Comparative Analysis of Cement Production Methods …
Manufacturing cement has a major impact on climate change, resource depletion, and pollution. Selecting sustainable cement alternatives is vital but entails difficult trade-offs between numerous variables. The objective of this study is to determine the most environmentally beneficial method of cement manufacturing by employing an integrated life cycle assessment …
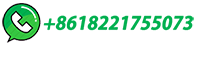
Sustainable Waste Management: A Case Study of …
total production. Cement plants are an essential part of India's industrial landscape and are increasingly important partners in innovative waste management solutions, called co-processing. Co-processing waste in this way consists of using both the calorific potential to heat the kiln and the material component from the fuel ash as a raw ...
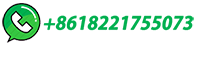
New Green Cement Production Method Could Bring …
By combining steel and cement recycling into an integrated process, researchers say they can turn demolished buildings into fresh sidewalk. They're testing at scale on Friday.
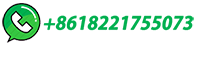
Raw materials used for Cement Production
In cement raw materials the lime component is generally represented up to an amount of 76-80 0/o. Therefore, the chemical and physical properties of this component are of decisive influence, when it comes to selecting a method of cement manufacturing as well as the type of production machinery. Marl
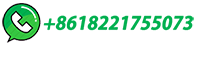
Cement: Applications, Manufacturing Process, …
Hydrophobic Cement. MAnufacturers produce hydrophobic cement by combining water-repelling compounds. It has great workability and strength. Furthermore, it repels water and remains unaffected throughout the monsoon …
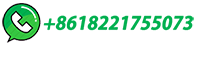
Full article: Manufacturing of building materials using …
1. Introduction. Bricks are utilised as construction materials worldwide (Phonphuak and Chindaprasirt Citation 2018).Most of these bricks are formulated with a significant amount of cement, and the production process and transportation of cement often contribute to the CO2 emissions of cement (He et al. Citation 2019; Nie et al. Citation 2022). ...
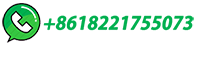
Cement recycling method could help solve one of the …
Eventually, this method could produce zero emission cement, if the EAF was powered by renewable energy. "We held a series of workshops with members of the construction industry on how we could reduce emissions from the sector," said Professor Julian Allwood from Cambridge's Department of Engineering, who led the research. "Lots of great ideas ...
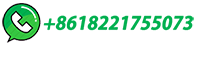
Basics of mineral resources for cement production
The actual production of cement-grade limestone in different states, of course, follows the demand pattern of the cement industry, which has been showing an increasing trend. It is tentatively presumed that about 1.5 tons of limestone are required to produce 1 ton of plain Portland cement, and about 0.8 tons of limestone for every ton of ...
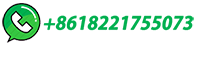
3D of concrete structures using the selective binding method …
3D (3DP) is a promising production method to minimize the costs of bionic-optimized material-saving structures. The investigated 3DP method "selective binding" generates a concrete ...
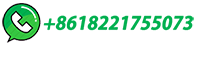
Electric recycling of Portland cement at scale | Nature
Cement production causes 7.5% of global anthropogenic CO2 emissions, arising from limestone decarbonation and fossil-fuel combustion1–3. Current decarbonation strategies include substituting ...
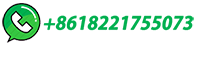
Projecting future carbon emissions from cement production …
Global cement emission patterns. Global emissions from cement production reached 2059 Mt CO 2 in 2018, where energy- and process-related emissions account for 34% and 66% respectively. Developed ...
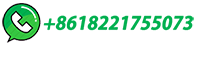
Raw materials used for Cement Production
In cement raw materials the lime component is generally represented up to an amount of 76-80 0/o. Therefore, the chemical and physical properties of this component are of decisive influence, when it comes to …
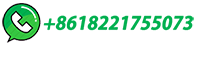
Explore Raw Material Used For Cement Production …
The production of raw cement involves the extraction and procurement of raw materials like limestone and clay or iron ore. These materials are then crushed and finely ground to form the raw mix. The raw mix is then subjected to high …
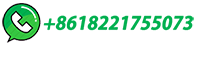
Applications of Cement
There are two methods for paving with concrete. The Slipform Method. In slipform paving, a machine rides on treads over the area to be paved—similar to a train moving on tracks. Fresh concrete is deposited in front of the paving machine, which then spreads, shapes, consolidates, screeds, and float-finishes the concrete in one continuous ...
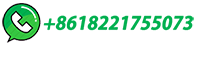
New Chemistry, Less Energy Could Yield Greener …
A One-Two Climate Punch. The problem lies in cement's chemistry, which is a sort of double-whammy of CO2 production. To turn Portland cement's key ingredient, calcium carbonate—found in ...
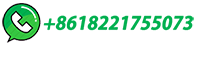
The four major costs associated with cement production
It primarily consists of silica, alumina and iron. As per the BIS standard for PPC cement, fly ash can account for 10-25 per cent of the cement mass, while the BIS standard for slag cement (PBFSC) allows slag to comprise 25-65 per cent of the cement mass. About 32 per cent of fly ash is used in the cement industry.
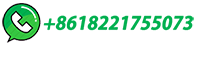
Manufacture of Cement- Materials and Manufacturing …
The major raw materials used in the manufacture of cement are Calcium, Silicon, Iron and Aluminum. These minerals are used in different form as per the availability of the minerals. Table shows the raw materials for Portland cement manufacture The mixing procedure of the manufacture of cement is done in 2 methods, Dry process; Wet process; a ...
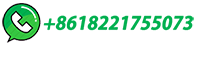
Gypsum Mining Method & Cost
Lime and hydraulic cement plasters compete to a limited extent with gypsum in the plaster field. Lime is used today in construction, chiefly as an ingredient in the finish coat over gypsum-plaster base coats. ... This method …
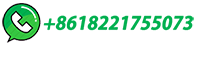
(PDF) REVIEW OF SELECTED POZZOLANAS FOR CONCRETE PRODUCTION …
Cement being a conventional binder in concreting undergoes hydration reaction producing lime as one of its by-products. This causes expansion thereby predisposing the composite to disintegration ...
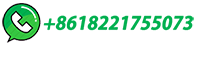
I pioneered a method to study cement using a particle …
The world makes four billion tonnes of Portland cement, the main ingredient of concrete, every year. This has an enormous carbon footprint — up to 8% of humanity's yearly production of CO 2 ...
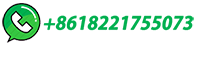
Everything about Cement Production
Process control, constant monitoring of cement production, and analysis of the data is needed to help ensure quality products reach the customer. In addition, proper analysis coupled with actions taken as a result of the data, …
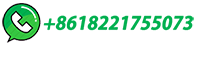
Methods for Production of High-Strength Concrete [PDF]
🕑 Reading time: 1 minute There are many methods through which high-strength concrete can be produced. Some of the widely known methods and techniques are- re-vibration, the use of admixtures, high-speed slurry mixing, prevention of cracks, Sulphur impregnation or Sulphur filling, use of cementitious aggregates, and seeding.
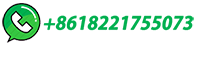
An Insight into the Chemistry of Cement—A Review
Cement is a hydraulic binder; it consists of a finely ground inorganic material which forms a paste when mixed with water, is able to set and harden because of numerous exothermic hydration reactions (and processes), and is thus capable of binding fragments of solid matter to form a compact whole solid [1,2,3].After hardening, cement retains its strength and …
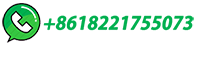
New approach suggests path to emissions-free …
Former postdoc Leah Ellis speaks with GBH All Things Considered host Arun Rath about Sublime Systems, an MIT startup she co-founded that aims to produce carbon-free cement to combat climate …
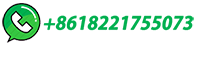
Binding mechanisms of radionuclides to cement
The most important reactions of cement with waste are those which lead to binding [2], i.e. a chemical reaction. The nature of the binding forces in a cement matrix is species specific, so it is difficult to produce a general description. Many species also form one or more solubility-limiting phases by reaction with cement components.
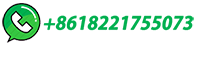
Deep decarbonisation of industry: The cement sector
2017, equivalent to a reduction in cement per capita from 0.5 to 0.3 tonnes per person (3). The CO 2 intensity of cement production over that period has improved by about 7% (0.6t of CO 2 emitted per tonne of cement in 2017) (2). By 2050, cement production in the EU is expected to remain below pre-2010 levels, ranging between 165Mt
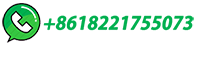
India's cement industry
India's cement production capacity In 2022, India's cement production amounted to an estimated 370 million metric tons, which accounted for a nine percent share of global cement production that year.
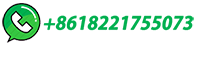
Digitalisation drives productivity in cement production
Cement producers are adopting Industry 4.0 across the flowsheet, taking advantage of digital solutions not only to support equipment availability, but also to reduce fuel consumption, increase production, improve product quality and save energy. ??igital technologies are having a major impact on cement production. Leading cement producers …
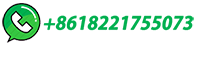
From raw materials to cement
Cement grinding Loading and shipping Quality control and Building on sustainability environmental responsibility HeidelbergCement Headquarters Berliner Strasse 6 69120 …
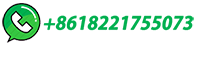