The future of flotation
The future of flotation. Woodgrove Technologies' staged flotation reactor (SFR) divides the flotation process into three chambers. Courtesy of Woodgrove Technologies. A s design criteria go, removing the froth layer from …
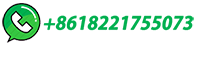
Flotation Guidebook
10.4 Mass of Solids in a Flotation Cell 41 10.5 Solids Mass and Water Calculation for Laboratory Flotation Tests 42 10.6 Reagent Usage Conversion (mL per minute to gram per tonne) 43 10.7 Residence Time 43 10.8 Laboratory Flotation Testing Tips 43 10.9 Standard Unit Conversions 45 Common Minerals and Properties 47 Particle Size Conversions 49
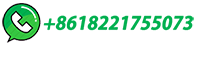
Review on advances in mineral processing technologies …
Mechanical and pneumatic flotation cells are the most widely used in mineral processing. Mechanical flotation cells utilise an impellor to agitate the slurry and produce turbulent regions for bubble particle attachment, whereas in pneumatic flotation cells pulp …
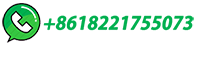
Flotation
Harness the power of experience. Flotation cells. Maintaining recovery and ensuring availability and sustainability while keeping costs under control is challenging. Our flotation solutions maximize your return on investment by …
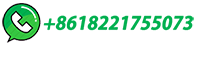
Flotation Processes: A Review
Flotation cell. Minerals2024, 14, 331 froth. Throughout the ß frothers, and activators are utilized to enhanc The e ßotation relies on the interaction of multiple factors, including a froth ßotation cell is shown in Figure 1, and a real photo from the Flotation cell. Figure 2. ßotation cells from the processing plant (photo taken by the ...
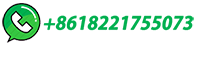
Flotation Processes: A Review
The effectiveness of flotation relies on the interaction of multiple factors, including particle characteristics, hydrodynamic conditions, and gas dispersion [2]. An example of a froth …
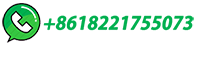
Enhancing flotation cells for increased sustainable production
The latest addition to Outotec's flotation equipment range is the Concorde Cell™, which sets a new benchmark in high intensity pneumatic flotation by recovering unachievable fine and ...
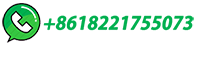
Different Types of Flotation Cells
Flotation is both a science and an art. It brings together many complex variables. Such basic factors as knowledge of mineral structure, chemical reagents, pH of mill water, pulp density, temperature, technical skills of the operator, the dependability of the flotation machine, as well as a host of other factors which affect the flotation of ... title="Different Types of …
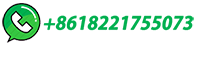
Froth Flotation for the 21st Century | E & MJ
's flagship product for flotation, the RCS flotation cell, is an all-purpose flotation machine suitable for applications including roughing, cleaning and scavenging. RCS cells use 's patented Deep Vane (DV) mechanism to …
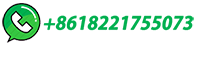
Digital twin of minerals processing operations for an …
The froth flotation process typically involves a series of multiple flotation cells arranged in a sequential manner. This configuration allows for a step-wise separation of valuable minerals from the ore, with each cell playing a specific role in the overall process [].The use of multiple cells in series enhances the efficiency of the flotation process by optimizing the …
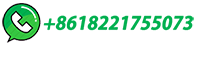
Minerals | Free Full-Text | The Challenges and Prospects of …
Flotation is a common mineral processing method used to upgrade copper sulfide ores; in this method, copper sulfide mineral particles are concentrated in froth, and associated gangue minerals are separated as tailings. However, a significant amount of copper is lost into tailings during the processing; therefore, tailings can be considered secondary resources or …
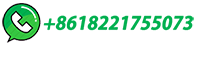
Flotation
How the data is used to determine flotation kinetics is a subject of a separate video. The key aspects are: the types and setup of the laboratory cell; sample to be tested, test conditions and; how the test is conducted. The standard laboratory cell and cell size for many decades has been the Denver D12 with 2.5 litre stainless steel cell.
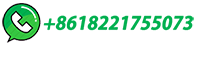
Flotation: The Past, Present and Future of Mineral Processing?
E&MJ explores the sustainability of a time-honored beneficiation technique . By Carly Leonida, European Editor. As we look to the future, the mining industry faces a myriad of challenges. While demand for metals like copper, cobalt, lithium and iron ore is projected to reach record highs by 2050, ore grades are decreasing, orebodies are becoming more complex, and fewer …
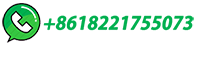
Winner's Profile
The RFC can be used in any flotation application ranging from rougher flotation to cleaning applications and across all mineral types. The high capacity nature of the technology allows for easy improvements. ... A plenum …
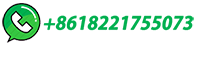
Flotation Innovations Increase Throughput, Recovery | E & MJ
Separately, FL reported the Smart Flotation upgrade is the best way for mines to optimize performance and transition into digital technologies. "It is the best way maximize recovery of valuable minerals, extend the equipment lifecycle, and increase availability and reliability of the equipment," Merrill said.
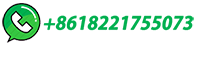
The future of flotation
Unfortunately, the conventional flotation cell achieves high recovery only in limited size ranges. For example, a sulfide ore might float very well at 90 to 120 microns, but not at 50 or 150 microns.
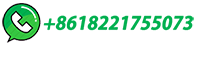
Flotation maestro: an audience with the inventor of the Jameson Cell
The accolades are an acknowledgement of Jameson's groundbreaking flotation technology, the Jameson Cell. The technology, which was made available in the late 1980s after 20 years of research, enables the mining industry to create billions of dollars of extra value by using bubbles to capture super-fine particles of less than a hair's breadth during mineral …
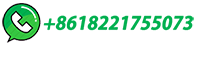
HydroFloat Flotation
The HydroFloat recovers particles +2x coarser than conventional flotation cells, which allows for a shift in the economic optimum grind size, and in turn increases profitability and improves environmental sustainability of mining projects. ... To meet society's needs for critical mineral resources, the mining industry must develop projects ...
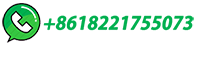
Gold Flotation
Best known of these are the Mineral Separation, the Fagergren, the Agitair, and the Massco-Fahrenwald. ... Ontario, have inserted a combination of flotation cell and hydraulic cone in their tube-mill classifier circuits. At the Mclntyre- Porcupine, according to J. J. Denny in E. and M. J., November, 1933, this cell is a 500 Sub-A type. The ...
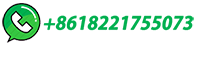
Froth Flotation
An obvious example is shown in Fig. 2, illustrating the conflicting hydrodynamic zones of best flotation performance for fine and coarse particles in a conventional flotation cell. Recovering those very fine or very large particles by flotation has become the main challenge in mineral processing and attracted much research effort today.
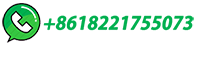
Minerals | Free Full-Text | A Review of Flotation …
Over the past few decades, the need to process more minerals while lowering capital costs has led to an increase in the size of flotation cells, e.g., 0.03 m3 to 1000 m3. However, this increase has created new challenges …
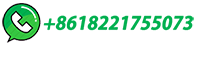
Flotation Cells
The flowsheet can be changed so that any cell can be used as a rougher, cleaner, or recleaner cell, making a simplified flowsheet with the best extraction of mineral values. The world-wide use of the Denver "Sub-A" …
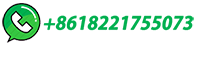
Wemco II Flotation Cell
WEMCO® II: The best in flotation just got better Over decades, original WEMCO flotation cells built their reputation on delivering the highest recovery. WEMCO II builds on the success of its predecessor by offering more recovery with the …
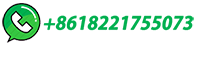
Coarse particle flotation: A review
Coarse particle flotation for early gangue rejection application has attracted considerable attention in the mineral industry. Since grinding units consume a significant amount of energy and sometimes stand as the most energy-consuming unit in the process (Curry et al., 2014, Jeswiet and Szekeres, 2016, Hassanzadeh, 2018), the early separation of gangue from …
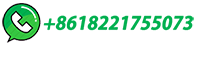
Flotation Cell
The use of power ultrasound in mining. L. Gaete-Garretón, in Power Ultrasonics, 2015 35.5.1 The flotation process. One of the most used processes to concentrate mineral from a mine is flotation. To perform a flotation process the mineral is finely ground (particle sizes between 50 and 150 μm), then the ground mineral is mixed with water in a container called a flotation cell.
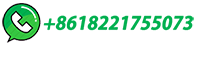
Flotation | Mineral Processing, Separation & Beneficiation
Flotation, in mineral processing, method used to separate and concentrate ores by altering their surfaces to a hydrophobic or hydrophilic condition—that is, the surfaces are either repelled or attracted by water. The flotation process was developed on a …
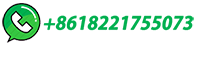
Winner's Profile
The REFLUX™ Flotation Cell (RFC™) combines several technologies to achieve superior flotation performance at a magnitude far beyond the capacity of existing flotation devices. This technology was developed by FLS in collaboration with Prof. Kevin Galvin and his team at the University of Newcastle, Australia who is also the inventor.
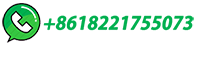
Minerals | Free Full-Text | Editorial for Special Issue "Design
Flotation is a significant and widely used processing technique, effectively separating valuable and gangue minerals. Mineral producers have long sought ways to consistently monitor and control the flotation process to ensure optimal conditions for effective mineral separation [].However, establishing such a sophisticated control system entails …
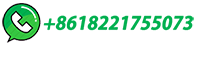
Technological assessments on recent developments in fine …
1. Introduction. Froth flotation was undoubtedly the most innovative and groundbreaking discovery for mining in the 19th century (Wills and Finch, 2015).Nevertheless, …
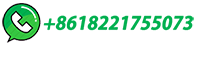
Mineral Flotation
Stawell gold mine in co-operation with Outotec Services completed a flotation circuit upgrade on time and on budget last year that, instead of the projected 3.5% improvement, resulted in an ...
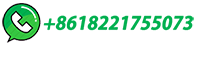