Direct Reduced Iron and its Production Processes – …
Direct reduced iron (DRI) is the product which is produced by the direct reduction of iron ore or other iron bearing materials in the solid state by using non-coking coal or natural gas. Processes which produce DRI by reduction of iron ore below the melting point of the iron are normally known as the direct reduction (DR) processes.
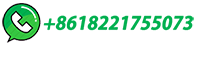
Advances in Low Grade Iron Ore Beneficiation
iron ore is expected to rise by more than 200 million tonne per year to meet the internal demand & export. This additional requirement of iron ore will need beneficiation of low grade ore/fines to get the major portion of increased demand. This paper deals in brief to use of available methodologies for beneficiation of iron ore in Indian context.
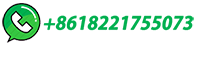
Iron Ore Beneficiation Process Flowsheet PDF | PDF
Iron ore beneficiation process flowsheet.pdf - Free download as PDF File (.pdf), Text File (.txt) or view presentation slides online. This document provides a flow diagram of a …
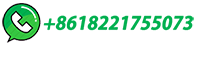
Magnetite Beneficiation Process Flow, Magnetite
Its characteristic is that the iron concentrate after conventional magnetic separation is selected by special beneficiation equipment to further improve the iron ore grade. Weak Magnetic – Strong Magnetic – Flotation Combined Process. The combined flotation process is mainly used to process polymetallic symbiotic iron ore and mixed …
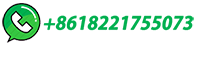
How to Extract Iron from Hematite: Methods and Plants
The process flow of the extraction of iron from hematite is as follows: crushing, grinding, extracting (flotation separation, magnetic separation, gravity separation, etc.) and drying. ... Fine-grained hematite refers to iron ore with an embedded particle size of less than 0.02mm. Based on the genesis of ore deposits, this kind of hematite is ...
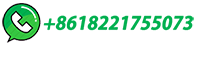
(PDF) Beneficiation and flowsheet development of a low grade iron ore …
In the present study a detailed characterization followed by beneficiation of low grade iron ore was studied. The Run of Mine (R.O.M) sample assayed 21.91 % Fe, which is very low grade in nature.
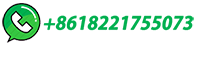
iron ore benefication prosses flow chart
Iron Ore To Steel Process Flow Chart. 24/10/2019 · Iron ore to steel raw material for manufacturing the tmt bar are iron ore coal dolomite in this process raw materials are piled recovered and mixed in required proportion the iron ore experiences beneficiation procedure to raise the iron substance at this point metal fines are gathered to shape a …
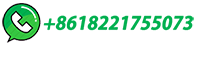
IRON ORE BENEFICIATION
IRON ORE BENEFICIATION Your Specialist in Process Equipment. PLEASE NOTE: ... TYPICAL IRON ORE BENEFICIATION FLOW SHEET Fine Product Effluent Pump Dewatering Screen Static Screen Panels Floats Drain & Rinse Screen Gyratory Crusher ROM Stockpile Sizing Screen Sizing Screen Spirals Thickener
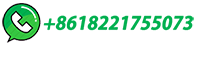
SGS MINERALS SERVICES – T3 SGS 960 11-20
SGS MINERALS SERVICES' EXPERTISE WITH BENEFICIATION Beneficiation is the process where ore is reduced in size and gange separated from the ore. Since all iron …
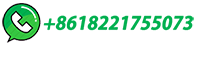
iron ore benefication prosses flow chart
Hematite Iron ore beneficiation process flow – FDM Home > Process flow and production line > Hematite Iron ore beneficiation…
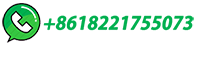
BENEFICIATION OF IRON ORE
Appropriate beneficiation process has to be advanced to reduce the waste generation in mines and for the sustainable growth of the iron ore industry some. Major reason for …
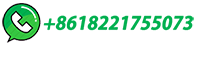
Beneficiation Plants and Pelletizing Plants for Utilizing …
Recently, the grade of iron ore deposits has deteriorated and further development of low grade deposits is desired. Presently, the most effective and often followed route taken to …
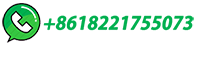
NMDC LIMITED
Kumaraswamy Iron Ore Mine (KIOM) at Donimalai Complex in Karnataka State. NMDC, India's single largest iron ore producer, is presently producing around ... SLDs, block flow diagram showing mass, water and metallurgical balance, process flow diagrams, control philosophy, functional description, test certificates, engineering, and installation ...
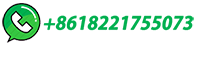
Low grade Iron Ore Beneficiation and the Process of Jigging
Due to this reason the availability of high grade iron ore is reducing and the supply of high grade iron ore to iron and steel plants is declining sharply. Hence, the scenario is steadily shifting towards the use of low grade iron ores and slimes which are stock piled in the mine's sites for years.
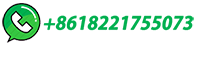
Exploring Steel Production: A Comprehensive Visual Process Chart
Steel making is a sophisticated process that turns iron ore into steel, involving methods like the Blast Furnace and Electric Arc Furnace to produce various grades of steel. The industry emphasizes sustainability by using additives and recycled materials while ensuring quality through rigorous testing for diverse applications.
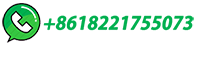
Extraction of Iron | Metallurgy | Blast Furnace and Reactions
The extraction of iron from its ore is a long and subdued process, that helps in separating the useful components from the waste materials such as slag. What happens in the Blast Furnace? The purpose of a Blast Furnace is to reduce the concentrated ore chemically to its liquid metal state. A blast furnace is a gigantic, steel stack lined with ...
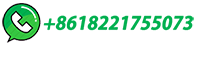
Iron Ore Processing: From Extraction to Manufacturing
Learn about the key stages in iron ore processing, including crushing, screening, and beneficiation techniques for optimal resource utilization.
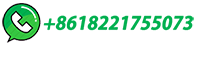
Iron processing | Definition, History, Steps, Uses, & Facts
Iron processing, use of a smelting process to turn the ore into a form from which products can be fashioned. Included in this article also is a discussion of the mining of iron and of its preparation for smelting. Iron (Fe) is a relatively dense metal with a silvery white appearance and distinctive
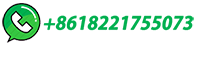
Beneficiation of Iron Ore
Crushing is done in the conventional manner in 2 or 3 stage systems to approximately all minus ¾ inch which is considered good feed for subsequent wet rod and ball mill grinding. The primary rod mill discharge at about minus 10- mesh is treated over wet magnetic cobbers where, on …
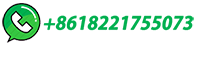
Process and Principle of Magnetic Separation of Iron Ore
According to the different types of iron minerals, the iron ore beneficiation process mainly includes magnetic separation, magnetized roasting-magnetic separation, flotation, and gravity separation.
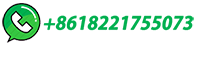
Iron Ore Processing, General | SpringerLink
Iron ore resource has its own peculiar mineral characteristics requiring suitable processing or beneficiation to produce quality raw material. Iron ore processing has become an integral part of ironmaking and steelmaking. The processing methods largely depend on the...
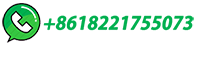
Iron ore beneficiation: an overview
This chapter briefly discusses the current scenario of the iron ore resources in India, iron ore mining methodology, beneficiation technique, and the current operating practices for achieving sustainable growth in the iron and steel industry.
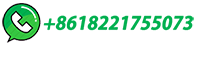
Understanding Pellets and Pellet Plant Operations – …
Iron ore pellets can be made from beneficiated or run of mine iron ore fines. Lean iron ores are normally upgraded to a higher iron ore content through beneficiation. This process generates iron ore filter cake which needs to be pelletized so that it can be used in an iron making process.
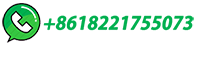
flow chart of iron ore beneficiation process
This page is about flow chart of iron ore beneficiation process, click here to get more infomation about flow chart of iron ore beneficiation process.
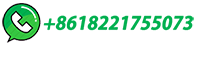
Iron ore beneficiation: an overview
Hence, the low-grade iron ore needs to be beneficiated to make the iron ore concentrate suitable for iron-making process. Thus, the main objective of …
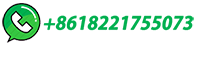
Iron Ore Processing Flowsheet
Typical Iron Ore Beneficiation Flow Sheet Multotec specialises in iron ore beneficiation equipment with over 50 years of global experience and leading technology. Our team of …
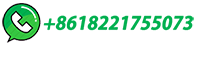
Lithium Processing Plant, Equipment
Lithium processing plant malinly includs crushing, grinding, gravity separation, flotation, magnetic separation or combined beneficiation process.
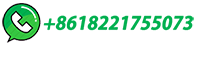
Introduction to Iron ore Pellets and Pelletizing processes
The various advantages of iron ore pellets are given below. Iron ore pellet is a kind of agglomerated fines which has better tumbling index when compared with the iron ore and it can be used as a substitute for the iron ore lumps both in the BF and for DRI production. Pellets have good reducibility since they have high porosity (25 % to 30 …
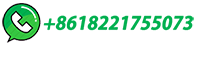
Steel Making Process – Complete Overview with …
In this article we will learn about what are the different methods of steel making process steps and the Flowchart to understand better. There are different processes involved according to the type and composition of …
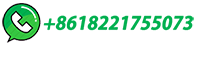
Iron Ore Pellets and Pelletization Process – IspatGuru
Iron Ore Pellets and Pelletization Process. Pelletizing of iron ore was started in the 1950s to facilitate the utilization of finely ground iron ore concentrates in steel production. For the pelletizing of iron ore there are two main types of processes namely, the straight travelling grate (STG) process and the grate kiln (GK) process.
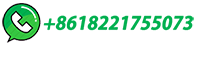