Direct reduction of iron to facilitate net zero emissions in the …
In the actual reduction process, the temperature distribution within the reactor is not uniform, and the reduction of iron ore is controlled by different kinetic processes (Huang et al., 2012). Hammam et al. (2021) compared the reduction pathways of iron ore using coal …
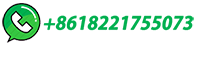
(PDF) Operation of Coal-Based Sponge Iron …
In this communication, OI methodology is used to study the operability characteristics of direct reduction of iron ore by coal in a rotary kiln using a rigorous process model.
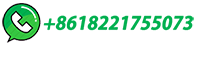
HYL Process for Direct Reduction of Iron Ore – IspatGuru
HYL process for direct reduction of iron ore was the fruition of research efforts begun by Hojalata y L.mina, S.A. (later known as Hylsa), at the beginning of the 1950s. After the initial evaluation of the concept, it was decided to install a process using a tunnel furnace and several runs were undertaken.
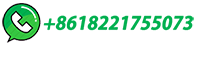
Direct-Reduced Iron
2.1 Midrex Process. Midrex is the most successful gas-based DR process; it is a continuous process. It is basically a countercurrent process where a hot and highly reducing gas (95vol.% of this gas mixture being hydrogen and carbon monoxide with a ratio of H 2:CO varying from 1.5 to 1.6) reduces lump iron ore or pellets to metallic iron as the metallic charge descends through …
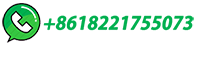
Application of coal-based direct reduction-magnetic separation process
FASTMET is a DR process that uses coal and iron ore. A layer of carbon composite agglomerates is created on the RHF hearth for reduction. ... Tunnel kiln coal-based direct reduction process flow chart. Hoganas's method has the characteristics of a high metallization rate, simple equipment, high mechanization degree and low initial investment ...
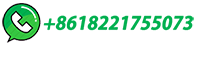
tunnel kiln design for reduction of ores
iron ore crusher building tunnel - seadoone.co.za. iron ore crusher building tunnel tunnel kiln design for reduction of ores,Process Crusher tunnel kiln design for reduction of ores 39 Views Read More; Get More Info tunnel technology of iron sponge making Tunnel Technology Of Iron Sponge Making iron ore crusher building tunnel Stone crushers China The mill is widely used …
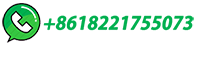
Direct Reduction of High-phosphorus Oolitic Hematite Ore …
DOI: 10.1016/S1006-706X(16)30134-0 Corpus ID: 138225940; Direct Reduction of High-phosphorus Oolitic Hematite Ore Based on Biomass Pyrolysis @article{Huang2016DirectRO, title={Direct Reduction of High-phosphorus Oolitic Hematite Ore Based on Biomass Pyrolysis}, author={Dongbo Huang and Yan-bing Zong and Ru-fei Wei and Wei-Jing Gao and Xiao-ming …
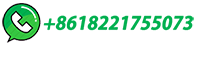
History, developments and processes of direct …
Processes for reduction of iron ores as alternative to the blast furnace were developed in a large number since the beginning of the 20th century [2]. One of the first development with a patent from the year 1918 was the Höganäs tunnel furnace process for fine ore reduction with carbon [3]. In the beginning of the
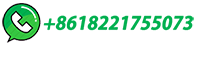
Direct Reduced Iron: Most Efficient Technologies for …
The effect of the coal properties on CO 2 emissions is not straightforward. Coal volatile matter contributes to the generation of heat and to the reducing conditions in the reactor (Chen et al. 2019).Highly volatile coals can generate more reductant gas than can be used in the reduction process (Park et al. 2017).This would lead to an unnecessary increase in the …
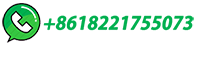
DIRECT IRON ORE REDUCTION
through a tunnel kiln and heated to about 2100°F, held for 12 to 36 hr, cooled, and emptied. This is the simplest and crudest of the direct reduction processes. Its great advantage lies in the …
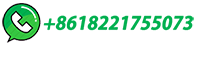
Production of Sponge Iron through Tunnel Kiln …
PDF | On Apr 1, 2010, Swaren Bedarkar and others published Production of Sponge Iron through Tunnel Kiln Process | Find, read and cite all the research you need on ResearchGate
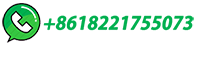
(PDF) Study on reduction of iron ore concentrate in rotary kiln …
The coulombs of cathorlic reduction can be measured when the high pure iron electrode passivated first in 0.5 mol L-1 H2SO4 for ten minutes was swept towards the cathodic direction, It is mainly ...
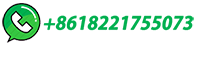
An innovative process for direct reduction of cold-bound
Successfully developed an innovative process of direct reduction of cold-bound pellets from iron ore concentrate with a coal-based rotary kiln, in comparison with the traditional direct reduction of fired oxide pellets in coal-based rotary kilns, possesses such advantages as: shorter flowsheet, lower capital investment, greater economic profit, good quality of direct …
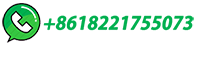
Direct Reduction Iron Process
Direct reduction · Metal recovery . Direct reduction ironmaking is a technological process of smelting ore into metallic iron under the condition of solid ore or solid–liquid mixed state [3]. Compared with traditional blast furnace ironmaking, direct reduction process has …
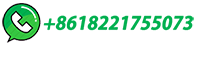
Argonne National Laboratory (ANL) | arpa-e.energy.gov
Argonne National Laboratory (ANL) will demonstrate a novel process for reducing iron ore to iron that reduces cost, eliminates CO2 emissions, and increases efficiency. ANL's process uses hydrogen (H2) plasma instead of carbon-rich coke or natural gas to reduce iron ore in a rotary kiln furnace, which will improve the thermodynamics and kinetics of iron ore …
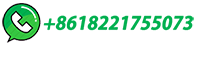
DIRECT IRON ORE REDUCTION
through a tunnel kiln and heated to about 2100°F, held for 12 to 36 hr, cooled, and emptied. This is the simplest and crudest of the direct reduction processes. Its great advantage lies in the reliability with which it will produce sponge iron from any ore. This is partly due to the fact that the ore is not moved during reduction. The
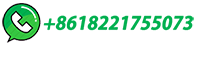
Iron Ore Reduction
As shown in Fig. 1 (Huang and Yuan, 2015), biomass is mixed with iron ore, and then charged into a high-temperature oxygen-deficient reactor where synthetic gases and metal iron can be produced simultaneously.The yield of syngas in the CBGIOR process was found to be much higher than that from biomass pyrolysis at 1173–1333 K, owing mainly to the large amount of …
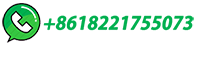
Reduction Efficiency of Iron Ore–Coal Composite Pellets in Tunnel Kiln
Anew process to produce iron nuggets at high temperature by direct reduction with basic synthetic iron ore coal briquette or pellet has been introduced, that is called Wcomet process in which the ...
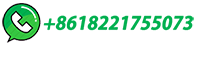
Direct reduced iron process
The reduction gases only dissolve oxygen from the iron ores. This causes the iron ores to crack on the surface. The appearance resembles a porous sponge, which is why the deoxidized and thus strongly ferrous iron …
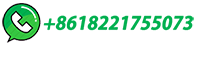
Chapter 1 Review of Sponge Iron Making Process …
Methods of producing low carbon wrought iron directly from the ore are known as direct reduction process. After the development of the blast furnace, ... 1930-1950s Saggers in Tunnel Kilns- Small Shaft Furnace- Rotary Kilns- Hogganas- Wiberg- Krupp & Lurgi- ... The term direct reduction of iron ore originates from the fact that the iron
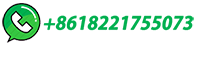
History, developments and processes of direct reduction …
Processes for reduction of iron ores as alternative to the blast furnace were developed in a large number since the beginning of the 20th century [2]. One of the first development with a patent …
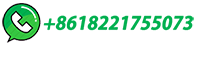
Ironmaking in Rotary Hearth Furnace – IspatGuru
The RHF is the process reactor which consists of a flat, refractory hearth rotating inside a stationary, circular tunnel kiln. Inside the RHF, direct reduction of iron ore or iron-bearing waste materials occurs, using coal as the reductant. ... In this process, the iron ore is reduced and melted, and the coal mixed in the raw material layer is ...
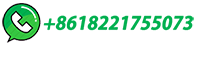
Sustainability Enhancement of the Coal Based Direct Reduction of Iron
1.1 The DRI Process. Sponge Iron or Direct Reduction Iron (DRI) refers to a porous metallic substance that is produced by the direct reduction of iron ore, where oxygen is removed from the iron oxide using coal or natural gas as reductants and dolomite as a desulphurizing agent . Raw materials are fed into the rotary Kiln by a conveyor to ...
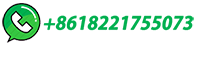
Direct reduction of iron to facilitate net zero
The global annual production of steel is approximately 2 billion tons, accounting for 8 % of the world's energy demand and 7 % of carbon dioxide (CO 2) emissions in the energy sector.Coal-based direct reduced iron (DRI) reduces CO 2 emissions by 38 % compared with traditional blast furnace–basic oxygen furnace (BF-BOF) ironmaking. Using a combination gas …
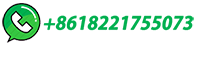
A review of ironmaking by direct reduction processes: …
The proposed iron ore reduction process therefore would be a potential to reduce iron directly using biomass with high efficiency and real environmental benefits. View Show abstract
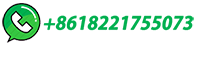
A review of ironmaking by direct reduction processes: …
Guo, D. et al. (2016) ‘Direct reduction of oxidized iron ore pellets using biomass syngas as the reducer’, Fuel Processing Technology. Elsevier B.V., 148, pp. 276â€"281. …
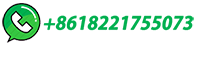
Prospects for Coal-based Direct Reduction Process
iron ore fines and pulverized coal. Once the agglomerates are heated, carbon monoxide is generated inside them, promoting the reduction of iron oxide. Thus, the reduction reaction proceeds 1975 1980 1985 1990 1995 2000 2005 World total Coal base 2008 (million ton) 17.6 68.5 70 60 50 40 30 20 10 0 Fig. 1 World DRI production by year 1)
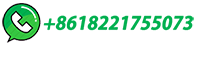
Research article Optimization of direct reduction in …
The direct reduction of iron in a tunnel kiln is a volumetric process in which raw material consumption is determined by the volumetric capacity of refractory crucibles. Non-coking coal …
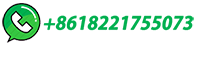
Direct reduction of iron to facilitate net zero emissions in …
Iron ore pellet production process. Iron ore, refined through ore-beneficiation techniques, yields iron-ore concentrate powder, which is directly utilized as the raw material in fluidized-bed reactors. ... Behavior of three non-coking coals from Iranian's deposits in simulated thermal regime of tunnel kiln direct reduction of iron. J. Anal ...
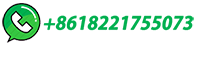
Effect of coal levels during direct reduction roasting of high
The length, height, and width of the tunnel kiln were 167, 5.5, and 2.34 m, respectively. This tunnel kiln was being used to produce direct reduction iron from iron scale at the same time. Mixed materials pass through three stages in the tunnel kiln: 12 h preheat; 12 h constant heat; and, 25 h cooling.
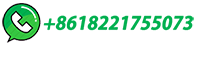