Optimisation of the swinging jaw design for a single toggle jaw crusher
This study reports on the design optimisation of the swinging jaw crusher plate. Jaw crusher machines are used in the mining and construction industry for crushing rocks and mineral ores to the appropriate sizes for direct application or further processing. During the crushing process, large and non-evenly distributed impact forces occur, …
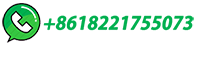
Scientific Methods to Design Crushing and Screening …
The commonly adopted practice of feeding the crusher directly from a vibrating screen discharge, while reducing plant construction costs, builds-in operating problems and …
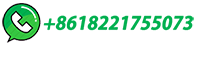
Roll Crusher
They therefore have the highest capital cost of all crushers for a given throughput and reduction ratio. The action of a roll crusher, compared to the other crushers, is amenable to a level of analysis. ... 6.2.3 Roll crusher circuit design. Roll crushers are generally not used as primary crushers for hard ores. Even for softer ores, such as ...
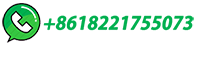
DESIGN AND ANALYSIS OF A HORIZONTAL SHAFT …
DESIGN AND ANALYSIS OF A HORIZONTAL SHAFT ... Jaw crusher and Impact crusher. Our objective is to design various components of an Impact crusher like drive mechanism, shaft, rotor, hammers, casing, and discharge mechanism which will be useful in minimizing weight, cost and maximizing the capacity and also do their analysis. Impact …
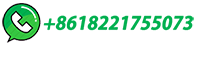
Design and Construction of Rock Crushing Machine …
The design and construction of a prototype rock crushing machine was performed this is with a view to ensuring that the designed crusher is capable of crushing rocks, lime stone and solid minerals for indigenous use. The research work was tailored mainly on the design and production of locally fabricated rock crushing machine for indigenous use.
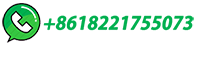
(PDF) Design and Construction of Rock Crushing Machine …
The design and construction of a prototype rock crushing machine was performed this is with a view to ensuring that the designed crusher is capable of crushing rocks, lime stone and solid minerals ...
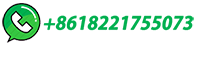
polysius® crusher | thyssenkrupp Polysius Crushing …
To do this, the entire upper part of the crusher had to be dismantled in advance, which was time-consuming and costly. The crusher segment design from thyssenkrupp Polysius now makes it easy to replace the crusher segments. The reconditioning of the worn crushing segments can then be carried out cost-effectively in the plant's own workshop.
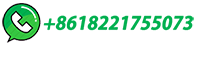
Svedensten
Parts of the rock material will thereby pass the crusher more then once. The two types of stages have some fundamental differences that affect the design of the crushing plant …
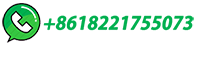
(PDF) Crushing and Screening Handbook
This is fundamental to ensure the set longer lifetime with a more regular parts wear, a better exploitation of the wear material weight, higher crusher eiciency and a better quality of …
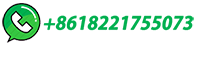
Cost Analysis for Crushing and Screening – Part I
The site consist of three crushing stages; one primary jaw crusher, one secondary S‐type cone crusher and two tertiary cone crushers, Vibrocone and H‐type.
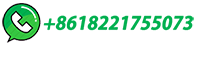
Primary Crusher Selection & Design
The rated capacity at 5" closed-side setting was 490 stph based on standard 100lbs/ft3 feed material. These crushers were fed a very fine ore over a 4″ grizzly which allowed the 1000 TPH the SAG mills needed. For crushing operations under 500 TPH, the design engineer will typically select a jaw crusher as they are of lower cost.
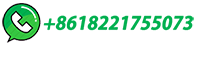
(PDF) Design and Fabrication of Pneumatic Can Crushing …
Works [9, 10] provide recommendations for the design and manufacture of crushers for aluminum cans, which cannot be directly applied to rock crushers. The work in [11] proposes the design of a ...
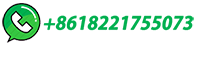
® C SeriesTM jaw crushers
It also reduces wear on the jaw dies, reducing operating costs. With a good grip, the jaw crusher can crush rocks efficiently through the entirety of the cavity, and the nip angle can be further improved with ... Convential jaw crusher design: C Series jaw crusher: 6 C Series C Series 7. C Series jaw crushers are
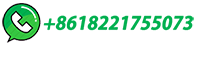
Mining crushers SuperiorTM MKIII Primary Gyratory
metallurgy and thousands of crusher installations around the world combine to create a Primary Gyratory crusher with the best performance, highest capacity and highest reliability. Outotec's line of Superior™ Primary Gyratory crushers are designed to meet the demand for high efficiency and high capacity mining installations.
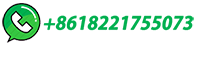
HP Series cone crushers – High performance …
® HP Series™ cone crushers The world's most popular modern cone crushers HP Series cone crushers bring together the optimal combination of crusher speed, throw, crushing forces and cavity design. As the name suggests, these proven and reliable universal crushers deliver High Performance in quarrying and mining applications.
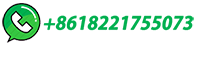
SUPERIOR® gyratory crushers
Advanced features has optimized the SUPERIOR design with one thing in mind — to be the most productive, reliable and efficient primary gyratory crushers on the market. ... maximizing availability, and minimizing maintenance and energy costs. Total crusher control Every aspect of the crusher is controlled by the TC System. The entire ...
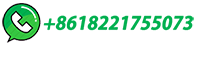
DESIGN AND ANALYSIS OF IMPACT CRUSHERS
mechanism used.Based on the mechanism used crushers are of three types namely Cone crusher,Jaw crusher and Impact crusher. Our objective is to design various components of an Impact crusher like drive mechanism, shaft, rotor,hammers, casing,feed and discharge mechanism which will be useful in minimizing weight, cost and maximizing …
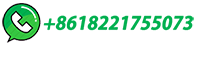
double-shaft hammer crushers
Fields of application and design characteristics In a single step, TITAN ® double-shaft hammer crushers crush run- of-mine (ROM) material to the required product size for either roller mills or ball mills.
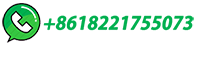
Comprehensive technical data of crushers for a wide …
the design of the crushing tools and the creation of a heavy- ... roller crushers are generally more compact in design. Additional advantages are achieved through …
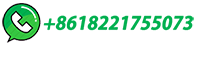
Crushers manufacturer in India
Puzzolana As a leading Crushers manufacturer in India, Puzzolana provides efficient crusher machines that compress and break the rocks, ensuring peak crushing efficiency at the lowest cost per ton.
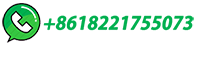
(PDF) Cone Crusher Performance
PDF | PhD Thesis Cone crushers are used by both the aggregate producing and the mining industry. ... the same time lowering the production costs. Prediction of crusher performance has been focused ...
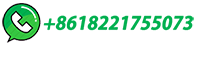
Cost Analysis for Crushing and Screening – Part II
The cost of crushing and screening is 2/3 and the raw material is 1/3. This study gave the result of 47.80 SEK/ton where raw material is 15.25 SEK/ton. 24 Cost Analysis for …
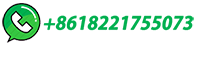
Estimate Jaw Crusher Capacity
The tables also show that for a comparable maximum size of feed and setting, a gyratory crusher has a much greater capacity than a jaw crusher. The gyratory crusher obtains this advantage only at the cost of greater power to drive the crusher. Capacities and Horsepower of Jaw Crusher (tons/hr)
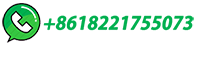
Small Scale Mechanized Stone Crusher, Mechanical Design
jaw crusher that employs the simple technology of a four bar mechanism, and design a small scale mechanized jaw crusher for crushing the stones into aggregates. This mechanism will help to evaluate its effectiveness in comparison with other different types of mechanisms in use especially the double toggle and the modified single toggle mechanism.
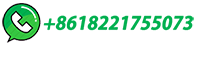
Primary Crusher Optimisation for Improved Comminution
Advantages of gyratory crushers: • Designed for direct dump from trucks up to 360 tons. • High capacity ratings. • Lowest maintenance per ton processed of any crusher design.
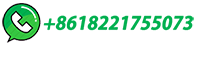
"Computer Aided Design of Jaw crusher"
crushers have the square opening design, and secondary jaw crushers have rectangular opening design. Jaw crushers are used as primary crushers in a mine or ore processing plant or the first step in the process of reducing rock. …
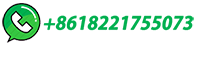
Primary Crusher Optimisation for Improved Comminution
The plant capacity determines the size of the crusher. As the term 'primary' implies, these crushers are used in the first stage on any size reduction cycle. The primary crusher is …
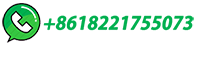
2. GYRATORY CRUSHERS
The parameters used in the basic design of a gyratory crusher are nip angle, feed rate, feed opening, closed-side setting, work index, and horsepower. The combination of the nip angle, feed opening, and closed-side setting determine the length of the crushing chamber and indirectly the length of the main shaft. ...
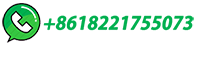
Construction Working and Maintenance of Crushers …
This information will help to achieve increased reliability at a decreased cost. Assemblage of this information will provide a single point of reference that might otherwise ... crusher at a setting which produces a satisfactory feed size for the secondary crusher and operating the secondary crusher (or the last stage crusher) in a closed circuit.
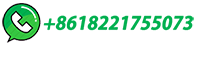
High pressure grinding rolls HRC 8 HRC
HRC 8 and HRC 800 design offers a unique and efficient crushing effect and can work in difficult applications with low crushability feed materials (very hard), moisture, clay and high fines content without creating any packing or crusher overload. Maintain high-quality with low cost per ton HRC 8 and HRC 800 produces the highest quality products
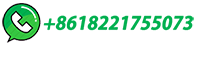