Open-Pit Mining | Method and Process | Epiroc
In hard rock mining, much of the world's annual output of copper, gold and iron ore is won from open-pit operations. Other commodities produced from open-pit mining include diamonds, molybdenum, manganese, lead and zinc, uranium and a variety of industrial minerals, such as borates, talc and specialist clays.
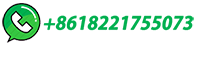
ITP Mining: Energy and Environmental Profile of the U.S.
4.1.1 Iron Ore Mining. There are two basic methods of mining iron ore. These are: Surface mining or open-pit mining . Underground or shaft mining. To be competitive, iron mining …
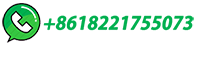
The stages of mining: 5 lifecycle processes explained
This is a definitive breakdown of the stages of mining. Learn exactly how ore is mined from this expert-approved guide.
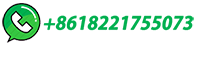
Step-by-Step Guide: Chrome Plant Process Flow Explained
Gain a comprehensive understanding of the exploration, ore extraction, crushing and grinding, beneficiation, roasting and leaching, precipitation and refining, smelting and alloying, and the final product stages …
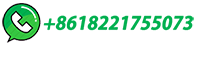
Digging deeper: Mining methods explained | Anglo …
Find out how 3 types of mining techniques work to mine shallow or deep deposits: open-pit, underwater, & underground mining.
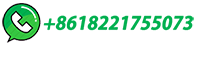
Copper Mining and Processing: Processing Copper Ores
Copper processing is a complicated process that begins with mining of the ore (less than 1% copper) and ends with sheets of 99.99% pure copper called cathodes, which will ultimately be made into products for everyday use.The most common types of ore, copper oxide and copper sulfide, undergo two different processes, hydrometallurgy and …
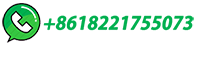
The six main steps of iron ore processing
Learn about the steps involved in iron ore processing, from crushing and grinding to separation. Contact Multotec experts for guidance on iron processing.
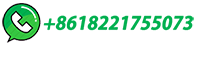
Blast furnace | Definition, Temperature, Diagrams, & Facts
Blast furnace, a vertical shaft furnace that produces liquid metals by the reaction of a flow of air introduced under pressure into the bottom of the furnace with a mixture of metallic ore, coke, and flux fed into the top. Blast furnaces are used to produce pig iron from iron ore for subsequent processing into steel.
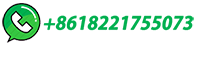
Iron | Geoscience Australia
Sintering is a process used to agglomerate iron ore fines in preparation for blast-furnace smelting and is usually carried out at iron and steelmaking centres. It involves the incorporation of crushed limestone, coke and other additives available from iron and steelmaking operations.
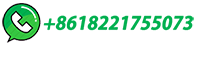
Steel Making Process – Complete Overview with Flowchart
In the crucible steel making process, mixtures of wrought iron, ... Carbon is released into the molten product as the iron ore melts and interacts with the burning coke. ... We have covered all types of steel making process and tried to explain with proper diagrams and images wherever required. Hope you liked this article.
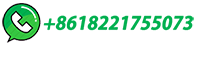
Top 6 Steps Of Iron Ore Processing
What Is Iron Ore Processing? - Explore the comprehensive guide to efficient iron ore processing in our top 6 steps. Discover more today!
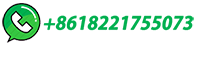
Simplified flow chart showing typical iron ore processing …
... activities involved in mining and processing iron ore on site are shown in the flow chart in Figure 1. Ore processing ranges from simple crushing and screening methods to more...
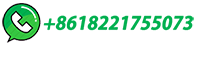
Pilbara mining process diagram
Iron Ore production in the Pilbara. Activities involved in finding, mining and processing iron ore at our Pilbara operations have been simplified in the following diagram. Rio Tinto …
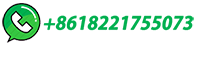
Direct reduced iron process
The reduction gases only dissolve oxygen from the iron ores. This causes the iron ores to crack on the surface. The appearance resembles a porous sponge, which is why the deoxidized and thus strongly ferrous iron ore is also called sponge iron. Sponge iron is a highly ferrous ore from the direct reduced iron process!
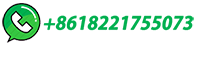
Planning an Iron Ore Mine: From Exploration Data to …
The process of developing an iron ore mine from exploration data through to informed mining decisions provides an example of a Complex Adaptive System.
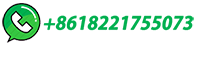
Copper Mining & Extraction Process Flow Chart
This flowchart made of machinery icons explains or expresses in simple but clear terms the step of the Copper Mining and Copper Extraction Process.. Starting from either open-pit or underground mining and using a different relevant treatment method for oxide or sulphide copper mineral (ore).
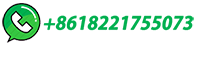
Iron processing
Iron processing - Smelting, Refining, Alloying: The primary objective of iron making is to release iron from chemical combination with oxygen, and, since the blast furnace is much the most efficient process, it receives the most attention here. Alternative methods known as direct reduction are used in over a score of countries, but less than 5 percent of iron …
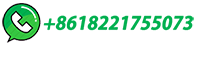
Iron ore beneficiation: an overview
This chapter briefly discusses the current scenario of the iron ore resources in India, iron ore mining methodology, beneficiation technique, and the current operating practices for achieving sustainable growth in the iron and steel industry.
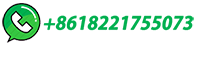
Iron Ore Characterization Techniques in Mineral …
Iron Ore Characterization Techniques in Mineral Processing ... 2 Department of Mining Engineering, National Institute of Technology, Surathkal, Mangalore 575025, Karnataka, ... the success of beneciation process is inu-enced by ore characteristics, such as the textural behavior.
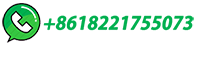
-The 3 basic stages of any Pelletizing Process
Download scientific diagram | -The 3 basic stages of any Pelletizing Process from publication: THE GROWING IMPORTANCE OF PELLETIZING FOR IRON ORE MINING AND IRON PRODUCTION | In the last years ...
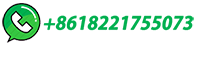
Mining
Mining - Underground, Safety, Techniques: When any ore body lies a considerable distance below the surface, the amount of waste that has to be removed in order to uncover the ore through surface mining becomes prohibitive, and underground techniques must be considered. Counting against underground mining are the costs, …
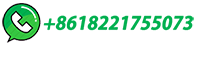
Planning an Iron Ore Mine: From Exploration Data to …
The process of developing an iron ore mine from exploration data through to informed mining decisions provides an example of a Complex Adaptive System. The detailed composition of an
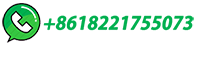
Hard Rock Lithium Processing
important lithium ore mineral. A typical run of mine ore can contain 1-2% Li 2 O, while a typical spodumene concentrate suitable for lithium carbonate production contains 6-7% Li 2 O (75% - 87% spodumene). Higher grade concentrates with 7.6% Li 2 O and low iron content are used in ceramics and more demanding industries.
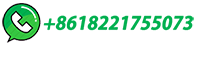
Exploring Steel Production: A Comprehensive Visual Process …
The Journey from Iron Ore to Steel: An Overview. The transformation of iron ore into steel is a remarkable process that involves a series of detailed steps. Beginning with the extraction of iron ore from the earth through mining operations, this raw material is then treated and prepared for the smelting phase. The extracted ore …
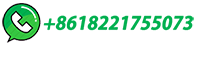
The mining value chain: A hidden gem | McKinsey
For product types that come in various grades of quality, such as iron ore, an additional step known as product blending takes place before the product is loaded onto the ship and transported to the customer. ... It includes a mindset shift—perceiving the mining value chain as one integrated process rather than a series of individual steps ...
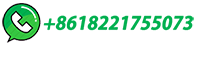
Iron Ore | Geoscience Australia
Marillana: In May 2018, Brockman Mining Ltd upgraded the Marillana Iron Ore Project's JORC (2004) Mineral Resource estimate, published in 2010, to comply with JORC (2012). Brockman stated that the upgraded, ... 4 Agglomeration is the process in which magnetite grains are aggregated into pellets using a chemical binding reagent. …
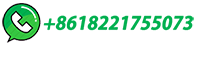
Iron Mining Process | Equipment | Flow | Cases
Iron mining process, how to extract mineral from rock and placer deposit, related processing plant flow chart and layout design. read more.
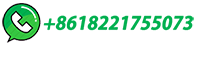
Iron processing
Mining and concentrating Most iron ores are extracted by surface mining. Some underground mines do exist, but, wherever possible, surface mining is preferred …
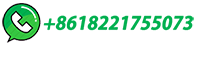
Steel Production
The blast furnace uses coke, iron ore and limestone to produce pig iron. Coal traditionally has been a key part of the coke-making process. The coal is crushed and ground into a powder and then charged into an oven where it is heated to approximately 1800°F in the absence of oxygen. As the oven is heated, the coal begins to melt so most of the ...
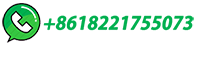
Life cycle assessment of iron ore mining and processing
The study used typical iron ore mining and processing operations in Pilbara, Western Australia, as a case study and covers the upstream part of the cradle-to-gate life cycle of steel: the mining and processing of iron ore.
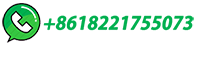