The Ultimate Guide on How to Crush Stone: Techniques and …
There are two critical factors influencing choice of crushing techniques and equipment. Hardness of the rock and abrasiveness. Hardness of the rock is typically …
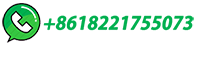
Everything you need to know about Crushers in Cement …
The roller crushers are used for moist and sticky materials. Generally the machines have to be rigid enough to crush also hard inclusions. As the reduction ratio is only about 5:1 a 2-stage crushing is required in most applications.
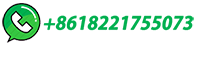
Types Of Crusher
According to the working principle, crushing machines are divided into the following types: cone crusher; jaw crusher; impact crusher; These are the most basic distinctions. There may also be sub-types of these machines. For example, impact crushers have varieties such as vertical shaft crushers or tertiary crushers
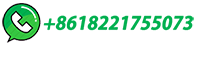
Crushing
Relation between Feed size and Shape. The greater reduction ratio the worse particle shape. Inter particle breakage improves shape. When crushing a bed of material weaker particles will …
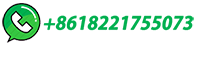
Gyratory Crusher l Introduce, Working Principle
Crusher Working Principle. The primary gyratory crusher breaks the material by feeding mouth into the two rollers between the extrusion crushing, finished materials naturally fall. In case of too hard or can not be broken, the roller crusher by hydraulic cylinder or the role of the spring can automatically retreat. ... Get more stone crusher ...
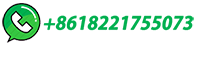
A Guide to Mobile Crushing Plants: Types, Components
Mobile crushing plants have revolutionized the way materials are extracted and processed in various industries. They offer flexibility, mobility, and efficiency that cannot be achieved with traditional stationary crushing plants. As the name suggests, these plants are designed to be easily moved from one site to another, making them ideal for use in remote …
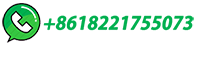
CRUSHING SCREENING
Primary impact crushers are preferred for their high performance and high reduction ratios in crushing softer substances like gypsum and limestone. Due to the different principle of crushing these ma-terials, the reduction ratio is higher than in jaw crushers. MPI1313 MPI 1515 MPI 1620 Max. feeding size (mm) 900 1000 1300
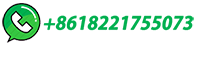
Crushing it: A Comprehensive Guide to Stone …
The workflow of a stone crusher plant involves several steps, including the feeding, crushing, screening, and conveying of materials. The materials are fed into the primary crusher by the vibrating feeder, where they …
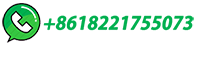
How Does a Jaw Crusher Work
Cone crushers and jaw crushers both work by compression, reducing materials by squeezing them until they break apart. The benefit that cone crushers offer over jaw crushers is their ability to output a more cubical product similar to impact crushers. Cone crushers have traditionally been used as secondary and sometimes tertiary crushing stations.
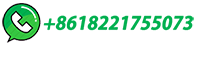
Cone crusher basics in 4 minutes
Cone crusher basics in 4 minutes. This is the starting point for understanding how cone crushers work – and how they can make your mine or quarry more productive. Elsewhere on the site you can find detailed information about all …
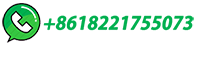
How it Works: Crushers, Grinding Mills and Pulverizers
Table Source: Wikipedia (Crushers) Cone crushers use a spinning cone that gyrates in the bowl in an eccentric motion to crush the rock between the cone surface, referred to as the mantle, and the crusher bowl liner.Gyratory crushers are very similar to cone crushers, but have a steeper cone slope and a concave bowl surface. As the gap between the bowl liner …
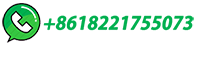
Working Principle of Crushers
Working Principle of Crushers. On left is a showing of the "standard gyratory with straight concaves" is a section through any vertical, radial plane in the crushing chamber of one of the intermediate sizes of the crusher. In order to understand the crushing action in such a chamber it is helpful to consider the process as though each step took place in an orderly, and …
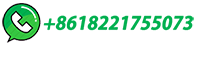
Vibrating Screen Working Principle: …
450t/h Stone Mobile Crushing Plant; 320t/h Construction Waste Material Crushing Station; 250t/h Limestone Mobile Crushing Plant ... their applications, advantages, and disadvantages. By understanding the working …
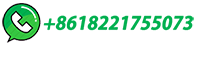
4 Types of Stone Crushers' Maintenance and Efficient …
Horizontal Shaft Impact crusher (HSI) Impact crusher working animation The working principle of impact crusher is that the spinning rotor under the driving of the motor can genetate strong impact force which make blow bars crush stone material into small pieces. Then the crushed material would be thrown by hammers towards, which makes another crushing …
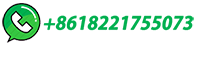
Construction Working and Maintenance of Crushers …
crusher consists of a heavy cast-iron, or steel, shell/frame which includes in its lower part an actuating mechanism (eccentric and driving gears), and in its upper part a cone shaped crushing chamber, lined with wear resisting plates (concaves). Construction detail and working of the crusher is as under.
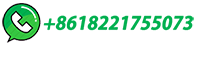
Cone crusher basics in 4 minutes
The basic principle is straightforward: the material to be crushed (the feed), drops into the crushing chamber. The mantle is a moving part that gyrates in an eccentric motion. That is, it doesn't remain completely centred – it swings …
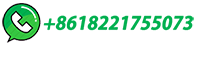
Introduction to Jaw Crushers: Understanding the …
Working Principles of Jaw Crushers: Crushing 101 Understanding the working principles of jaw crushers is pivotal to appreciating their efficiency. The primary steps in the crushing process include ...
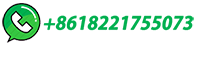
A Detailed Overview of Cone Crushers and What …
In this Cone Crusher article we want to educate you about what to consider when purchasing a cone crusher. It also will inform and educate you if you are a current owner or operator of a Cone Crusher. If you have a good …
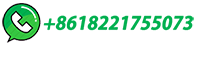
What is the role of 'jaw crusher' in the construction industry
Jaw Crusher Working Principle: Unlocking the Secrets of Efficiency. Jaw crushers are robust pieces of equipment that utilize mechanical pressure to crush rocks and minerals, offering several benefits in the construction and mining industries. Understanding their working principle sheds light on why they are essential assets in various projects.
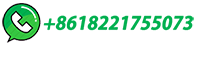
How does an impact crusher work? | RUBBLE MASTER
There are 2 main types impact crushers - horizontal shaft impact (HSI) crushers and vertical shaft impact (VSI) crushers. Horizontal Shaft Impactor (HSI) The horizontal shaft impactors are the most common impactor type that can be used in recycling, primary and secondary crushing applications. This type impactor will take reasonable size pieces ...
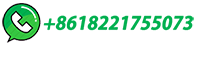
Crushing Principles of Mechanical Crushing
Optimization of a Final Crushing Stage. . Optimization of one parameter (CSS) can be done by sampling and analysis The invested time and lost production will quickly be repaid by …
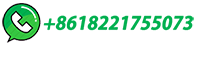
How Does a Cone Crusher Work and What is It?
Ideal for Secondary and Tertiary Crushing Stages: Because of their high reduction ratio and precise control over the product size, cone crushers work particularly well in the secondary and tertiary stages of crushing. For example, in a multi-stage crushing operation, a primary jaw crusher might reduce ore from a 1-meter size to 100mm, and then ...
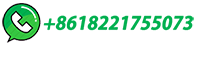
The Ultimate Guide to Jaw Crushing Machines: Types
Working Principles of Jaw Crushers. Jaw crushers are used to crush and reduce the size of various materials, including rock and ore. They work by using compressive force to break down the materials. Understanding the working principles of jaw crushers is important for ensuring that you choose the right crusher for your specific needs.
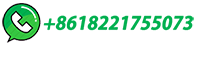
Stone Crushers: A Technical Review on Significant Part of …
Crushers are one of the essential quarrying machines used in foresaid industries which are generally used to reduce the size of large size rocks into small stones, sand dust and gravels. …
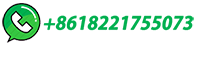
4 Types of Stone Crushers' Maintenance and …
Horizontal Shaft Impact crusher (HSI) Impact crusher working animation The working principle of impact crusher is that the spinning rotor under the driving of the motor can genetate strong impact force which make …
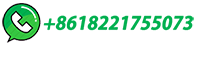
Working Principle of Cone Crushers
Cone crushers derive their name from their conical design. Essentially, cone crushers have a cylindrical body with a conical head designed to compress and crush materials within. This head rotates thanks to an eccentric shaft, allowing …
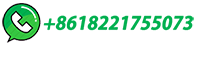
Crushers: Breaking Down the History of these Machines
Blake's crusher was announced in 1857 and patented in 1858. Perhaps surprisingly, the same basic design is still in use today for rock crushers. In the years following the design of the Blake Jaw Crusher, another type of crusher was designed. A gyratory crusher was patented by Philetus W. Gates in 1881.
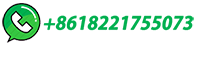
What Are the Differences Between The 7 Types of Crushers?
Jaw crusher needs to work together with feeding equipment to complement the crushing process. You can see that the granite material is reduced by the compressive force generated by two jaw dies. When the size of the material is smaller than that of discharging port, the final product will fall out of the bottom and be sent by the conveyor belt ...
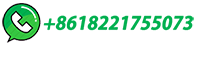
Chapter 4 The Principles of Single-Particle Crushing
However, in crushers only those principles are used, which introduce the load by the working surfaces (Fig. 11). The application of a certain loading case depends on the material and its behaviour. Since predominantly brittle materials are comminuted in crushers mainly three loading cases are only used. Download : Download full-size image; Fig. 11.
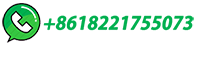
Jaw Crusher Working Principle – StudiousGuy
2. Both the structure and working of a jaw crusher are quite simple. 3. The product size is quite small and can range up to millimetres. 4. Repair and maintenance of a jaw crusher are convenient and easy. 5. The reliability of a jaw crusher is significantly high. 6. The broken parts of the jaw crusher are easy to replace. Disadvantages of a Jaw ...
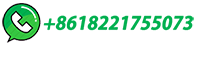