Enhanced Iron Recovery from Ultrafine Iron Ore Tailing
The present study has been made to overcome the drawbacks of processing iron ore tailings with containing ultrafine and low Fe. This study has been carried out using gravity and magnetic separation to recover the iron value. The accumulation of waste in the slime is associated with low-grade iron ore consisting of …
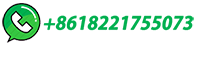
SLon Magnetic Separators Applied in Various Industrial Iron Ore …
SLon magnetic separators utilise the combined force fields of magnetism, pulsating fluid and gravity to continuously beneficiate fine weakly magnetic minerals. They possess the advantages of high efficiency, low operative cost and high reliability. Until now there were about 600 SLon magnetic separators widely applied in processing oxidised iron ores, …
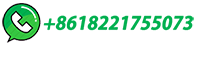
Developing high gradient magnetic separators for greener …
As the primary beneficiation method for iron ore, magnetic separation improves ore grade, reduces silica and harmful impurity content, and facilitates the smelting process [28], [32], [33]. Utilizing magnetic separation is an important step towards achieving green and low-carbon steel production.
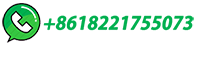
Increasing efficiency of iron ore magnetic separation by …
The method of identifying processes of separation, delivery and dehydration of materials directly inside the magnetic separator under various operating modes will be developed …
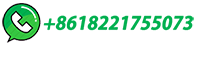
Magnetic Separator
The Franz is also used to characterize materials, separating fractions that can then be identified. These data can form the basis of predicting separation in full size magnetic separators. For ferromagnetic materials, the Davis tube is more suitable and is the common tool for characterizing magnetic iron ores (Davis, 1921).
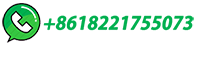
Magnetic separation: A review of principles, devices, and …
Conventional magnetic separation devices are widely used for the removal of tramp iron from a variety of feed materials and for the beneficiation of ferrous ores. These devices …
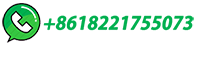
Increasing efficiency of iron ore magnetic separation …
enhance efficiency of iron ore magnetic separation by applying ultrasonic technologies. Thus, it is required to combine research results in the following directions: theoretical and practical research into iron ore magnetic separation; methods and means of operative control over physical-mechanical and chemical-
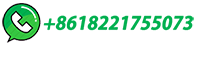
Magnetic separation: A review of principles, devices, and applications
Conventional magnetic separation devices are widely used for the removal of tramp iron from a variety of feed materials and for the beneficiation of ferrous ores. These devices for separation of strongly magnetic materials employ a variety of mechanical designs. Recently developed high gradient magnetic separation devices extend the useful …
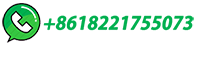
Recycling of iron ore tailings into magnetic nanoparticles …
Iron ore tailing is a major solid waste requiring advanced recycling methods because ore tailing powder is polluting air and water resources. For instance, about 300 million tons of tailings are disposed yearly in 1229 iron ore tailings dams in the Hebei province in China. Iron ore tailings can be recycled as functional materials because these tailings are …
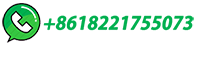
Mining separation and sorting equipment for processes in the mining
Mining separation - magnetic separation and sensor sorting solutions for improved throughput and recovery rates in ore sorting and mineral processing From traditional and trusted magnetic separation equipment, right through to innovative sensor sorting technologies, we help our customers achieve their goals with sustainable solutions.
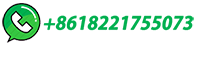
Dry beneficiation of iron ore
Falling prices for iron ore with lower quality than 60 % Fe have led increasingly to the design of iron ore beneficiation lines. General problems of water scarcity and risks with tailings dams have led to the focus shifting to dry beneficiation technologies.
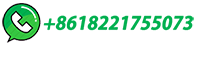
Non-magnetic physical separation of hematitic/goethitic iron ore
Whereas the correct sizing of iron ore is achieved through comminution and screening processes as described in Chapter 8, this chapter concerns the further processes applied to comminuted and sized portions of iron ore for subsequent physical removal of unwanted gangue in a bid to enhance chemical properties. The main physical …
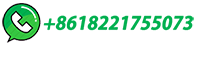
Recovery and separation of iron from iron ore using …
In this investigation, a pilot-scale fluidized magnetization roasting reactor was introduced and used to enhance magnetic properties of iron ore.
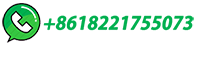
STEINERT MRB for two-stage magnetic separation of …
A combination of our magnet separators enables optimal separation of ferrous metal fines without further conveyors and transfer points.
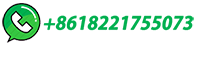
Wet High Intensity Magnetic Separation
WHIM is the short acronym for Wet High Intensity Magnetic Separation. At present, most U.S. iron raw materials are produced from magnetic taconites, which are ground to a nominal minus 270 mesh (53 …
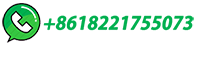
Comparing strategies for iron enrichment from Zn- and Pb …
Apart from Fe content and Fe recovery, the contents of Zn and Pb in concentrates should be taken into consideration in the treatment of Zn- and Pb-bearing refractory iron ore through reduction roasting-magnetic separation. Hematite in the iron ore was reduced to magnetite through magnetic roasting at 800 °C for 60 min, and iron …
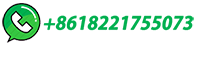
Iron Ore Processing: From Extraction to Manufacturing
High-intensity magnetic separators are used to separate the magnetic iron-bearing minerals from the non-magnetic gangue minerals. This technique is effective for removing strongly magnetic impurities from the ore.
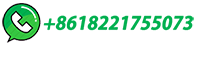
North America Iron Ore Magnetic Separator Market Size …
North America Iron Ore Magnetic Separator Market Size 2024 & Analysis By Application | Hematite, Limonite, Ilmenite, Siderite, Chromite
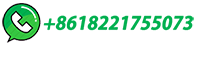
Magnetic separation studies for a low grade siliceous iron ore sample
Investigations were carried out, on a low grade siliceous iron ore sample by magnetic separation, to establish its amenability for physical beneficiat…
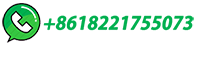
Study on Metallized Reduction and Magnetic Separation of Iron …
Separation of iron from fine particles of high iron bauxite ore by the process of metallized reduction and magnetic dressing was researched systemically. The effect of magnetic field intensity, reduction temperature, reduction time, mole ratio of fixed carbon to reducible oxygen (FC/O) and ore particles size on separation indexes was researched.
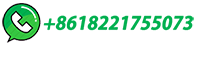
DRY MAGNETIC SEPARATION OF MAGNETITE ORES
The separation of chromite ore with lowest particle size fraction was done using Mozley mineral separator followed by the magnetic separation of the sink product by magnetic separator. The results obtained revealed about 77% of the total material containing 300 μm particle size, 52% ˂ 212 μm and 17% below 75 μm.
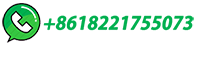
Separations | Free Full-Text | Application of Magnetic Separation
Magnetic separation technology is a physical separation method that uses the differences in magnetism between matter to separate them from each other by different motion behaviors in a non-uniform magnetic field. It is highly efficient, green, and environmentally friendly, with little change in the physical and chemical properties of raw …
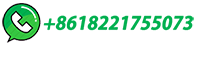
Physical separation of iron ore: magnetic separation
The SLon-1000 magnetic separator can treat weakly magnetic minerals in the size range of 0–2.0 mm, and has been used in industry for upgrading roasted kaolin of 0–0.2 mm particle size by removing the impurities comprising oxidized iron ore and other …
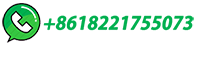
Separations | Free Full-Text | Application of Magnetic …
Magnetic separation technology is commonly used in the field of mineral processing engineering for magnetite, hematite, titanite, and other magnetic ferrous …
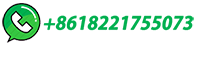
For dry and wet processing Low Intensity Magnetic …
The Low intensity magnetic separators are available in several types for vast number of duties and could be seen as split into two categories, i.e. dry separation and wet separation.
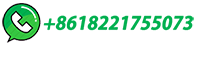
The six main steps of iron ore processing
Learn about the steps involved in iron ore processing, from crushing and grinding to separation. Contact Multotec experts for guidance on iron processing.
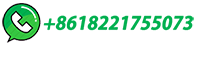
Magnetite
accounts for approximately 50% of global iron ore production. The magnetic properties of magnetite enable it ... magnetic separator circuit in the magnetite extraction plant. ... separated according to particle size.
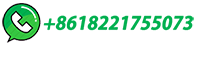
How Magnetic Separation Optimizes Sorting and …
Understanding the magnetic susceptibility of the industrial and included diamonds to be sorted is imperative to optimizing the magnetic cut-point for minimizing yield on the …
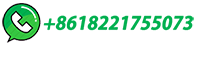
High Pressure Grinding Roll and Magnetic Separation for
This paper presents an industrial verification test, adding a high pressure grinding roll and magnetic separation operation after the third-stage fine crushing operation to reduce the particle size of ball mill feed and improve the processing capacity of grinding operation. The optimal process parameters of high pressure grinding roll and …
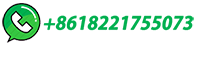
Development of a centrifugal dry magnetic separator for separation …
In this investigation, a new full-scale centrifugal dry magnetic separator (cDMS) was introduced and applied to pre-concentrate a low-grade fine magnetite ore, and its separation performance regarding feed particle size was evaluated, in comparison with a typically dry magnetic separator. 2. Experimental2.1.
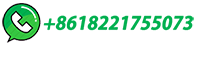