For dry and wet processing Low Intensity Magnetic …
Intensity Magnetic Separators) commonly use an alloy of neodymium, iron, and boron (NdFeB). Magnetic separation process Magnetic separation technology can roughly be divided into three classes of magnetic intensity i.e., low, medium, and high, all depending on the characteristics of the minerals subjected to magnetic processing:
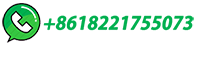
Improve Mineral Processing Efficiency By Magnetic Separator
Magnetic separator is the basic tool used by mineral processing plants to separate ferrous and non-ferrous metals from extracted ore, ensuring high-quality final products. Its works by attracting magnetic particles such as iron, steel and nickel, and then using powerful magnets or electromagnets to separate these particles from other materials.
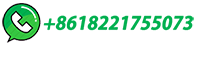
How Magnetic Separation Optimizes Sorting and …
Stage 1: A weak magnet and a high-belt speed – scalping process removes ferromagnetic material. Stage 2: A medium-strength magnet and/or slower belt speed – removes strongly …
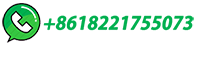
Mining separation and sorting equipment for processes in the mining
Mining separation - magnetic separation and sensor sorting solutions for improved throughput and recovery rates in ore sorting and mineral processing From traditional and trusted magnetic separation equipment, right through to innovative sensor sorting technologies, we help our customers achieve their goals with sustainable solutions.
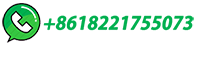
Magnetic Separator
Developments in the physical separation of iron ore. D. Xiong, ... R.J. Holmes, in Iron Ore, 2015 9.5.2 Utilization of subeconomic iron ores. As magnetic separators progress toward larger capacity, higher efficiency, and lower operating costs, some subeconomic iron ores have been utilized in recent years. For example, magnetite iron ore containing only about 4% Fe (beach …
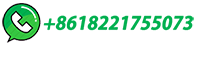
Magnetic separators
separators for iron ore processing Magnetic separation theory The magnetic separation process is complex in many respects due to varying magnetic susceptibility of the material …
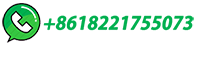
Iron Separator, Magnetic Stirrer, Magnetic Separator
This series of products has an ul- tra-high background magnetic field that cannot be achieved by ordinary electromagnetic equipment, and can effectively separate weakly magnetic substances in fine-grained minerals.It is suitable for beneficiation of rare met- als, non-ferrous metals and non-metal- lic ores, such as cobalt ore enrichment, impurity removal and purification of kaolin and …
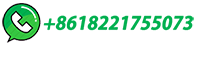
CHINIOT IRON ORE RESOURCE
Magnetite ore Hematite ore Copper ore 2017-2022 2021-2022 2017 2014-2017 2022 PMC driving Chiniot Project Phase I of Exploration NI 43 101 Report 149.8 Million Tons Iron Ore Resource Phase II of NI 43 101 Report Expected 250 Million Tons Iron Ore Resource Investor Interaction Transaction Structuring Agreeing terms and conditions with investors
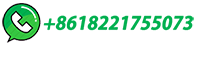
Magnetic separation in mineral processing
Iron ore – they are used to separate magnetic minerals from non-magnetic minerals by removing the magnetic fraction from the non-magnetic material, which results in a high-grade concentrate. Industrial minerals – magnetic separation is used to remove magnetic impurities from industrial minerals like feldspar, quartz, and mica.
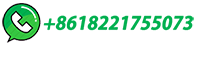
Magnetic Separators
Permanent Magnetic Separators . ... Mineral processing plants utilize a variety of material handling systems. The type of magnetic protection applied is normally matched to the system at the point that protection is required. ... Magnetite ore concentration; Removal of grinding iron from ball and rod mill pulps. Recovery of precipitated cobalt ...
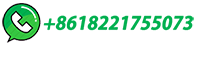
How Does A CIP Gold Processing Plant Work?
The main process of the CIP gold processing plant to extract gold from ore and convert it into pure metal can be divided into 6 steps: crushing, screening, grinding, classification, carbon slurry gold extraction and tailings treatment. ... 8 Types of Iron Ore Magnetic Separator. (04:03:13) Research on Vat Leaching Test of A Small Gold ...
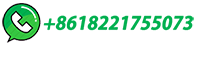
How Magnetic Separation Optimizes Sorting and …
They're extensively used in iron ore processing, but they also have a critical place in diamond processing plants and application in other ... At SRC, we also have a two -stage magnetic separator for our plant, which is similar to a three-stage separator. In the two-stage, you typically have the weaker magnet at the top to separ ate ...
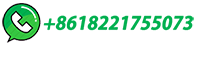
Intensity Magnetic Separator
As shown in Figure 13.2, minerals with ferromagnetic properties have high susceptibility at low applied field strengths and can therefore be concentrated in low intensity (<~0.3 T) magnetic separators. For low-intensity drum separators (Figure 13.11) used in the iron ore industry, the standard field, for a separator with ferrite-based magnets, is 0.12 T at a distance of 50 mm …
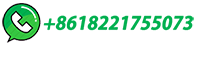
Magnetic Separator
Concentrators, which are used for the separation of magnetic ores from the accompanying mineral matter. These may operate with dry or wet feeds and an example of the latter is the Mastermag wet drum separator, the principle of operation of which is shown in Figure 1.43.An industrial machine is shown in operation in Figure 1.44.A slurry containing the magnetic …
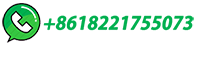
Magnetic Separation Plant Units
Industry leading partner for metals processing technologies. Explore Solutions ... Magnetic Separation Plant Units provide unrivaled selectivity, resulting in high recovery of …
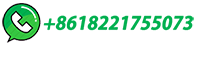
Magnetic separators
separators for iron ore processing Magnetic separation theory The magnetic separation process is complex in many respects due to varying magnetic susceptibility of the material and its particle size. The magnetic force on a specific particle depends upon these factors as well as other properties, such as magnetic flux and mag-netic field ...
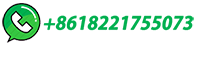
The six main steps of iron ore processing
3. Feeding the crusher (Reclaim) The surge pile allows a constant supply of material to be fed into the mill, which ensures consistent results and stability in the ore recovery process. 4. Grinding. The primary grinding mill grinds the …
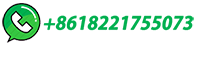
(PDF) An overview of the beneficiation of iron ores via …
separators for a low-grade oxidis ed iron ore at the Gong g mineral processing plant have demonstrated the high efficiency of SLon separators. These separators provided high-grade magnetic
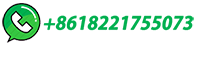
Beneficiation of Iron Ore
Beneficiation of Iron Ore and the treatment of magnetic iron taconites, stage grinding and wet magnetic separation is standard practice.This also applies to iron ores of the non-magnetic type which after a reducing roast are amenable to magnetic separation. All such plants are large tonnage operations treating up to 50,000 tons per day and ultimately requiring …
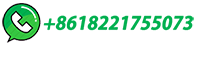
Beneficiation of Ultrafine Iron Ore Using Tribo …
separation is reserved for weakly magnetic iron bearing minerals, such as hematite, goethite, and limonite (Flippov et al. 2014). Two iron ore samples were tested in this research project: …
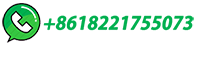
Recovery and separation of iron from iron ore using …
Finally, the magnetic component of the roasted ore can be recovered by magnetic separation after being liberated from gangue minerals. Many pilot-scale suspension magnetizing roasting and magnetic ...
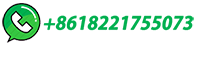
Magnetic Separation
The magnetic separation of solid waste is a method of separating ferromagnetic substances using the magnetic field generated by the magnetic separation equipment. Magnetic separation is primarily used in solid waste treatment systems to recover or enrich ferrous metals, or in certain processes to remove ferrous materials from solid waste.
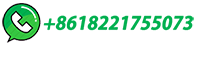
Iron Ore Magnetic Separator at Rs 98000
Star Trace Solutions Private Limited - Offering Iron Ore Magnetic Separator,Dry Magnetic Separator in Chennai, Tamil Nadu. Also get Magnetic Drum Separator price list from verified companies | ID: 3922821197. ... We offers …
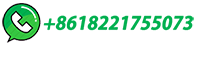
Wet High Intensity Magnetic Separator
Laboratory scale batch testing or continuous pilot plant duty Beneficiation of iron ore fines from 10 microns to 1mm Purification of silica / glass sands Removal of magnetic / contaminants …
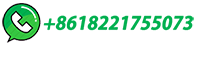
Wet High Intensity Magnetic Separator
Recovery of fine iron ore from tailing streams Separation of ilmenite from heavy mineral sand concentrates to reduce downstream processing Removal of magnetic contaminants from slurried materials eg cassiterite, kaolin, ... Laboratory scale batch testing or continuous pilot plant duty Beneficiation of iron ore fines from 10 microns to 1mm
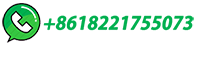
Iron ore tailings valorization through separate
Yu et al. studied the iron recycling from iron ore tailings by fluidized magnetization roasting followed by low-intensity magnetic separation. In iron ore processing plants, different tailing streams are usually transferred to the tailings thickener for partial dewatering and finally transferred to the tailings dam as a single stream.
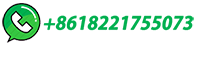
Iron Ore Processing: From Extraction to Manufacturing
b. Magnetic Separation: Magnetic separation utilizes the magnetic properties of iron ore minerals. High-intensity magnetic separators are used to separate the magnetic iron-bearing minerals from the non-magnetic gangue minerals. This technique is effective for removing strongly magnetic impurities from the ore.
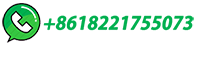
The Magnetic Separation Process for Ore Processing
Applications of Magnetic Separation: The versatility of magnetic separation extends its application across various industries: 1. Iron Ore Processing: Magnetic separation is widely used in iron ...
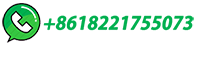
Magnetic Separation | SpringerLink
The attraction of magnetite to iron was discovered in China as early as 300 BC during the Warring States Period (476–221 BC). In the eleventh century, Shen Kuo (1031–1095) of the Northern Song Dynasty (1127–1279) of China, using the magnetism of a magnet (the presence of two magnetic poles), invented the nautical compass (one of the Four Great …
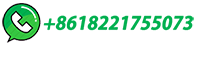