Crushing Principles of Mechanical Crushing
Optimization of a Final Crushing Stage. . Optimization of one parameter (CSS) can be done by sampling and analysis The invested time and lost production will quickly be repaid by …
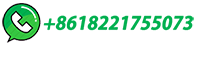
What is a ?
What is a ? January 14, 2021 | webheadscompactors | News / Resources. s are used for crushing empty, full, half-full, line rejects, or off date products aluminum or steel cans for easier recycling. A can save you a significant amount of time and space. Using a to reduce the capacity of waste materials …
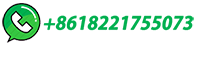
Design and development of cocoa pod breaking and beans extraction machine
This designed machine severs the poles and ruptures the pods facilitating extraction of the beans on the hulls. It can be assembled and disassembled easily, reliably and without any risk for the user.
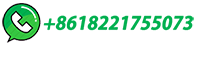
Construction Working and Maintenance of Crushers for …
For primary crushing with a reduction ratio of 6 to 1. When a relatively coarse product is desired, top size usually larger than 38 mm (1 1/2") Closed Circuit Crushing System To control top …
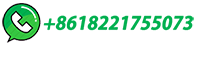
Crushing Machine Operator Job Description
The Crushing Machine Operator job function is to set up, operate, or tend machines to crush, grind, or polish materials, such as coal, glass, grain, stone, food, or rubber. Duties: The Crushing Machine Operator reads work orders to determine production specifications and information. The Crushing Machine Operator observes operation of …
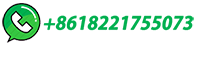
Construction Working and Maintenance of Crushers …
crusher for another pass through the machine. Efficiency of a multiple stage crushing plant can be maximized by operating a primary crusher at a setting which produces a satisfactory feed size for the secondary crusher and operating the secondary crusher (or the last stage crusher) in a closed circuit. Glossary of Terms
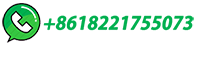
Selecting the right crusher for your operations
Crushing is demanding and arduous work, so machines must be durable enough to withstand the daily rigours of the task. It is widely accepted that operators that invest in quality equipment and components right from the start tend to save money in the long run by reducing the costs of upkeep and future maintenance.
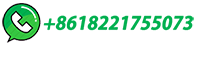
AMIT 135: Lesson 5 Crushing – Mining Mill Operator Training
K = machine characteristic constant: L min = closed side setting: θ – jaw angle . Critical Jaw Crusher Parameters A Diagram of Jaw Crushers [image: (135-5-14)] ... The rate at which the crushed particles move through the crusher is a function of the cycle frequency, Ï….
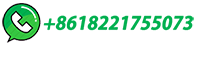
Empty Fruit Bunch Shredder, EFB Fiber Crushing Machine
Introduction of EFB Fiber Crushing Machine Hammer Mill Crusher is a machine to shredder the EFB fiber again into 4~10mm length. It is also a professional pulverizer to process lumber trims, slabs, veneer trims, edgings, blocks, oversized chips and solid wood. The pulverizing room is designed to be wide to crush material.
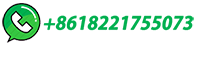
How Crusher Machines Work: A Comprehensive Guide
This comprehensive guide will take an in-depth look at how crushing machines function to better understand their purpose. The primary component of any crusher machine is its internal mechanism which works together with other parts to perform its specific task. Inside a crusher machine, several moving parts interact with one another to produce ...
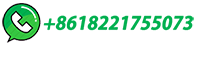
Grinding Machine-Parts, Functions, and Types
The Function of a Grinding Machine: Finishing work pieces that require high surface quality (e.g., low surface roughness) and high shape and dimension accuracy are often completed using grinding. Grinding, with its 0.000025 mm precision in dimensions, is typically used as a finishing operation that removes only a small amount of metal (between ...
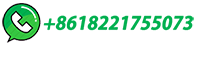
Prediction of Size Distributions from Compressing Crusher Machines …
The choice and mix of breakage functions is a central subtopic i the analysis of the crusher machine processes. Known breakage functions are reviewed and evaluated. A new concept for determination of a true breakage operator which is related to physical properties of the crusher device and the size distribution of the feed material is introduced.
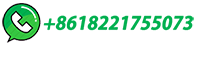
Types of Crushers Explained: Everything You Need …
The rotating shaft connects the two jaws; the moving jaw presses the material against the stationary jaw. On the contrary, Blake jaws crushers vs gyratory crushers, the bottom is where the moving jaw is pivoted in the latter …
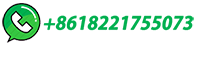
Functions of concrete batching plants and its different types
Content on the Site and/or the Services is provided to you AS IS for your information only and may not be used, copied, reproduced, distributed, transmitted, broadcast, displayed, sold, licensed, or otherwise exploited for any other purposes whatsoever without the prior written consent of the respective owners. We reserve all rights not expressly granted in …
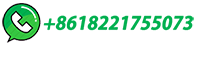
Selecting the right type of crushing equipment
In most cases, the fine crushing and cubicising functions are combined in a single crushing stage. The selection of a crusher for tertiary crushing calls for both practical experience and theoretical know-how. ... Jaw …
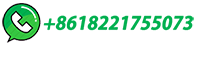
Crushing
Relation between Feed size and Shape. The greater reduction ratio the worse particle shape. Inter particle breakage improves shape. When crushing a bed of material weaker particles will …
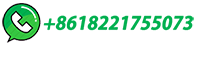
Mechanical Operations Questions and Answers – Crushers
Explanation: At low speeds, the balls simply roll over one another and little crushing is obtained, thus reducing the equality of product. 7. At high speed, Crushing obtained can be _____ a) Minimum b) Maximum c) No effect ... Electrical Machine Design MCQ Questions; Chemical Reaction Engineering MCQ Questions; Subscribe to our Newsletters ...
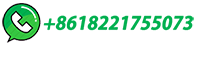
Understanding the Cone Crusher Working Principle: How It …
In summary, the hydraulic system is a crucial component of the cone crusher that enables precise control over the machine's various functions. It allows for quick and easy adjustments to be made to the crusher's settings, prevents damage to the machine, and ensures optimal performance in high-volume production environments.
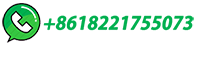
How to Crush Charcoal?
For industrial-scale charcoal production, investing in a specialized charcoal crushing machine is the most efficient choice. These machines are designed to crush charcoal effectively and consistently, catering to large-scale demand. ...
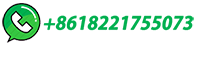
Understanding Cone Crusher Parts Names, …
The following are some of the types of cone crusher parts: Mainshaft and head center: The mainshaft is a rotating component that connects the mantle to the motor. The head center is a stationary part that supports the …
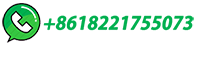
Crushers: Breaking Down the History of these Machines
A gyratory crusher was patented by Philetus W. Gates in 1881. Thomas A. Edison also designed a rock crusher to use in his own mining operation. Edison's design used giant rolls to function as a primary crusher. These machines never gained much popularity though because the gyratory and jaw crushers were more versatile.
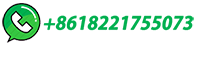
Reliability analysis and optimization of the hammer rotor of …
During the operation of a forage crusher, the common issues usually faced are shorter mean time between failures and low reliability. The hammer rotor, a critical component, is prone to fatigue fracture, hammer wear, violent vibration of the rotor system caused by uneven wear of the hammers, and other issues that reduce the machine's service life and reliability. In …
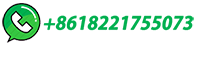
Types of Rock Crushers | Quarry Crushing …
However, you'll find four basic designs—cone, jaw, gyratory, and impact crushers—operating within many crushing plants. Jaw Crushers. In compression crushing, jaw crushers tend to be more of a blunt instrument compared to …
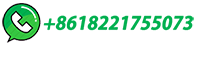
Construction Working and Maintenance of Crushers for …
crusher for another pass through the machine. Efficiency of a multiple stage crushing plant can be maximized by operating a primary crusher at a setting which produces a satisfactory feed size for the secondary crusher and operating the secondary crusher (or the last stage crusher) in a closed circuit. Glossary of Terms
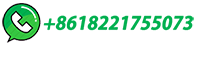
A Comprehensive Guide to Stone Crusher Machines
Stone crusher machines are essential tools in the construction industry, used to crush rocks and stones into smaller pieces for a variety of applications. This guide provides an overview of stone crusher machines, including their history, components, applications, and buying considerations. Whether you are a contractor, landscaper, or building owner, this guide …
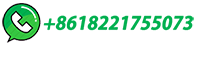
6 Types of Coal Crusher: Which Is Best for Crushing My Coal?
To ensure that coal is not affected by over-crushing while achieving the required particle size and output requirements, FTM Machinery will help you choose the optimal coal crusher machine. 1. Jaw crusher The jaw crushers are popular primary crushers for coal. They are often used in mines and quarries where large amounts of coal are mined.
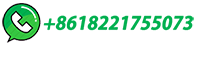
The Ultimate Guide to Jaw Crushing Machines: Types
A jaw crushing machine is a type of equipment used to break down hard materials, such as rocks, minerals, and ores. It consists of a fixed jaw plate and a movable jaw plate that is positioned in a V-shaped configuration. As the movable jaw plate moves back and forth, it crushes the material against the fixed jaw plate.
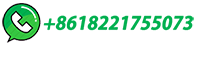
Design and Fabrication of Aluminium Tin
of laser cutting machine, Truama Bend V Series (bending machine), shearing machine, vertical bend saw, bench work and welding processes.[12] 1.1 Background of The Work: Different types of existing tin s are: 1) Manually operated single , 2) Manually operated multiple , Pneumatically operated single s
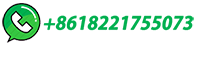
TECHNICAL NOTES 5 CRUSHERS
Figure 5.4 A typical internal classification function for a crusher Figure 5.5 The breakage function for crushing machines. This function has a value 1 at the representative size of …
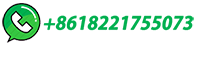
How it Works: Crushers, Grinding Mills and Pulverizers
Table Source: Wikipedia (Crushers) Cone crushers use a spinning cone that gyrates in the bowl in an eccentric motion to crush the rock between the cone surface, referred to as the mantle, and the crusher bowl liner.Gyratory crushers are very similar to cone crushers, but have a steeper cone slope and a concave bowl surface. As the gap between the bowl liner …
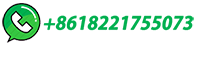