Iron Ore Characterization Techniques in Mineral Processing
The most common element that makes up rock formations is iron, which accounts for about 5 percent of the earth's crust. India alone has a significant reserve of iron ore in the world [].The two most common iron minerals, hematite and magnetite, and are widely exploited for commercial applications, particularly steel production [].However, in addition to these …
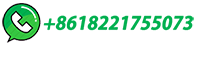
Iron Ore Processing: From Extraction to Manufacturing
The final stage in iron ore processing is ironmaking, where the iron ore is transformed into molten iron through a process called reduction. The most common method of ironmaking is the blast furnace route. In a blast furnace, iron ore, coke (carbon), and fluxes (limestone or dolomite) are loaded into the furnace from the top.
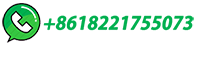
SINTERING AND PELLETISATION OF INDIAN IRON ORES
High grade iron ore less than 10% of the total reserves. ROM iron ore with Fe less than 58 – 60% discarded as waste. After beneficiation iron ore availability can improve by about 50%. Steel community and the country demand technological solutions for utilising low grade ores. The technology task that would be imperative: 1.
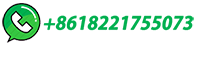
Existing and New Processes For Beneficiation of Indian Iron …
10.1007@s12666-020-01878-z (1).pdf - Free download as PDF File (.pdf), Text File (.txt) or read online for free. This document discusses beneficiation practices for Indian iron ores. It notes …
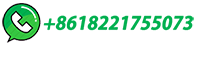
Your iron ore beneficiation solutions
iron ore recovery solutions across Australia, Canada, Brazil, India and Africa. Today, we are recognised by customers worldwide as the 'go to' partner for process solutions across the project lifecycle. Customers call us when they need fast, cost effective process improvements to lower costs, convert tailings into revenue or
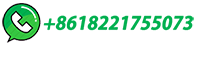
A review of ironmaking by direct reduction processes: …
In the former, the blast furnace uses iron ore, scrap metal, coke and pulverized coal as raw materials to produce hot metal for conversion in the BOF. Although it is still the prevalent process, blast furnace hot metal production has declined over the years due to diminishing quality of metallurgical coke, low supply of scrap metal and ...
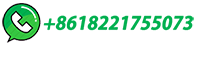
Insight of Reduction Roasting of a Low-Grade Goethitic …
The iron ore production in India increased by 27% during 2021–22 (April–January) compared to the preceding year, indicating a heavy demand for iron in the downstream steel Abstract This communication delves into a thorough examination of the reduction roasting–magnetic separation process for a low-grade Indian iron ore that is unrespon-
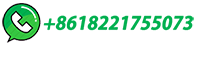
The Blast Furnace: A Vital Tool in Climate Neutral Ore-Based
The process of transformation of iron ore to steel involves a number of steps—irrespective of the exact process route followed. It usually involves a stage of primary winning of metal from mineral ore (ironmaking—with a liquid or solid output) followed by a refining step (steelmaking—always with a liquid output).
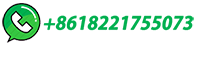
IRON ORE Indian Minerals Yearbook 2019
IRON ORE Indian Minerals Yearbook 2019 (Part-III: Mineral Reviews) 58th Edition IRON ORE (FINAL RELEASE) GOVERNMENT OF INDIA MINISTRY OF MINES INDIAN BUREAU OF MINES Indira Bhavan, Civil Lines, NAGPUR – 440 001 PHONE/FAX NO. (0712) 2565471 PBX : (0712) 2562649, 2560544, 2560648
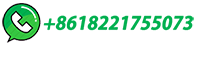
Iron Ore Pelletizing Process: An Overview
The iron ore pelletizing process consists of three main steps: 1. Pelletizing feed preparation and mixing: the raw material (iron ore concentrate, additives ... the balling step, in this case using a disc pelletizer, and the induration step. Figure 2. Typical pellet plant using disc pelletizer as balling technology. Source: Elaborated by the ...
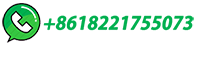
IRON ORE Indian Minerals Yearbook 2019
onnes, i.e., about 69% during 2018-19.Gradewise analysis of the current year's output reveals that out of total output of 206.44 million tonnes, iron ore lumps constituted 66.61 million …
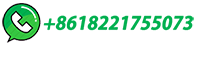
Steel Coal and Iron ore report
resources like iron ore, coking/metallurgical coal, steel scrap and power. India has adequate iron ore reserves, and utilization of iron ore fines and low-grade iron ore is a key determinant for the success of the industry. India does not have sufficient reserves of coking/metallurgical coal and is dependent on imported coking coal which are
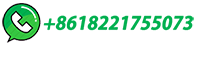
Existing and New Processes for Beneficiation of Indian Iron …
The iron ore industries of India are expected to bring new technologies to cater to the need of the tremendous increase in demand for quality ores for steel making. With the high …
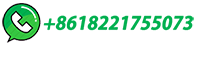
Advances in Low Grade Iron Ore Beneficiation
iron ore is expected to rise by more than 200 million tonne per year to meet the internal demand & export. This additional requirement of iron ore will need beneficiation of low grade ore/fines …
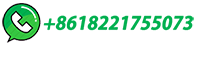
Hazard Identification, Risk Assessment, and Control …
General. India has the fourth largest iron ore reserves in the world after Russia, Brazil, and Australia.[] As per the survey conducted by the Indian Bureau of Mines (IBM) in April 2000, India had 9919 million tonnes of recoverable reserves of haematite and 3546 million tonnes of magnetite.[]As good quality iron ore deposits are depleting very fast, beneficiation …
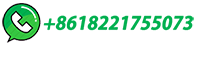
(PDF) A Case Study: Iron Ore Mining in India
India's steel vision of 2030 requires a huge amount of quality iron ore. The utilization of low-grade iron ores such as banded iron ores will play an important role to achieve the same production.
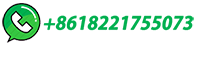
Iron Ore Characterization Techniques in Mineral …
India alone has a signicant reserve of iron ore in the world [1]. The two most common iron minerals, hema-tite and magnetite, and are widely exploited for commercial …
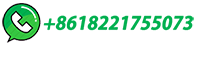
Iron Ore Characterization Techniques in Mineral …
India alone has a signicant reserve of iron ore in the world [1]. The two most common iron minerals, hema-tite and magnetite, and are widely exploited for commercial applications, particularly steel production []. However, in 2 addition to these minerals that are commonly used to extract metallic iron, iron ore deposits are frequently contaminated
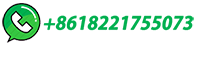
Processing the ores of rare-earth elements | MRS Bulletin
Rare-earth elements (REEs) are required for use in modern high-tech applications and demand has increased significantly over the last decade. 1 However, processing of REE ores poses potential hazards to human health and the environment due to challenges in the management of thorium (Th) and uranium (U) in waste products. 2 If well managed, REE can …
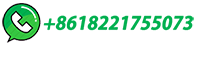
(PDF) An Overview of the Reduction-Smelting Process of Iron …
Preliminary studies have revealed that there are tendencies to achieve more than a 90 % metallization degree from the direct reduction of iron ore/oxides using non-coking coal or charcoal as a ...
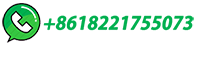
(PDF) iron-steel making From start to finish
PDF | On Dec 27, 2019, Mr. Bhavesh R Rana published iron-steel making From start to finish | Find, read and cite all the research you need on ResearchGate
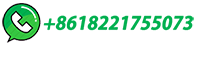
pdf iron ore process india steps – Grinding Mill China
Uncertainty in sampling – iron ore 6 Sampling procedure ISO 3082:2000. Iron ores … » Free Online Chat. DEVELOPMENT OF PROCESS FOR BENEFICIATION OF LOW-GRADE IRON ORE … DEVELOPMENT OF PROCESS FOR BENEFICIATION OF LOW-GRADE IRON ORE SAMPLES FROM ORISSA, INDIA 1239 from 64.81 to 65.08 as well as iron recovery …
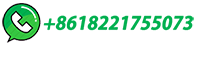
Chrome ore beneficiation challenges & opportunities – A …
Rao et al. (1987), depicted that, low grade chrome ore with Cr 2 O 3 of about 20–30% of Sukinda region of India, can be beneficiated to a marketable grade of 45% Cr 2 O 3 with 45% recovery, by grinding the chrome ore (d 80 passing size 260 μm) and desliming the same using hydrocyclone and by treating the under flow on sand table and the ...
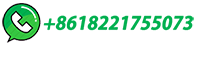
Iron Ore Processing
Key words : L ow grade iron ore, beneficiation, gravity, magnetic, sinter, pellet . 1. Introduction India is one of the leading producers and exporters of ir on ore in the world with over 28 …
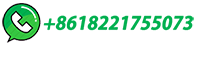
(PDF) Froth flotation process and its application
The paper is about the froth flotation process and its application. It is a metallurgical process for the extraction of metals in a pure state from their ores: especially for sulfide ores.
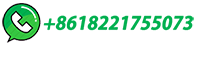
BENEFICIATION OF IRON ORE
2.3 Processing of Iron ore in India 8 2.4 Slimes of Iron ore 11 3. BENEFICIATION PLANT STUDY OF NOAMUNDI ... Fig 1.1 Graphical depiction of grade wise distribution of hematite …
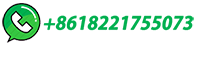
(PDF) Planning an Iron Ore Mine: From Exploration Data to …
For banded iron formation-hosted deposits accurate boundary modelling is critical to ore-grade estimation. Key to estimation fidelity is the accurate separation of the different domains within the ...
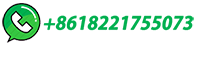
Iron ore: Mineralogy, processing and environmental sustainability
Sintering is an important step in the iron-producing process, where loose iron ore fines (< 6 mm) are transformed at temperatures between 1250 and 1350 C into a mechanically stable composite that ...
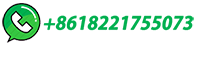
Iron Ore Characterization Techniques in Mineral Processing
Numerous occurrences of medium to high grade (44.1 to 65 wt%) pocket type iron ore bodies within the Meso to Neo-Proterozoic albitites and meta-sedimentary rocks are exposed around the south and ...
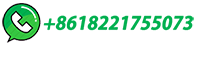
ENERGY-EFFICIENT TECHNOLOGY OPTIONS FOR DIRECT …
3.0 Energy-efficient Technologies in Direct Reduction of Iron Process 17 3.1 Waste Heat Recovery for Power Generation 18 3.2 Iron Ore Preheating Rotary Kiln Using Waste Heat Recovery System 20 3.3 Coal Gasification for Partial Substitution in Rotary Kiln 22 3.4 Waste Heat Recovery-based Absorption Chiller 23
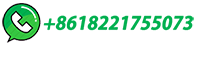