Thermal energy analysis of a lime production process: Rotary …
In this paper, thermal energy analysis of three zones of a lime production process, which are preheater, rotary kiln and cooler, is performed. In order to perform a …
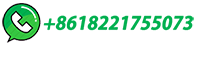
Heat Recovery Analysis of a Rotary Kiln in Cement Industry
Energy efficiency of a cement production process is quite small due to large amounts of heat loss from the systems. Rotary kilns have been widely used in the cement industry to produce clinker.
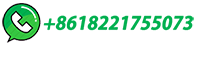
MENENTUKAN HEAT CONSUMPTION PROSES PRODUKSI KLINKER PADA ROTARY KILN …
Heat loss is affected by heat in the calcining zone of the rotary kiln. The higher the heat consumption value and the smaller the kiln feed out calcining zone produced, the greater the possibility ...
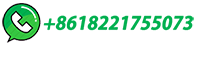
Investigating the potentials to improve the energy …
Sarcheshmeh lime rotary kiln in the south of Iran consumes a lot of thermal energy compared with other rotary kilns. As a result, Sarcheshmeh lime kiln is being investigated for the potential to improve energy consumption.
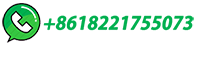
Rotary kiln process: An overview of physical …
Other challenges faced by rotary kilns include: energy optimization (recovery, storage and recovery of waste heat from the kiln, optimization of process control laws, etc.), the use …
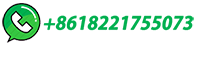
CFD analysis of a rotary kiln using for plaster production …
In this study, the CFD analysis of the rotary kiln is carried out for examining effects of various parameters on energy consumption and efficiency of the rotary kiln. The flue gas recirculation using in many applications is a useful method for combusting of fuel unburned in the flue gas. Also, effects of flue gas recirculation on the combusting of fuel, …
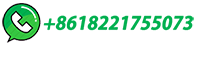
Indirectly heated rotary kiln – for efficient thermal processing
FL's Indirectly Heated Rotary Kiln is a more sustainable and affordable choice when compared to others on the market, as it offers both minimised fuel consumption and maintenance.
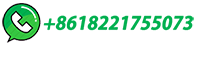
ENERGY-EFFICIENT TECHNOLOGY OPTIONS FOR DIRECT …
2.3 Specific Energy Consumption 11 2.4 Material Balance 12 2.5 Energy Balance 15 2.6 Energy Performance Assessment of Key Equipment 15 3.0 Energy-efficient Technologies in Direct Reduction of Iron Process 17 3.1 Waste Heat Recovery for Power Generation 18 3.2 Iron Ore Preheating Rotary Kiln Using Waste Heat Recovery System 20
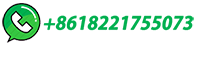
Rotary Kiln
Furthermore, the most significant effect of rotary kiln heat transfer is the convection from the hot gas to the solid, which controls almost 70% of the energy transferred to the particles. ... The O 2 concentration in the medium will decrease in the same direction because of its consumption. Therefore, the zone in the vessel located near the ...
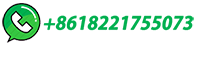
Research on Online Monitoring of Energy Consumption of Rotary Kiln …
The results show that the energy consumption model of thermal rotary kiln based on least squares support vector machine for clinker formation can realize real-time monitoring of rotary kiln energy consumption. It is of great significance for the analysis of energy consumption of cement rotary kiln.
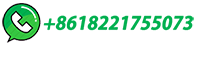
Rotary Kiln Design: Thermal Analysis Part 2
Rotary Kiln Design: Thermal Analysis Part 2 – Specific Heat and Heat Transfer. This article was co-authored by: Rotary kilns are a high-temperature thermal processing …
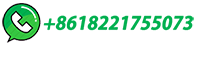
JURNAL MULTIDISIPLIN
119 Kumpulan Manuskrip Ilmiah JURNAL MULTIDISIPLIN Menghitung Heat Loss dan Specific Fuel Consumption (SFC) pada alat Rotary Kiln di Pabrik II PT.
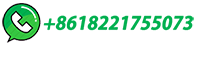
Production of Smelter Grade Alumina (SGA) by Calcination
The rotary kiln is a counter current heat exchanger with a very complicated direct heat transfer process taking place between the hot gas, ... The production of alumina is seldom weighed directly but calculated from a standard specific heat consumption applied to all calciners at the refinery, or calculated from the measured wet hydrate feed ...
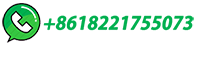
Heat Balance Analysis in Cement Rotary Kiln
The purpose of this study is optimizing the air and fuel quantities at kiln considering design parameters of the cement plant by keeping adequate safety factors at each level of calculations to assure that neither production rate nor quality of the clinker vary. Analysis of Heat balance was used to determine the sources of heat loss from the …
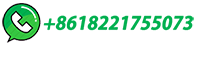
EVERY THING YOU NEED TO KNOW ABOUT HEAT BALANCE …
The following shows three different heat balance models, one each for a wet, a dry, and a preheater kiln. In comparing these tile differences in over all specific heat …
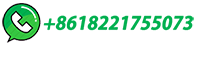
Research on Online Monitoring of Energy Consumption of …
Abstract: For the heat balance and thermal efficiency calculation of the cement rotary kiln firing system, the heat of cement clinker formation plays an important role in energy …
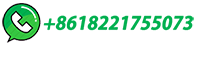
Computation of steady state thermochemistry in rotary …
A rotary kiln is therefore fundamentally a reactive heat exchanger where energy from a hot gas phase is transferred to the condensed bed material. Download : Download high-res image (297KB) Download : Download full-size image; Fig. 1. Model scheme of the counter current rotary kiln.
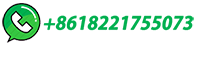
Enhancing Rotary Kiln-Electric Furnace Process of Saprolitic …
How to reduce the energy consumption of the rotary kiln-electric furnace (RKEF) process has become an important issue for the stainless steel industry. The aim of this study is to reduce the energy consumption of ferronickel production from saprolite nickel laterite in the RKEF process. The effects of the slag binary basicity, FeO content, …
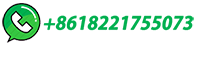
HEAVY FUEL OIL COMBUSTION IN A CEMENT ROTARY KILN …
In this paper, a comprehensive 3D mathematical model for rotary cement kiln including heavy fuel oil combustion, hot flow, zone heat flux model for clinker formation and rotating wall was developed.
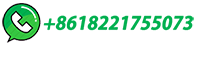
Utilization of cement rotary kiln waste heat for calcination …
These cross‐sectional views well portray a cut‐away portion of the rotary kiln to present inner components as well as flow of heat energy into the main machine i.e. rotary kiln. Heat inside the kiln is being radiated through hot flame and intended towards the solid bed surface of raw meal.
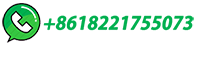
Large- and Particle-Scale energy assessment of
The Rotary Kiln-Electric Furnace process is a widely recognized pyrometallurgical route for ferronickel production. This paper focuses on the rotary kiln furnace, an intermediate stage in which partially dried minerals convert into calcine, ready for smelting in an electric arc furnace.
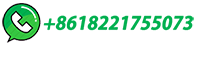
Analysis of the parameters affecting energy consumption of a rotary
In this study, the effects of refractory bricks and formation of anzast layer on the specific energy consumption of a rotary kiln are investigated.
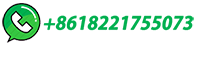
ANALYSIS OF HEAT LOSS IN KILN IN CEMENT INDUSTRY-A REVIEW …
In this study, heat loss from rotary kiln was examined. Analysis of energy balance was used to determine the sources of heat loss from kiln system.
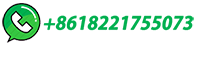
Clay calcination technology: state-of-the-art review by the …
Similar to clinker manufacture, the use of a cyclone preheater improves the thermal efficiency and lowers the fuel consumption, effectively reducing operational costs . A series of counter current flow cyclones recover heat and filter particulate matter. ... Existing rotary kiln heat transfer models [90, 96,97,98 ...
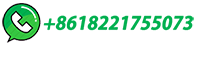
Rotary Kiln Design: Thermal Analysis Part 2
Similar to specific heat, the thermal conductivity, or heat transfer properties of a material, also play a big part in the design of a rotary kiln. How a material transfers heat will have a direct effect on how the material behaves in the rotary kiln; will it transfer its heat easily, causing even heat distribution and low retention time, or ...
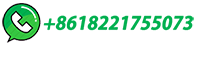
Thermal energy analysis of a lime production process: Rotary kiln …
In this paper, thermal energy analysis of three zones of a lime production process, which are preheater, rotary kiln and cooler, is performed.
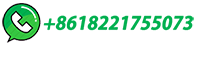
Energy- and economic-balance estimation of pyrolysis
3–2 Estimate the heat consumption in the reactor, which consists of the reaction heat, sensible and latent heats of products, and heat loss of a water-cooling feeder. ... Exergy and energy analysis of pyrolysis of plastic wastes in rotary kiln with heat carrier. Process Saf Environ, 142 (2020), pp. 203-211, 10.1016/j.psep.2020.06.021. …
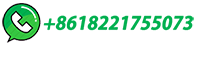
Rotary kiln process: An overview of physical mechanisms, …
Highlights • Solid transport, heat transfer and thermochemical transformation are discussed in detail. • The heat and mass transfer modeling process in rotary kilns is summarized. • The commonly used correlations involving rotary kilns are categorized by …
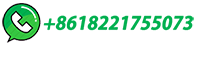
RotarEkiln™
As the name signifies, RotarEkiln is an electrically powered, indirectly-heated rotary kiln, which doesn't consume fossil fuels. For the RotarEkiln, the burner system of standard indirect rotary kilns is substituted by an electric heating system, which utilizes resistive emitters that provide radiative heat transfer to the kiln shell.
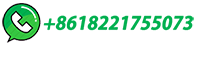
Rotary Kiln | SpringerLink
The advantages of the rotary kiln are: (1) uniform heating and high heat transfer efficiency. The solid materials are heated in the uniformly rotating cylindrical kiln body, which move reversely against the gas; (2) large equipment scale, high operation continuity, and large production capacity; (3) stable product quality; (4) low energy …
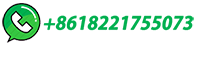