Investigation of Pyrometallurgical Nickel Pig Iron (NPI) …
Nickel is mainly used in stainless steel production as ferronickel. In recent years, low grade ferronickel or nickel pig iron (NPI) is used in stainless steel production to reduce expenditure of ...
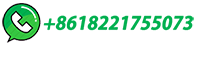
Advances and Innovations in Ferronickel-Making
This book introduces the most inspiring progress in the production of ferronickel from laterite ores from both theoretical and technological perspectives. ... Based on a detailed overview of nickel utilization from laterite ores, it provides the advances of four main methods for laterite ore processing, including the solid-sate reduction ...
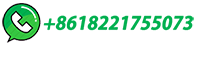
FERRONICKEL PRODUCTION AND OPERATION
grade ferronickel or nickel pig iron (NP!) in stainless steel production is a relatively new trend to reduce the cost of high grade ferronickel. In this study, low grade lateritic nickel ores were ... The process is almost same as pig iron production processes. The only difference is that the ore contains more nickel. The blast furnace products ...
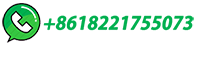
Oxidative Acidic Leaching of Ferronickel Slag for
Pyrometallurgical processing of lateritic ore produces huge amounts of ferronickel slags, which may contain valuable metals. This paper describes a novel hydrometallurgical route to recover metals from ferronickel slag samples and reduce liability matters using oxidative acidic leaching. Hydrochloric acid and hydrogen peroxide were …
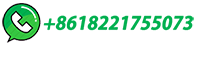
Production of Ferronickel Concentrate from Low-Grade Nickel …
The production of ferronickel concentrate from low-grade nickel laterite ore containing 1.31% nickel (Ni) was studied by the non-melting reduction magnetic separation process. The sodium chloride was used as additive and coal as a reductant. The effects of roasting temperature, roasting duration, reductant dosage, additive dosage, and grinding time on the …
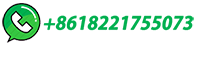
Effect of thiosulfate, sulfide, copper(II), cobalt(II)/(III) and iron …
Rates of nickel dissolution from particle leaching and electrochemical tests are of the same order (~10 –4 mol m –2 s –1).Pure nickel, ferronickel alloys and roasted calcines in typical Caron lixiviant system show similar leaching curves with 70%–90% Ni extraction depending on the Ni mole fraction of the feed, but iron dissolution is slow and low (< 2%) due …
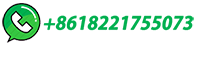
High-Grade Ferronickel Concentrates Prepared …
Nickel is widely used in industrial processes and plays a crucial role in many applications. However, most of the nickel resource mainly exists as nickel oxide in laterite nickel ore with complex composition, resulting in …
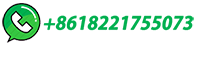
Improving the rotary kiln-electric furnace process for …
1. Introduction. Ferronickel, an alloy containing 20–40 wt% nickel and 60–80 wt% iron, is essential to manufacture stainless steel and other alloys [1], [2].Ferronickel is vital to …
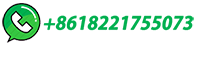
RKEF Lateritic Nickel Rotary Kiln for Sale, Rotary Kiln for Nickel …
Laterite nickel rotary kiln is the main equipment for ferronickel production after calcination and smelting of laterite nickel ore. The nickel laterite ore rotary kiln can produce nickel iron by direct reduction method, and it is also one of the key pieces of equipment in the rotary kiln electric furnace (RKEF) smelting process.. The laterite nickel rotary kiln produced by AGICO Rotary …
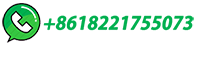
High-Grade Ferronickel Concentrates Prepared from Laterite …
Nickel is widely used in industrial processes and plays a crucial role in many applications. However, most of the nickel resource mainly exists as nickel oxide in laterite …
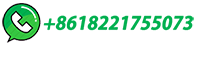
Ferronickel
An evaluation of operations with high and low amounts of iron reduction is shown Table 6.2.Generally, high reduction of iron (lower content of nickel in ferronickel) is favored when (i) high recovery of nickel is critical, (ii) a reasonable price is realized for the Fe in the ferronickel; and, (iii) the costs of transportation of the ferronickel to market are low.
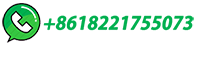
The Nickel Production Methods from Laterites and the Greek …
Primary world nickel production in 2020 was 2430.7 kt Ni; 69% (1677.7 kt) of them came from oxidized nickel ores (laterites) and 31% from sulfides. Production-wise, 87.7% of the 1677.7 kt came from pyrometallurgical and 12.3% from hydrometallurgical processes. For a long time, …
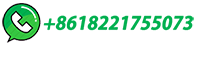
Effect of thiosulfate, sulfide, copper(II), cobalt(II)/(III) and iron …
Request PDF | Effect of thiosulfate, sulfide, copper(II), cobalt(II)/(III) and iron oxides on the ammoniacal carbonate leaching of nickel and ferronickel in the Caron process | Previous studies ...
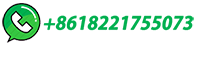
Nickel in Indonesia: A Story of Trade Restraints and …
Figure 1: Simplified production process for nickel in Indonesia. 2. Ferronickel/Nickel Pig Iron Production : Since the export ban was first enforced in 2014, Indonesia's NPI production has increased substantially, and it has become the leading supplier of NPI to China. According to the World Bureau of Metal Statistics, Indonesia produced
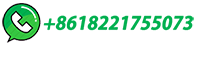
Preparation of ferronickel from nickel laterite via coal-based
The sticking phenomenon between molten slag and refractory is one of the crucial problems when preparing ferronickel from laterite ore using rotary hearth furnace or rotary kiln processes. This study aims to ameliorate sticking problems by using silicon dioxide (SiO2) to adjust the melting degree of the briquette during reduction roasting. Thermodynamic analysis …
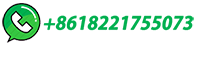
Metallurgy of Ferronickel | SpringerLink
The specific energy consumption for metallurgical processing of 1 ton of Pobuzhsky dry nickel-containing ore with 1% Ni is 810 kWh/t or 78,200 kWh per 1 ton of nickel. ... The extraction of iron in ferronickel is 4.2%. Author information. Authors and Affiliations. National Metallurgical Academy of Ukraine, Dnipro, Ukraine. Mikhail Gasik ...
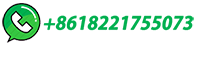
Ferronickel Production from Nickel Laterite via Sulfide …
Conclusion. A sulfide-based processing pathway is presented for ferronickel production from laterite. Analyses of laterite feedstock and sulfidation products suggest that …
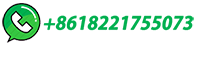
Preparation of high-grade ferronickel from low-grade nickel …
According to thermodynamic analysis of metallic nickel and iron oxidised by CO 2 and the experimental results of nickel laterite processing via self-reduction and selective …
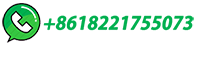
Assessing the energy and greenhouse gas footprints of …
The first processing treatment for recovering nickel from laterites was developed in 1879 in New Caledonia, based on the iron blast furnace technology of the day. Processing …
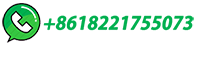
An Overview of Nickel Utilization from Laterite Ore
The technological process of producing nickel pig iron (NPI) ... and integrating the continuous casting and rolling process to ferronickel and stainless steel production [98, 99]. However, compared with the direct reduction process and blast furnace process, the cost of RKEF process is still 10–20% higher. ...
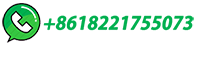
Ferronickel smelting plant Electric furnace off-gas …
Ferronickel is an alloy containing iron and nickel and is used mainly as raw material for producing stainless steel. In recent years, the global stainless steel market has seen ... 1 Ferronickel smelting plant and process Kawasaki's ferronickel smelting plant follows the process shown in Fig. 1. Ferronickel ore with 1.8-2.2% nickel
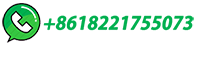
Production of Ferronickel Concentrate from Low …
The production of ferronickel concentrate from low-grade nickel laterite ore containing 1.31% nickel (Ni) was studied by the non-melting reduction magnetic separation process. The sodium chloride was used as additive and coal as a …
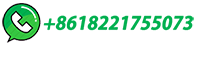
An Overview of Nickel Utilization from Laterite Ore
The metal elements, including nickel, iron, and cobalt, are selectively leached at high temperature and high pressure. The leaching of nickel and cobalt reach nearly 95%, ...
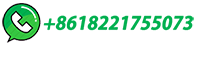
The Nickel Production Methods from Laterites and …
Iron-nickel ores in the plant are characterised by high moisture content, a very important factor influencing the process of scraping the charge in rotary kilns and presenting in general. Among the iron-nickel ore used in the ferronickel …
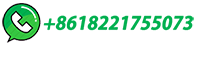
Modelling of Nickel Laterite Smelting to Ferronickel
to as the "RKEF process" (Walker et al., 2009) due to its use of rotary kilns (RK) and electric furnaces (EF). Typical industrial data was given by Warner et al. (2006) and part of this is ... The activities of iron and nickel in ferronickel alloys were determined by Conard et al. (1978) and showed that the activity coefficient of iron is ...
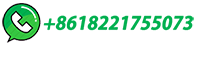
Ferronickel Sulfidation: A Solution to Supplying the Battery …
Saprolites are formed beneath the limonitic zone and are rich in magnesia and silica. These ores are typically processed via the rotary kiln, electric furnace (RKEF) process to produce Class II nickel products including ferronickel (FeNi, typically 20–40% Ni) and nickel pig iron (NPI, typically 8–12% Ni).
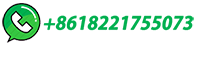
Technology of Ferronickel
The standard ferronickel for steelmaking has a wide range of compositions, from 5% to 25% Ni, Table 10.1. Solar et al. (2008) noted two trends in nickel laterites processing, one favoring high-grade ferronickel (35% to 40% Ni) and the other favoring lower grades (20% to 25% Ni). Because the ores processed vary widely in terms of nickel content and other …
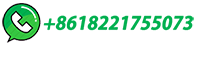
Material and energy flows in rotary kiln-electric furnace smelting …
Kotzé [16] proposed the process of producing ferronickel from nickel oxide ores and dust particles by DC arc furnace technology. Guo [17] carried out ferronickel smelting experiment to investigate the selective reduction and melting-separation processes, and to analyze the influence parameters of metallization rate. ... Effective extraction ...
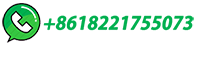
Metals | Free Full-Text | Nickel Laterite Smelting …
Low-grade ferro-nickel is simply an iron–nickel alloy that contains lower nickel than standard ferro-nickel does (i.e., minimum of 15%). ... In relation to the future development of the ISASMELT TM process for nickel …
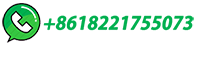
Nickel production from low-iron laterite ores: Process descriptions
The softening-melting behaviors of CVTP, the reduction of nickel into pig iron, and the depolymerization of slag structure indicate the feasibility of producing nickel–iron alloy through the ...
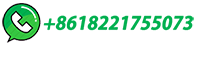