NextGen Pelletizing™
Iron ore pelletizing is crucial for the "green" future Outotec Traveling Grate Pelletizing ... By improving our customers' energy and water efficiency, increasing their productivity, and reducing environmental risks with our product and process expertise, we are the partner for positive change. ...
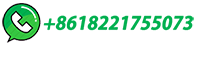
Use of Boron Compounds as Binders in Iron Ore …
The most commonly employed one is pelletizing in iron ore industry. In pelletizing, iron ore, water and a binder are balled in a mechanical disc or drum to produce agglomerates. Bentonite is the most widely used binder. ... use as binders in iron ore pelletizing, with an objective of finding the material that would produce the highest-quality
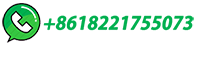
Iron ore pelletization
A brief introduction to recent developments in iron ore pelletizing is provided in this chapter, including the world output of fired pellets, pellet production processes, …
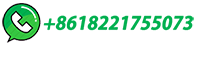
Iron Ore Pelletizing Process: An Overview
The iron ore pelletizing process consists of three main steps: Pelletizing feed preparation and mixing: the raw material (iron ore concentrate, additives—anthracite, dolomite—and binders are prepared in terms of particle size and chemical …
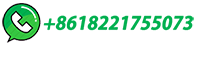
Pelletization
However, the following issues need to be considered when evaluating and selecting organic binders for pelletizing applications: Water migration speed ... As the raw materials available to produce fluxed pellets become more difficult, more attention is being paid to the use of hydrated lime in iron ore pelletizing.
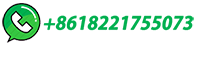
Traveling Grate Pelletizing Plant
Traveling grate pelletizing plant is an induration technology for iron ore pellet production for a wide range of plant capacities.
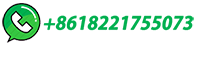
Iron Ore Pelletization: Part I. Fundamentals | Semantic Scholar
ABSTRACT The behavior of iron ore pellet binders is complex. Any pellet binder is subject to a handful of practical requirements: that it be readily dispersed through a pellet, that it effectively controls the movement of water within the pellet, and that it contributes to the inter-particle bonding within the pellet. Meeting these requirements …
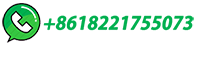
Pelletizing Plants | BOLLFILTER
Pelletizing is the process through which iron ore fines are transformed into an agglomerated form called "iron ore pellets" suitable for use in an iron-making furnace at a steel mill, such as a blast furnace or electric arc furnace.
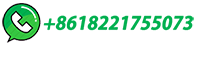
Iron Ore Pelletizing Process: An Overview
The iron ore pelletizing process consists of three main steps: Pelletizing feed preparation and mixing: the raw material (iron ore concentrate, additives —anthracite, dolomite—and …
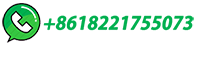
Iron Ore Pelletizing
The high water absorbtion and swelling capacity of NATIONAL STANDARD PG promotes balling of iron ore concentrate. This improves the green, drop, and dry strengths of the pellet which prevents the collapse of the pellets as they are transported to the kiln.
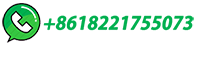
ALTERNATIVE BINDERS TO BENTONITE FOR IRON ORE PELLETIZING…
Iron ore pellets are essential inputs for producing direct reduced iron (DRI), but the conventional binders, used in iron ore pelletizing, introduce gangue oxides to the DRI and consequently ...
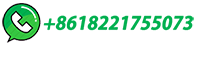
Use of Organic Binders and Borates in Pelletizing of Iron …
Even though the use of bentonite in iron ore pelletizing is essential, it is also a problem due to its adverse effects, caused by the impurities introduced with bentonite, on iron-steel economy.
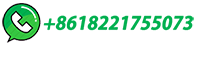
Feasibility study of novel water-lean solvent technology for …
Feasibility study of novel water-lean solvent technology for CO2 capture from iron ore pelletization flue gas. ... and 40 mg/m3 of iron particles. The iron particles collected from a straight grate iron ore pelletizing plant located in Vale's operation in the state of Espirito Santo, were added to fresh eCO2SolTM and showed that the presence ...
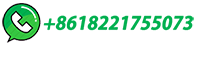
THE GROWING IMPORTANCE OF PELLETIZING FOR IRON …
PDF | In the last years, pelletizing has been playing an important role in iron ore mining and in iron production (iron making and direct reduction).... | Find, read and …
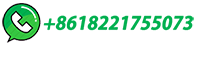
IMPROVEMENT OF MECHANICAL STRENGTH OF IRON …
agglomeration technique is pelletizing by which a mixture of iron ore, water, and binder is rolled up in a mechanical disc or drum to produce agglomerates (green or wet pellets) (Sivrikaya and Arol, 2010).
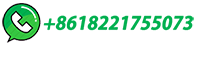
Iron Ore Pelletization Technology and its Environmental …
Agglomeration technologies such as Pelletization / Sintering have to be added to Steel Plant so that concentrates can be used as feed material. This paper will give an …
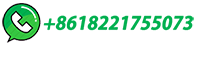
Iron Ore Pelletizing Essential in Meeting Future Steel Needs
As the world leader in tumble growth agglomeration, FEECO provides a variety of services and equipment for iron ore pelletizer plants. As the needs of the steel industry change, one production component looks to be increasingly important in meeting the needs of the modern steel industry: iron ore pelletizing. Iron ore pelletizing, or balling, is the …
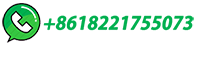
EVOLUTION AND GROWTH OF IRON ORE PELLETIZING
In the last years, pelletizing has been playing an important role for iron ore mining and ironmaking. Some factors have contributed to this fact like as: depletion of high-grade iron ore reserves ...
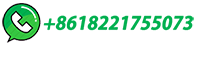
(PDF) IRON ORE PELLETIZING PROCESS
As greater amounts of fine iron ore concentrates enter the marketplace, new investments in iron ore pelletizing capacity are inevitable to deliver these concentrates to steel industry consumers.
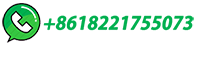
Iron ore pelletization
A brief introduction to recent developments in iron ore pelletizing is provided in this chapter, including the world output of fired pellets, pellet production processes, preparation of pellet feed, inorganic and organic binders, and new additives.
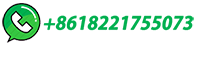
Use of Organic Binders and Borates in Pelletizing of …
in the iron ore industry. In iron ore pelletizing, bentonite is the conventional binder and used 0.5-1.5% by weight of iron ore. Bentonite with its high water adsorption ...
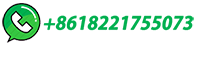
Use of Boron Compounds as Binders in Iron Ore Pelletization
The most commonly employed one is pelletizing in iron ore industry. In pelletizing, iron ore, water and a binder are balled in a mechanical disc or drum to produce agglomerates. Bentonite is the most widely used binder. However, it is considered as an impurity due to its high SiO 2 and Al 2 O 3 content. Many researchers have …
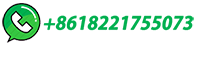
Iron Ore Pelletization Technology and its Environmental …
The actual requirement of water is approx. 1200 m3 /day. The industry has ETP to treat the water and use in the system resulting into zero discharge. 8.3. ... after commissioning of about 9 no. of units which are at various stages of commissioning. • There are several iron ore pelletizing processes/technologies available in the world ...
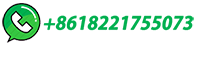
Effect of colloidal agents in iron ore pelletizing
Organic binders have been used to replace bentonite in the pelletizing process of iron ore. In this research, colloidal agents were evaluated in a pelletizing process comparing their influence ...
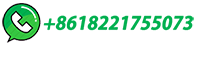
Iron Ore Pelletization: Part I. Fundamentals
Iron ore concentration typically involves comminution, separation, and agglomeration. ... that it effectively controls the movement of water within the pellet, and that it contributes to the inter-particle bonding within the pellet. ... and provides a framework so that the chemical factors leading into an effective pelletizing process can be ...
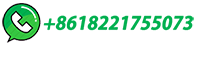
Understanding Pellets and Pellet Plant Operations – …
The location of a pelletizing plant affects the method of receiving raw materials such as iron ore, additives and binders. Many pelletizing plants are located near iron ore mines. This is because these plants are installed to pelletize the iron ores which are beneficiated at these mines. Such plants receive the iron ore by rail and/or slurry ...
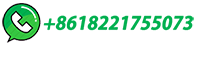
pelletizing iron ore water use m3
The most commonly employed agglomeration technique is pelletizing by which a mixture of iron ore, water, and binder is rolled up in a mechanical disc or drum to produce agglomerates (green or wet pellets) Figure 1: Iron pellets The pelletizing process is a process which contains numerous subprocesses, or process segmentsOct 06, 2017 The …
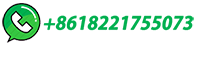
Iron Ore Agglomeration Technologies
This iron ore is mixed with water, bentonite (or other organic binders less expensive and contaminant [12]), and lime and treated ... Regarding pelletizing technologies, it is possible to mention two that are used at industrial scale: rotary drum and rotary disc. The rotary drum is a large drum-shaped cylinder that is
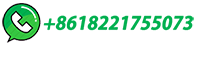
The Iron Pelletizing Process
Explore the iron and steel industry's use of iron ore, focusing on the pelletizing process of low-grade ores. Learn about the various sub-processes, including crushing, grinding, …
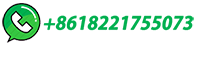
What Are Iron Ore Pellets and How to Make Them? | Fote …
98% of iron ore is used as raw material for steel and iron. Iron ore pellets are preferred instead of raw ore when smelting steel because pelletization can maximize the use of iron ore and improve the blast furnace performance. What are iron ore pellets? Iron ore pellets are spheres of typically 8-16 mm to be used as feedstock for blast …
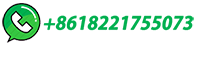