Dynamic quality prediction and control in rotary sponge iron …
The quality of sponge iron produced in the coal-fired rotary kilns at TATA Steel Long Products Limited (TSLPL) is permitted to vary in a small window of 80-83% …
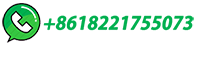
Operation of Coal-Based Sponge Iron Rotary Kiln to
Sponge iron is the final product of coal fired rotary kilns. The schematic diagram in Fig. 1 describes the unit processes involved in a sponge iron a production plant [1] .
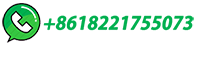
PEMBUATAN SPONGE IRON DARI BIJIH BESI LAMPUNG MENGGUNAKANROTARY KILN
The process of reduction of iron ore pellets in a rotary kiln and shaft furnace has done fairly satisfactory. ... Kata kunci: bijih besi, pulverized coal burner, reduksi, rotary kiln, sponge iron ...
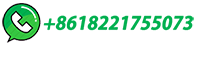
Flow of materials in rotary kilns used for sponge iron …
The present work identifies the basic features of burden movement in a rotary kiln. The cold model study was conducted with iron ore as the feed material to determine the influence …
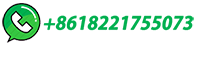
Direct Reduction Ironmaking | SpringerLink
There are many rotary kiln processes that vary in terms of raw material and product, but their basic process and raw material are the same. SL-RN process is a representative one. Rotary kiln direct reduction process has developed rapidly in the regions in lack of natural gas. Rotary kiln direct reduction is used to produce direct …
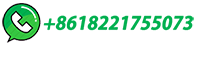
Flow of materials in rotary kilns used for sponge iron …
The present work identifies the basic features of burden movement in a rotary kiln. The cold model study was conducted with iron ore as the feed material to determine the influence of length to diameter ratio (L/D) of a rotary kiln on the filling degree, hold-up, and residence time of the charge. An empirical equation correlating different operating …
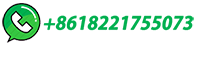
Flow of materials in rotary kilns used for sponge iron …
rotary kilns. The present study, on cold models, was under- taken to assess the importance of various parameters influ- encing the flow of materials in sponge iron rotary kilns. B In rotary kiln based direct reduction processes, it is essen- tial to identify the optimized flow conditions which give rise
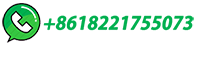
Sponge Iron Production in Rotary Kiln Kindle Edition
Sponge Iron Production in Rotary Kiln - Kindle edition by Sarangi, A. Sarangi, B.. Download it once and read it on your Kindle device, PC, phones or tablets. Use features like bookmarks, note taking and highlighting while reading Sponge Iron Production in Rotary Kiln.
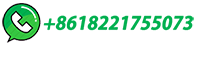
Recovery and Utilization of Waste Heat in a Coal Based …
Rotary Cooler Sponge iron (magnetic) At 110 oC Water: at 30 oC DSC 900 C 1020 C Dust: ABC Air: WHRB Waste gas Water: ESP Dust Wet scraper waste gas Dusty gas Chimney Steam Water: at 34.5 oC ... gas from ESP outlet to rotary kiln an insulated duct, which is a hollow cylinder of 43m length and 0.6m diameter, is used. To
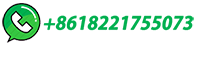
Excellent Sponge Iron Kiln To Deal With Your Sponge Iron
AGICO offering goods in stock: sponge iron kiln, sponge iron kiln parts, sponge iron plant in all kinds of models. Also, our technical personnel will offer installation advice and after-sells service.
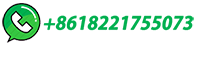
(PDF) Operation of Coal-Based Sponge Iron Rotary Kiln to …
Optimization problem discussed here for a coal-based rotary kiln to find the optimal operating conditions keeping desired targets like quality and accretion formation …
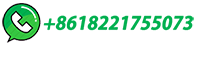
Flow of materials in rotary kilns used for sponge iron …
Looking forward to the need of developing coal-based sponge iron technology in India, a country having no significant resources of either coking coal or natural gas, the …
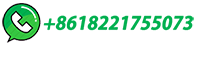
Flow of materials in rotary kilns used for sponge iron …
The formation of accretions or 'rings' in rotary kilns used for the manufacture of directly reduced iron (sponge iron) affects the residence time of the charge, kiln hold-up, and the kiln output to a great extent. In this part of the work, the effect of ring formation was simulated at room temperature in a scaled-down model of a rotary kiln by inserting …
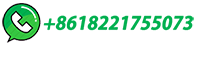
Energy Conservation in Sponge Iron Production Process …
In this process screened iron ore (6tph), coal (3.3tph) and dolomite (0.2tph) are charged into the rotary kiln with the help of a conveyor. Air (17.978 tph) is injected along the …
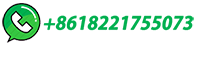
A review of ironmaking by direct reduction processes: …
However, for coal-based DR the reductant is generated from non-coking coal and rotary kilns, rotary hearth furnaces and multi-hearth furnaces are used (Ghosh and Chatterjee, 2017). It has been estimated that approximately 65-75% of sponge iron production cost is attributed to the cost of raw materials (Indian Bureau of Mines, 2011).
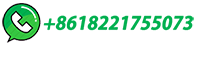
Dolomite – Its Processing and Application in Iron and
Dolomite – Its Processing and Application in Iron and Steel Industry. satyendra; June 28, 2017; 7 Comments ; calcining, dolomite, flux, lining, magnesia, refracory material, Rotary kiln, sintering, vertical kiln, Dolomite – Its Processing and Application in Iron and Steel Industry. Dolomite is an anhydrous carbonate mineral.
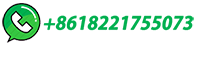
Sponge Iron | SpringerLink
(i) Discuss the principle of rotary kiln process for sponge iron production. (ii) What are the problems of rotary kiln process and how to overcome them? 4. Discuss the salient features of rotary kiln process. 5. Why coal-based sponge iron cannot form HBI? 6. Discuss the principle of Midrex process for production of HBI. 7.
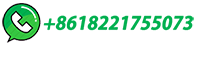
Premium rotary kiln sponge iron For Industries
Invest in brilliant rotary kiln sponge iron at Alibaba and boost your productivity. The rotary kiln sponge iron are designed for cement production efficacy.
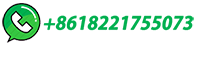
Energy survey of the coal based sponge iron industry
In the sponge iron process concentrated and finely divided iron ore is reduced in solid phase into sponge iron at high temperatures in rotary kiln. The process is very energy demanding. In order to identify the largest losses and to find ways to increase the efficiency, an energy survey of the sponge iron plant was carried out for a number …
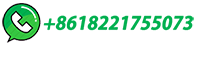
Advances in Rotary Kiln Sponge Iron Plant
Contents: IntroductionRotary Kiln Process of Making Sponge IronThermodynamic Considerations: Feasibility of ReactionAerodynamics inside a Sponge Iron Rotary KilnMathematical Modelling in Rotary Kiln Sponge Iron MakingPhysical Movement of Solids inside a Rotary Kiln: Charge Movement and Coal …
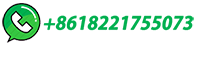
sponge iron rotary kiln in China
The sponge iron rotary kiln of our company is not only economical, but also has many performance characteristics, such as reliable quality, long service life, good calcination effect, high efficiency, safety and stability, and low cost. It allows users to purchase reliable and good sponge iron rotary kiln equipment at less cost, so that …
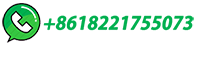
Decarbonisation Options for Rotary Kiln-Induction …
Figure 1: Schematic diagram of a rotary kiln-based sponge iron plant integrated with a captive power plant and induction furnace for crude steel production
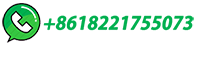
Computational fluid dynamics analysis of sponge iron rotary kiln
The temperature profiles of the gas and charge in a coal-fired rotary sponge iron kiln affect both the iron ore reduction process and accretion formation. The temperature profile of charge is … Expand
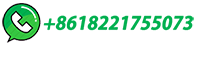
Sponge Iron Production in Rotary Kiln
This book comprehensively deals with the production of sponge iron in the rotary kiln. The book is divided into 17 chapters. The initial chapters give a brief on the fundamental theories and basic principles of sponge iron production, commercially used DR (direct reduction) processes and physico-chemical principles of sponge iron …
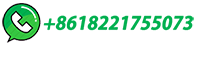
Analysis of temperature profile and % metallization in rotary kiln …
The present paper deals with 2D CFD model of sponge iron rotary kilns. Using this model the effects of variations of input parameters, such as angle of inclination, number of rotation and mass flow rate of iron ore are studied on output parameters like Fe content, temperature profile.
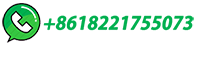
Dynamic quality prediction and control in rotary sponge iron kilns
The quality of sponge iron produced in the coal-fired rotary kilns at TATA Steel Long Products Limited (TSLPL) is permitted to vary in a small window of 80-83% Fe.
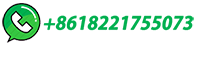
A study on the accretion formation in DRI kilns and …
Abstract: Direct reduction of iron ore with aid of either carbon or natural gas under controlled temperatures and pressures within a rotary kiln generates sponge iron as a product. However rotary kiln performance is adversely affected by the ring formation known as accretion. These accumulated sintered solid particles which
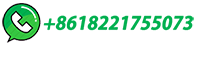
Innov Engineering Pvt. Ltd
Innov Engineering is a leading manufacturer and supplier of advanced and custom-made rotary kilns used to heat solids at high temperatures, ensuring durability, efficiency, and longevity. ... We design custom solutions to provide effective and low-maintenance rotary kilns operations for quality sponge iron production through our extensive ...
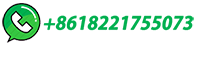
New Sponge Iron Rotary Kiln Design In Sponge Iron …
A new design sponge iron rotary kiln energy comprehensive utilization system. High energy efficiency, increased lung heat recovery system, energy saving.
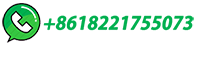
Steel Exchange India Ltd
The company is able to manufacture 0.225 MTPA of Sponge Iron per annum. Each Rotary Kiln is 70 meters long, 4.4 meters wide and inclined at 2.5%. The kilns each have a thick 250mm refractory lining inside, 3 support rollers and a dual drive with two 155 kW DC Motors. Each Kiln also has seven shell air fans and air tubes for air supply inside ...
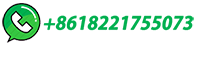