A REVIEW ON STUDY OF JAW CRUSHER
Toggle jaw crushers may feature hydraulic toggle adjusting mechanisms. It is shown below Figure 1 & Figure 2. Figure 1 Single Toggle Jaw crusher Figure 2 Double Toggle Jaw crusher II. FORMULATION OF PROBLEM The term size refers to the physical dimension or magnitude of an object and the reduction refers to
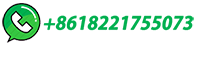
Computer aided parametricc design of tooth-shape in jaw crusher
Abstract: This paper proposed a new computer aided parametric design (CAPD) method by which a visual and three-dimensional entity model of crushing jaw plate and tooth-shape in a jaw crusher has been achieved based on a Pro/E's function of entity model creating. Relevant explanations have particularly been present for screening of specific parameters and …
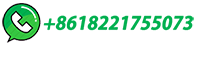
Failure rate analysis of Jaw Crusher: a case study | Sādhanā …
1.2 The jaw crusher. Crushing is the first stage of size reduction of mined rocks. Primary crushers are heavy-duty machines, used to reduce the run-of-mine (ROM) ore down to a size suitable for easy handling. A line diagram of a double toggle jaw crusher and its main components is shown in figure 2. The jaws are set at an angle to each other.
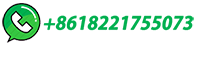
Jaw Crusher Working Principle – StudiousGuy
2. Both the structure and working of a jaw crusher are quite simple. 3. The product size is quite small and can range up to millimetres. 4. Repair and maintenance of a jaw crusher are convenient and easy. 5. The reliability of a …
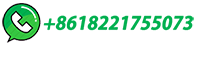
Below the surface: Setting up an underground primary jaw crusher
Jaw crushers are the most common solution in underground applications when the throughput is below 1000 tonnes per hour, depending somewhat on the scalping solutions. Above 1000 tph, primary gyratory crushers are an option. After the throughput reaches 2000 tph, jaw crushers are very rare, with the exception of a parallel plant layout.
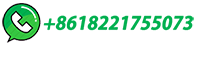
Jaw Crushers Manufacturer in India
This jaw motion also reduces the common scrubbing action found in single-toggle jaw crushers. These crushers are renowned for their outstanding strength, reliability for continuous operation, and cost-effective maintenance. The …
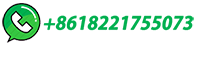
Jaw Crusher: Range, Working Principle, Application
A jaw or toggle crusher consists of a set of vertical jaws, one jaw being fixed and the other being moved back and forth relative to it by a cam or pitman mechanism. The jaws are farther apart at the top than at the bottom, forming a tapered chute so that the material is crushed progressively smaller and smaller as it travels downward until it ...
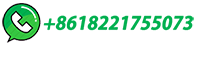
How Does a Jaw Crusher Work? A Simple Guide
Process Details; Primary Crushing: To reduce large and bulky materials to a manageable size. Jaw Crusher: 500 mm to 800 mm: ... A jaw crusher is a robust, essential and rugged crusher used primarily in mining …
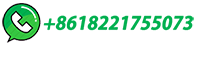
Type of crushers and their difference
The Dodge jaw crusher has a variable feed area and a fixed discharge area which leads to choking of the crusher and hence is used only for laboratory purposes and not for heavy-duty operations. The jaw crusher is usually made of cast steel because it is such a heavy-duty machine. Its outer frame is generally made of cast iron or steel.
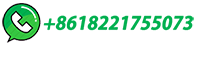
Failure rate analysis of Jaw Crusher: a case study
Primary crushers are heavy-duty machines, used to reduce the run-of-mine (ROM) ore down to a size suitable for easy handling. A line diagram of a double toggle jaw crusher and its main components is shown in figure 2. The jaws are set at an angle to each other. The moving jaw moves gradually forward towards the fixed jaw causing fragmentation of
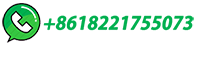
Below the surface: Setting up an underground …
Jaw crushers are the most common solution in underground applications when the throughput is below 1000 tonnes per hour, depending somewhat on the scalping solutions. Above 1000 tph, primary gyratory …
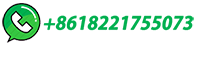
Jaw Crusher: What Is It & How Does It Work?
However, jaw crushers can also be found in other applications, such as recycling materials or separating minerals from ore. To learn about The Importance Of Performing Market Research, Click here! Types Of Jaw Crushers. There are two main types of jaw crushers: jaw crushers that use stationary jaw plates and jaw crushers that use movable jaw ...
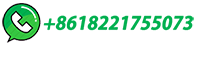
J-1175 Tracked Jaw Crusher | Rock Crushing Machine
Incorporating a ® Jaques JW42 jaw crusher and a heavy duty vibrating grizzly feeder, the Finlay® J-1175 gives optimum production in a range of applications. Its compact size, quick set up times, ease of transport and simple maintenance make the Finlay® J-1175 Tracked Jaw Crusher ideal for quarrying, mining, demolition and recycling ...
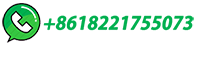
Blake Jaw Crusher
In the history of crushers, both chronologically, and by virtue of its standing in the field of heavy-duty crushing, the Blake jaw crusher stands first in the list. All of the large, heavy-duty primary crushers of the jaw type are built around the Blake principle which, for simplicity and brute strength, is unsurpassed by any mechanism thus far devised for rock and ore breaking.
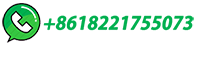
Understanding Jaw Crusher Parts and Their …
Introduction: Jaw crushers are powerful machines that are widely used in the mining, quarrying, and recycling industries. These machines are designed to crush large rocks and ores into smaller pieces for further …
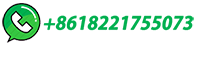
C Series jaw crushers
group, has installed over 10 000 jaw crushers since the 1920s. Today the C Series is indisputably the world's favourite jaw crusher. Where cost-efficient primary reduc-tion of hard, abrasive materials is concerned, C Series crushers represent the highest tech-nical and manufacturing knowledge. All C Series jaw crushers are based on a
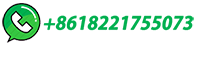
Detail Dimensional Figures Of 2012 Jaw Crusher
Construction aggregate - Wikipedia,, Typical Concrete Ringwall,jaw crusher dimensional design - academie-fribourg,17/03/2021· jaw crusher dimensional design Jaw crusher kinematics simulation and analysis Based on the overall structure of the jaw crusher design, using UG software to build three-dimensional jaw crusher models and their ...
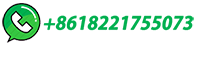
ROCK PROCESSING GUIDE 2013 Chapter C Jaw Crushers
Standard Jaw Plates Wide Teeth (WT)/Corrugated (C)/Coarse Corrugated (CC) PERFORMANCE DIMENSIONS (mm) Jmax, TF F L H TH W1 W2 W3 D 2 032 1 882 N.A. 2 986 N.A. 2 815 1 …
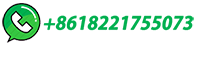
Jaw Crusher Explained
For example, a 32 x 54 sized jaw crusher will measure 32 inches from the movable to stationary jaw (when measured at the top i.e. the opening), and each jaw will have a 54-inch width. If a jaw crusher is rated by jaw plate size, a suitable rating maybe 600 x 400, which indicates a 600 mm by 400 mm jaw plate dimension.
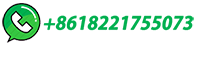
Assessing the energy efficiency of a jaw crusher
The analysis will concentrate on jaw crushers as typical and widely used comminution process equipment. A jaw crusher (see Fig. 2) is a comminution device designed to impart an impact on a rock particle placed between a fixed and a moving plate (jaw). The faces of the plates are made of hardened steel.
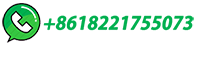
detail dimensional figures of 2013 jaw crusher
Analysis of The Single Toggle Jaw Crusher Kinematics. The concept of the single toggle jaw crusher is illustrated in Fig. 1. The swing jaw. drive mechanism, which includes the eccentric shaft, the frame, the swing jaw and the. toggle link, can be modelled as a planar four bar mechanism that is known as the. crank and rocker (Erdman and Sandor, 1991; Kimbrell, 1991).
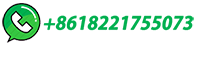
Jaw Crusher | SpringerLink
The moving jaw rotates around the eccentric axis as well as swings around the same center (Fig. 2).By removing the moving jaw suspension shaft and the front toggle plate of simple pendulum jaw crusher, and suspending the moving jaw on eccentric shaft to combine the connecting rod and the moving jaw into whole, a compound pendulum jaw crusher takes …
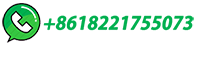
Jaw Crusher Technical Specification For Mining
This comprehensive technical guide covers the key details you need to know when evaluating jaw crusher models for your mining application. ... This details the maximum size of material …
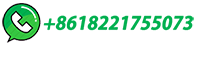
Jaw Crusher Diagram: Simplified Guide
The jaw crusher diagram is instrumental when it comes to adjustments for altering the granularity of the output. One critical metric is the Closed Side Setting (CSS)—the smallest gap between the jaws during the …
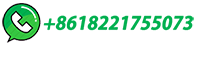
Laboratory Jaw Crusher – Labtech Group
Laboratory Jaw Crusher. Standards: ASTM C289. Laboratory jaw crushers allow you to process hard materials in extremely small sizes. In this sense, the laboratory type jaw crusher allows product output between 0 and 5 mm. You can also achieve higher product output by adjusting the grain size. The laboratory jaw crusher is built to create a high ...
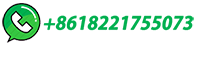
The Complete Guide to Primary Crushing, Secondary …
Jaw crushers are commonly used in the aggregates industry and are designed to handle large, blocky materials. Gyratory crushers are often used in primary crushing for high-capacity crushing plants and are well-suited for use in mines and quarries. Impact crushers are ideal for producing high-quality end products and are used for crushing soft ...
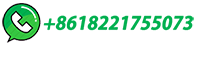
(PDF) DESIGN AND OPERATIONS CHALLENGES OF …
Abstract and Figures. A review on the design and operations challenges of a single toggle jaw crusher is presented. Strength and fracture toughness of the material to be crushed are intrinsic ...
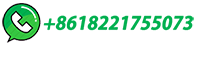
What Is a Jaw Crusher? Here's How It Works
Whether it's creating aggregates or mining, jaw crushers are your go-to. Jaw crushers were created in 1858 by Eli Whitney Blake. And since then, they've only become more widespread. This article will focus on what jaw crushers are and how they're used in the professional setting. What is a Jaw Crusher? A jaw crusher may sound like some ...
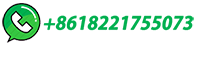
A fundamental model of an industrial-scale jaw crusher
To achieve a model using physical modelling techniques, the machine of interest, a jaw crusher in this case, has to be broken down into smaller subsystems and modelled separately, for example, breakage, dynamics or pressure, as seen in Fig. 1.For this research, the modelling approach is similar to the approach used by Evertsson (2000) when developing an …
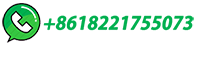
J-1160 Primary Mobile Jaw Crusher | Tracked Crusher | Finlay
The heartbeat of the machine is the renowned and aggressive 1000 x 600mm (40" x 24") jaw crusher with a proven pedigree in recycling, demolition and aggregate production applications. The hydrostatic drive gives the operator the flexibility of variable crushing speed and the ability to run the chamber in reverse in certain applications.
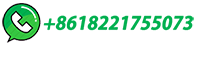