Chapter 2. Production and Processing of Aluminum
smelting process consumes, in addition to electrical energy, about 1.95 tonnes of alumina, 0.5 tonnes of anode coke, and small amounts of fluoride salts. 2 By G.W. Bulian. 11 The electrolysis cell, or "pot," shown schematically in Fig. 2.4, is shaped like a shallow rectangular basin. It consists of a steel shell with a lining of fireclay ...
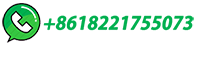
PT SMELTING Gresik Smelter & Refinery
The Mitsubishi Process for smelting stage and ISA Process for refinery were selected for the main processes that were used in Gresik Copper Smelter and Refinery, and also continuous casting system is used at anode casting stage. The Lurgi-Mitsubishi double contact and double absorption is installed to treat Smelter off-gas.
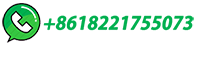
Copper Process Flowsheet Example
A simplified schematic drawing of copper flotation flowsheet. Run-of-mine open pit ore will be crushed in a gyratory crusher. The crushed ore will be processed by means of semi-autogenous and ball mill grinding followed by rougher flotation, regrind, cleaner flotation, and dewatering to produce copper concentrate. The concentrate will be trucked via the existing …
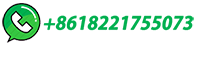
Copper Smelting
Copper Smelting. In subject area: Engineering. Copper smelting slag is a type of solid waste produced in the copper smelting process, which contains many silicon and aluminum …
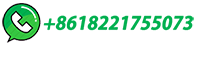
Copper Smelting
a new smelting facility or modernizing an existing operation. Recent developments in copper smelting are reviewed with particular reference to the newer smelting processes. Cri teria for process selection, the impact of oxygen enrichment, energy consumption, environmental controls, and investment costs are discussed. INTRODUCTION
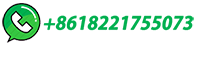
Ausmelt TSL Process
The Ausmelt TSL Process offers an integrated solution for copper smelting and converting or it can be coupled with existing site processes. The Ausmelt TSL Furnace can process copper concentrates with a wide range of copper contents and high impurities contents. For copper smelting the Ausmelt TSL Process has been installed in relatively small
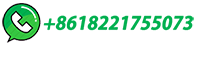
Copper processing
Copper processing - Roasting, Smelting, Converting: Once a concentrate has been produced containing copper and other metals of value (such as gold and silver), the next step is to remove impurity elements. In older processes the …
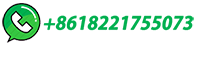
12.6 Primary Lead Smelting
12.6 Primary Lead Smelting 12.6.1 General15 Lead is found naturally as a sulfide ore containing small amounts of copper, iron, zinc, precious metals, and other trace elements. The lead in this ore, typically after being concentrated at or near the mine (see Section 12.18), is processed into metallurgical lead at 4 facilities in the U. S.
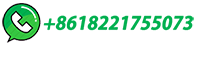
Copper Smelting
c smelting overall economics. In reviewing theprocesses suitable for a will ikely befor application where special metallurgical project, concentrate mineralogy, analysis, and the plant …
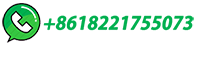
Thermodynamic Considerations of Copper Complex Resources Smelting Process
Large quantities of copper complex resources are produced globally and urgent to be cleanly processed. This article presents a thermodynamic analysis of mixed smelting process including low-grade polymetallic copper sulfide concentrates, high copper content sulfide concentrates, metallurgical by-products (copper removal slag from lead metallurgy), …
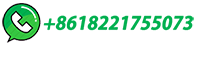
Copper Metallurgy | SpringerLink
Mitsubishi copper smelting, Vanyukov copper smelting, ISA process, Ausmelt process, and oxygen-rich bottom blowing smelting are also extensively used. Application of oxygen is a great advancement of matte-making smelting technology. The oxygen-enriched concentration in various matte-making smelting processes is from 40% to technical pure oxygen.
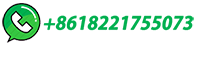
Energy Efficiency of the Outotec Ausmelt Process for …
consumptions for a range of different copper flowsheets. It also compares the energy efficiency of the Ausmelt Process against the Bottom Blown Smelting process, which has become widely adopted in China over the past 5–10 years. INTRODUCTION For more than a century, the non-ferrous metals processing sector has evolved continually to meet
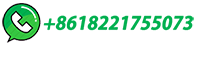
Copper Mining & Extraction Process Flow Chart
This flowchart made of machinery icons explains or expresses in simple but clear terms the step of the Copper Mining and Copper Extraction Process. Starting from either open-pit or underground mining and using a …
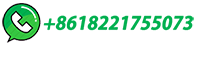
Taskinen, Pekka; Jokilaakso, Ari; Lindberg, Daniel; Xia, …
developers of a novel copper smelting technology faced, including a new approach of process chemistry, a specialised heat balance and its management, and the smelting vessel geometry. That is why the break-through experimental observations and modelling issues are introduced without a deeper analysis of their significance.
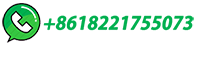
Copper Smelting and Refining Process | Pan …
The copper concentrates are fed through the flash smelting furnace with oxygen-enriched air. In the furnace, the concentrates are instantly oxidized, after which they melt and separate by their own reaction heat into copper matte …
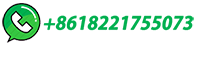
Flash Smelting of Copper | SpringerLink
Process Flow. In copper matte smelting, fine and pulverized burdens (concentrate, solvent, dust, etc.) are uniformly mixed, dried (moisture less than 0.3%), and then stored in the feed bin at the top of a furnace. Burdens and oxygen-enriched air (oxygen content: 80–90%) are sprayed uniformly through the central divergent nozzle into the ...
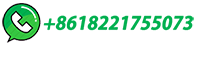
OVERVIEW OF PGM PROCESSING
sulphide ores containing PGMs, Nickel, Copper and other metals: • Platinum (Pt), Palladium (Pd), Rhodium (Rh) and Ruthenium (Ru) are the most prevalent of the six PGMs, ... Smelting Ore Anglo Converting Process (at Rustenburg) Our configuration differs from our competitors - we have a broad footprint across all 3
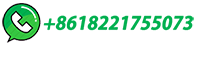
12.3 Primary Copper Smelting
In the smelting process, either hot calcine from the roaster or raw unroasted concentrate is melted with siliceous flux in a smelting furnace to produce copper matte. The required heat …
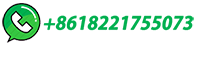
The Mitsubishi Process, Process Description
Return to Menu . PROCESS DESCRIPTION. The figure shown below schematically describes the Mitsubishi Process, illustrating its sequence of continuous and controlled smelting of copper concentrates, coal, and flux; the separation of copper matte and discard slag; the continuous conversion of copper matte to blister copper; and finally, the continuous delivery of blister …
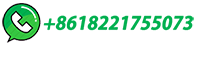
Comparison of environmental performance of modern copper smelting
The goal of the LCA study was to quantify and compare the environmental footprint of the seven different copper smelting process models. The scope, i.e., functional unit and system boundaries, were selected to accompany this goal. The functional unit of the study is 1 tonne of copper in the produced blister copper. Thus, all raw materials ...
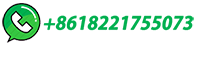
(PDF) minerals Sensors and Process Control in Copper
the copper smelting process are the combustion of fossil fuels (char, coal, fuel oil, natural gas, methane, etc.) and the characterization of molten p hases in the iron and steel industry.
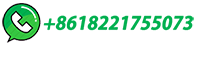
Modelling copper smelting – the flash smelting plant, process …
The effectivity of present copper smelting technologies have their roots in industrial and laboratory-scale experience accumulated over the past decades. Since early '60s, the tools for improving the processing conditions and smelting vessel design included scale modelling and manual computing of homogeneous multicomponent equilibria.
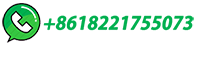
Copper Mining and Processing: Processing Copper …
This process uses a series of physical steps and high temperatures to extract and purify copper from copper sulfide ores, in four …
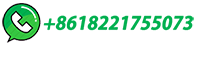
(PDF) Processing of Complex Materials in the Copper …
The ASARCO (American Smelting and Refining Company) smelter in El Paso, Texas accepts Cu concentrates with a maximum As content of 0.2% [61]. Meanwhile, the Lepanto roaster of the Lepanto ...
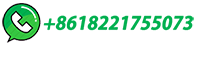
Copper Smelting Slideshow
The structure housing the furnace may be made of steel, but the furnace itself is made of refractory brick. Refractory bricks are made from clays with super high melting temperatures and insulating properties that make …
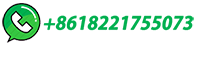
Centralized and hierarchical scheduling frameworks for copper smelting …
Optimal scheduling of copper smelting process is an ongoing challenge due to conflicting objectives of the various process units and the inter-dependencies that exist among these units. To design a scheduling framework, two potential alternatives – centralized and hierarchical approaches – can address those inter-dependencies in this ...
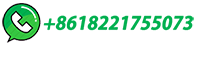
PT SMELTING Gresik Smelter & Refinery
Smelting use Mitsubishi technology in Copper smelting process and ISA technology in copper refining process. Mitsubishi process is a continuous process of smelting and converting, with a friendly environment and …
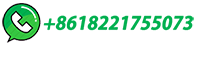
Flowsheet Options For Processing Copper Gold & Gold …
In the latter case, gold credits are obtained from smelting the copper concentrates and if gold reports to the flotation tailings, they may also require cyanidation which can prove problematic with cyanide soluble copper. ... Outokumpu process Copper and gold recovery Materials of construction Not used NO NSC process Copper and gold recovery ...
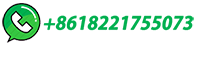
[PDF] Modelling copper smelting – the flash smelting plant, process …
The effectivity of present copper smelting technologies have their roots in industrial and laboratory-scale experience accumulated over the past decades. Since early '60s, the tools for improving the processing conditions and smelting vessel design included scale modelling and manual computing of homogeneous multicomponent equilibria. The scale …
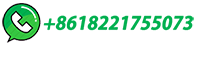
Copper Smelting Process
Modern copper smelters use processed copper ore fed into a flash furnace, typically fired by oxygen which produces blister copper, being further processed in a converter furnace. Molten copper is poured from here into rectangular …
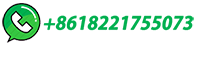