Portland Cement Association
The Portland Cement Association is the premier organization serving America's cement manufacturers. With a focus on safety and sustainability, we support innovative approaches at every stage of the manufacturing and distribution processes, helping members to continuously improve the nation's infrastructure and economy. ...
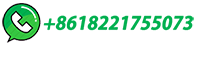
Cement hydration
Cement hydration. By the process of hydration (reaction with water) Portland cement mixed with sand, gravel and water produces the synthetic rock we call concrete. Concrete is as essential a part of the modern world as are electricity or computers. Other pages on this web site describe how PC is made and what is in it.
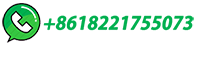
Portland Cement: Properties, Composition, Types and Uses
Cement is the basic ingredient of concrete, mortar and plaster which consists of a mixture of oxides of calcium, silicon and aluminium. This article on Portland Cement discusses its composition, manufacturing process, properties, type, uses, etc.
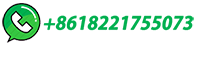
PPC Cement Manufacturing Process
Portland Pozzolana Cement Manufacturing Process. Portland pozzolana cement shall be manufactured by mixing and inter-grinding Portland cement clinker, pozzolanic materials, and gypsum. The manufacturing process is approximately the same as ordinary Portland cement, which can be divided into four processes: raw material crushing, raw material ...
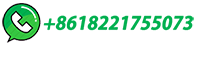
Electric recycling of Portland cement at scale | Nature
In the process shown in Fig. 3e, and described in the patent application 26 for Cambridge Electric Cement (CEC), the emitting lime flux used in steel recycling is replaced by recovered cement ...
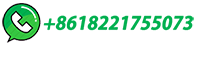
Brimstone | Deeply Decarbonized Cement
This initiates the negotiations process to finance Brimstone's first-of-a-kind decarbonized portland cement plant, which would avoid 120,000 metric tons of CO2/year. ... Brimstone's process makes ASTM C150 ordinary portland cement, the type of cement used in virtually all construction today. Cost-Competitive at Scale.
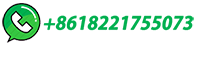
The Cement Plant Operations Handbook
Portland cement in today's world 2. Raw materials management system – 22. Concrete problems 16 1. Raw materials – 2. Raw mix – 3. Reserves – 4. Crushing ... Cement milling process summary data – 8. Typical equipment downtime 110 1. Storage of clinker and other components – 2. Cement milling – 3. Separators (classifiers) – 4.
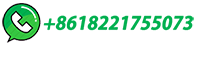
How Cement is Made
Stage of Cement Manufacture. There are six main stages of the cement manufacturing process. Stage 1: Raw Material Extraction/Quarry The raw cement ingredients needed for cement production are limestone (calcium), sand and clay (silicon, aluminum, iron), shale, fly ash, mill scale, and bauxite. The ore rocks are quarried and crushed into smaller pieces of about 6 …
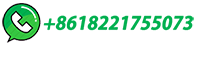
Cement
Cement - Composition, Properties, Major Cements: Portland cement is made up of four main compounds: tricalcium silicate (3CaO · SiO2), dicalcium silicate (2CaO · SiO2), tricalcium aluminate (3CaO · Al2O3), and a tetra-calcium aluminoferrite (4CaO · Al2O3Fe2O3). In an abbreviated notation differing from the normal atomic symbols, these compounds are …
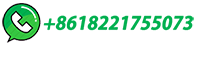
Portland Cement: A Concrete History With …
The composite material, consisting of three key raw materials, is a hydraulic cement. It works through a process called hydration, which entails adding water to dry cement particles or powder. This initiates a chemical …
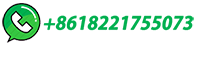
Background Facts and Issues Concerning Cement and …
hydraulic (chiefly portland) cement and, to some degree, concrete. Part 2 describes the monthly and annual U.S. Geological Survey (USGS) cement industry canvasses in general terms of their coverage and ... Process chemistry ..... 25 Calcination zone reactions ...
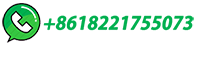
Manufacturing of Cement By Dry and Wet Process
Burning: In this operation, the slurry is directly fed into a long inclined steel cylinder called a Rotary kiln.In this kiln there are 3 different zones shown in fig. below. Cement Manufacturing Process Flow Chart (i) Drying Zones: In the wet process, the drying zone is comparatively larger than the dry process. It is because the raw material in slurry form is directly fed into the kiln …
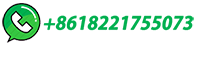
Manufacturing of Portland Cement – Process and Materials
A diagram of the process, which encompasses production of both portland and masonry cement, is shown in Figure 11.6-1. As shown in the figure, the process can be …
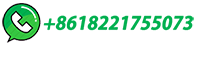
New approach suggests path to emissions-free cement
A variation of this process can be used to convert calcium carbonate (CaCO 3) into calcium hydroxide (Ca(OH) 2), which can then be used to make Portland cement without producing any greenhouse gas emissions. Cement production currently causes 8 percent of global carbon emissions.
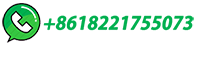
11.6 Portland Cement Manufacturing
11.6 Portland Cement Manufacturing. ing11.6.1 Process Description1-7Portland cement is a fine powder, gray or white in color, that consists of a mixture of hydraulic cement materials …
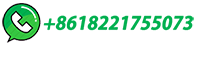
Applications of Cement
Full-depth reclamation (FDR) with cement is a process where an old, damaged asphalt road is ground up and mixed with cement, then compacted to form a new, stabilized base layer. Because this technique recycles deteriorated road surfaces, it is both cost-effective and environmentally friendly. ... White portland cement allows for a wide range of ...
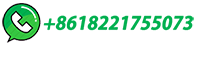
Concrete: Scientific Principles
The water causes the hardening of concrete through a process called hydration. Hydration is a chemical reaction in which the major compounds in cement form chemical bonds with water molecules and become hydrates or hydration products. ... Hydration of Portland Cement. Concrete is prepared by mixing cement, water, and aggregate together to make ...
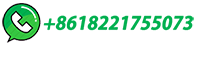
Portland Cement Manufacture | Portland …
Specific Portland cement manufacturing process as follows: STEP1: Crushing and pre-homogenization of Portland cement. In the portland cement production, most of raw materials should be crushed, such as limestone, clay, …
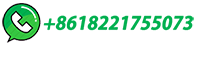
Manufacture of Cement- Materials and …
Manufacture Process of Cement. The manufacture procedures of Portland cement is described below. 1. Mixing of raw material. The major raw materials …
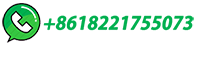
The Composition of Portland Cement and Production Process
Portland cement was first introduced in 1824 by Joseph Aspdin, a brick layer from Leeds, England [5]. On setting, the color of cement resembles the color of rocks near Portland, …
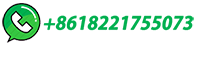
How Cement is Made
The Cement Manufacturing Process. While each cement plant may differ in layout, equipment, and appearance, the general process of manufacturing portland cement is the same: crushed limestone and sand are mixed with …
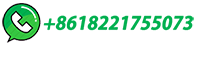
Best ways to cut carbon emissions from the …
Around 3.5 billion tonnes of Ordinary Portland Cement, a critical building material worldwide, are produced annually – but every tonne emits up to 622 kg of carbon dioxide (CO 2) ... The cement production process. Cement …
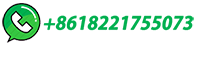
What is Portland Cement and How it is Manufactured
In the wet process, the limestone is first crushed into small pieces, and then it is mixed with clay or shale along with water to form a slurry. The slurry is a creamy liquid, and it has a water content of 35% to 50%. This mixture is fed to the furnace cylinder, and from here, it follows the same path as the dry process for making Portland Cement.
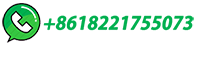
What is Portland Slag Cement (PSC)? Properties, Use, …
The manufacturing process of Portland Slag Cement (PSC) involves the following steps: Obtaining Granulated Blast Furnace Slag: Granulated blast furnace slag is obtained as a by-product in the iron and steel industry. During the production of iron, blast furnaces produce molten slag, which is then quenched rapidly with water or air to form ...
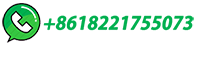
Portland Cement
Genetically-enriched microbe-facilitated self-healing nano-concrete. Brajadulal Chattopadhyay, in Smart Nanoconcretes and Cement-Based Materials, 2020. 1.3 Portland cement. Portland cement is the basic ingredient of concrete, mortar and plaster which consists of a mixture of oxides of calcium, silicon and aluminum. Portland cement and similar materials are made by …
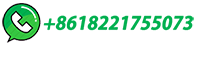
Ordinary Portland Cement -Constituents, Properties, Types …
Ordinary Portland cement is one of the most widely used type of Cement. Types, properties, constituents, manufacture, uses and advantages of Ordinary Portland Cement is discussed. ... There are 3 type of manufacture process of cement Dry Process; Wet Process; Semi wet Process; Crushing and grinding process varies depending upon the type of ...
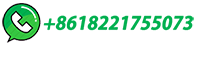
Cement | Definition, Composition, Manufacture, History,
Cements may be used alone (i.e., "neat," as grouting materials), but the normal use is in mortar and concrete in which the cement is mixed with inert material known as aggregate.Mortar is cement mixed with sand or crushed stone that must be less than approximately 5 mm (0.2 inch) in size. Concrete is a mixture of cement, sand or other fine aggregate, and a coarse …
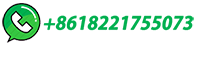
What is the Manufacturing Process of Portland …
The production of Portland cement, a cornerstone of modern construction, involves a meticulous selection of raw materials. Understanding these materials is crucial to grasping the overall manufacturing process. Common …
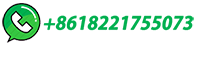
All about the Wet Process of Cement Manufacturing
For example, we add gypsum to obtain the ordinary Portland cement and add gypsum and fly ash to obtain the Pozzolana Portland Cement. Applications of Wet Process Cement Manufacturing. Wet process cement manufacturing …
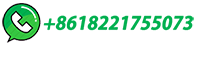
Cement Manufacturing Process
Cement Manufacturing Process. Cement Manufacturing Process. Cement Manufacturing Process. Cement is a material which is used to bind other materials together. Binding means it has an effect of gluing the …
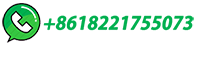