Sintering and Pelletizing
Ensure your plant's high performance and profitability while lowering investment and operating costs with our agglomeration technologies. Our innovative sintering and pelletizing solutions are based on over 60 years' experience and world …
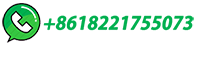
Sinter Plant
Learn about the sinter plant process, its emissions, energy efficiency, and alternatives in the iron and steel industry. Find chapters and articles from various books and journals on …
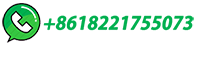
Virtual Sinter ® : Digital Twin for Integrated Sinter Plants
The Virtual Sinter ® digital twin software tool is developed to address operational challenges faced by sinter plant operators and to assist and advise them on day-to-day operation of the plant. The schematic of Virtual Sinter ® is shown in Fig. 2.Virtual Sinter ® interacts with an actual sinter plant in real time, utilizes the model-based monitoring, diagnosis and …
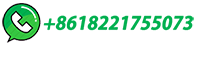
(PDF) Iron Ore Sintering: Process
Sintering is a thermal agglomeration process that is applied to a mixture of iron ore fines, recycled ironmaking products, fluxes, slag-forming agents and solid fuel (coke).
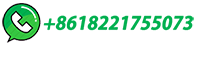
Sintering | Eurotherm
Figure 1 shows a simplified diagram of a sinter plant. Materials enter the sinter plant from storage bins. They are mixed in the correct proportions using weigh hoppers, one per storage bin, except for the return fines for which an impact meter is used instead. Weighing is continuous, as is the whole sintering process.
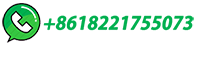
Sintering
ensuring a suitable sinter bed permeability and thus improving the productivity of the sinter plant. † Fernández-González et al. (2017b): Iron ore sintering: Process, where the ori-gins of …
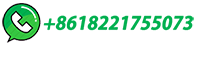
Multi-objective Optimization of Integrated Iron Ore Sintering Process
The steps involved in the iron ore sintering process is shown in Fig. 1.Various raw materials used in sintering viz. iron ore fines, fluxes, solid fuel and steel plant reverts are blended in a specific proportion as per the desired chemical composition of sinter and …
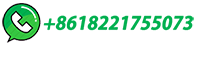
Prediction of Sinter Properties Using a Hyper-Parameter …
The present work aims at performing prediction validation for the physical properties of coke layered and nonlayered hybrid pelletized sinter (HPS) using artificial neural networks (ANNs). Physical property analyses were experimentally performed on the two HPS products. The ANN model was then trained to obtain the best prediction results with the grid …
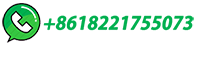
Ore Sintering
Sintering emissions and their mitigation technologies. L. Lu, ... X. Li, in Iron Ore, 2015. 18.1.1 Key gaseous emissions from sinter plants. Iron ore sintering is a material preparation process employed worldwide in the production of iron and steel. According to statistical data on pollution, sintering plants rank second in terms of toxic emissions, after the …
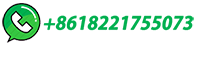
State of the Art in Air Pollution Control for Sinter Plants
The process off-gas from a sinter plant is usually de-dusted in an electrostatic precipitator (ESP) . At some sinter plants, a subsequent process for off-gas desulphurization (DeSOx), reduction of dioxin emissions and/or further de-dusting has been installed in order to comply with tighter emission limits.
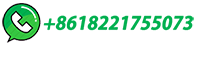
Factors influencing Sinter and Sintering Process …
Optimum mean size of iron ore fines for good sintering process will vary from sinter plant to sinter plant since it is dependent on several factors but as a general rule higher mean size is better for permeability and hence helps in …
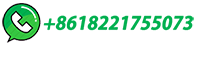
Sinter Plant Operations: Raw Materials | SpringerLink
The size of limestone used in the sintering process will strongly affect the sinter plant performance; however, if we are looking for higher productivity, then a coarse limestone particle is required (<6.3 mm), if we want …
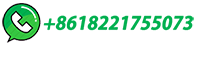
Iron ore sintering
The sintering process begins with preparation of a sinter mixture consisting of iron ore fines, fluxes, solid fuel (called bonding agents in Japan) such as coke breeze, and return fines from the sinter plant as well as recycled ferruginous materials from downstream iron and steelmaking processes.
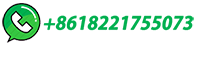
Sintering
The sintering process begins with preparation of a sinter mixture consisting of iron ore fines, fluxes, solid fuel (called bonding agents in Japan) such as coke breeze, and return fines from the sinter plant as well as recycled ferruginous materials from downstream iron and steelmaking processes. After being mixed in a rotating drum, water is ...
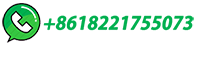
Iron Ore Sinter
Automated optical image analysis of natural and sintered iron ore. E. Donskoi, ... J.R. Manuel, in Iron Ore, 2015 4.2.2 Sinter. Low-temperature (< 1300 °C) iron ore sinter is an agglomerate of unmelted and partially melted nuclei particles (+ 1 mm) and a matrix bonding phase produced from the melting of fine ore (− 1 mm) and flux particles, with the majority of melt formation …
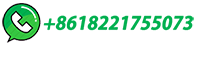
Optimizing Manganese Ore Sinter Plants:Process …
The process of sintering is an agglomeration technique for fine ore that relies on heat to melt the surface of smaller particles together to form larger agglomerates. A typical sinter plant consists of a number of sequential operating units with the sinter strand at the heart of the plant. The simplified process sequence is as follows:
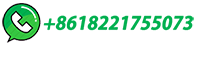
Sintering
The sintering process begins with preparation of a sinter mixture consisting of iron ore fines, fluxes, solid fuel (called bonding agents in Japan) such as coke breeze, and return fines from …
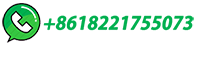
Sinter Plant
A sinter plant can process various materials into a finished product that has the desired chemical composition and grain size to be used in the blast furnace. Materials include iron ore fines, limestone, dolomite and waste dust, scale and slag particles. The mixture of materials are baked on a moving conveyor, ignited by burners from above with ...
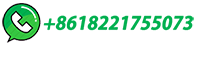
Sintering: A Step Between Mining Iron Ore and …
Sinter quality begins with the mined iron ore and the proper selection and mixing of the raw materials. Inhomogeneous raw mix can affect …
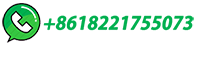
Coke Ovens-Sinter-BF-BOF Route | SAIL
SINTERING PROCESS A Sinter Plant typically comprise the following sub-units as shown below. SINTERING PROCESS. The raw materials used are as follows - Iron ore fines (-10 mm), coke breeze (-3 mm), Lime stone & dolomite fines (-3mm) and other metallurgical wastes. The proportioned raw materials are mixed and moistened in a mixing drum.
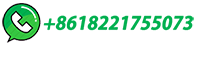
Sintering Process | Carmeuse
Burnt lime, as compared to limestone, improves the heat transfer in the sintered layer. At the same basicity and the same volume of fuel, a change in the CO 2 /CO ratio can occur, due to the different amounts of carbonates after their replacement by lime. For lime too, the quality, granulometry, quantity, and method of lime addition to the agglomeration process are critical …
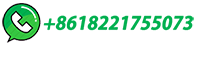
How we make steel
The ingredients – iron ore, coke and limestone fines – are carefully stacked and blended, then passed under an ignition hood at the sinter plant. This heating process is carefully controlled to make sure the resulting sinter has the right composition and optimum sizes for the next stage of the process at the blast furnaces.
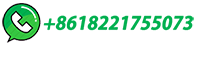
The sintering plant at a glance | PIEPER
Process monitoring, which focuses on detailed monitoring and evaluation within a production chain, should not disregard visual observation of the complete plant.For this purpose, overview cameras are installed in such a way that they provide an overall picture of the running production.The images generated in this way reach the control centre via live stream so that …
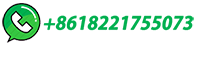
Traveling Grate Sinter Plant
has built more than 400 iron ore sinter plants worldwide. This process, primarily used for iron ores, can also be used for sintering manganese and nickel ore fines. Our energy-optimized version of the sintering (EOS) process reduces off-gas volumes and the emission of hazardous pollutants, while simultaneously reducing fuel consumption.
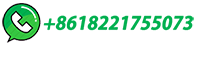
Lead and Zinc Sintering | IntechOpen
A typical flowsheet of sinter process is shown in Figure 2. The product is a partially fused porous agglomerate, which is crushed and large lump material is fed to the blast furnace. Fine sinter material is recycled or returned …
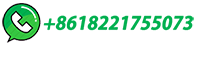
Iron Ore Sintering Process & Equipment in Steel …
Sinter is the primary feed material for making iron in a blast furnace. According to the U.S. Environmental Protection Agency, the sintering process converts fine-sized raw materials, including iron ore, coke breeze, limestone, mill scale, and flue dust, into an agglomerated product, sinter, of suitable size for charging into the blast furnace. ...
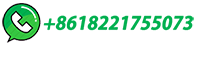
Sintering | Eurotherm
Figure 1 shows a simplified diagram of a sinter plant. Materials enter the sinter plant from storage bins. They are mixed in the correct proportions using weigh hoppers, one per storage bin, except for the return fines for which an impact …
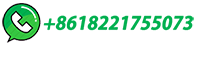
Investigation of the Contents of the Stack Emissions of Iron Ore Sinter
Our sinter plants have one ESP to filter the process gas and one ESP for de-dusting each. The filtered gas joins a common stack (excepting one sinter plant, without a bag filter). A sinter plant has maximized emission reduction of sintering (MEROS) and waste gas recycling (WGR) and another one high-temperature bag filter (HTBF).
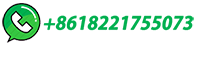
Sintering emissions and mitigation technologies
A real-scale plant trail was carried out to reduce emissions of PCDD/Fs from the iron ore sintering process by optimizing its sinter raw mix (Chen et al., 2016). Compared with the reference conditions (existing raw mix), the emissions of total PCDD/Fs, I-TEQ, and WHO-TEQ was found to decrease by 65%, 76%, and 75%, respectively, as the sinter ...
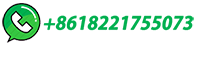
Iron Ore Pelletizing Process: An Overview | IntechOpen
The fines resulting from the concentration process must be agglomerated for use in iron and steelmaking. This chapter shows the status of the pelletizing process with a special focus on binders. ... and superior environmental performance of pellet plants as compared to sinter plants; the main iron producing systems, blast furnace, and DR ...
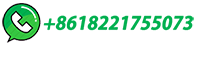