest producer of iron oxide product/concentrate in China, is low-grade, complex, difficult-to-separate carbonate-con-taining refractory iron ore.6 With the development of the mining operation, the carbonate contents have increased in the iron ore at the Donganshan
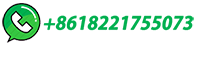
Minerals | Special Issue : Iron Ore Flotation
Iron ore flotation is a key technique to concentrate intermediate-low-grade ore, in order to reach the market requirements for higher-grade concentrates of iron. ... flotation chemistry, bubbles, froths, …
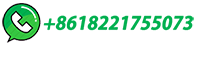
(PDF) Reagents in iron ores flotation
Iron recovery and silica content in the concentrate as a function of dosage for three types of CMC (1 slightly cationic CMC; 2 and 3 mixture of anionic CMCs with different degrees of substitution).
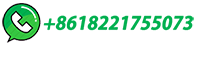
An overview of the beneficiation of iron ores via reverse …
The flotation of apatite used to lower the levels of phosphorus from 0.1 to 0.025% of P 2 O 5 in the LIMS magnetite concentrate is applied as a pellet feed with a fatty-acid-type …
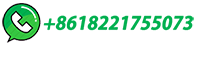
Iron Oxide Ore Mineralogy and Its Plant Flotation Circuits …
A large proportion of iron ore at the Donganshan processing plant, which is the largest producer of iron oxide product/concentrate in China, is low-grade, complex, difficult-to …
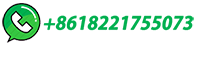
Froth Flotation of Iron Ores
The reagents used in iron ore flotation, including starch, amines and fatty acids, and the mechanisms of their interactions with the minerals in iron ore are examined. ... To further upgrade the concentrate, froth flotation has been established as an efficient method to …
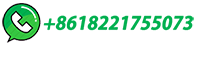
Processing of high alumina iron ore slimes using classification and
Highlights Recovering iron values from high alumina iron ore slimes from Joda, India Classification using two stage hydrocyclone to remove ultra fine particles and to upgrade iron values Studies on the effect of hydrocyclone design variables on grade and recovery Flotation of hydrocyclone underflow with amines and fatty acid Investigation on the effect of …
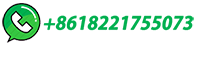
Purities prediction in a manufacturing froth flotation plant: …
Accurate and timely investigation to concentrate grade and recovery is a premise of realizing automation control in a froth flotation process. This study seeks to use deep learning technologies modeling a manufacturing flotation process, forecasting the concentrate purities for iron and the waste silica. Considering the size and temporality of engineering data, we …
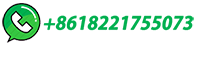
Flotation | Mineral Processing, Separation & Beneficiation
Flotation, in mineral processing, method used to separate and concentrate ores by altering their surfaces to a hydrophobic or hydrophilic condition—that is, the surfaces are either repelled or attracted by water. The flotation process was developed on a …
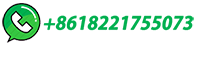
Iron Ore Flotation Process: The Journey from Ore to Concentrate
Factors affecting iron ore flotation. 1. Ore properties: The physical properties (such as density, hardness, etc.) and chemical properties (such as mineral composition, surface wettability, etc ...
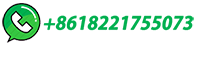
Processing Spodumene by Froth Flotation for Lithium Extraction
A Mineral Jig is included to recover a heavy mineral concentrate. Crushing. Mine run ore is usually bulky to avoid fines and ... The conditioned pulp is then diluted to a 20-25% solids for flotation. Complete removal of iron minerals along with some remaining feldspar is accomplished in a froth product which is small and is discarded ...
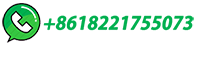
Characterization and Beneficiation of Dry Iron Ore …
concentration followed by the combination of grinding, classification, and froth flotation produced iron concentrate of 2.36% Al 2O 3 with 75.8% yield which can be used in sinter/pellet making. Keywords Rejectedironorefines .Characterization .Beneficiation .Flowsheetdevelopment 1 Introduction Iron ore is the basic raw material for iron and ...
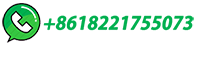
Iron Oxide Ore Mineralogy and Its Plant Flotation Circuits …
This work describes the concentration of iron ore slimes on a pilot scale by using a 500-mm diameter flotation column and a novel collector, which renders the use of a depressant unnecessary.
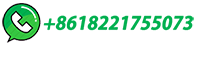
New perspectives in iron ore flotation: Use of collector …
The reverse flotation of the iron ore with etheramine collector is significantly impacted when the iron-bearing silicates and the kaolinite are present in the silicates gangue mineral complex. This paper aims to propose a new amidoamine collector N-[3-(Dimethylamino)propyl]dodecanamide for iron ore reverse flotation with a potential of …
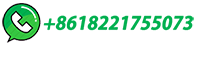
How to use Column Flotation to Reduce Silica
The requirement for higher quality pellets demands that the silica content be lowered to levels ranging from 0.25% – 2.0% SiO2. Reverse flotation (silica is floated away from the iron concentrate) has proven to be an economical and effective method for reducing the concentrate silica content to very low levels.
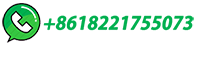
Collecting Agent–Mineral Interactions in the …
Froth flotation has been widely used in upgrading iron ores. Iron ore flotation can be performed in two technical routes: direct flotation of iron oxides and reverse flotation of gangue minerals with depression of iron …
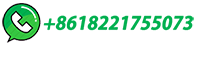
Flowsheet of iron ore flotation process with zoom on single flotation
Download scientific diagram | Flowsheet of iron ore flotation process with zoom on single flotation cell from publication: Purities prediction in a manufacturing froth flotation plant: the deep ...
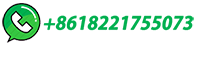
Improving recovery of iron using column flotation of iron ore …
The first industrial application of flotation columns in this country was silica flotation to concentrate iron ore at Samarco Mineração in the early 90′s and soon a great expansion of the application of this technology was observed in the iron ore flotation circuits (Flint et al., 1992, Araujo and Peres, 1995).
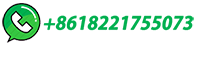
Hematite Processing by Flotation
Direct shipping of high grade iron ore, because of depletion or partial depletion of reserves, or high costs of operation has forced operators to use some means of beneficiation to produce an acceptable product with the lower grade iron ore reserves. Deposits of comparatively lower grade iron ore that remain relatively untouched or by-passed, are ...
DESULFURIZATION OF IRON ORE CONCENTRATE USING A …
The proper feed for the pelletizing plant must have iron and the Blaine number more than 67 % and 1900 cm 2 g-1 and sulfur content less than 0.1 %, respectively.
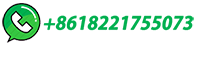
(PDF) An overview of the beneficiation of iron ores via …
Flotation is the most effective solution, both technologically and economically, when upgrading iron concentrates. Research regarding iron ore flotation began in 1931, demonstrating that reverse ...
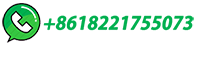
Innovative Flotation Routes in an Iron Ore Concentrator
Pi-lot scale column flotation yielded enhanced iron recoveries for both products in comparison with those achieved in laboratory mechanical cells, without impairing the …
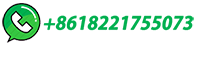
Minerals | Special Issue : Iron Ore Flotation
Special Issue Information. Dear Colleagues, Iron ore flotation is a key technique to concentrate intermediate-low-grade ore, in order to reach the market requirements for higher-grade concentrates of iron. The presence of …
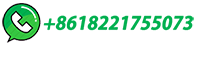
New perspectives in iron ore flotation: Use of collector …
However, detailed studies on reverse cationic flotation with iron ore samples from different deposits over the world (Brazil, Russia, Mexico) performed by Filippov and co …
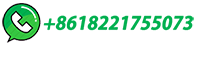
Existing and New Processes for Beneficiation of Indian Iron …
Cliff's Tilden plant in Cleveland, USA, is the only iron ore beneficiation plant, where selective flocculation technique, using degraded starch as the flocculant, has been applied to produce pellet grade concentrate from a feed containing around 32% Fe . The plant has a capacity of processing 10 million tons and is in operation since 1975.
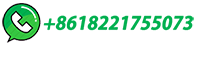
Minerals | Free Full-Text | Iron Ore Slimes Flotation Tests …
This work describes the concentration of iron ore slimes on a pilot scale by using a 500-mm diameter flotation column and a novel collector, which renders the use of a depressant unnecessary. The pilot column was operated in series with the industrial plant Vargem Grande 2 (Iron Quadrangle, Brazil) receiving, as feed, part of the underflow from the desliming …
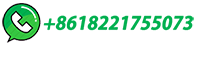
Flotation of Iron Ores: A Review
The impact of the zeta potential and surface chemistry on flotation and deslime is also discussed. The aim of this paper is to provide a well-detailed, well-referenced source for the current status of iron ore flotation, and thus provide a useful guide to its future development and to further improve flotation performance for iron ore.
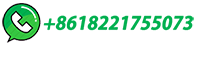
(PDF) Significance of reagents addition sequence on iron …
At the Donganshan Sintering Plant, the ore is a low-grade, complex, hard-to-separate carbonate containing iron ore, and a two-step flotation circuit was previously developed to overcome the ...
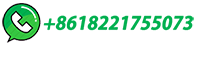
Froth Flotation Process
The costs given in Table 33 may be considered as applying to a plant built on a flat site for the two-stage selective flotation of a complex ore in subaeration machines with a tank for conditioning the pulp ahead of each stage and one cleaning operation for …
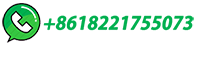
An overview of the beneficiation of iron ores via reverse …
The flotation of apatite used to lower the levels of phosphorus from 0.1 to 0.025% of P 2 O 5 in the LIMS magnetite concentrate is applied as a pellet feed with a fatty-acid-type collector called Atrac 1563 (mixture of 95–98% of ethoxylated tall oil ester of maleic acid and 2–5% of maleic anhydride) at 30–70 g/t at the Kiruna (KA2) and Malmberget plants in Sweden.
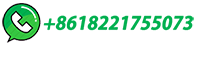
Flotation
The FLOTATION PROCESS is one of the commonest methods of extracting the valuable minerals from certain classes of ores, and it is generally more efficient as regards the recovery of the minerals than any other process applicable to the treatment of similar types of ores. The metallic contents of the minerals are recovered from the concentrates in a …
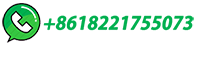