Copper Mining and Processing: Processing Copper Ores
Copper processing is a complicated process that begins with mining of the ore (less than 1% copper) and ends with sheets of 99.99% pure copper called cathodes, which will ultimately be made into products for everyday use.The most common types of ore, copper oxide and copper sulfide, undergo two different processes, hydrometallurgy and …
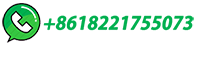
Nickel processing
Nickel processing - Extraction, Refining, Alloying: The extraction of nickel from ore follows much the same route as copper, and indeed, in a number of cases, similar processes and equipment are used. The major differences in equipment are the use of higher-temperature refractories and the increased cooling required to accommodate the higher operating …
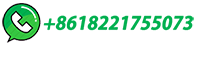
Iron Ore Processing, General
Making iron and steel from iron ore requires a long process of mining, crushing, separating, concentrating, mixing, agglomeration (sintering and …
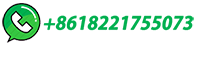
Why Is Iron Ore Valuable? Behind the Scenes of Production …
Learn about the extraction and production process of crude iron ore, along with which countries mine and store the most. See what experts say.
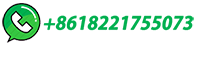
Taconite | Minnesota DNR
Information on mining taconite, a low grade iron ore, in Minnesota from the publication, Digging Into Minnesota's Minerals by the Minnesota Department of Natural Resources Division of Lands and Minerals.
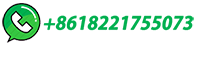
Ore
Ore is a deposit in Earth's crust of one or more valuable minerals. The most valuable ore deposits contain metals crucial to industry and trade, like copper, gold, and iron.
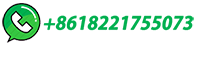
Fact Sheet: Final Amendments to Air Toxics Standards …
• EPA issued the initial air toxics standards for Taconite Iron Ore Processing on October 30, 2003. The rule applies to major source facilities engaged in separating and concentrating iron ore from taconite (a low-grade iron ore) to produce taconite pellets. These taconite pellets are then used as feed in blast furnaces to produce steel.
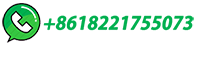
Dry beneficiation of iron ore
The ongoing exploitation of high-grade iron ore mines will force iron ore producers on other continents, too, to pay greater attention to their beneficiation technologies. This is forced by the fact that smelting of iron ore with lower iron content will entail ever higher costs and environmental emissions for blast furnaces.
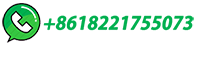
Iron Ore Characterization Techniques in Mineral Processing
While iron is a pivotal metal that is exploited commercially, its extraction from ores, subsequent processing and purification follows a series of steps, and material characterization in terms of physical, chemical and mineralogical features and behavior is imperative at each stage. Some characterization tests rely solely on physical …
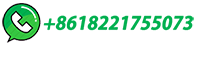
Life cycle assessment of iron ore mining and processing
The study used typical iron ore mining and processing operations in Pilbara, Western Australia, as a case study and covers the upstream part of the cradle-to-gate life cycle of steel: the mining and processing of iron ore.
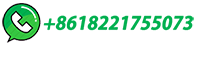
Ironmaking 101 – From Ore to Iron with Blast Furnaces
Iron is made by reacting iron ore (iron oxide and impurities), coke (a reductant) and limestone (CaCO 3) in a blast furnace. Iron ores with lower iron content …
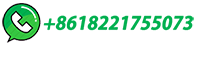
23.3: Metallurgy of Iron and Steel
Cast iron has already been mentioned above. This section deals with the types of iron and steel which are produced as a result of the steel-making process.
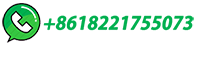
Steel Production
Even though equipment is improved and higher production rates can be achieved, the processes inside the blast furnace remain the same. The blast furnace uses coke, iron ore and limestone to produce pig iron. …
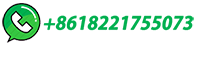
Chromium processing | Extraction, Uses & Applications
Chromium processing, preparation of the ore for use in various products. Chromium (Cr) is a brilliant, hard, refractory metal that melts at 1,857 °C (3,375 °F) and boils at 2,672 °C (4,842 °F). ... If pure chromium is desired, iron must be removed from the ore or from an intermediate ferrochromium product by hydrometallurgical techniques ...
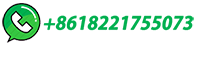
How iron is made
Iron ore is converted into various types of iron through several processes. The most common process is the use of a blast furnace to produce pig iron which is about 92-94% iron and 3-5% carbon with smaller amounts of other elements.
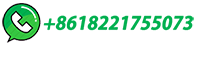
Extraction of Iron | Metallurgy | Blast Furnace and Reactions
Extraction of Iron. Extraction of iron from its ore is the third and the penultimate process in the Metallurgy. The extraction of metals and its isolation occurs over a few major steps:
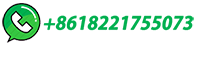
From Ore to Alloy: Navigating Ironmaking in Modern Steel …
At the heart of steel production lies the intricate process of ironmaking, where iron ore is transformed into molten iron and eventually alloyed to create various grades of steel. This article delves into the journey from ore to alloy, exploring the technologies, challenges, and innovations that shape modern ironmaking.
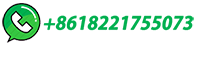
Iron Production
The production of iron from its ore involves an oxidation-reduction reaction carried out in a blast furnace. Iron ore is usually a mixture of iron and vast quantities of impurities such as sand and clay referred to as gangue. The iron found …
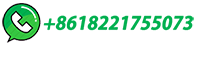
Iron Ore Pelletization: Part I. Fundamentals: Mineral Processing …
Iron ore concentration typically involves comminution, separation, and agglomeration. Comminution is the grinding of the ore to liberate the valuable iron-bearing minerals from gangue materials (of...
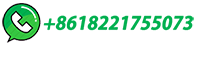
(PDF) A REVIEW OF IRONMAKING BY DIRECT REDUCTION
The proposed iron ore reduction process therefore would be a potential to reduce iron directly using biomass with high efficiency and real environmental benefits. View. Show abstract.
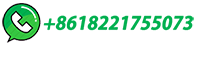
Iron processing
Iron processing - Smelting, Refining, Alloying: The primary objective of iron making is to release iron from chemical combination with oxygen, and, since the blast furnace is …
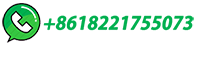
Manufacturing Process From Ore To Stainless Steel: A Step …
The quality and purity of the iron ore, as well as the precise blending of various alloying elements, directly impact the final characteristics of the stainless steel product. Now that we understand the significance of iron ore, let's explore the techniques used to convert iron into steel.
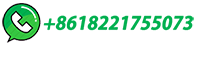
Iron Ore | HowStuffWorks
The most primitive facility used to smelt iron is a bloomery. There, a blacksmith burns charcoal with iron ore and a good supply of oxygen (provided by a bellows or blower). Charcoal is essentially pure carbon. The carbon combines with oxygen to create carbon dioxide and carbon monoxide (releasing lots of heat in the process). Carbon and carbon ...
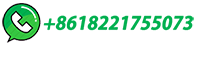
Iron (Fe) Ore | Minerals, Occurrence » Geology Science
Iron ore deposits Mining and Processing. Mining and processing of iron ore involve several stages, including exploration, development, extraction, beneficiation, and transportation. The overall process can vary depending on the type of iron ore deposit, its location, and the economics of extraction.
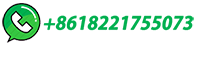
Iron Ore in India, Types, Uses, Distribution, World Map
India Ranks 4th in terms of iron ore production. Know more about Iron Ore, its Types, Distribution in India & world, Map in this article for the UPSC exam.
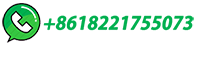
Iron ore | BHP
How is iron ore used? 98 per cent of all iron ore is converted into pig iron for steel making. It is then used in construction, transportation, energy infrastructure and even …
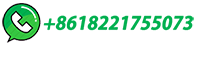
The six main steps of iron ore processing
Learn about the steps involved in iron ore processing, from crushing and grinding to separation. Contact Multotec experts for guidance on iron processing.
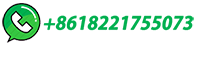
Iron Ore Processing: From Extraction to Manufacturing
Iron ore processing is a complex and vital process that transforms raw iron ore into usable steel. From exploration and extraction to grinding, beneficiation, and …
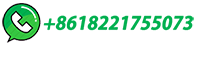
Sintering: A Step Between Mining Iron Ore and Steelmaking
Learn about the technology used in sintering, the process that converts fine-sized raw materials, including iron ore, limestone, etc. into product for blast furnace.
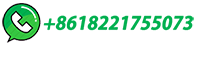
Introduction: Overview of the global iron ore industry
Iron ore is regarded as the second most important commodity behind oil. As an essential input for the production of crude steel, iron ore feeds the world's largest trillion-dollar-a-year metal market and is the backbone of global infrastructure.
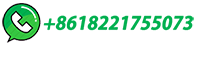