Jaw Crushers
Jaw crushers are the workhorse of the crushing industry for mining, construction, and demolition recycling. Mt. Baker Mining and Metals' jaw crushers are industrial grade, continuous duty machines. ... They take large pieces of rock, ore, concrete, or other materials, and crush them down to smaller sizes, for further processing in a ball mill ...
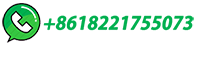
Jaw Crushers Manufacturer in India
Jaw Crushers. Designed to crush ROM feed material for demanding quarrying, mining, and demolition purposes. With their unique Elliptical motion of the swing jaw Crushers, ensure highly efficient production rates at any setting. This jaw motion also reduces the common scrubbing action found in single-toggle jaw crushers. These crushers are ...
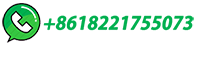
Jaw Crushers
AGGRETEK Jaw Crushers are designed for applications where cost-efficient primary reduction of hard, abrasive materials is concerned. Representing the highest technical and manufacturing knowledge, our heavy duty crushers match the most arduous crushing conditions encountered.
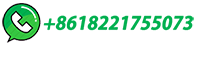
Jaw Crusher Explained
How Jaw Crushers Work. A jaw crusher uses compressive force for breaking ore pieces. Compressive force is applied by two jaws (dies), one of the crusher jaws is stationary (fixed jaw) whilst the other is moving (swing jaw). Material is fed into the top feed opening (gape) and gradually moves downwards towards the lower discharge outlet.
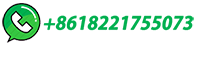
(PDF) DESIGN AND OPERATIONS CHALLENGES OF A SINGLE TOGGLE JAW …
A review on the design and operations challenges of a single toggle jaw crusher is presented. Strength and fracture toughness of the material to be crushed are intrinsic properties that determine ...
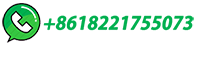
Jaw Plates: Everything You Should Know | Crusher Wear Parts
Different jaw crushers have different requirements for jaw plate shapes, sizes, and mounting methods. ... To minimize jaw plate wear, it is important to choose the correct type of jaw plate material, operate the crusher within the recommended parameters, and ensure proper feeding and alignment. Regular maintenance and inspection can also help ...
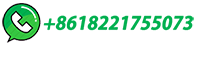
Crushers : VIRIDIS Engineering Sdn Bhd
Gyratory crushers are similar to cone crushers; they are frequently used in large-throughput primary crushing roles. Typically, they have larger capacities (up to 8000 tph) compared to jaw crushers (up to 1500 tph). Gyratory operate at a slower speed than cone crushers, typically in the range 85 to 105 rpm.
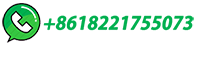
McLanahan | How To Size A Jaw Crusher
Jaw Crushers are primary crushers used in the first stage of the crushing process. They feature a V-shaped cavity (called the crushing chamber) that is formed by a moving piece of steel and a stationary piece of steel (called jaw dies). Material to be crushed enters the top of the chamber, where it is squeezed between the moving piece of steel ...
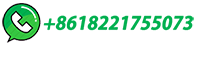
How Does a Jaw Crusher Work? A Simple Guide
In the operation of jaw crushers, challenges such as jaw plate wear significantly impair efficiency, necessitating timely replacement when discharge sizes increase. Blockages, often caused by sticky or wet materials, require consistent cleaning and …
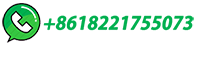
Intro to Aggregate Equipment: The Jaw Crusher
Jaw crushers, often called "crushers" for simplicity, are essential machines for handling aggregates. They are frequently used in everything from landscaping to the construction industry to take materials and grind them into …
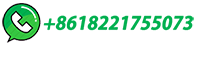
What is a Jaw Crusher and Selecting the Right One …
Advantages of a Jaw Crusher. Many factors make laboratory jaw crushers the optimum selection for effective and efficient primary crushing of hard, brittle, rock-like materials. Laboratory models are available with sample top sizes …
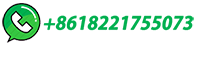
How Does a Jaw Crusher Work | Jaw Crusher
Cone crushers and jaw crushers both work by compression, reducing materials by squeezing them until they break apart. The benefit that cone crushers offer over jaw crushers is their ability to output a more cubical product similar to …
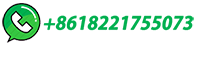
Selecting the right crusher for your operations
The harder the material, the longer it may take to crush. In addition to production times the degree of hardness will influence the specific crusher for the operation. JAW CRUSHERS Jaw crushers, which use a moveable jaw and a stationary plate designed to form a "V", crush material using compressive force.
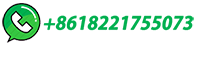
How it Works: Crushers, Grinding Mills and …
Material is reduced by crushers and grinders by fracturing, which takes place when the material is put under stress by the moving parts of the crushing or grinding equipment. Forces applied during the process may be …
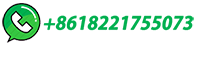
Crushing 101 – Different types of crushers for distinctive needs
All rock crushers can be classified as falling into two main groups. Compressive crushers that press the material until it breaks, and impact crushers that use the principle of quick impacts to crush the material. Jaw crushers, gyratory crushers and cone crushers operate according to the compression principle.
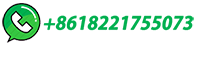
Primary Jaw Crusher – Everything You Need to …
A primary jaw crusher is a machine designed to reduce large rocks into smaller rocks, gravel, or rock dust. It is used in many industries, including mining, construction, and demolition, to crush materials such as …
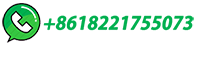
Jaw crushers, Stationary Jaw crusher series
Jaw crushers come with everything you need for plug-and-play primary crushing operations. Each jaw crusher comes with feed hopper, feed hopper interface, drive and subframe with v-belt guard and motor bracket, our unique …
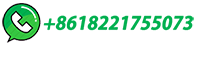
The Complete Guide to Jaw Plates: 10 Essential …
The material to be crushed is placed between these two jaws, and the movable jaw exerts force to compress and break the material. Jaw crushers are widely used for reducing the size of materials for further processing or …
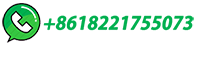
Crushers
Compressive crushers that press the material until it breaks, and impact crushers using the principle of quick impacts to crush the material. Jaw crushers, gyratory crushers, and cone operate according to the compression principle. Impact crushers, in turn, utilize the impact principle. Jaw crushers . Jaw crushers are mainly used as primary ...
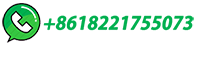
Jaw Crushers | RSE Projects
Jaw crushers are always at the for front of the sample preparation chain, pre-crushing all hard and brittle materials. They are primary used in the Laboratories and Pilot Plants operating under rough conditions for on-line quality control of raw materials. The jaw crushers are available in 4 different sizes as shown above.
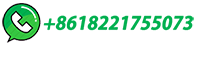
Laboratory Jaw Crusher – Labtech Group
Laboratory jaw crushers allow you to process hard materials in extremely small sizes. In this sense, the laboratory type jaw crusher allows product output between 0 and 5 mm. You can also achieve higher product output by adjusting the grain size. The laboratory jaw crusher is built to create a high user experience.
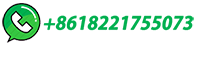
Jaw Crushers — Material Testing Expert
Jaw crushers are robust machines used for crushing rock, ore, and aggregate materials. These crushers are essential in mining and construction industries for reducing large rocks into smaller pieces, a critical step in mineral processing and construction projects. Mechanics of Jaw Crushers The f
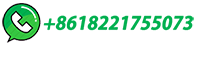
The Complete Guide to Primary Crushing, …
In jaw crushers, the material is fed into the crushing chamber and is crushed between a fixed jaw and a movable jaw. Gyratory crushers work by crushing materials between a mantle and a concave, while impact …
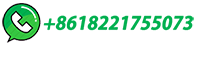
Pioneer® Jaw Crushers
The Pioneer ® Series of jaw crushers represents the very latest in jaw crusher technology.. Engineered to be the highest-capacity jaw crusher on the market, the Pioneer ® Jaw Crusher will deliver up to 25 percent more tons per hour than comparable jaw crushers. Pair that with heavy-duty flywheels for reduced horsepower requirements and class-leading stroke for higher …
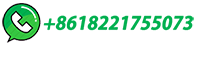
Our Range of ® Jaw Crushers |
The ® CTHT Series is often used to process recycled materials and slag waste including concrete and demolition (C&D) waste. In general, jaw crushers are most effective when working with dry feed materials as any moisture in the feed can increase wear inside the crusher, reducing overall throughput and tonnage.
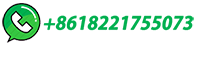
What Type of Crusher Is Best for Primary Crushing?
Gyratory Crushers typically have a higher capital cost and require a large housing structure that can become a significant engineering investment. Jaw Crushers. Jaw Crushers are another excellent choice for primary …
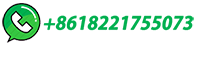
® C Series™ jaw crushers
® C Series™ jaw crushers have proven to be reliable and productive in thousands of mining, quarrying, recycling and industrial applications with over 12,000 jaw crusher installations since 1975. Developed to crush the hardest …
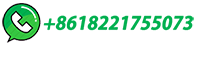
What Is a Jaw Crusher? Here's How It Works
Jaw crushers are so powerful that they've earned the moniker "rock breakers" because of their brute force. All jaw crushers will have one fixed jaw and a moving one. These two form a V-shaped chamber, where the materials are fed. The movable jaw will move back and forth against the fixed one, compressing all materials in the space between ...
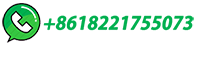
Jaw crusher EB | FL
For example, the patented swing jaw and front wall design absorb load peaks during operations. In our Pro series, we offer the following models (see more details below) Jaw Crusher EB 20-15 Pro with a capacity range of 600 – 1,600 tph; Jaw Crusher EB 16-12 Pro with a capacity range of 400 – 1,200 tph
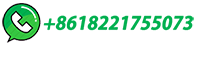
The Ultimate Guide to Jaw Crushing Machines: Types
A Guide to Types of Jaw Crushers for Crushing Rocks and …
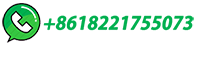