Iron Ore Processing Equipment
Pelletizing and Recovery. FEECO is an industry leader in custom agglomeration equipment and process solutions. We can provide individual pieces of equipment, as well as …
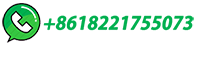
Multi-objective Optimization of Integrated Iron Ore Sintering Process
In the iron ore sintering process, it is desirable to maximize the productivity and quality of sinter while minimizing the fuel consumption for any given raw material (iron ore, flux and solid fuel) quality. However, given the complexity of the sintering process and the large number of manipulated variables, it is not practical for operators to identify …
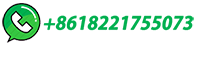
Iron processing
Iron ore sintering consists of heating a layer of fines until partial melting occurs and individual ore particles fuse together. For this purpose, a traveling-grate machine is …
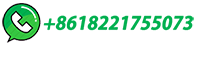
NextGen Pelletizing™
Iron ore pelletizing is crucial for the "green" future ... technology for iron ore pellet processing, which is based on over 60 years of experience and world-class R&D. This process produces pellets with excellent physical ... • Indurating machine • Pallet Cars • Digital Solutions • Burners (Standard, LowNOx) ...
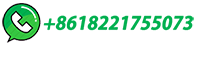
Iron Ore Beneficiation Plant Equipment For Mining Process
Iron ore is an essential iron-making material with a wide application. The iron ore processing plant usually adopts the magnetic separation method. The iron ore magnetic separation production line consists of iron ore beneficiation equipment, including crushing equipment, screening equipment, grinding and grading equipment, magnetic …
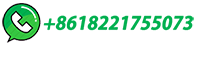
Iron processing
Iron processing - Smelting, Refining, Alloying: The primary objective of iron making is to release iron from chemical combination with oxygen, and, since the blast furnace is much the most efficient process, it receives the most attention here. Alternative methods known as direct reduction are used in over a score of countries, but less than 5 percent of iron …
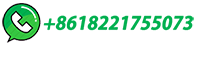
Optimal proportioning of iron ore in sintering process …
Proportioning is an important part of sintering, as it affects the cost of sintering and the quality of sintered ore. To address the problems posed by the complex raw material information and numerous constraints in the sintering process, a multi-objective optimisation model for sintering proportioning was established, which takes the …
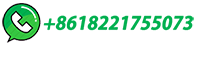
Reliable equipment for iron ore mines
For the large volumes of iron ore you produce every day, you need proven and reliable equipment to sustain or increase your production level and avoid unplanned stops.
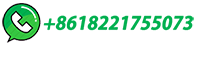
Steel Production
Even though equipment is improved and higher production rates can be achieved, the processes inside the blast furnace remain the same. The blast furnace uses coke, iron ore and limestone to produce pig iron. Coal traditionally has been a …
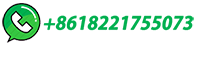
Advancing Iron Ore Beneficiation: Exploring Cutting-Edge
In the dynamic landscape of mining and metallurgy, the iron ore beneficiation process stands as a cornerstone, pivotal in transforming raw…
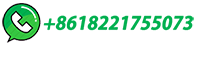
Wet High Intensity Magnetic Separation
WHIM is the short acronym for Wet High Intensity Magnetic Separation.. At present, most U.S. iron raw materials are produced from magnetic taconites, which are ground to a nominal minus 270 mesh (53 micrometers), beneficiated by wet low-intensity magnetic separation, and pelletized.
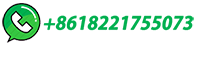
Iron Ore Pellet Size Analysis: A Machine Learning-Based …
In this article, an ensembled convolutional neural network (CNN)-based algorithm is proposed for iron ore pellet size analysis. A new customized CNN is ensembled along with VGG16, MobileNet, and ResNet50. The algorithm uses images captured from the inside area of a pelletizer disk to directly estimate the pellet size class instead of employing a …
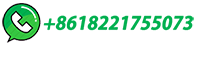
Rotary Scrubber
Our rotary scrubber is used for washing muddy and impurity ore before the beneficiation process, and it has dual efficient functions of washing and screening.
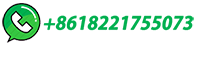
Iron Ore Processing
Iron ore is mainly used in the production of iron and steel. Natural iron ore needs to be processed through a series of processes such as crushing, grinding, magnetic …
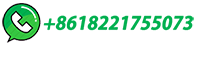
Iron Ore Pelletizing Process: An Overview | IntechOpen
The iron ore production has significantly expanded in recent years, owing to increasing steel demands in developing countries. However, the content of iron in ore deposits has deteriorated and low-grade iron ore has been processed. The fines resulting from the concentration process must be agglomerated for use in iron and steelmaking. …
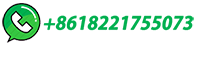
HBI production | International Iron Metallics Association
International Iron Metallics Association. The IIMA is dedicated to those involved in the ore-based metallics value chain - raw material supply, production and transformation, trading and distribution, transportation and logistics, technology and equipment.
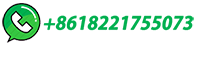
Iron ore | BHP
How is iron ore mined? From pit to port, our iron ore undergoes a series of processes before export. First, we explore the geology of the region to find the best iron ore prospects for our operations. Once the ideal site has been chosen, the ore is drilled and blasted. It is then transported to the primary crusher for processing.
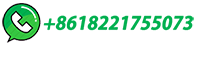
Iron Processing | Equipment, Process Flow, Cases
Iron processing description from its geology mineral property to how to extract mineral from rock and placer deposit, related processing plant flow chart and layout design.
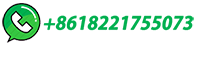
Iron Ore Processing, General
Iron Ore Processing, General 1 Introduction Iron is the world's most commonly used metal–steel, of which iron ore is the key ingredient, representing almost 95% of all metal used per year. It is used primarily in structural engineering applications and in maritime purposes, automobiles, and general industrial applications (machinery).
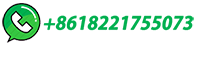
Mineral Processing Equipment
Driven by a global team of process engineers and metallurgical specialists, Multotec designs, builds, manufactures, installs and maintains equipment throughout the entire value chain of mineral processing plants across all commodity sectors, from diamonds to coal, gold, iron ore, platinum and phosphates.
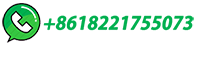
Iron Mining Process
At the processing plant, the taconite is crushed into very small pieces by rock crushing machines. The crushers keep crushing the rock until it is the size of a marble. The rock is mixed with water and ground in rotating mills until it is as fine as powder. Separation The iron ore is separated from the taconite using magnetism.
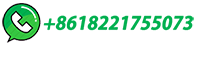
Iron processing
Iron processing - Smelting, Refining, Alloying: The primary objective of iron making is to release iron from chemical combination with oxygen, and, since the blast furnace is …
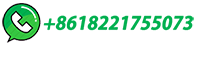
From Ore to Iron with Smelting and Direct Iron Reduction
Ironmaking is a critical step in producing high performance steel because high-quality raw materials reduce the time and energy to purify the iron to steel. On the …
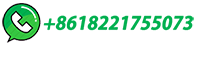
Open-Pit Mining | Method and Process | Epiroc US
In hard rock mining, much of the world's annual output of copper, gold and iron ore is won from open-pit operations. Other commodities produced from open-pit mining include diamonds, molybdenum, manganese, lead and zinc, uranium and a variety of industrial minerals, such as borates, talc and specialist clays.
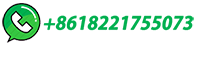
Wet High Intensity Magnetic Separators | Multotec
Wet High Intensity Magnetic Separators (WHIMS) from Multotec apply magnetism, matrix rotation and gravity to achieve para-magnetic materials separation. Applications include heavy minerals, ilmenite, manganese and iron ore (haematite) beneficiation; PGM upgrading as well as manganese recovery from slimes dams.
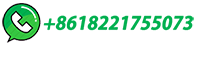
Iron ore pelletizing
This process generates iron ore filter cake which needs to be pelletized to be used in the steel making process. Also during the processing of high grade iron ores which don't need beneficiated, fines which are generated can be pelletized and used instead of being disposed of. Iron Ore Pellets are formed from beneficiated or run of mine iron ...
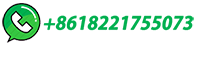
Ore processing (Mekanism)
Mekanism provides 4 tiers of systems to process ores and obtain two to five ingots from 1 ore. The complexity of the systems rises with each tier and at the higher tiers various secondary machines are required to produce consumables for the main ore processing line. The following page shows the layout of these systems as well as some in-game …
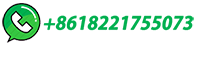
From Ore to Alloy: Navigating Ironmaking in Modern Steel …
At the heart of steel production lies the intricate process of ironmaking, where iron ore is transformed into molten iron and eventually alloyed to create various grades of steel. This article delves into the journey from ore to alloy, exploring the technologies, challenges, and innovations that shape modern ironmaking.
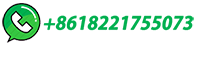
Ore Processing
Each tier use a specific machine to process the raw ore ( for direct ingots, dusts, clumps, shards or crystals ).Then the product is processed by the machines of the previous tiers. Ore processing flowchart (Mekanism v10)
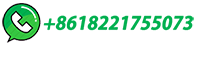
Introduction: Overview of the global iron ore industry
Learn about the global iron ore industry, its history, trends, challenges and opportunities in this comprehensive introduction chapter.
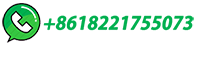