Wet High Intensity Magnetic Separator
Upgrading iron ore fines (10micron to 1mm) Recovery of fine iron ore from tailing streams Separation of ilmenite from heavy mineral sand concentrates to reduce downstream processing Removal of magnetic contaminants from slurried materials eg cassiterite, kaolin, silica, etc
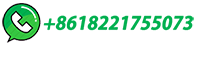
Energy analysis of the convective drying of iron ore fines
Drying operations in iron ore processing plants have a particularly high energy demand due to the massive solid flow rates employed in this industry. ... • Handling and drying of wet ...
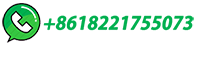
Iron Ore Processing FEASIBILITY OF PRODUCING …
2 Generally, the beneficiation of high/medium grade hematite iron ores in India includes dry circuit covering crushing, screening or wet circuit consisting of crushing, scrubbing, washing and classification [3- 4].
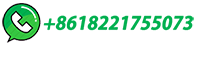
Simec Mining 950tph Iron Ore Beneficiation Wash Plant
950tph iron ore beneficiation wet processing project in South Australia. Learn more about this award-winning CDE and Simec Mining project.
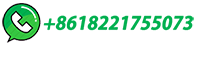
Liquefaction potential evaluation for iron ore fines based …
Liquefaction potential evaluation for iron ore fines based on a correlation between moisture content and cyclic strength ... w is the gravimetric moisture content defined as the ratio of the mass of water to the total mass of wet ore, ... The cyclic shear stress ratios were calculated at the same locations (The calculating process was …
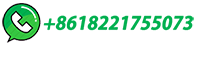
Ore, Rock & Aggregate Screening (Complete Guide)
A-Z Guide to Screening Ore, Rock & Aggregate A simple definition of a "screen" is a machine with surface(s) used to classify materials by size. Screening is defined as "The mechanical process which accomplishes a division of particles on the basis of size and their acceptance or rejection by a screening surface". Knowledge of …
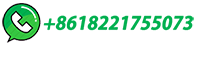
The use of filter aids on iron ore fines
A current trend amongst producers is the increase in dewatering of iron ore fines (<0.5 mm), due to an increase in wet beneficiation processes used to upgrade lower quality …
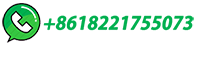
Modification of Wet Granulation Process During Iron Ore …
Sintering is the most extensively used and economic agglomeration process to prepare iron ore fines for blast furnace use. Granulation is the most critical factor controlling iron ore sintering process, as it improves sinter mix permeability. Currently, sinter plants are receiving significant proportion (up to 40%) of − 150 μm micro-fines in …
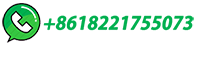
Iron ore beneficiation: an overview
Iron ore processing operating practices vary depending upon the the quality of iron ore deposit. For high-grade ore, dry- or wet processing can carried out and for …
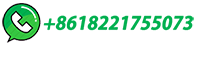
IRON ORE FINES
• Iron ore fines are a product of the screening of iron ore • They are used to produce sinter or pellets in the steel industry. INTRODUCTION ... a wet process, froth flotation, which leaves the ore in a wet state. BENEFICIATION The …
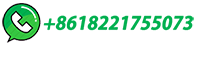
The effect of particle size on green pellet properties of iron ore fines
Iron ore pellet making process involves balling of green mix (containing iron ore fines, binder, limestone and coke) using rotating disk or drum to produce green pellets. ...
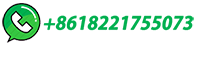
The use of filter aids on iron ore fines
A current trend amongst producers is the increase in dewatering of iron ore fines (<0.5 mm), due to an increase in wet beneficiation processes used to upgrade lower quality ore deposits, increased water content in orebodies located below the water table, and increasing focus on transportable moisture limits (TML). Vacuum filtration is commonly …
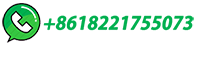
Advances in screening technology in the mining sector
3 Screening machines for iron ore and coal. The crushing and screening systems for iron ore processing vary widely, depending on whether a magnetite or hematite deposit is being mined. While good quality magnetite is now dry-processed, hematite from deposits below the water line requires wet processing due to sticky quartz and clay contaminations.
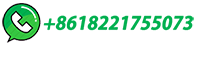
Iron Ore Processing, General | SpringerLink
Iron ore processing has become an integral part of ironmaking and steelmaking. ... between various minerals to achieve a separation and is normally a wet process although examples of dry gravity separators exist. ... Sintering involves the heating of fine iron ore with flux and coke fines or coal to produce a semi-molten mass that …
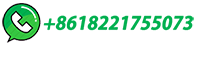
POTENTIAL APPLICATIONS FOR DRY BENEFICIATION …
upgrading of fine iron ore. STET has performed exploratory studies with several iron ores and experimental results to date have demonstrated that low-grade iron ore fines can be upgraded by means of STET tribo-electrostatic belt separator. The STET dry electrostatic separation process offers many advantages over traditional wet processing
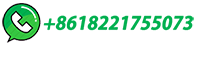
Improved dewatering of iron ore fines by the use of …
The role of chemical reagents to reduce moisture in iron ore fines is explored in the present work which includes ionic and non-ionic surfactants. The…
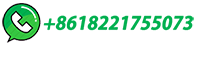
Evaluation of VSK separation in the classification of two …
matrix generally demands wet processing techniques for achieving efficient separation. However, it suffers from the ... Extensive research has been conducted on the application of wet processing techniques for treating iron ore fines, using wet high-intensity magnetic separators, spirals, flotation, and selective flocculation [5–9]. However ...
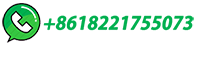
Development of processing technology for beneficiation of lean iron ore
PDF | On Jan 1, 2011, A. Vidyadhar and others published Development of processing technology for beneficiation of lean iron ore fines from Goa | Find, read and cite all the research you need on ...
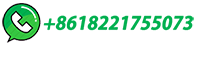
Characterization and Beneficiation of Dry Iron Ore Processing …
Characterization and beneficiation of dry iron ore processing plant reject fines of Khondbond region, India, was investigated. Different characterization techniques viz. size analysis, size-wise chemical and density analysis, X-ray diffraction analysis, sink-float analysis, thermo gravimetric analysis, scanning electron microscopy, and …
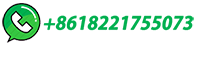
Recovery of Iron Ore Fines and Ultrafines from Tailings …
The most widely used process for the recovery of these valuable fine and ultra-fine hematite iron particles is the wet high-intensity magnetic separation technique, originally developed by Dr Jones over 55 years ago.
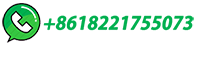
Iron Ore Pelletizing Process: An Overview
However, the content of iron in ore deposits has deteriorated and low-grade iron ore has been processed. The fines resulting from the concentration process must …
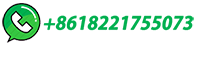
Recovery of Iron Ore Fines and Ultrafines from Tailings byUsing Wet
In addition, consideration is given to dewatering of iron ore product and tailings.Two types of tailings have been identified for processing. Firstly, tailings that have already been deposited in a tailings storage facility, and secondly, live tailings streams from an existing wet iron ore beneficiation plant.
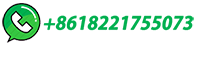
SCIENTIFIC PAPER ENERGY ANALYSIS OF THE …
Drying operations in iron ore processing plants have a particularly high energy demand due to the ... • Handling and drying of wet agglomerates of iron ore fines in a fixed bed;
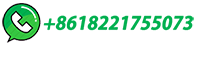
How fines dry magnetic separation could solve mining's …
Storing tailings has long been an issue for the mining industry, but fines dry magnetic separation technology offers a safer, less water-intensive approach.
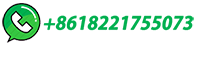
Wet High-Intensity Magnetic Separators (WHIMS) for Recovering Iron …
Iron ore tailings dams at Quadrilátero Ferrífero, Minas Gerais (MG), Brazil, are full and present significant risks. The material contains approximately 30% of the iron, and recovering this iron is...
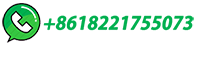
Characterization and Beneficiation of Dry Iron Ore …
composition of iron ore fines. Co mpositionally, Indian iron ore fines contain hematite and goeth ite as major iron bearing min-erals. Gangue minerals are mostly alumina-silicate which re-mains inside the pores of goethite minerals in ultrafine size. However, some studies have focused on beneficiation of Indian iron ore fines and slimes using ...
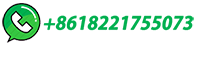
The Sintering Process of Iron Ore Fines – IspatGuru
Sintering process helps utilization of iron ore fines (0-10 mm) generated during iron ore mining operations. Sintering process helps in recycling all the iron, fuel and flux bearing waste materials in the steel plant. …
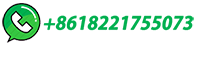
Iron Ore Agglomeration Technologies | IntechOpen
However, the depletion of high-grade iron ore sources has made necessary the utilization of concentration processes with the purpose of enriching the iron ore. Because of these processes, a fine granulometry is produced, and thus iron agglomeration process is necessary.
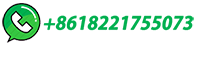
Fine Size Dry Iron Ore Beneficiation Using Thin Bed Air
At different stages of wet beneficiation, nearly 1 m 3 of water is required for processing one tonne of iron ore. Processing the iron ore through a dry processing …
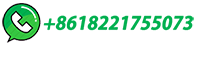
Innovative Technique to Generate Saleable Iron Ore Fines
With the above wet process particles above 45 microns sizes are recovered with 77 % weight recovery. During the ... conducting in-house and external study to recover escaped iron ore bearing minerals from ultra-fines recovery plant on …
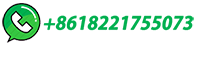