The Ultimate Guide to Ball Mills
Raw materials are ground through a hollow shaft neck into a hollow cylinder containing grinding media of various diameters (steel balls or gravel, etc.).
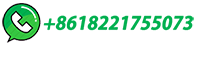
Ball Mill | Iron Ore Processing Equipment
A Ball Mill a type of grinder is a cylindrical device used in grinding (or mixing) materials like ores, chemicals, ceramic raw materials and paints. Ball Mills rotate around a horizontal axis, partially filled with the material to be ground plus the grinding medium.
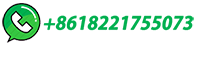
Energy Efficiency Analysis of Copper Ore Ball Mill Drive …
Ore is then transferred to ball mills, in which it is first subjected to coarse grinding, and in the second phase (i.e., fine grinding) it is treated with grinding bodies (rods or cylpebs), which are introduced into the mill. Specific energy consumption during the milling process depends on the geomechanical parameters of the raw material
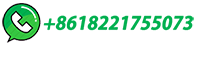
Review on vertical roller mill in cement industry & its …
Raw mix, high grade limestone, sand and iron ore are transported from their bins to raw mills for drying and further fine grinding. The raw mill is either a Ball mill with two chambers or Vertical roller mill with inbuilt classifier. The hot gases from the pre heater enter the mill and are used for drying material in the mills.
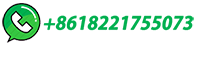
Iron Ore Pelletizing Process: An Overview
Pelletizing feed preparation and mixing: the raw material (iron ore concentrate, additives —anthracite, dolomite—and binders are prepared in terms of particle size and chemical …
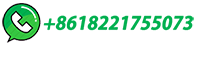
Titanium Ore Plant: Efficient Mining and Processing Methods
The Best Titanium Ore Processing Plants. The production of titanium raw materials is consolidated around three leading producers, Rio Tinto," "Exxaro" and "Iluka Resource LTD," which account for two-thirds of raw material production, depending on market conditions and production parameters.
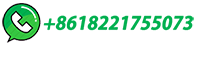
Oreo Balls Recipe (The Healthy Version)
These oreo balls are made with clean ingredients and a healthy dose of protein for a delicious ball that satisfies and fuels your body!
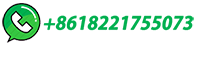
A comparison of wear rates of ball mill grinding media
One of the most popular milling machines is the cement mill, which is used to crush raw materials such as lime, silicate, alumina and iron oxide using grinding balls [3]. The quality and ...
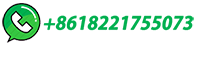
How Does a Raw Mill Work in a Cement Industry
Typically, a cement raw mill comprises a hopper for feeding materials into the mill, grinding elements such as rollers or balls, a separator, and a system for driving the rotating rollers or balls. The grinding process reduces the size of the raw materials, producing fine powder that is then fed into the kiln for firing.
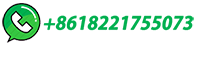
SREE BALAJI METACAST INDUSTRIES | HI CR GRINDING MEDIA BALLS …
Hi Chrome Grinding Media Balls & Cylpebs. Our organization is instrumental in providing our clients with a superior quality range of Hi Chrome Steel Grinding Media Balls. Fabricated using high quality raw material such as metals & alloys and advanced machinery, these products ensure durability to the end user.
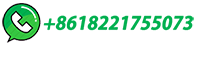
Sinter Plant Operations: Raw Materials | SpringerLink
The raw materials for an integrated steelworks can be classified into four categories, which are iron ores, fluxes, fuels, and reverts. The characteristics of these raw materials strongly affect the metallurgical properties of iron ore sinter and sinter plant...
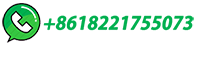
PMAI I Pellet Manufacturers Association of India
The pellets are used as raw material for Iron making in the plants as an alternate material for Sinter and/or Lump Ore. The pellets are preferred over sinter and lump ore as their shape, size, strength and excellent …
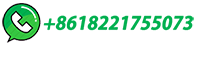
(PDF) Iron Ore Pelletizing Process: An Overview
ore pelletizing plant. ... the raw material (iron ore concentrate, additives ... Pellets are balls formed by rolling moist concentrates and fines iron ores of different mineral-
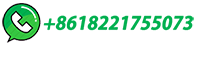
Iron Ore Pelletizing Process: An Overview
ore pelletizing plant. The idea of rolling moist fine ore in a drum to form balls and then drying and firing it was first ... the raw material (iron ore concentrate, additives ... The height and width of the trajectory increase as the ball size increases until the balls hit the scraper blades. After that, they move down and pass under the water ...
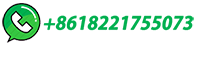
Ball Milling royalty-free images
It is also use grinding balls like a ball mill. Industrial ball mill on the ore concentration plant. Motion blurred rotated drum. ... region of northern Chile. Ball mill at a Copper Mine in Chile at dawn. A ball Mill inside of a copper processing industry. raw material ball mill (isolated monochrome graphic image, the 34 in the perspective) ...
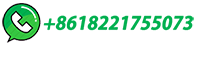
Exploring Ball Mill Diagram: A Comprehensive Guide
The size of the balls is based on the size of the raw material and the desired final product size. Ceramic and rubber balls are used in processes where steel balls are unsuitable for contamination, e.g., in the production of …
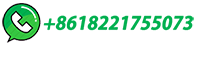
Ball Mills
In all ore dressing and milling Operations, including flotation, cyanidation, gravity concentration, and amalgamation, the Working Principle is to crush and grind, often with rod mill or ball mill, the ore in order to liberate the minerals. In the chemical and process industries, grinding is an important step in preparing raw materials for …
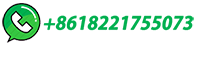
5,691 Ball Mill Royalty-Free Images, Stock Photos & Pictures
raw material ball mill (isolated color yellow-black and monochrome graphic, 34 in perspective) Close up view of the large ball and sag mill in the mine plant. A typical type of fine grinder is the ball mill.
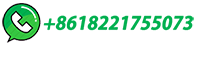
Ball Mill | Mining Grinding Mill
The ball mill is a tumbling mill that uses steel balls as grinding media. Ball mills can be used in wet or dry systems for bulk and continuous milling, and are most widely used in small or large-scale ore beneficiation plant. Dry grinding: suitable for materials that react with water, such as building stones such as cement and marble. Due to ...
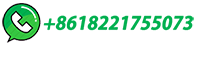
Ball Mill | Bauxite Ore | Star Trace Pvt. Ltd.
A Ball Mill a type of grinder is a cylindrical device used in grinding (or mixing) materials like ores, chemicals, ceramic raw materials and paints. Ball Mills rotate around a horizontal axis, partially filled with the material to be ground plus the grinding medium.
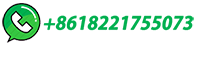
Iron Ore Pelletization
Iron ore is a critical raw material in modern society; it is the basis of the steel industry, which provides us with everything from infrastructure to appliances.
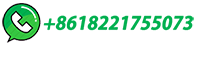
Iron ore pellets as a solution to steel—making raw materials …
Iron ore pellets as a solution to steel—making raw materials at the crossroad and dominant constituent of basket of iron ores available for export in the future ... fines generated from the iron ore mining and crushing units for sizing the feed for blast furnace and sponge iron ore plants are mostly un-utilised. Pelletisation technology is ...
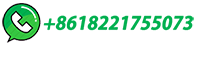
Iron Ore Pellets and Pelletization Process – IspatGuru
Pellets plants are normally integrated with the iron ore beneficiation plants. In case they are not integrated then concentrated iron ore in slurry form is usually pumped to the pellet plant by slurry pipelines. ... bonding by the formation of ceramic bonds and by greater compaction of the particles during the rolling of green balls ...
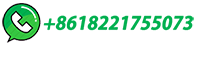
Ball Mill Success: A Step-by-Step Guide to Choosing the …
In the intricate dance of ball milling, where raw materials are transformed into finely milled particles, the choice of grinding media emerges as a pivotal performance lever. ... Ceramic Balls: Composed of materials like silicon nitride, alumina, ... a copper processing plant struggled with inefficient ore grinding using standard steel balls ...
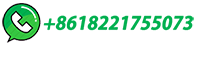
Cooling Air Velocity on Iron Ore Pellet Performance Based …
After the ball making, a round hole sieve is used to screen the pellets to achieve a particle size of 10–12.5 mm for the raw balls. Through the performance …
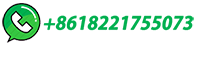
Integrated steel plant in Scunthorpe, UK Raw material …
Granulation of raw materials is the single most important factor in controlling the permeability of the ... Iron ore nuclei Serpentine Iron ore adhering fine Limestone Moisture [Water between ... the ball ceases, the balls stop growing and its strength reaches maximum value.
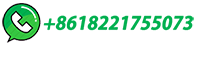
The six main steps of iron ore processing
Six steps to process iron ore. 1. Screening. We recommend that you begin by screening the iron ore to separate fine particles below the crusher's CSS before the crushing stage. A …
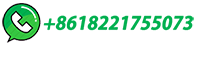
Iron Ore Pelletization
Pelletizing, or balling, is a key part of efficiently and sustainably producing steel from iron ore fines of varying sources.
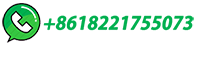
What are high chrome grinding media balls used for?
Grinding media balls are used in industries such as mining, cement production, and chemical processing to crush and grind materials into fine powders or particles. These balls are typically made of steel or other materials and come in various sizes and shapes.
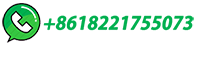
Raw Material Drying-Grinding
Ball Mill Ball mills with high efficiency separators have been used for raw material and cement grinding in cement plants all these years. Ball mill is a cylinder rotating at about 70-80% of critical speed on two trunnions in white metal bearings or slide shoe bearings for large capacity mills. Closed circuit ball mill with two compartments for ...
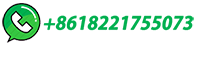