DRI production | International Iron Metallics …
DRI production. Direct reduction of iron is the removal of oxygen from iron ore or other iron bearing materials in the solid state, i.e. without melting, as in the blast furnace. The reducing agents are carbon monoxide and hydrogen, coming …
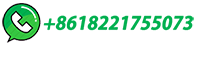
Direct Reduced Iron briquette machine,briquette equipment
Direct reduction iron(DRI) also named sponge iron, It is the raw material for electric furnace steelmaking. In the direct reduced iron production process, no matter what kind of production process is, all need use briquette machine to complete briquetting raw materials, mixing all materials such as iron ore, iron concentrates, coke, coal and bidner together, to press them …
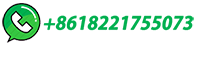
Ironmaking 101 – From Ore to Iron with Smelting and Direct Iron
Figure 1: Steelmaking byproducts for blast furnace (BF), basic oxygen furnace (BOF) and electric arc furnace (EAF) processes. Source: World Steel Association (worldsteel) The first step in the production of steel or cast iron alloys is the reduction of iron ore—which contains iron oxide and gangue or mineral impurities—to unrefined, reduced iron form.
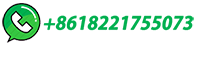
Process modelling for the production of hydrogen …
The iron and steel industry is a major emitter of global CO 2 emissions, responsible for approximately 7 to 9%. 1–3 Conventional blast furnace-basic oxygen furnace (BF-BOF) steelmaking process (73.2% share) …
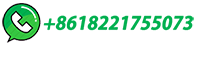
Behavior of direct reduced iron and hot briquetted iron in …
It is considered that the use of prereduced ferrous materials and sources of metallic iron such as direct reduced iron (DRI) or hot briquetted iron (HBI) improves the productivity of the blast furnace (BF). However, oxidation of DRI/HBI can occur in the upper zone of the BF, which may increase the content of the reducing gases but may not decrease the coke rate substantially. …
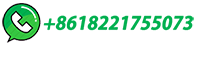
DRI briquetting, sponge iron briquette making – why and how
What is sponge iron Sponge iron, also known as DRI (direct reduced iron or direct reduction iron), bulk density 1.6-1.9g/cm3, apparent density 3.4-3.6g/cm3, typical size 4-20mm, is a kind of material produced by the reduction of iron ore with reducing gases such as H2 or CO gas generated from various carbon or hydrocarbon resources. The name is got …
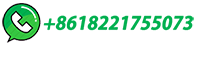
Optimization of Steelmaking Using Fastmet Direct Reduced Iron …
The potential of using direct reduced iron (DRI) from the FASTMET process in a blast furnace to substitute iron oxide pellets was studied by simulation and optimization. Mathematical models of the unit operations in the steel plant were combined to yield a description of the entity, and the arising system was optimized with respect to ...
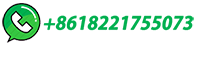
The Direct Reduction of Iron
Abstract. For the past 100 years, the dominant technology to produce iron from iron ores has been the blast furnace, which utilizes carbothermic reduction at elevated …
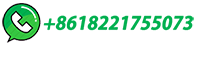
Studies on direct reduced iron melting in induction furnace
DRI was used to observe the effect of different fractional reduction on the removal of impurities from pig iron melt during EAF melting. On the basis of results, three types of reduced flux DRI ...
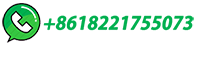
Analysis of the Theoretical and Practical Energy
This paper derives from first principles simple relationships that can be used to compute energy requirements for the production of hot metal (pig iron) in a blast furnace (BF) or direct reduced iron (DRI) in a direct reduction furnace (DRF), and the transformation of hot metal and DRI into crude steel in a basic oxygen furnace (BOF) or electric arc furnace (EAF) …
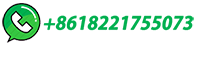
Direct reduction of iron to facilitate net zero
The global annual production of steel is approximately 2 billion tons, accounting for 8 % of the world's energy demand and 7 % of carbon dioxide (CO 2) emissions in the energy sector.Coal-based direct reduced iron (DRI) reduces CO 2 emissions by 38 % compared with traditional blast furnace–basic oxygen furnace (BF-BOF) ironmaking. Using a combination …
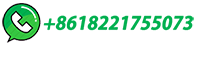
Research on technical parameters of electrical arc furnace …
Process dynamics of electric arc furnace during direct reduced iron melting. Metall Mater Trans B 2002; 33: 187–199. Crossref. Google Scholar. 9. Kirschen M, Badr K, Pfeifer H. Influence of direct reduced iron on the energy balance of the electric arc furnace in steel industry. Energy 2011; 36: 6146–6155. Crossref.
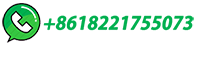
Use of Direct Reduced Iron (DRI) in the Electric Arc …
Use of Direct Reduced Iron (DRI) in the Electric Arc Furnace (EAF) for Steelmaking • Steel production in the EAF continues to grow both in North America and worldwide. The past 5 …
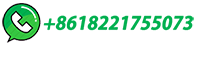
DRI-Direct Reduced Iron Rolling mill
Direct Reduced Iron (DRI-Direct Reduced Iron) is a low-carbon porous substance formed by the reduction of refined iron powder or iron oxide at a low temperature in a furnace. Its chemical composition is stable and its …
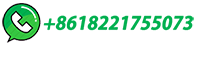
Direct reduced iron
India is the world's largest producer of direct-reduced iron. [8] Sponge iron is not useful by itself, but can be processed to create wrought iron or steel. The sponge is removed from the furnace, called a bloomery, and repeatedly beaten with heavy hammers and folded over to remove the slag, oxidize any carbon or carbide, and weld the iron together. This treatment usually creates …
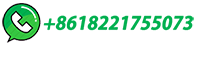
Direct Reduction Iron Process | SpringerLink
As shown in Fig. 2.2, the higher the direct reduction temperature, the smaller ΔG Ө, indicating that the reduction reaction is more likely.Fe 3 O 4 in copper slag can be easily reduced to metallic iron, and Fe 2 SiO 4 can also be reduced to metallic iron when the direct reduction temperature is higher than 1036.7 K. If CaO is added in the direct reduction …
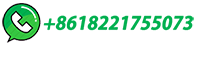
DRI(Direct Reduced Iron)とは
DRIはDirect Reduced Iron(ダイレクトリデュースドアイアン)のであり、におけるつののです。DRIプロセスは、(に)をへするであり、はガスやコークスオーブンガス(COG)などのを …
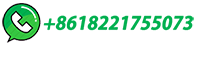
History, developments and processes of direct reduction …
the solid stage producing a solid product sponge iron or direct reduced iron (DRI), which contains all gangue materials of the iron ores. Direct reduction processes Processes for …
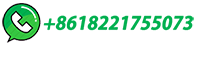
(PDF) Properties and features of direct reduced iron
In addition, direct reduced iron has a well-defined chemical composition when compared with steel scrap and has efficient melting properties in the electric arc furnace.
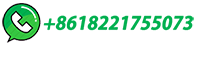
Dynamic modeling of a direct reduced iron shaft furnace to …
An alternative method to produce steel is to use direct reduced iron (DRI) shaft furnaces followed by electric arc furnaces (EAFs). In this route, syngas (a mix of carbon …
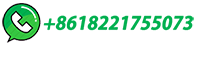
North Africa: Focus on Direct Reduction Ironmaking
There is no doubt that the technology of the blast furnace/basic oxygen (BF/BOF) route has improved steelmaking efficiency, productivity, and product quality compared to the open-hearth furnace. However, the direct reduced iron/electric arc furnace (DRI/EAF) route is a better option for North Africa and the Middle East-North Africa (MENA) region.
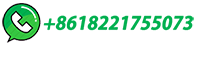
Process Improvements for Direct Reduced Iron Melting in …
Steelmaking based on direct reduced iron (DRI, and its compacted derivative hot briquetted iron, HBI) is an anticipated important global alternative to current steel production based on FeOx reduction in blast furnaces due to its lower specific CO2 emission. The majority of DRI is melted and refined in the electric arc furnace with different process conditions …
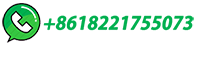
HYL Process for Direct Reduction of Iron Ore – IspatGuru
With the successful production of direct reduced iron with the gas-based HYL direct reduction process, studies were begun for the design of the first commercial plant with a daily capacity of 230 tons of DRI. ... to convert iron pellet/lump ore into metallic iron by the use of reducing gases in a solid-gas moving bed shaft furnace. O2 is ...
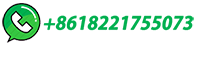
A review of ironmaking by direct reduction processes: …
Central Iron and Steel Research Institute, 17(3), pp. 1â€"7. doi: 10.1016/S1006-706X(10)60064-7. [12] Yilmaz, C. and Turek, T. (2017) ‘Modeling and simulation of the use …
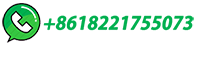
Influence of direct reduced iron on the energy balance of the electric
The direct carbon dioxide (CO 2) emissions from the iron and steel sector are nearly 7 % of the global CO 2 emissions from energy use. India is the world's second-largest producer of steel and the largest sponge iron producer. India produces one-third of the global sponge iron, mostly from rotary kilns using coal as an energy source, resulting in higher …
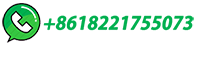
Direct reduced iron process
Figure: Shaft furnace for the direct reduced iron process. The heart of the direct reduction is the shaft furnace, which is filled from the top with lump ore and pellets. Carbon monoxide and hydrogen are used to dissolve out …
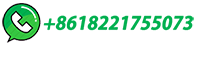
Low-Carbon Production of Iron & Steel: Technology Options …
Direct reduced iron to electric arc furnace (DRI-EAF) production is 5% and growing, it appears to have better decarbonization potential to move towards net-zero. Secondary steel production using mainly steel scrap in electric arc furnace (EAF-scrap) is 24% of global production and has both the lowest energy consumption and is technically ...
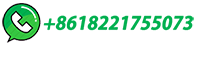
Assessment of hydrogen direct reduction for fossil-free …
In the latter, the basic concept is to use a hydrogen direct reduction (H-DR) process to produce direct reduced iron (DRI) which is then converted to steel in an electric arc furnace (EAF). There is so far very little information on the hydrogen direct reduction (H-DR) process in the scientific literature.
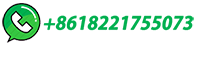
Green Hydrogen-Based Direct Reduction for Low-Carbon …
1 Introduction. The iron and steel industry as one of the biggest industrial emitters of CO 2 accounts for approximately 30% of the global industrial CO 2 emissions. As set in the Paris Agreement, the emissions of greenhouse gases have to be reduced by 80–95% until 2050 compared with preindustrial levels to keep global warming below 2 °C.
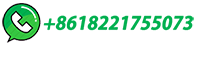
Green steel: design and cost analysis of hydrogen-based direct iron …
Hydrogen-based direct reduced iron (H2-DRI) is an alternative pathway for low-carbon steel production. Yet, the lack of established process and business models defining "green steel" make it ...
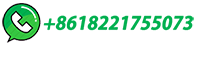