Direct Reduced Iron and its Production Processes – …
Iron ore is used mostly in pellet and/or lumpy form. Oxygen (O2) is removed from the iron ore by chemical reactions based on H2 and CO for the production of highly metalized DRI. In the direct reduction process, the solid metallic iron (Fe) is obtained directly from solid iron ore without subjecting the ore or the metal to fusion.
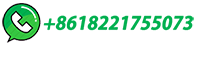
Top 6 Steps Of Iron Ore Processing
Visit our Australian Mining Product and Services to see what our professionals are equipped with to help you in your processing iron ore journey or what other services we can offer. Alternatively, call us on 1300 241 620 to speak to our experts today and learn all about the mining iron ore process. Types Of Iron Ore In Australia
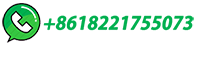
Iron Ore Processing Improvements through Process …
He also presented magnetic separator and hydrocyclone model structures compatible with the type of data produced by the liberation model. ... some modifications in plant flow sheets and …
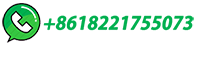
Ore Processing | Multotec
Iron ore processing. For iron ore extraction, the iron ore processing plant receives ROM where it undergoes crushing and subsequent screening on a grizzly screen. It is then sized and above cut point ore sent for further crushing and additional sizing; Coarse material has tramp removed via an overbelt magnet and into a DMS drum
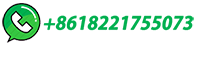
Iron Processing | Equipment, Process Flow, Cases
The iron-rich ore that can be directly into the furnace in China only accounts for 2.6% of the total reserves. There are many types of lean iron ore, mainly magnetite, vanadium-titanium magnetite and hematite, as well as siderite, limonite, etc.
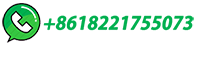
Revolutionising iron ore processing
's SuperStack technology has helped redefine the way iron ore beneficiation plants operate. In the dynamic world of mining, Corporation has become synonymous with innovation.
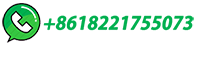
Mineral Processing Flowsheets
The Mineral Processing Flowsheets shown on the following pages are based on actual data obtained from successful operating plants. Metallurgical data are shown in these flowsheets which incorporate Crushers, Grinding Mills, Flotation Machines, Unit Flotation Cells, and Selective Mineral Jigs as well as other standard milling equipment. The Flotation Machine, …
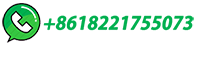
Copper Mining and Processing: Processing Copper Ores
Copper processing is a complicated process that begins with mining of the ore (less than 1% copper) and ends with sheets of 99.99% pure copper called cathodes, which will ultimately be made into products for everyday use.The most common types of ore, copper oxide and copper sulfide, undergo two different processes, hydrometallurgy and pyrometallurgy, respectively, …
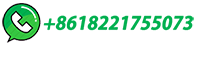
Crushing Plant Design and Layout Considerations
The life of the mine is a key element in the design of any crushing plant. Short-term mine lives (three to eight years) require a very careful approach to design, layout and construction. Since …
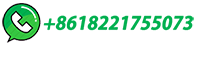
6 Aspects Should Be Considered in Design of Iron Ore Processing Plant
The design of an iron ore processing plant is a complex process involving multiple considerations. The following are the general steps and key points that should be followed when designing an iron ore concentrator, including resource assessment, process design, equipment selection and configuration, environment and resources, infrastructure …
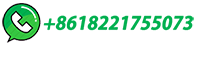
The six main steps of iron ore processing
Six steps to process iron ore. 1. Screening. We recommend that you begin by screening the iron ore to separate fine particles below the crusher's CSS before the crushing stage. A static …
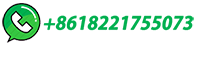
Processing Plant Flowsheet Design | SRK Consulting
Processing Plant Flowsheet Design. The foundation for superior process design is sound ore deposit knowledge and comprehensive testwork. Our metallurgists are experienced in …
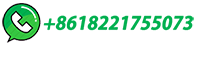
The Beginner's Guide to Mica Processing | Mining Pedia
Mica is a common silicate mineral with the chemical formula KAl2(AlSi3O10)(OH)2 and has a layered structure that can be divided into thin sheets. Mica has a wide range of applications in both mineralogy and industry. This article will describe the properties of mica, its application areas, the separation process and the issues that need attention during the …
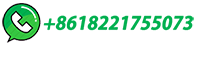
Chrome Ore Process Plant
The mainly process of chrome ore processing is gravity separation.Sometimes low intensity magnetic separation or high-intensity magnetic separation will be used to deal with the chrome concentrate for a second processing to improve the grade of the chrome. Also some ores treated by flotation, but the gravity separation is still the main processing way for chrome ores.
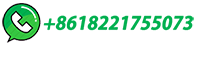
Dry beneficiation of iron ore
Falling prices for iron ore with lower quality than 60 % Fe have led increasingly to the design of iron ore beneficiation lines. General problems of water scarcity and risks with tailings dams have led to the focus shifting to dry beneficiation technologies. In the following article, current developments are examined and case studies referenced.
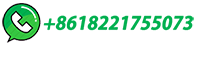
240TPH Iron Ore Processing Plant in Pakistan
240TPH Iron Ore Processing Plant in Pakistan ... Iron Ore Processing Plant Solutions & Flow Design. Talk To An Expert. Main equipment. Equipment name: Model: Power(kw) Qty: Vibrating feeder: 590*1100: 22: 1: ... Processing Mineral Types . Processing Capacity . Additional Infomation . Send Message.
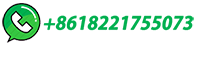
Iron Ore Processing | Home
Narvik is situated at the Ofotfjord, north of the Arctic Circle, and has an average annual temperature of around 4° C. Thanks to these temperatures, which are influenced by the Gulf Stream, the fjord remains free of ice almost all year round.This is where the processing plant of Scandinavia's biggest iron ore producer is located, with a facility for direct loading of iron ore …
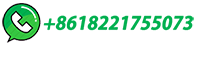
Mineral Processing
VI The Mineral Processing Plant. Most mineral processing plants are represented by the flow sheet shown in Fig. 11. Simpler operations, such as a quarry producing aggregate, would involve only the initial stages of size reduction. Conversely, a more complex plant, producing a number of concentrates, requires a series of concentrating circuits.
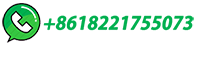
Modeling and simulation for design of iron ore processing …
Basic purpose of this model is to use simulation for efficient plant design and help in minimizing risk at the very initial stage of project. Feed to the plant is Hematite iron ore …
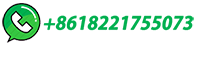
Iron Ore production in the Pilbara
Iron Ore production in the Pilbara Activities involved in finding, mining and processing iron ore at our Pilbara operations have been simplified in the following diagram. Rio Tinto operates 11 iron ore mines in the Pilbara and the specific sequence of activities varies from mine to mine. Excellence in planning, scheduling and quality control
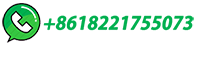
Various Types Of Iron Ore Beneficiation Processes
The beneficiation of various types of iron ore is a complex process that requires careful analysis and planning. Whether it is hematite, magnetite, or any other iron ore, implementing effective beneficiation technology can significantly improve the economic viability of a mining operation.
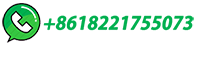
Characterization and Beneficiation of Dry Iron Ore …
fine ore having size below 8 –10 mm. Dry processing of iron ore is popular for treating hard massive hematitic ores; however, fines generated during processing of goethite-rich mineral cause significant quantity loss of iron values in rejects and make the process inefficient. During dry processing of iron ore in
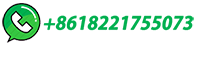
Manganese Ore Processing
The problem involved in Manganese Ore Processing deals with the production of acceptable specification grades of manganese concentrates at a maximum recovery of the total manganese from ores having variable characteristics. The flowsheet provides for both gravity and flotation with a maximum recovery of the manganese values in a coarse size in the most …
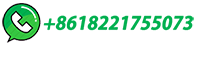
World leader in fine iron ore beneficiation
Quebec Iron Ore, Canada Bloom Lake is one of Canada's long‑life iron ore mines and a major supplier of high quality iron ore to global markets. Mineral Technologies was awarded the CAD$40 million circuit upgrade project in 2016. The operational focus was to optimise the separation circuit to recover high grade 66% Fe iron concentrate.
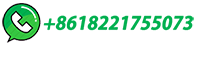
Hematite Processing by Flotation
Direct shipping of high grade iron ore, because of depletion or partial depletion of reserves, or high costs of operation has forced operators to use some means of beneficiation to produce an acceptable product with the lower grade iron ore reserves. Deposits of comparatively lower grade iron ore that remain relatively untouched or by-passed, are ...
Lithium Ore Flotation Plant
The Pineer froth flotation process enables sustainable and cost-effective spodumene/lithium ore recovery. Comes from one supplier, responsible for the whole package. Provides mechanical and performance guarantees for the entire plant machinery, with clear battery limits for engineering and implementation.
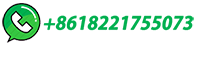
Simplified flow chart showing typical iron ore processing …
The findings suggest that iron ore tailings behave comparably to other types of tailings, indicating that inferences about tailings behavior made from other types of tailings can be reasonably ...
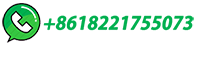
20TPH Alluvial & Rock Tin Ore Process Plant In Zimbabwe
20TPH Alluvial & Rock Tin Ore Process plant flow. ... and the final concentrate recovery rate must reach 95%. JXSC has developed a complete set of tin ore process plant equipment lines based on customer needs. The following is the specific process flow: ... This tin-ilmenite processing plant has a precise process design, low operating costs, no ...
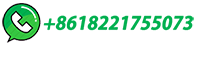
Eco-efficient and cost-effective process design for magnetite iron ore …
Supporting your operations, from plant design expertise to equipment, parts and services for every stage of your process. ... Eco-efficient and cost-effective process design for magnetite iron ore . Currently, the mining industry is facing several issues related to energy consumption so the optimized use of energy is an ever-increasing need ...
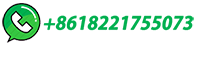
Iron Ore Processing, General | SpringerLink
The iron ore processing industry produces usable concentrations of iron-bearing material by removing nonferrous rock (gangue) from low-grade ore. In the United States, …
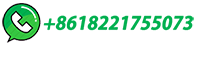
Simec Mining 950tph Iron Ore Beneficiation Wash Plant
Alumina levels range from 5.9% to 8.8% and are reduced to 2.8% after processing. The iron ore wash plant also removes clays from the feed material and the combined effect means the Fe content increases from between 43.4% and 52.7% in the feed to above 60% iron ore product, with a yield of up to 50%.
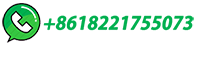