Flotation Plant
A flotation plant treats 500 t of solids per hour. The feed pulp, containing 40% solids by weight, is conditioned for 5 min with reagents before being pumped to flotation. …
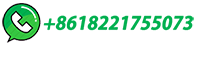
Flotation Plant Design and Production Planning …
The key to successful flotation plant design, production planning and mine/mill optimisation is a solid understanding of the resource to be processed. As advocated by the authors of this paper, the main components of geometallurgical modelling of an orebody and its associated flotation plant are:
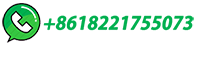
Flotation technique: Its mechanisms and design parameters
The overview of the flotation techniques and design parameters. • Details in design, analysis, optimization, operation, modelling is reported.
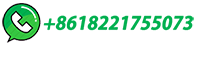
Flotation
Flotation is widely used to separate valuable minerals from the rock and fine coal particles from clay, silt, shale, and other ash-producing matter. It is usually preceded by crushing and finely grinding the ore to liberate valuable particles in a host rock, and may be followed by metallurgical processes.
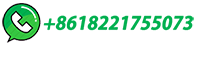
FLOTATION PLANT DESIGN AND PRODUCTION …
The key to successful flotation plant design, production planning and mine/ mill optimisation is a solid understanding of the resource to be processed. benchmarking. As advocated by the authors of this paper, the main components of geometallurgical modelling of an orebody and its associated flotation plant are:
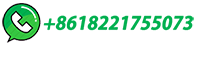
Flotation Cell Design: Application of Fundamental …
Flotation machines, in general, may be categorized into four different classes: (i) mechanical or con-ventional cells; (ii) energy-intensive pneumatic cells; (iii) column cells; …
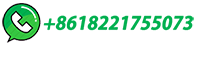
Bulk
This complete process plant is for recovering metal monometallic ore deposits. This applies, but is not limited to, the recovery by froth flotation of most base metals: Copper, Lead, Zinc, Cobalt, Nickel, Molybdenum, Pyrite, Pyrite-Gold, Silver-Sulphides. This process will also recover silver and/or gold associated with sulphide minerals. If your ore only …
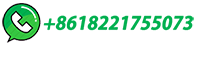
Flotation of Gold and Gold-Bearing Ores
Application of flotation on a reasonable scale within the gold-mining industry commenced in the early 1930s following the introduction of water-soluble flotation collectors (specifically xanthates and dithiophosphate collectors) that allowed differential flotation of sulfide minerals, followed by the installation of pyrite flotation plants on …
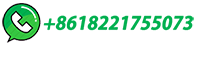
Flotation | Mineral Processing, Separation & Beneficiation
Introducing Flotation Plant Units. Through seamless integration of functional design and comprehensive scope, Flotation Plant Units deliver unparalleled metallurgical …
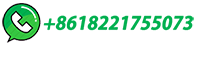
Flotation Plant Optimisation
Get Textbooks on Google Play. Rent and save from the world's largest eBookstore. Read, highlight, and take notes, across web, tablet, and phone.
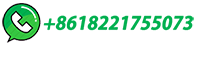
Froth Flotation
Froth Flotation Froth flotation is one of the most versatile and flexible of all mineral separation processes. Reasonable results are fairly easy to obtain but outstanding performance from a circuit requires constant attention
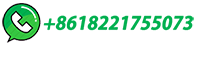
Flotation | SpringerLink
Flotation plant. Full size image. At the initial stage, skin flotation method and bulk-oil flotation method were used. The former method is to scatter ore powders on the flowing water surface in the flotation device, and hydrophobic minerals floated on the surface were recovered. The latter method is to mix a certain amount of mineral oil with ...
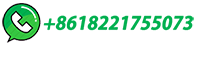
(PDF) The Same-level Arrangement Technology of Flotation Plant
Stepwise arrangement of flotation cells is the most common layout for flotation circuit in mineral processing industry. In such design, slurry flows from upstream to downstream by gravity and the ...
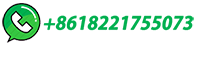
Efficient flotation recovery of lead and zinc from refractory …
The new process is reliable, economical, environmentally friendly and promising for recovery industry of the complex mixed sulfide-oxide lead-zinc ores. This study will provide some reference and guidance for researchers working on flotation indexes optimization, and for flotation plants facing the similar problems.
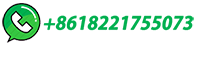
Flotation: The Past, Present and Future of Mineral Processing?
Dr. Kevin Brooks, global lead at Hatch, has pioneered the use of model predictive control (MPC) on flotation plants worldwide. Work with Anglo Platinum, FQML and …
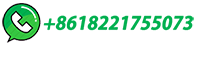
Flotation Plant Optimisation (first edition)
Why are your recoveries lower than expected? Is the concentrate grade out of spec? Can the metallurgical performance be improved? Have you got hard data to support your assumptions? This new Spectrum Series volume provides the reader with a logical series of steps to identify and solve problems within base metal sulfide flotation plants. Chapter …
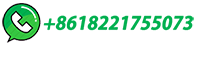
Flotation
Flotation Plant The actual process of concentrating the minerals by flotation is but one of a sequence of operations, a complete flotation plant comprising …
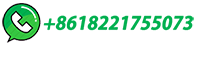
A review of froth flotation control
The last few decades have seen major advances in instrumentation and technology, and simplifications and modifications of new flotation plant designs.…
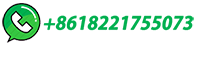
Modelling for froth flotation control: A review
Flotation is a conceptually simple operation; however, as a multiphase process with inherent instability, it exhibits complex dynamics. One of the most efficient ways to increase flotation performance is by implementing advanced controllers, such as Model Predictive Control (MPC).
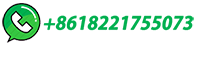
Large Scale Flotation Plants
Also amenable to upgrading by flotation are fine coals and other mineral commodities such as fluorspar, glass sand, barite, pyrite, talc, and iron oxides. Capital Cost of Flotation Plant. Table 36 gives the approximate factory cost of the machinery of a modern single-stage flotation plant, including the buildings and all equipment.
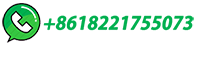
On lifetime costs of flotation operations
Overall economy of a flotation operation bears much more than investment costs. The lifetime operation and maintenance of a flotation machine may affe…
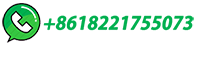
The future of flotation
Low grades, complex ores and rising energy costs have prompted the development of entirely new flotation vessels, improvements to existing technology, and new thinking about flotation flowsheets. The froth-free flotation vessel comes by way of Eriez Flotation Division, which patented it in 2002 and marketed it under the name …
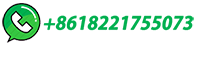
Copper Flotation
Flotation of Copper Ores. In most plants engaged in the flotation of ores containing copper-bearing sulphide minerals with or without pyrite, pine oil is employed as a frother with one of the xanthates or aerofloat reagents or a combination of two or more of them as the promoter.
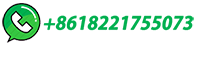
Flotation Plant Optimisation: A Metallurgical Guide to
Why are your recoveries lower than expected? Is the concentrate grade out ofspec? Can the metallurgical performance be improved? Have you got hard data tosupport your assumptions? This new Spectrum Series volume provides the readerwith a logical series of steps to identify and solve problems within base metalsulfide flotation plants. Chapter 1 …
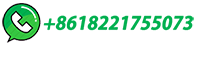
Purities prediction in a manufacturing froth flotation plant: …
We construct a stacked LSTM architecture to model an engineering froth flotation process with the goal of predicting the iron and silica purities based on several fast, easy measurements from a manufacturing froth flotation plant. This plant employs reverse cationic flotation to separate iron from undesired particles that are mainly silica.
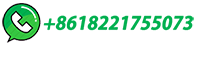
Flotation
Flotation plant operations. Flotation piloting. In order to satisfy rigorous due diligence requirements in the modern project development process, most flotation concentrator projects will need to undergo piloting to prove the process can run effectively in continuous/dynamic operation and meet the process design criteria (PDC) achieved on …
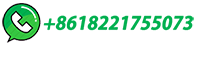
Flotation
Eriez Flotation Eriez Flotation provides novel and industry-changing flotation technologies that are changing the way mineral processing plants are designed. Our vision is to make mineral processing more efficient and less impactful on the environment.
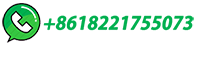
Flotation Plant Optimisation, second edition PDF
Prepared by a team of well-respected professionals, this publication provides the reader with practical advice for getting the best out of your flotation system. Chapter 1 outlines a methodical approach that can be used to determine where and how losses occur in your plant. The methodology utilised in the initial chapter is supported by more detailed …
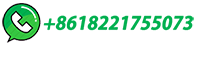
Flotation in Water Treatment | SpringerLink
Dissolved-air flotation has become accepted as an alternative to sedimentation, in particular in the Scandinavian countries and the United Kingdom, with more than 50 plants in operation or under construction. The largest dissolved-air flotation plant currently being constructed is the 315 Ml/day Frankley water treatment works in the UK.
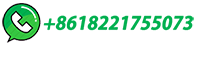
Flotation Cell Design: Application of Fundamental …
II/FLOTATION/Flotation Cell Design: Application of Fundamental Principles 1503 Figure 4 Typical flow patterns in a mechanical flotation cell (courtesy of Outokumpu Mintec Oy, Finland). sure through the hollow shaft to the impeller region.
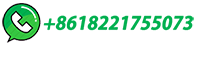