Minerals | Free Full-Text | Influence of Mineralogy on the Dry Magnetic …
Magnetic separation is often considered pertinent for manganese ore beneficiation when the ore is abundant with siliceous rich gangue mineral phases. However, the process is deemed to be inapposite for the ferruginous type of ore, and remains a grey area of research. In the present investigation, two different types of manganese ore were studied in …
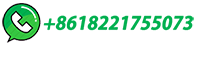
Physical separation of iron ore: magnetic separation
The SLon-1000 magnetic separator can treat weakly magnetic minerals in the size range of 0–2.0 mm, and has been used in industry for upgrading roasted kaolin of 0–0.2 mm particle size by removing the impurities comprising oxidized iron …
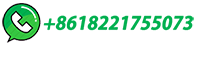
Assessing the performance of a novel pneumatic magnetic separator for
A novel low-intensity pneumatic planar magnetic separator designed to recover and concentrate fine-grained magnetite minerals is investigated and the performance compared with those of conventional wet magnetic separators, i.e., …
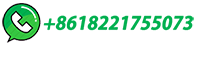
Mineral Magnetic Modification of Fine Iron Ore Tailings …
magnetic separation of magnetite quartzite leads to the concentration of magnetite in a valuable product due to its strong magnetic properties, while weakly magnetic minerals, i.e., hematite, goethite, and quartz, are discharged in tailings via slurry. The quantity of tailings is constantly increasing, since in most cases they are not
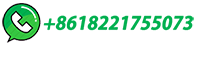
Experimental Study on Magnetic Separation of Oolitic Hematite Ore
To enhance effective use of resources, we use magnetic separation method on the experiment study of a refractory oolitic hematite ore. Research showed that: the grade of raw ore (TFe) was 47.44% ...
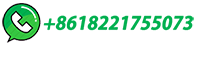
Comparison Of Limonite Gravity, Magnetic And Flotation Separation
Each process has its advantages and disadvantages when separating limonite ore. Gravity separation offers a low-cost method but may need help recovering fine particles or efficiently removing impurities.Magnetic separation is highly selective but requires large equipment and may produce tailings with lower iron grades.Flotation has many uses, but often …
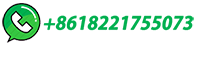
Magnetic separation of hematite and limonite fines as …
Magnetic separation of weakly magnetic iron mineral fines in the form of flocs, which is termed Floc Magnetic Separation (FMS) process, has been studied in the present work, in order to find a substitution for high-intensity or high-gradient magnetic separators to treat the ores with weakly magnetic iron minerals in the fine size range.
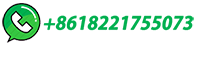
Hematite: A primary ore of iron and a pigment mineral
Hematite's Streak: All specimens of hematite will produce a reddish streak. The streak of a mineral is its color in powdered form when scraped across a streak plate (a small piece of unglazed porcelain used to produce a small amount of mineral powder). Some specimens of hematite will produce a brilliant red streak, others will produce a reddish brown streak.
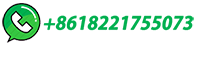
Mineral Jig Separator | Jig Concentrator
Jig separator (jig concentrator, jig machine) is a equipment that drives pulses of water upwards through a thick bed of settled sediment to keep it loose and agitated.This achieves gravitational separation by allowing the denser minerals to sink easily and quickly through the lighter minerals. Jig separator are widely used in various heavy metal, metallic and non-metallic …
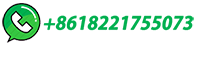
Magnetic separation of hematite and limonite …
The slurry was first adjusted for pH using sodium hydroxide solution, and then was strongly conditioned at 1200 rev/min for a given time while sodium oleate or kerosene emulsion was added, leading to the formation of hydrophobic flocs …
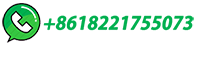
A pilot study on recovery of iron from sulfur-bearing …
At this time, iron minerals could be effectively recovered by a grinding and low-intensity magnetic separation process. Under the optimum roasting and magnetic …
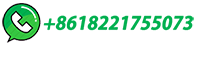
Beneficiation of a low-grade, hematite-magnetite ore in China
In China, most reserves of rich iron ores have now been depleted and sustainable development of low-grade iron ores has become a critical discussion topic in the mining industry today. The aim of this study was to evaluate the applicability of beneficiating a low-grade, hematite-magnetite ore (assaying 18.64% Fe) for subsequent utilization. In this study, …
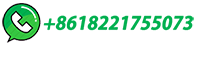
Mineral Magnetic Modification of Fine Iron Ore Tailings and …
In this paper, the properties, mineral magnetic modification, and beneficiation of tailings from the central mining and processing plant in Kryvyi Rih, Ukraine, have been studied. Samples were investigated by X-ray diffraction, X-ray fluorescence, microscopy, and magnetization measurements. The beneficiation was conducted using magnetizing roasting …
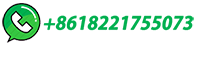
Minerals | Free Full-Text | Parameter Optimization …
Iron is a common ferrous metal that has wide application in various fields, including metallurgy, chemical industry, and the manufacture of mechanical equipment [1,2].Hematite (α-Fe 2 O 3), an iron mineral that is widely …
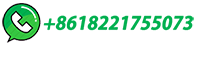
Types of Mining Magnetic Separators
Common Iron Minerals are magnetite (strong magnetic minerals), hematite (weak magnetic minerals), Limonite, specularite, siderite (all weak magnetic minerals). They are raw materials for the steel industry. ... Wet Permanent Magnetic Drum separator is a kind of magnetic separator often used in iron ore concentrators. It is suitable for ...
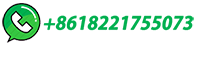
(PDF) Magnetic separation of monazite from mixed minerals …
A wet high-intensity magnetic separator (WHIMS) was selected to remove iron oxides at low magnetic field intensities while concentrating the REE minerals at higher magnetic field intensities, with ...
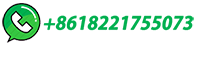
Simultaneously Roasting and Magnetic Separation to …
Abstract. During the roasting process, siderite (FeCO 3) transforms to magnetite (Fe 3 O 4) along with producing carbon monoxide (CO), but hematite (Fe 2 O 3) needs CO to reduce into magnetite.The process of simultaneously roasting and magnetic separation was developed to treat the low grade siderite and hematite ores without adding any reductant.
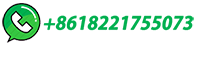
Intensity Magnetic Separator
As shown in Figure 13.2, minerals with ferromagnetic properties have high susceptibility at low applied field strengths and can therefore be concentrated in low intensity (<~0.3 T) magnetic separators. For low-intensity drum separators (Figure 13.11) used in the iron ore industry, the standard field, for a separator with ferrite-based magnets, is 0.12 T at a distance of 50 mm …
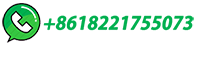
Beneficiation of Low-Grade Hematite Iron Ore Fines by …
Present investigation includes the magnetizing roasting of low-grade iron ore fines followed by grinding and beneficiation using magnetic separation. The hematite iron ore used in the ...
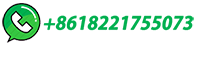
Beneficiation of Low-Grade Hematite Iron Ore Fines by …
Present investigation includes the magnetizing roasting of low-grade iron ore fines followed by grinding and beneficiation using magnetic separation. The hematite iron ore used in the investigation contains 53.17% T Fe, 10.7% SiO2, and 4.5% Al2O3. Powdered bituminous …
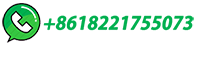
Recovery of magnetite-hematite concentrate from iron …
A processing flowsheet includes magnetic separation, milling and gravity concentration methods. The separation technology provides for production of iron ore concentrate with total …
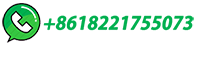
Beneficiation of Low-Grade Hematite Iron Ore Fines by …
Hematite ore's magnetic characteristics were significantly impacted by magnetizing roasting. By selectively magnetizing roasting, hematite is transformed into magnetite. With an Fe grade of 65.25% at a recovery value of 72.5% in the concentrate, magnetic separation produced the greatest result for Fe.
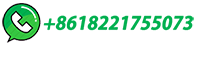
Thermally assisted magnetic separation and
For example, the magnetic separation of the unheated ore at 0.77 T results in a product having a yield of 30.3% and 62.5% Fe. On applying the same magnetic intensity, the ore treated at 500 °C gives rise to an enhanced yield of 43.55% with a decrease in Fe percentage to 61.68%. ... The micron sized hematite minerals are finely dispersed within ...
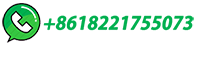
Chemical and mineral transformation of a low grade goethite ore …
The most ferromagnetic iron compound is magnetite although hematite and siderite can be separated by magnetic separation after phase transformation into magnetite by reduction roasting. The magnetic separator divides the samples into …
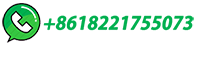
The Magnetic Separation Process for Ore Processing
Benefits of Magnetic Separation in Ore Processing: 1. High Efficiency: Magnetic separation offers high efficiency in separating valuable minerals, leading to increased yields and reduced ...
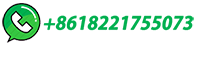
A pilot study on recovery of iron from sulfur-bearing hematite ore …
Sulfur is a harmful impurity in iron ore, which seriously affects the subsequent smelting process and product quality. In this study, a novel process of hydrogen-based mineral phase transformation followed by magnetic separation was proposed to treat sulfur-bearing refractory iron ore.
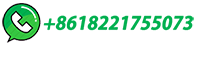
Wet High Intensity Magnetic Separation of Iron Minerals
As can be s reducing particle size from −200 + 100 µm to <75 µm leads to an increase in iron g from 27% to 33%, whereas the iron recovery diminishes from 96% to 73%.
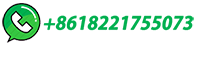
Pelletization of hematite and synthesized magnetite concentrate from …
The BHQ ore sample was obtained from one of the iron ore mines of Hospet located in the Karnataka state of India. The chemical analysis of the BHQ sample is given in Table 1.The sample was crushed to below 10 mm size, and a representative sample was drawn to generate hematite and magnetite pellet feed concentrates through the techniques of …
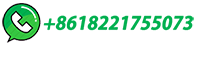
Mineralogical reconstruction of Titanium-Vanadium hematite and magnetic
Fig. 1 shows the magnetic reduction roasting device used in the experiment, the main body of which comprises a thermal-resistant wire heating furnace and a quartz tube. One end of the quartz tube was connected to the gas input tube for protective N 2 and reducing agent CO to control the surrounding atmosphere of the sample to be roasted. At a constant roasting …
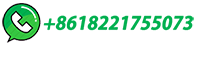
(PDF) Mineral and Technological Features of Magnetite–Hematite …
Mineralogical studies have established that the main iron-bearing mineral is hematite, which contains 69.02 to 70.35% of iron distributed in the ore. ... magnetic separation, will precipitate into ...
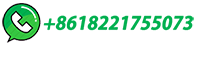