Cold Bonding of Iron Ore Concentrate Pellets: Mineral Processing …
Iron ore concentrate pellets are traditionally hardened at high temperatures in horizontal grates and grate-kiln furnaces. However, heat induration requires tremendous quantities of energy to produce high-quality pellets, and is consequently expensive. Cold bonding is a low-temperature alternative to heat induration.
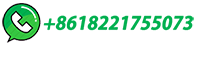
Recent Trends in the Technologies of the Direct Reduction …
The blast furnace and direct reduction processes have been the major iron production routes for various iron ores (i.e. goethite, hematite, magnetite, maghemite, siderite, etc.) in the past few decades, but the challenges of maintaining the iron and steel-making processes are enormous. The challenges, such as cumbersome production routes, scarcity of …
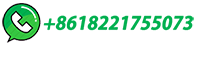
Pilgangoora Operation | Pilbara Minerals
The processing plants were named by the Traditional Owners of the land, the Nyamal People, in recognition of their connection to the country on which the Pilgangoora Operation is located. ... sorting facility capable of processing up to 5 Mtpa of ore throughput and supporting further process improvements and concentrate quality. First-ore was ...
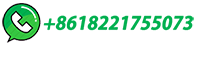
Iron Ore Plant royalty-free images
Find Iron Ore Plant stock images in HD and millions of other royalty-free stock photos, 3D objects, illustrations and vectors in the Shutterstock collection. Thousands of new, high-quality pictures added every day.
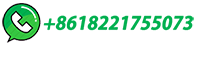
Development of ore sorting and its impact on mineral processing
The energy costs required to refine metal values contained in ore to concentrates constitute the majority of the cost to produce metals. On average across the mining industry, 44% of the total electricity consumption is dedicated to crushing and milling activities (Fig. 1).Size reduction operations, nearly 150 × 10 9 kW h, are the largest single consumer of energy …
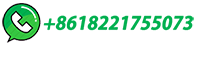
Iron ore pelletization
15.1. Introduction. Iron ore lump, sinter, and pellets comprise the main burden of modern blast furnaces. However, sinter and pellets are now the dominant blast furnace burden, because the natural lump supply has declined dramatically due to depletion of the world's high-grade competent iron ore resources.
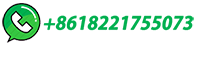
Iron ore beneficiation: an overview
Dry processing of iron ore: In dry processing of iron ore, ROM is generally crushed below 40 mm through three-stage crushing and thus segregated by screening into 10–40 and −10 mm fractions. For softer ore, tumbler index is generally low and hence lump ore is crushed below 10 mm to produce fine product. Yield from the plants has been ...
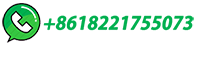
ROSIE—Revolutionizing Ore to Steel to Impact Emissions
land, CALaser Furnace for Reduction of Iron Ore to Iron Metal - $2,910,346Limelight Steel is developing a laser furnace to convert iron ore into ir. n metal without emitting carbon dioxide …
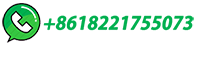
A critical review on metallurgical recovery of iron from iron ore
Fig. 2 illustrates the iron ore beneficiation process, particularly magnetic separation, resulting in the generation of inevitable tailings. Due to the characteristics of iron ores and the conditions during beneficiation, it is inevitable that approximately 2.5–3 tons of IOTs are generated for every 1 ton of iron ore concentrate produced [7].In 2019, the global annual …
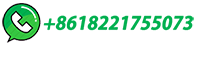
A review of ironmaking by direct reduction processes: …
Blast furnace ironmaking requires separate coke making and sintering plants and often has reduced operating flexibility (Lu, Pan and Zhu, 2015). ... H. (2011) ‘In fl uence of direct reduced iron on the energy balance of the electric arc furnace in steel industry’, Energy. ... requirements of iron ore for iron production’, in ...
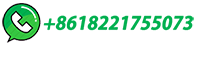
8.2 Mining and Ore Processing – Environmental Geology
When ore is first processed (typically close to the mine) it is crushed to gravel-sized chunks and then ground to a fine powder and the ore minerals are physically separated from the rest of the rock to make a concentrate. At a molybdenum mine, for example, this concentrate may be almost pure molybdenite (MoS 2). The rest of the rock is known ...
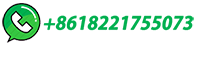
Driving investments in ore beneficiation and scrap …
The pressure on the steel industry to reduce its carbon footprint has led to discussions to replace coke as the main reductant for iron ore and turn to natural gas, bio-syngas or hydrogen. Such a major transition from the blast …
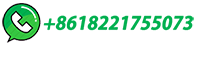
Development of Ironmaking Technology by the Direct …
with gaseous reduction of iron ore concentrate (MBIT). These technologies are designed to produce iron directly from iron concentrate without requiring pelleti-zation/sintering and cokemaking. They take advantage of the high reactivity of the concentrate particles and will significantly reduce energy consumption and carbon
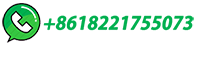
Fortescue's Iron Bridge Magnetite project marks …
The Iron Bridge project is going to create hundreds of jobs and make a significant contribution to the WA economy." The nature of the Iron Bridge ore bodies and Fortescue's innovative use of a dry crushing and …
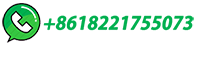
A Comprehensive Guide to Manganese Ore Processing
Battery Manufacturing: Manganese is an essential component in lithium-ion batteries, used in electric vehicles and renewable energy storage systems. Efficient processing of manganese ore ensures a ...
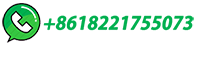
Iron ore tailings valorization through separate
Process flowsheet of the iron ore processing plant. An iron ore processing plant with an average throughput of 650 tons per hour is located at northeast of Iran and it produces 2.5 million tons of iron ore concentrate with iron grade more than 65% annually. The run of mine ore with an average iron grade of 45% is fed to a gyratory crusher.
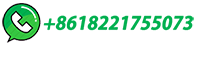
Integrated Production and Distribution Planning for the Iron Ore …
There are mainly three stages in the iron ore concentrate supply chain, i.e., the mining stage, the ore concentrate production stage, and the distribution stage. In the mining stage, the crude ores are mined from multiple ore locations, satisfying the mining capacity limits and the quality requirements (e.g., the minimum ore grade requirement ...
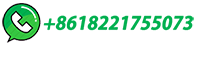
8.2: Mining and Ore Processing
When ore is first processed (typically close to the mine) it is crushed to gravel-sized chunks and then ground to a fine powder and the ore minerals are physically separated from the rest of the rock to make a concentrate. At a molybdenum mine, for example, this concentrate may be almost pure molybdenite (MoS 2). The rest of the rock is known ...
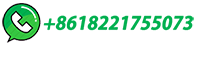
Pelletization of hematite and synthesized magnetite concentrate from …
The BHQ ore sample was obtained from one of the iron ore mines of Hospet located in the Karnataka state of India. The chemical analysis of the BHQ sample is given in Table 1.The sample was crushed to below 10 mm size, and a representative sample was drawn to generate hematite and magnetite pellet feed concentrates through the techniques of …
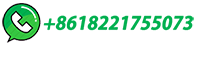
Process simulations in mineralogy-based …
Materials. The two feeds that used for plant simulation were from Luossavaara-Kiirunavaara Ab (LKAB) iron ore deposit. The first data set is actual feed to the plant that were collected a during plant survey and analyzed in …
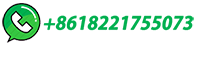
PGM Ore Processing at Impala's UG-2 Concentrator
Figure 3: MF1 UG2 plant setup (1991-1994) Figure 4 MF2 circuit at Impala's UG2 plant (1994-2001) UG-2 Ore PrOcessinG PrObleMs and sOlUtiOns Historically UG2 ore could not be processed due to the high chrome content in the feed and subsequently in the final concentrate. Very little of the chrome itself exhibits any degree of
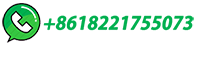
High Pressure Grinding Roll and Magnetic Separation for Energy …
With the increasingly serious problems of low-grade, fine iron minerals, and difficult-to-treat ore properties, the required particle size of ore grinding products are becoming finer, and the requirements for energy saving, consumption reduction, and efficiency improvement of mineral processing plants are also becoming more and more urgent [1 ...
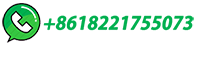
Pilot-Scale Demonstration of Ilmenite Processing …
The historic difficulty in processing titanium resources from the OUI resulted from impurities, such as magnesium oxide, in the crude ore and concentrate products. Previous research found that a large portion of the magnesium is associated with the chemical composition of the ilmenite and cannot be removed using conventional processing techniques.
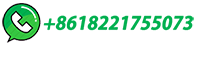
Making Iron Directly From Concentrate by Gaseous Reduction
The reduction of magnetite concentrate by CO was determined to be much slower than the reduction by H 2 gas. Experiments were performed to investigate the reduction …
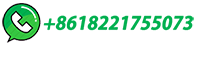
Iron Ore Processing
Resource Recovery and Recycling from Metallurgical Wastes. S. Ramachandra Rao, in Waste Management Series, 2006 9.8 Production of Ceramic Tiles from Iron Ore Tailings. Current practice of washing iron ore before it is processed for extractive metallurgical operation results in three products, coarse ore lumps with sizes in the range 10-80 mm, which are directly charged …
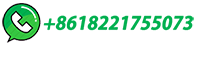
Iron processing | Definition, History, Steps, Uses, & Facts
Iron processing, use of a smelting process to turn the ore into a form from which products can be fashioned. Included in this article also is a discussion of the mining of iron and of its preparation for smelting. Iron (Fe) is a relatively dense metal with a …
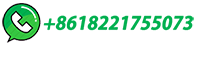
Mechanism of magnetite iron ore concentrate morphology …
1. Introduction. Iron ore pellets are one of the significant sources of iron for iron and steel making due to their superior metallurgical performance, low energy consumption, and less emission of environmentally harmful dust and gases during the production process [1], [2], [3].The two primary raw materials for pellet production are hematite and magnetite concentrates.
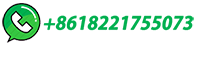
Sintering: A Step Between Mining Iron Ore and …
The remaining 2% of domestic iron ore was produced for non-steel end uses. Seven open-pit iron ore mines (each with associated concentration and pelletizing plants), and three iron metallic plants—one …
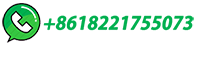
Froth Flotation of Iron Ores
With the depleting reserves of high-grade iron ore in the world, froth flotation has become increasingly important to process intermediate- and low-grade iron ore in an attempt to meet the rapidly growing demand on the international market. In over half a century's practice in the iron ore industry, froth flotation has been established as an efficient method to remove …
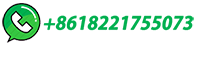
Recent Trends in the Technologies of the Direct Reduction …
The blast furnace and direct reduction processes have been the major iron production routes for various iron ores (i.e. goethite, hematite, magnetite, maghemite, siderite, …
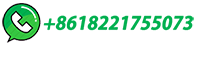