Cone crushers for even your toughest applications
Cone crushers for even your toughest applications. With over 100 years of experience and expertise in crushing, we can deliver the cone crusher solutions you need to increase …
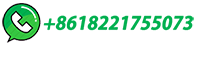
Cone crusher basics in 4 minutes
The CH cone crusher can be calibrated to achieve specific results, maximize productivity and minimize wear, but any calculation will be undermined without a solid understanding of what is going in to the crusher. Sampling is a vital part of the crushing process, to ensure that you know the size distribution of the feed. ...
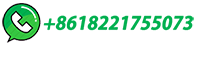
Five Types of Crusher in the Mineral Processing
According to the different crushing principle and particle size of size, the types of crusher is divided into many kinds and a variety of new types of crusher have been widely developed, mainly ...
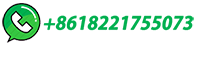
Cone Crusher
The cone crusher is a modified gyratory crusher, and accordingly many of the same terms including gape, set, and throw, apply. The essential difference is that the shorter spindle …
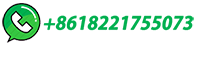
Cone crushers
Engineered for all rock types, ® GP Series™ cone crushers can be utilized as secondary, tertiary, and quaternary crushers in aggregates production plants and in …
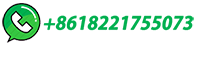
Modular Crushing & Screening System
The cone crusher module station: Uses for medium and fine crushing of minerals and rocks with medium hardness and above. The impact crusher module station : Uses for medium crushing of minerals and rocks below …
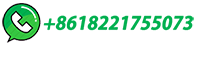
Gyratory Crusher vs. Cone Crusher: What's the Difference?
In the mining industry, crushing equipment is used to break down large stones and rocks into smaller pieces. This is crucial for ensuring that minerals can be extracted from the materials that are mined. Two types of crushing equipment that are commonly used are gyratory crushers and cone crushers.
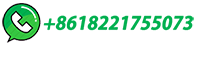
Raptor® Cone Crushers for Mining and Aggregate
Versatile and highly portable, the Raptor R450 can accept primary-crushed ore from a jaw crusher with greater flexibility (up to 25% larger material) because of its 1.3m (52-inch …
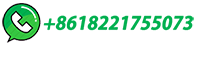
Fives | Mineral crushing with FCB VIF™ & FCB Rhodax® 4D
Fives develops heavy-duty crushing chambers for the mineral industry, from primary crushers to fine grinding equipment such as the FCB VIF™ or FCB Rhodax®.
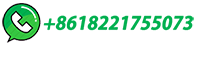
Cone Crushers Manufacturer
JXSC Cone crusher is suitable for various stone and ore crushing plants, high crushing efficiency, automatic hydraulic control, and good grain shape of the finished product.
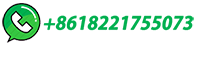
Home | Minerals Processing Systems
Minerals Processing Systems provides a complete range of crushing and screening process equipment to customers around the world.
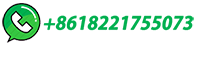
Prediction of power consumption and product size in cone …
A review of modeling and control strategies for cone crushers in the mineral processing and quarrying industries. ... In another example, Bearman et al. (1991) conducted a comprehensive study of a cone crusher, including power consumption, discharge product size distribution and wear of the concave and mantle of the device, …
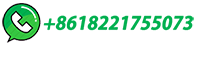
A review of modeling and control strategies for cone …
Cone crushers are used in the mineral, mining, and aggregate industry for fragmentation and production of rock materials. Cone crusher control systems are widely used for machine protection, wear … Expand
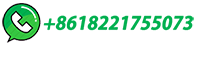
CEDARAPIDS Crusher Aggregate Equipment For Sale
Designed with the user in mind, Cedarapids jaw crushers feature the brand's renowned jaw chamber for optimal performance and reliability. Some jaw crusher models, such as the portable CRJ3042, combine the jaw crusher with a high stroke, vibration grizzly feeder. Cedarapids cone crushers have hydraulic iron relief, automation, and telematic ...
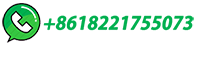
Cone crusher basics in 4 minutes
Cone crusher basics in 4 minutes. This is the starting point for understanding how cone crushers work – and how they can make your mine or quarry more productive.
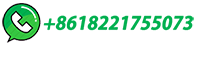
Jaw Crusher
The jaw crusher is the most widely used and is fully suitable for various sand and gravel, aggregate processing, mineral crushing plants, etc. The wide adjustment range of the discharge port increases the flexibility of the equipment.
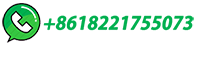
Control oriented modeling of flow and size distribution in cone
Cone crushers are a vital stage in the comminution chain in many mineral processing plants, and are used as a secondary, tertiary, ... A dynamic cone crusher model that describes the output size distribution (size reduction), and the …
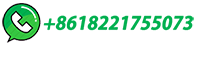
Affordable Cone Crusher for Heavy-duty Applications | E & MJ
Sepro Mineral Systems' new Blackhawk 100 cone crusher for heavy-duty crushing applications incorporates advanced technology with affordability to provide a reliable and simple-to-operate crushing solution, offering a combination of speed and 100 kW of power for fine crushing capability and high capacity in a compact design. The Blackhawk 100 …
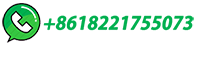
Cone Crusher Wear Parts & Replacement
A cone crusher is a crushing equipment commonly used in the mining and aggregate industries. It's known for its efficiency in crushing hard and abrasive materials.
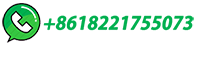
TECHNICAL NOTES 5 CRUSHERS
The chief difference between cone and gyratory or jaw crushers is the nearly parallel arrangement of the mantle and the cone at the discharge end in the cone crusher. This is illustrated in Figure 5.2. Reduction ratios in the following ranges are common for cone crushers: 6:1 - 8:1 for secondaries 4:1 - 6:1 for tertiary and quaternary crushing.
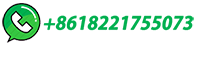
(PDF) Cone Crusher Performance
Applied to Cone Crushing", Minerals Engineering, V ol. 10, 199-214, February. 1997. ... cone crusher already at the design stage would enable improvements without full-scale testing.
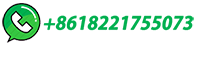
Evaluation of size reduction process for rock aggregates in cone crusher
The size reduction process of rocks in cone crushers is one of the most important issues, particularly for the secondary and tertiary stages of crushing operations. In this study, 17 different rock types were considered for the evaluation of their size reduction variations that occurred in a laboratory-scale cone crusher. Based on several …
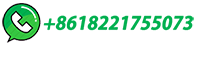
A review of modeling and control strategies for cone …
We aim to provide a starting point for people who wish to investigate the modeling and control strategies of cone crushers. This review contains a compilation of …
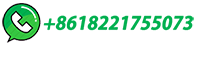
Selecting the right crusher for your operations
Like the jaw crusher, the cone crusher provides a relatively low cost crushing solution, but there are application drawbacks that may make another crushing solution more appealing. First, cone crushers cannot accept all material sizes. Any material fed to the crusher must be pre-sized for that particular crusher (usually 200mm or less).
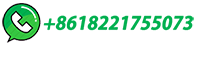
Cone Crushers For Sale
Aimix Group has many types of cone crushers for sale, you can choose according to the required production capacity and output size.
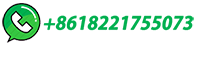
Comprehensive technical data of crushers for a wide …
powerful drive. Due to the robust design of the roller crushers, depending on the type of minerals, they can process compres-sive strengths of up to 300 MPa. The DRC series is …
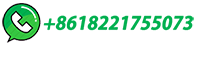
Crusher Reduction Ratio
Crusher Reduction Ratio. I have mentioned the fact that, as the % of voids in the crushing chamber decreases, the production of fines by attrition increases.
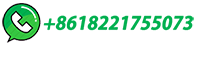
AMIT 135: Lesson 5 Crushing – Mining Mill Operator Training
Gyradisk Cone Crusher. For finer size products (e.g., -6 mm), a special cone crusher known as the Gyradisc is commonly used. Operation is similar to the Standard Cone Head; however, breakage is mostly by attrition rather than impact. Reduction ratio is around 8:1. Feed size is limited to less than 50 mm with a nip angle between 25 ° and 30 °.
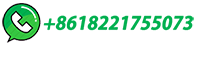
Breakage process of mineral processing comminution …
However, in mineral processing, it is not common to reach this low level of rate. For instance, Evertsson introduced cone crushers as a compressing crusher in which the rock is broken by squeezing between two surfaces [33]. He calculated the working velocity in a specific type of cone crusher at choke-level from 0.5 to 1 m/s.
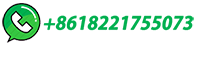
Downstream Crushing Options for Secondary, Tertiary …
Short-head Cone Crushers work exactly like Standard Cone Crushers, but they feature a smaller crushing cavity, making them ideal for finer crushing applications. The closed-side setting on a Short-head Cone Crusher can be adjusted tighter than a standard cone to improve final product size and shape.
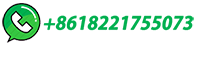