My Plant Planner
A free-to-use drag and drop configurator that helps you design more productive and efficient plants through real-time insights. Design and simulate a new crushing and screening plant in 3D or test how upgrading your current …
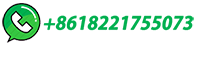
Crushing Plant Design and Layout Considerations
Hopper design. One of the first steps in the process is to select the equipment to load the primary hopper. The truck size and number of trucks or loaders needs to be determined to evaluate the hopper capacity. ... Impact …
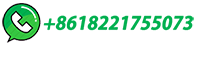
jaw crusher
Tag: jaw crusher ×. Advertisement ... The Computer-Aided Design ("CAD") files and all associated content posted to this website are created, uploaded, managed and owned by third-party users. Each CAD and any associated text, image or data is in no way sponsored by or affiliated with any company, organization or real-world item, product, or ...
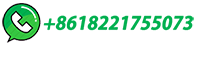
Jaw Crusher
The boulder hopper is often located near the primary crusher or the primary screening unit. It can be stationary or mobile, depending on the specific requirements of the operation. Some hoppers may have additional features such as hydraulic or mechanical systems to facilitate the controlled discharge of the boulders onto the next stage of ...
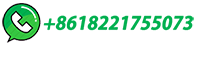
Mesin Stone Crusher
Bagian bagian mesin stone crusher ditandai pada gambar. Di sini saya akan memberi Anda pengantar terperinci tentang fungsi komponen-komponen ini. Hopper: Hopper memiliki dua karakteristik penyimpanan dan aliran. Menurut …
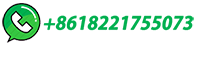
Scientific Methods to Design Crushing and Screening …
Hammermills and pure impact crushers have rotating impellers which lift the kinetic energy of the material to a level where, on sudden impingement against a stationary plate, breakage occurs. …
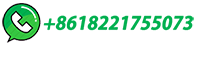
Mobile Feeder and Hopper
The Pilot Modular feed and hopper range consists of a complete range of ready to use semi-mobile, skid mounted grizzly and vibrating feed hoppers, designed for rapid installation and ideal for removing oversized rock and ore from feed material before the primary crushing process. Feeders & Hoppers:
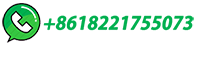
My Plant Planner
My Plant Planner is a free-to-use drag and drop plant simulator and configurator that helps you design more productive and efficient plants through real-time insights. ... Material is reduced in a jaw crusher. ... Hopper with a pebble feed curve with a MP800 cone crusher stand alone.
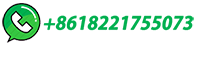
Tips for designing an efficient crushing and screening operation
FEEDER AND HOPPER DESIGN {{image2-a:r-w:200}}One of the first steps in the process is to select the equipment to load the primary hopper. The truck size and number of trucks or loaders needs to be determined to evaluate the hopper capacity. ... These are typically used for hard and medium abrasive stone. The primary impact crusher, also known ...
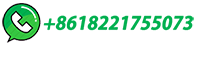
Mobile Crusher Plant in The Philippines
Jaw mobile crushing plant is also known as a coarse crushing tire mobile crushing station. Therefore, it is usually used for primary crushing equipment.The small mobile jaw crusher plant adopts an integrated operation method, which eliminates the installation of complex site infrastructure and auxiliary facilities. The overall structure of the mobile jaw crushing station is …
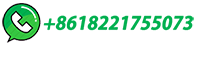
McLanahan | Vibrating Grizzly Feeders
Vibrating Grizzly Feeders reduce the amount of material going into the crusher by scalping out the product size ahead of the crusher. This reduces the size of the primary crusher required. ... water control and decorative stone applications; for sorting gravel in dredge applications for sized decorative landscaping applications; to scalp roots ...
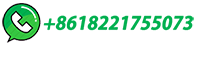
Portable crushing and screening solutions NW …
crusher only Cone crusher or screen feed Four-deck inclined screen Automation as standard (onboard or remote) Multiple end products Dumper hopper Primary station with bypass option and rock breaker Side conveyor Surge hopper Cone or screen feed Closed circuit can be opened to make sub-base material with cone crusher only Four-deck inclined screen
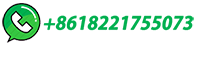
Hopper Design Principles
δ. φ. Jenike [1] found that the hopper angle required to allow flow along the walls depends on the friction between the powder and the walls, the friction between powder particles, and the geometry of the hopper.Design charts originally developed by Jenike [1] provide allowable hopper angles for mass flow, given values of the wall friction angle and the effective …
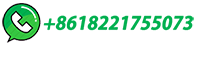
Tips for designing an efficient crushing and …
FEEDER AND HOPPER DESIGN {{image2-a:r-w:200}}One of the first steps in the process is to select the equipment to load the primary hopper. The truck size and number of trucks or loaders needs to be determined to …
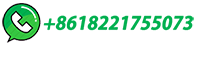
CS550 CONE CRUSHER
GENERAL DESIGN CRITERIA Crusher type Cone crusher, hydraulically adjusted Application Minerals processing Secondary Max. feed size 431 mm CSS range 22-72 mm ... Feed hopper Rubber / steel lined steel hopper Two inspection doors Capacity 3,433 kg (Bulk density 1,600 kg/m3) Feed level sensor UC400-30GM-IUR2-V15 Main shaft Supported at both ends
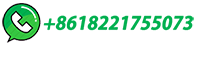
Hoppers & Feeders
Model 101-4620 Front End Loader Hopper for Large... Inventory Number: 101-4620. View Details . Model 108-2P Portable 2 Bin Blending Hopper. Inventory Number: R2520. View Details . Model 108-2P-RAP Portable 2 Bin RAP/Shingle Feeder. Inventory Number: 108-2RAP. View Details .
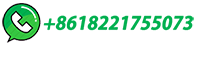
Environmental Guidelines for Stone Crushing Units
3.1 Transportation of raw material: Stones extracted from various sources are transported to stone-crushing units by means of trucks, trailers or automatic dumpers. 3.2 Primary crushing: Mined stones are fed directly into the primary crusher through stone feeders. The primary crusher breaks large stones and boulders into 100-140 mm size stones.
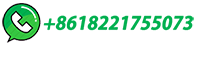
Mobile Hopper Feeders
The mobile hopper feeder allows operators to directly discharge from wheel loaders, grab cranes or excavators, and eliminates the double handling of material on site. ... Crushed stone is a versatile product that can be used in a wide range of applications from construction to road building and even agriculture. Processing this material may ...
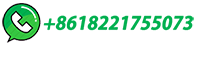
Stone Crushers: A Technical Review on Significant Part …
Granite stone crusher Design + Analysis The design of stone crusher for crushing particle size between 25–135 mm to about 24–20.2 mm was done.ANSYS software is used to find out high region stress area as major factor for safe working of proposed equipment 2020 Tauyanashechikuku et al.[24] Zimbabwe 13 Secondary crusher
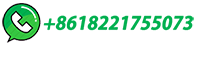
Crushed Stone Machines: The Key to High-Quality Building …
Here are the main parts of a typical crushed stone machine: Feeder. The feeder is responsible for feeding the material into the crushing chamber. It is designed to ensure that the material is evenly distributed and fed into the machine at a consistent rate. Hopper. The hopper is the container that holds the material being crushed.
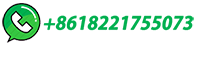
How the stone crusher hopper is designed?
Here are some general guidelines for designing a stone crusher hopper: 1.Size: The size of the hopper should be designed to hold enough material to ensure uninterrupted operation of the crusher. 2 ...
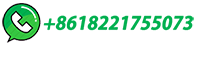
(PDF) Design of Impact Stone crusher machine
The main objective is to design impact stone crusher. Impact stone crusher involves the use of impact rather than pressure to crush materials. The material is held within a cage, with openings of the desired size at the bottom, end or at sides to allow crushed material to escape through them. Impact stone crusher is used with soft materials ...
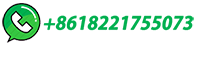
Minerals | Free Full-Text | Torque Analysis of a Gyratory Crusher …
Comminution by gyratory crusher is the first stage in the size reduction operation in mineral processing. In the copper industry, these machines are widely utilized, and their reliability has become a relevant aspect. To optimize the design and to improve the availability of gyratory crushers, it is necessary to calculate their power and torque accurately. The discrete …
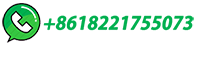
Stone Crusher Plant
CPC SURGE HOPPER For Stone Crusher Plant. - Surge Hopper Is Used to ensure Continous and even flow of material to the Secondary Crusher. - Our Surge Hopper Stone Box Design that Gives Very Long Life. - Our Surge Hopper Size Available Up-to 1000 CFT.
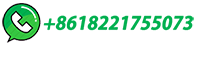
Crushing and Screening Handbook
the crusher and scalp out fi nes. Primary gyratory crushers – ideally suited to all high-capacity primary hard rock crushing applications. Jaw crushers – we have more installed jaw crushers than anyone in the world. The lead-ing choice due to their high reduction ratio and heavy duty design. Cone crushers – capacities available to suit all
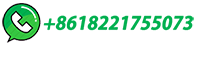
Jaw Crushers
The RockRanger has a wide discharge conveyor with good clearance under the crusher. Installation is rapid and easy to set up. The feed hopper is an externally reinforced heavy-duty steel plate hopper to stand up to the toughest of jobs. RockSledger / RockSizer heavy-duty jaw crusher; Heavy duty feeder with grizzly section
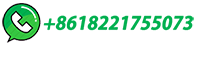
Selecting the right crusher for your operations
Components such as the crusher's engine, hopper and wear liners are just as important in ensuring the best fit and keeping maintenance to a minimum. ... The specialised design uses a shelf system with an abrasion-resistant wear bar that allows crushed material to build up and act as a wear liner. The result is zero maintenance, which ...
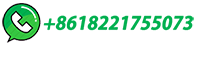
The Ultimate Guide to Stone Crusher Plant Design
Stone crusher plant design is a crucial factor in the efficient operation of the crushing process. The primary goal of plant design is to achieve the desired product size and capacity while balancing capital and operational …
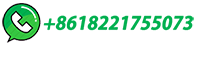
VYKIN 50-JC Mobile Mid-Sized Tracked Jaw Crusher
The VYKIN 50-JC is a compact mid-sized mobile tracked jaw crusher and can be used as an excellent concrete crusher. It is best for crushing all types of material, such as crushing concrete, asphalt, rock, stone, limestone, pavers and more. With a wide jaw inlet opening of 26.75" x 17" and a production capacity of up to 50 tons per hour, the VYKIN 50 crusher is one of our most …
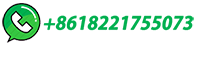
Industrial ACA crusher for stone wool and insulation
The ACA insulation crusher is a slow-turning machine that crushes standard stone wool bats as well as special hard-pressed plates or rolls. The crusher is a strong machine with a high torque. The crusher's noise level is 75 DB at a distance of 1 metre from a machine running on empty. A machine with only 15 RPM per minute produces a minimum of ...
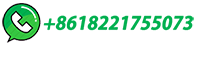