Roll crushers | PPT
8. DOUBLE ROLL CRUSHER Working Principle and Structure of Double Roller Crusher 1.this series of roll crusher is mainly formed by the roller, roller support bearing, compression and adjusting device, drive components etc. 2.the adjustment of the particle size: between the two rollers equipped with adjustment device like pads or wedge.The wedge …
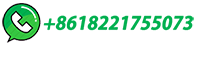
Double Roll Crusher DRC | FL
The rolls are operating with 5 m/s or more and shear and compression forces crush the material between the roll in the gap. The crushed material is released through the crusher base frame onto a discharge conveyor. ... DRS therefore …
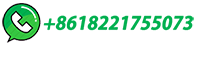
Construction Working and Maintenance of Crushers …
the crushing chamber until the material is reduced to top size. This results in over grinding a ... Generally gyratory crushers, jaw crushers, high speed double roll crushers, low speed sizers, impactors and hammer mills are used as primary crushers. In the secondary and subsequent stages, the material is further reduced and refined for proper ...
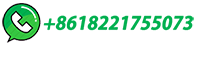
How Does a Jaw Crusher Work? A Simple Guide
The choice between a single or double toggle jaw crusher depends on the nature of the task, the size of the feed material, and the required size reduction. For large, heavy-duty operations, a double-toggle jaw crusher is often the go-to. ... Deep Crushing Chamber: Enhances feeding capacity and overall throughput. Steep Nip Angle: ...
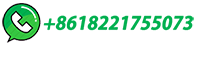
What's a Double-Roller Crusher?
The double-roller crusher can be used for finely crushing various high and medium hardness ores and rocks in industrial sectors such as mineral processing, chemical industry, cement, refractory materials, abrasives, building materials, etc., especially in the production of melonite and mung bean paste in the building materials industry.
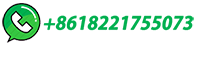
McLanahan | Triple Roll Crushers
Depending on the duty class, they can be used in most ROM applications, such as coal, salt, lime, pet coke and potash operations. Triple Roll Crushers combine a Single Roll Crusher with a Double Roll Crusher to form a crusher that is capable of achieving a 6:1 reduction ratio in the primary stage and a 4:1 reduction in the secondary stage while producing a cubicle product at …
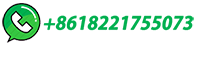
Laboratory-scale validation of a DEM model of a toothed double-roll …
A toothed double-roll crusher (referred to hereafter as TDRC) consists of a pair of oppositely rotating rolls, which have a series of intermeshing teeth protruding from the roll surfaces. The crushing action of TDRC is a combination of compression and ripping, where the teeth can dig into the rock and larger pieces than the roll diameter can be ...
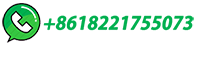
McLanahan | Types of Crushers in Sampling Applications
For the smallest crushed particle sizes, rolls may not have individual teeth. For fine crushing with roll crushers, beaded or smooth face roll may be incorporated. Roll Crusher rolls after processing a salt sample. Sampling Roll Crusher Sizes. Sampling Rolls Crushers are generally available for capacities up to 15-20 stph (13.6-18.1 mtph).
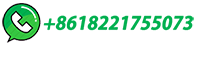
TRACKED DOUBLE-ROLL CRUSHER DOPPIATRAC
double-roll crushing, sizing and stockpiling machine. The DR400 is the world's only mass-produced, fully mobile double-roll crusher. Key Benefits: • Guaranteed product sizing in one pass as small as 35mm without the need for post screening • Feed size up to 180mm • Fully site mobile with a quick set up time
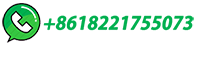
Roll Crushers | Williams Crusher
Double roll crushers reduce primarily through compression, although toothed rolls provide some shear. Rolls come in smooth, corrugated, and toothed designs. Double Roll Crushers produce a finer product at lower reduction ratios and capacities. ... These dust-tight roll crushers are perfect for crushing ash, limestone, coal, or glass ...
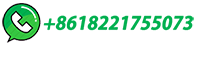
McLanahan | Roll Crushers
McLanahan offers belt-driven Roll Crushers in four designs (Single Roll, Double Roll, Triple Roll and Quad Roll) and can be designed for any application. ... Depending on the feed size, material is fed into the crushing chamber and encounters a single or a pair of rotating rolls. If a two-stage reduction is required, either a Triple or Quad ...
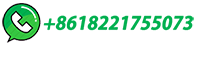
Roll Crusher
Double-roll crushers are able to crush more finely than single-roll crushers, because they are designed with teeth that mesh together rather than rotating past a smooth plate. They can reduce coal to as little as ¼ inch (0.6 cm) topsize, although they are more commonly operated close to 2 inches (5 cm). They have a higher capacity than ...
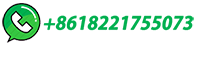
Roll Crushers
Progress in Roll-Crushing. BY C. Q. Payne, New York, N. Y. On the right, a Roll Crushers is shown in a sectional elevation of the A-C single-roll crusher while here below is a cutaway view of the machine, with hopper and part of the near side frame removed to show the crushing chamber. The moving elements of the machine consist of the roll, with its supporting shaft …
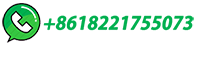
What Type of Crusher Is Best for Primary …
The main features of a Gyratory Crusher include a tall crushing chamber lined with replaceable manganese wear plates, a main shaft with head and mantle, and a spider to anchor the top of the main shaft bearing. ...
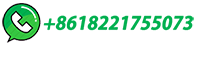
Dynamics in double roll crushers
Rolls were easy to manufacture, to install and to operate in a wide range of applications. A robust and reliable design, low machine height and an excellent ratio of capacity versus machine mass make double-roll crushers (DRC) still today the preferred choice for many soft to medium-hard rock applications in quarries and ore mines.
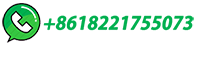
Double Roll & Teethed Roll Crusher
Although its brief period of popularity passed some thirty-odd years since, and only a few sets were installed before interest reverted to other types, the high-speed double roll crusher developed by Thomas A. Edison shortly before the end of the last century warrants a place in any discussion-of crushing equipment. In 1960, the largest machine of this type the 6 …
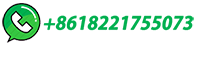
Double Roller Crushers
Double roll crusher is driven by the motor through the pulley or gear shaft opposite two rollers rotate, or were driven by two motors rotate two rollers. ... When a hard material or transport of …
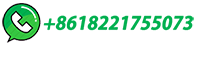
The Ultimate Guide to Jaw Crushing Machines: …
The double toggle jaw crusher is designed for crushing hard and abrasive materials, with its unique features including a double toggle plate and a large feed opening. One of the advantages of a double toggle jaw …
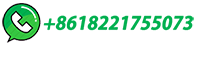
Study on productivity of eccentric roll crusher based on …
1. Introduction. Currently, in the primary crushing stage, commonly used crushers include jaw crushers and gyratory crushers. Recently, FL (2022) has introduced an eccentric roll crusher, which has gained favor in the crushing industry due to its high efficiency and energy-saving advantages. They are widely used for primary crushing of ores such as …
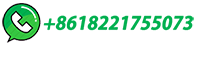
The Advantages and Applications of Double Roll …
This article explores the benefits and uses of double roll crushers in the mining industry. It provides an in-depth analysis of the components, operating principles, and various applications of double roll …
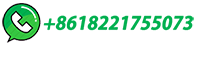
P&Q University Lesson 7: Crushing & Secondary Breaking
The crushing chamber is formed by massive drums, revolving toward one another. ... composed of heavy manganese steel castings known as roll shells that are available with either a smooth or corrugated crushing surface. Double roll crushers offer up to a 3-to-1 reduction ratio in some applications depending on the characteristics of the material ...
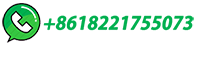
Mining Crushers | AllMinings
Crushing Chamber: The material enters the crushing chamber, where the rotating mantle applies pressure against the stationary concave, crushing the material. ... A roll crusher, also known as a double roll crusher, is a type of compression machine used to crush hard materials. It consists of two large metal rolls that rotate in opposite directions.
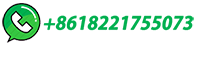
(PDF) SIZE REDUCTION BY CRUSHING METHODS
The double jaw crusher is designed for crushing hard materials, also quarried materials, sand and gravel, and recycling. [4, 5] crusher [4] The tie rod and compression spring ensure that the ...
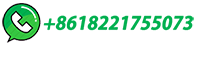
Factors to Consider When Selecting the Proper Roll Crusher …
Also, as the material rides on top of the crushing rolls, it begins to act as a grinding agent, thereby accelerating the wear of the crushing elements. ... rule of thumb for single-stage crushers is that a Single Roll Crusher provides up to a 6:1 ratio of reduction and a Double Roll Crusher provides up to a 4:1 ratio of reduction.
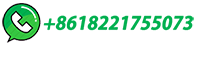
Roll Crushers
It was required to further crush it down to 0.5 cm in a roll crusher with smooth rolls. The friction coefficient between steel and particles was 0.25, if the rolls were set at 6.3 mm and both revolved to crush, estimate the diameter of the rolls. ... is required due to voids between particles and the increase in bulk density of the particles as ...
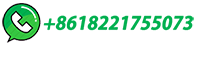
Design, Fabrication and Testing of a Double Roll Crusher
The degree of crushing in a single-roll crusher with block stop on the roll cannot be equal to 4 or more. It was proved that destruction of isotropic materials occurs along the plane of action of ...
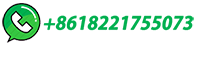
What Are the Differences Between The 7 Types …
Crushing cases of the two crushers Manufactured sand made by roll crusher in Indonesia. The video shows the double roller crusher is turning small-sized stones into manufactured sand. There is a certain gap between …
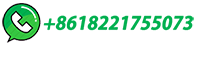
McLanahan | Quad Roll Crushers
The top stage of the Quad Roll crusher is essentially made up of a double roll crusher, which is designed with the appropriate diameter rolls and tooth configuration to readily grab the incoming feed material. ... tramp relief systems employ a spring-and-toggle mechanism that activates whenever an uncrushable object enters the crushing chamber ...
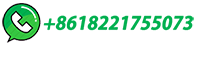
SRC | Single roll Crusher
The single roller crusher has a driven roller and a swivelling crushing wall. The crushing tools of both units are coordinated so that a defined final grain can be produced. The end product can be optimized through the hydraulic gap adjustment.
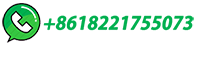
Roll Crushers
Roll crushers with differing tooth configurations can handle feed material of up to 1500 mm to generate a product of some 250 mm at rates of up to 2500 t/h. Roll crushers with smooth rolls are used for pulverization to generate a product granulometry of ≤ mm. ... The crushing chamber of the housing is lined with wear plates. The upper section ...
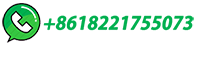