Use of Bentonite and Organic Binders in the Briquetting of …
The reducing gas hydrogen, the inert gas argon, and the inert gas nitrogen were purchased from Nippon Gases. Iron ore pellets, which were delivered by voestalpine Stahl , were used as a reference in the reduction tests. These iron ore pellets had a mean iron content of 66.1 wt%, with the iron being in the form of Fe 2 O 3. The grain size of ...
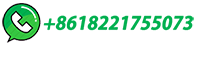
Microstructure of bentonite in iron ore green pellets
Sodium-activated calcium bentonite is used as a binder in iron ore pellets and is known to increase strength of both wet and dry iron ore green pellets. In this article, the microstructure of bentonite in magnetite pellets is revealed for the first …
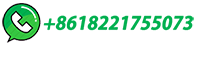
Effects of bentonite fiber formation in iron ore pelletization
Iron ore pelletization plants in the United States used approximately 612,000 metric tons of bentonite as a binder to produce iron ore concentrate pellets in 2000 (Virta, 2001). It is a major cost item, with individual plants spending US$3–5 million annually for bentonite.
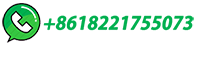
Synthesis, characterization and properties of organically
To improve the ballability of iron concentrates and enhance the performance of green balls and dry pellets in the production of iron ore pelletizing, the bentonite was usually used as a binder in the pelletizing process [].Bentonite, a very important nonmetallic mineral, is mainly composed of montmorillonite [2, 3], which is an aqueous aluminosilicate with the …
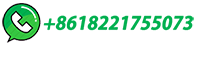
Bentonite for iron-ore pelletizing | Bentonite
While interacting with the water, bentonite clay expands and becomes sticky. This property allows to effectively use it as a binder for the production of pellets from iron ore concentrate (wet, crushed iron ore that has been beneficiated).. Pellets are used in blast-furnace redistribution and electrometallurgical production.
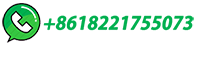
Microstructure of Bentonite in Iron Ore Green Pellets
The microstructure of bentonite in wet and dry iron ore pellets, as well as in distilled water, was imaged by various imaging techniques (e.g., imaging at low voltage with monochromatic and ...
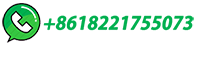
Study on Mechanical Properties and Reduction Behavior of
Jayson Ripke and Komar Kawatra investigated bentonite bonds with iron ore agglomeration by physical and chemical binding mechanisms to improve the compressive strength and reducibility of the pellets . Rusila Zamani Abd Rashid et al. investigated the reduction behavior of composite pellets by using an electric tube furnace . A novel ...
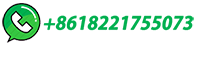
How to Dry, Grind and Granulate Your Bentonite Clay?
Bentonite clay is a high-quality foundry sand binder. Bentonite binders are cost-effective, environmental solutions since the majority of the sand and binder can be reused in a cyclical system. Bentonite clay in iron ore pelletizing Bentonite clay is used as a binder for the formation of iron ore pellets.
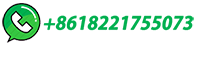
Microstructure of Bentonite in Iron Ore Green Pellets
The microstructure of bentonite in wet and dry iron ore pellets, as well as in distilled water, was imaged by various imaging techniques (e.g., imaging at low voltage with …
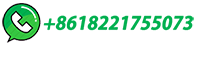
Effects of bentonite fiber formation in iron ore pelletization
In the production of iron ore concentrate pellets, binders are required to improve pellet green strength. The most popular binder for this purpose is bentonite clay, which is …
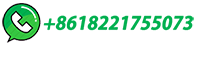
Iron Ore Pelletization
GIMBOND ® is natural high swelling sodium based bentonite of exceptional purity. It is mined and processed in North West part of India. GIMBOND ® is sodium activated bentonite designed to meet the requirements of pelletization industries. GIMBOND ® is used as green and dry ore binder for all kind of pellets. GIMBOND ® offers superior performance as per ASTM …
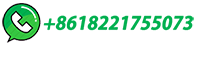
Bentonite | Imerys
Bentonite binders are cost-effective, environmental solutions since the majority of the sand and binder can be reused in a cyclical system. In iron ore pelletizing Imerys bentonite is used as a binder for the formation of iron ore pellets. Pellets are balls produced from iron ore or concentrates and are used as feed material for iron making.
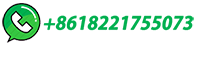
Iron Ore Pelletization
Iron ore must go through a lengthy pre-processing stage before it can be pelletized – a series of steps that work to beneficiate and concentrate low-grade ores. ... Binder selection can vary from process to process depending on the unique goals of the project at hand, but bentonite clay is a common choice for iron ore. Various additives may ...
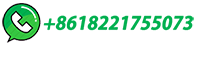
Binding mechanisms in wet iron ore green pellets with a bentonite …
The beneficial influence of viscous binders in iron ore balling is well known from everyday practical operations. The large variety of binders studied in the iron ore industry was recently reviewed by Eisele and Kawatra [9]. The most common binder is bentonite, of which additions of 0.5–0.7% are usually made.
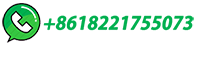
Stabilization of iron ore tailings with cement and …
producer of raw (un-smelted) iron products in Iran. A comprehensive series of compaction and uniaxial compression tests was performed on mixtures of cement/bentonite and tailings. Test results reveal that the introduction of cement/bentonite to iron ore tailings requires higher water content for optimum compaction and results in lower dry density.
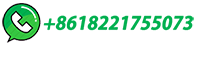
Partial Replacement of Bentonite by Fly-Ash as a Binder in
For pellet preparation, required quantities of iron ore fines were mixed with flux along with bentonite and fly-ash in the appropriate proportions in a laboratory scale high intensity Eirich mixer to obtain a specific fired pellet chemistry [].Therefore, despite the difference in the Fe content of bentonite and fly-ash, the fired pellet chemistries for the two experimental …
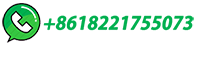
Iron Ore Pellets
Iron ore pellets, like concentrates, are raw materials for the manufacture of iron, which is pulverized and ground into pellets ranging from 0 to 100 microns for supply to industry as pellet feed. ... the process and time of the reaction of bentonite with iron oxide to form slag takes place (the bentonite content in the pellet is about 0.5-1%). ...
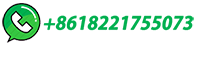
Effects of bentonite fiber formation in iron ore pelletization
In the production of iron ore concentrate pellets, binders are required to improve pellet green strength.The most popular binder for this purpose is bentonite clay, which is added at a rate of approximately 0.5–1.0% by weight of moist concentrate. Bentonite is a significant cost item in iron ore pelletization, and also contributes undesirable amounts of silica to the finished …
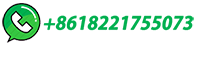
Process Development Essential to Bentonite …
Binder in Iron Ore Pelletizing. Bentonite is the most commonly employed binder in the iron ore pelletizing, or "balling" process used in the production of steel. The importance of iron ore pelletizing has been on the rise in recent years as high …
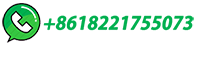
ALTERNATIVE BINDERS TO BENTONITE FOR IRON ORE …
KEYWORDS: iron ore pelletizing, bentonite & organic binder, boron compounds, colemanite, physical and mechanical properties.. HOLOS, Ano 30, Vol. 3 - Edição Especial - XXV ENTMME / VII MSHNT 94 SIVRIKAYA & AROL (2014) 1 INTRODUCTION The main raw material for iron-steel industry is natural iron oxide ores. Natural iron oxide ores can be ...
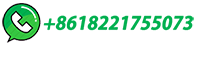
IRON ORE PELLETIZING BENTONITE – Bentonite
Bentonite is commonly used in pelletting of iron ore. Bentonite plays an important role in using degradable iron ores with low grades upon pelleting. While activated calcium bentonites swell about 5-6 times of their volume, Sodium bentonites can swell up to 25-30 times. Swelling is directly influenced by the Enslin value required for the pellet.
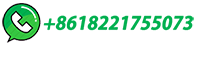
Bentonite | Properties, Formation, Uses » Geology Science
Bentonite is an important material in various fields due to its unique properties and characteristics. Here are some of the key uses and benefits of bentonite: 1. Drilling industry: Bentonite is widely used as a drilling mud in the oil and gas industry. It helps to lubricate and cool the drill bit, as well as remove debris from the borehol…
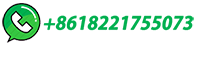
ALTERNATIVE BINDERS TO BENTONITE FOR IRON ORE …
The use of conventional bentonite binder is favorable in terms of mechanical and metallurgical pellet properties, however, because of its acid constituents bentonite is considered as impurity especially for iron ores with high acidic content. Therefore, alternative binders to bentonite have been tested. Organic binders are the most studied binders and they yield …
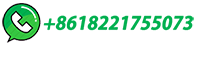
Effect of binders on reduction degree of iron ore pellets
Bentonite is the most preferred silicate-based binder in iron ore pelletizing. However, it is considered an impurity due to its high SiO 2 and Al 2 O 3 content. The iron …
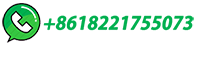
Decreasing bentonite dosage during iron ore pelletising
Results show that it is influenced by the properties of bentonite, water and iron ore concentrate. The dosage of bentonite can be halved by exchanging cations in the …
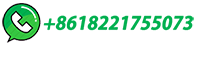
(PDF) Hyperactivation of Bentonite in Pelletizing Process
The replacement of bentonite as the standard iron ore binder is an important factor in the future of iron processing. Bentonite adds unwanted silica to the final concentrated iron ore product.
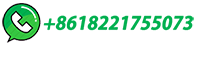
Iron Applications
The most common agglomeration technology in the iron ore industry is pelletization with bentonite being the most often used binder. The addition of very small amounts of Alcotac ® CS allows to reduce the dosage of bentonite by about 50% or more - without compromising on pellet quality. Depending on the quality of the bentonite and ore, sulfur ...
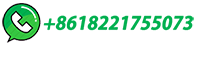
Can fly-ash extend bentonite binder for iron ore …
⋅ Iron ore pelletization with bentonite binder works by a different binding mechanism than with FBB. Bentonite is a physical binder, while FBB is a pozzolanic binder. ⋅ Iron ore concentrate pellets produced with up to 50% of the bentonite replaced by fly-ash exceeded minimum industrial specifications for dry compressive strength. However ...
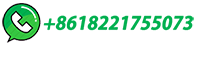
Decreasing bentonite dosage during iron ore pelletising
Factors affecting the bonding efficiency of bentonite during pelletising were investigated. Results show that it is influenced by the properties of bentonite, water and iron ore concentrate. The dosage of bentonite can be halved by exchanging cations in the interlayer to activate bentonite, removing bivalent cations to soften the water and milling the mixture to advance the contact …
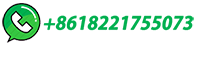
The bonding mechanism and effects of sodium
Bentonite is the most commonly used binder for iron ore pellets. However, due to its high alumina and silica content, the slag volume and energy consumption are increased.
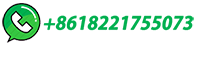