Knowing the Basics Leads to Better Care
standard cone crusher, the main shaft is housed in a frame attached to a mantle. A pinion (counter) shaft assembly drives a bevel gear that rotates the cone. As material presses against the bowl liner by the mantle or cone, it is crushed into smaller pieces that fall through to …
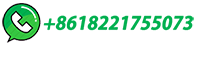
A Comprehensive Guide to Stone Crusher Machines
Jaw crusher: The jaw crusher is the main component of a stone crusher machine. It works by using pressure to crush the rocks and stones into smaller, usable pieces. Conveyor belts: The conveyor belts are used to transport the crushed stones to the next stage of the process. They are designed to be durable and able to handle the weight of the ...
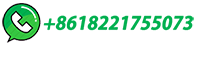
Jaw Crusher Parts
The eccentric shaft is the main shaft of the jaw crusher, which is subject to substantial bending torque and is made of high-carbon steel. The eccentric part must be fine finishing and heat treated, and the bearing lining must be cast with Babbitt alloy.
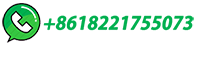
P&Q University Lesson 7: Crushing & Secondary Breaking
Between stages, screens with two or three decks separate the material that already is the proper size. Most secondary crushers are cone crushers or horizontal-shaft impact crushers. Tertiary and quaternary crushers are usually cone crushers, although some applications can call for vertical-shaft impact crushers in these stages. GYRATORY CRUSHER
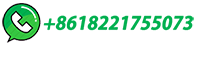
McLanahan | CMB Cone Crushers
CMB Cone Crushers feature a lower mainframe housing the main shaft, an upper frame supporting a concave bowl assembly and a tapered wedge assembly machined to correspond with the inner tapered surface of the main frame. A drive turns the horizontal countershaft, and a pinion gear on the countershaft rotates the eccentric gear on the main shaft.
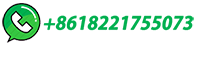
"Computer Aided Design of Jaw crusher"
opening of 22" by 30", a 46 x 46 jaw crusher has a opening of 46" square. Generally primary jaw crushers have the square opening design, and secondary jaw crushers have rectangular opening design. Jaw crushers are used as primary crushers in a mine or ore processing plant or the first step in the process of reducing rock.
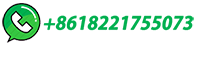
Design and Analysis of Rotor Assembly of Hammer Mill Machine …
Pillow Block Bearing 4.1 Bearing Life Calculation Type of bearing used: Pillow Block Bearing Diameter of Shaft: 45mm Speed of Shaft, N= 1728 rpm Nominal or Rated speed in hours, L h = 10000 hrs ...
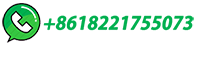
The Ultimate Guide to Jaw Crushing Machines: Types
Jaw crushers are a popular choice for crushing and reducing the size of various materials, but like any type of crusher, they have both advantages and disadvantages. Advantages of Using a Jaw Crusher. One of the main advantages of using a jaw crusher is that it can handle a wide range of materials.
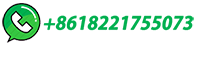
Hammer Mill Crusher & Grinder
The hammer mill is the best known and by far the most widely used crushing device employing the impact principle of breaking and grinding stone. Thus far we have described machines which do a portion of their work by impact, but the only machine described in which this action plays an important role was the sledging roll type and particularly the Edison roll …
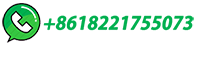
Construction Working and Maintenance of Crushers for …
working of the crusher is as under. The main shaft of the crusher is journaled in the spider bearing and in the eccentric bearing assembly. The spider bearing fixes the position of the upper end of the main shaft. Eccentric bearing assembly with inner bushing can be replaced, or in some models turned, to adjust the stroke.
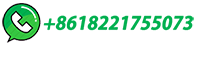
Application guide SUPERIOR® primary gyratory crusher …
gap is opened and closed by an eccentric assembly in the bottom shell, which causes the central vertical shaft to gyrate. The vertical shaft is free to rotate about its own axis. Gyratory crushers are one of the main primary crusher types used in mines and quarries. The size designation of gyratory crushers is
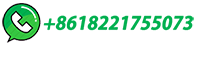
A Comprehensive Guide to Different Types of Crusher Wear Parts …
In addition to the mantle and concave, other critical components in a cone crusher include the eccentric, main shaft, and bearings. ... Choosing high-quality crusher wear parts can have a significant impact on the performance and longevity of the machine. High-quality wear parts can increase efficiency, reduce maintenance costs, and prevent ...
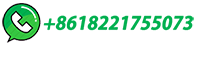
4 Types of Stone Crushers' Maintenance and Efficient …
The sand making machine is also known as the vertical shaft impact crusher. Its working mode is that the material falls vertically from the upper part of the machine into the high-speed rotating impeller. The impeller is one of the important parts of the sand making machine, and it is also the most vulnerable part.
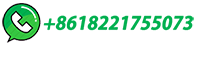
Shredding Machines: Types, Applications, Advantages, and …
The machine upgrades cardboard waste material into eco-friendly and high-quality cardboard void fill material, like strips, chips or netting, or packaging material. Cardboard shredding machines are user-friendly, very simple to operate, and safe to use. The machine is …
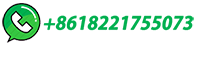
MP 1000 and MP 800 Series Cone Crushers
The pedestal-type main shaft is rigidly held in a tapered bore in the center of the crusher frame. The main shaft is forged of high-strength alloy steel. Abrasion-resistant wear liners and guards provide extra protection to areas exposed to material passing through the crusher. Arm and counter-shaft box guards are cast from hi-chrome...
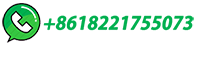
Cone Crusher Parts
The cone crushers reduce the size of rocks by compressing the material between the mantle and bowl liner. The mantel, also known as the moving cone, covers the cone head to protect it from wear.
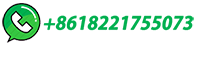
Cone Crusher Diagram: Simplified Guide
A cone crusher diagram shows the main parts of the machine. These include the crushing shell, eccentric shaft, adjustment ring, and bottom shell. The bottom shell is made from annealed cast steel. Safety devices …
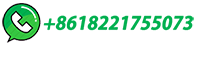
Crusher Equipment Africa
CE Africa offers Gyratory, Jaw & Cone Crushers Spares, Repairs & refurbishment. We Strip, Assemble, Machine or Supply All Crusher Equipment. 011 568 8324 info@ce-africa ... Compared to other cone crushers, it has a higher main shaft speed and bigger crushing. ... A gyratory crusher topshell and topshell assembly including an outer crushing ...
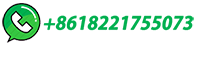
Gyratory Crushers
Wearing parts in the gyratory crusher may be either chilled cast iron or manganese steel, depending on the character of the material to be crushed and the particular class of service for which the machine is intended. Standard crushers, in the small and medium sizes, are customarily fitted with chilled-iron head and concaves for crushing soft and medium …
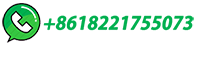
Understanding the Cone Crusher Working …
Cone crushers require regular maintenance to ensure optimal performance and avoid costly breakdowns. Here are some tips to keep your cone crusher operating smoothly: Regularly inspect and clean the machine's …
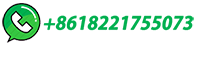
Crusher Wear Parts: What They Are and Why …
Cone Crusher Wear Parts. Cone crushers are used for secondary and tertiary crushing in mining and aggregate industries. Cone crusher wear parts include mantles, concaves, bowl liners, and torch rings. …
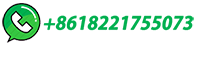
How Does A Cone Crusher Work: Understanding …
A cone crusher is crucial, especially in aggregates and mining industries. It plays a role in crushing hard rocks into smaller rocks for further processing. ... Mantle: It's a fixed surface with a concave shape attached to …
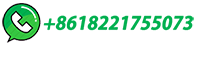
Barmac® B Series™ impact crushers
Barmac® vertical shaft impact (VSI) crushers were the first vertical shaft impactors in the world. The original Barmac® was developed in New Zealand over 40 years ago after which the VSI crushers have spread to thousands of crushing sites around the globe.
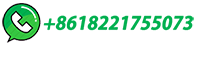
Minerals Processing Systems JW SERIES JAW …
JW Series Jaw Crusher Construction RELIABLE Main shaft The main shaft is of large diameter and is forged from hardened and tempered alloy steel to suit heavy-duty applications. The shaft has high fatigue resistance because of its quality surface finish and the absence of screw threads and sharp radii that can cause stress concentrations. Bearings
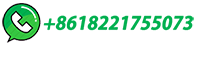
Types of Crushers Explained: Everything You Need to Know
The impact crushers are applicable for less abrasive materials such as limestone, dolomite, and soft to medium – hard rocks. They can generate a more cubical and uniform product shape which compression crushers do not have. There are two main types of impact crushers: horizontal shaft impactors (HSI) and vertical shaft impactors (VSI).
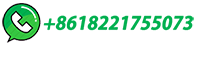
Types of Rock Crushers | Quarry Crushing Equipment | Kemper
Cone crushers, vertical shaft impactors (VSIs), ... These types of machines break apart material by the impacting forces of certain wear parts known as blow bars and impact plates or toggles. Some operations also use impact-style crushers after they have already used a different type of rock crusher that produces a more elongated stone. This ...
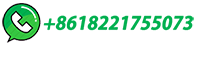
Construction Working and Maintenance of Crushers …
working of the crusher is as under. The main shaft of the crusher is journaled in the spider bearing and in the eccentric bearing assembly. The spider bearing fixes the position of the upper end of the main shaft. Eccentric bearing assembly with inner bushing can be replaced, or in some models turned, to adjust the stroke.
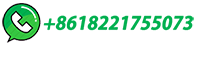
How it Works: Crushers, Grinding Mills and Pulverizers
Table Source: Wikipedia (Crushers) Cone crushers use a spinning cone that gyrates in the bowl in an eccentric motion to crush the rock between the cone surface, referred to as the mantle, and the crusher bowl liner.Gyratory crushers are very similar to cone crushers, but have a steeper cone slope and a concave bowl surface. As the gap between the bowl liner …
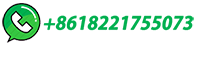
Cone Crusher
The cone crusher is a modified gyratory crusher, and accordingly many of the same terms including gape, set, and throw, apply. The essential difference is that the shorter spindle of the cone crusher is not suspended, as in the gyratory, but is supported in a curved, universal bearing below the gyratory head or cone (Figure 6.8).Major suppliers of cone crushers include …
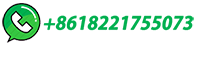